Author. Eng. Euclides Quiñonez, September 22, 2023.
Introduction
Ensuring safe and reliable operation throughout the useful life of industrial assets requires constant and continuous maintenance; However, corrosion is a natural phenomenon that can compromise the structural integrity of these assets. According to the World Corrosion Organization, the global costs related to this natural phenomenon are estimated at 2.2 trillion dollars, which represents 3.5% of the Gross Domestic Product (GDP) worldwide.
Prevention and early detection of signs of degradation are critical to avoiding costly damage, catastrophic accidents and production losses. In this context, new sensor technologies play an important role in real-time monitoring for management and control.
This article highlights the importance of the technology of these devices to address corrosion in industrial infrastructure.
Sensors and corrosion detection
Sensing and control involves the continuous monitoring of industrial assets and this is achieved through a variety of specific sensors, designed to detect changes in the environmental and structural conditions of materials.
In recent years, there has been significant progress in corrosion monitoring technology; which has enabled the implementation of software-based monitoring systems, capable of providing real-time data and the widespread adoption of solutions, especially in the oil and gas industry.
“Data analysis for predictive maintenance has become an additional source of income, in this sense important suppliers have developed platforms based on digitalization, offering solutions aimed at boosting their growth in this market.” Among these suppliers, the company Emerson stands out.1 uses cutting-edge sensor technology and wireless data delivery to continuously monitor metal loss in pipelines due to corrosion or erosion in corrosive environments and environments. Rosemount Wireless Permasense systems (Figure 1) reliably deliver amazing data quality and frequency for better-informed operational decision making and enable safer, more profitable operations.
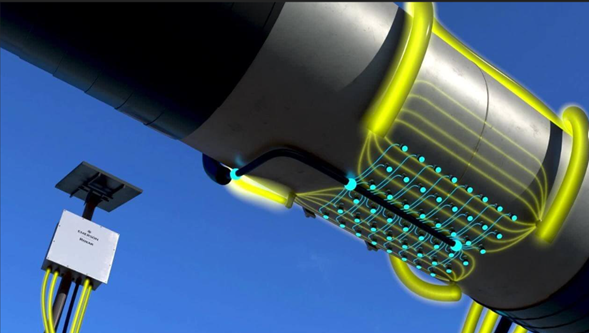
Each sensor is designed for a specific function, using different technologies and testing techniques, but all with the objective of detecting deviations that could lead to failure or degradation of the material. These sensors can be installed permanently on equipment or structure for permanent monitoring or used on portable equipment for temporary evaluations.
Types of sensors for corrosion detection
- Electrical Resistance (RE): Their function is to monitor the electrical resistance of a metal surface and detect variations in this property; which indicates the presence of corrosion. As the electrical resistance increases, resulting in an alarm signal, these RE probes perform a similar function to coupons, providing a basic measure of metal loss.
- Ultrasound: They use high-frequency sound waves to inspect the integrity of metallic materials, detecting a decrease in thickness.
- Electrochemical: They are highly sensitive chemical devices that respond to specific changes in electrical potential or current as a consequence of the presence of a chemical species; which is an indication of the formation of corrosion products.
- Image Sensors: Like thermal imaging cameras, they can identify abnormal heat patterns on the surface of industrial assets, indicating damage or deviations in the operation of an asset.
Use of sensors in corrosion monitoring
The use of these devices depends on the type of damage to be evaluated. Below are some applications:
Corrosion Under Insulation (CUI): They are permanently installed in pipes or containers under thermal insulation. Provides information on the status of assets in real time, regarding corrosion or the presence of moisture, (figure 2)
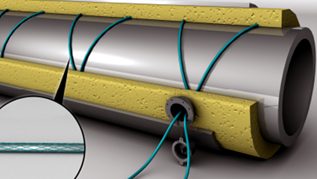
Loss of thickness in pipes: Ultrasonic thickness measurements are the most used Non-Destructive Testing method to monitor the loss of thickness in equipment and pipes. Other non-destructive techniques such as Eddy currents and Magnetic Field Leakage are also used for the same purpose or to detect cracks and deformations. Below is some of the equipment and probes developed for this purpose:
- Instrumented tool: These devices, also known in the industry as smart pigs, integrate a selection of ultrasonic (UT) or Magnetic Field Leakage (MFL) sensors and cleaning tools. They have different diameters and are introduced into the pipes in service, traveling along the route driven by the flow of liquid or gas, performing cleaning and inspections over long distances. These can collect data on corrosion or thickness loss, cracks and abnormalities in the weld beads.
- Guided waves: This technology uses collars with multiple sensors and advanced software that allow 100% of the pipe volume to be swept, covering a distance of up to 100 m in a single intervention. Detects thickness loss in buried or thermally insulated pipes. Companies such as Guided Ultrasonics Limited and Eddyfi Tecnologices have developed very versatile guided wave equipment, with real-time response and high precision. (figures 3 and 4).
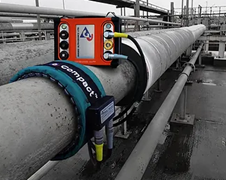
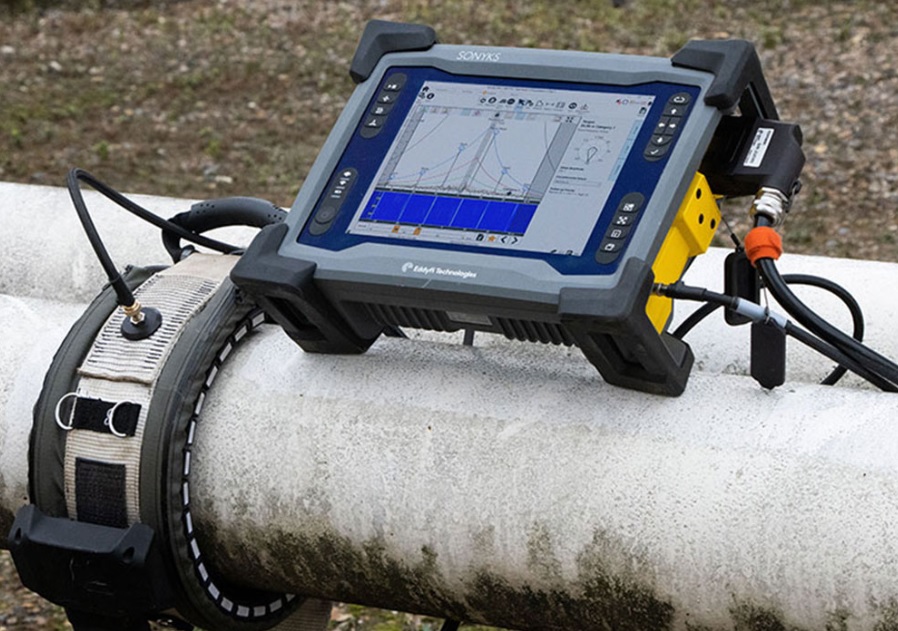
Corrosion monitoring in civil structures
Special sensors have been developed to monitor the risk of reinforcement corrosion in concrete structures due to chloride penetration and carbonation of the concrete, (Figure 5).
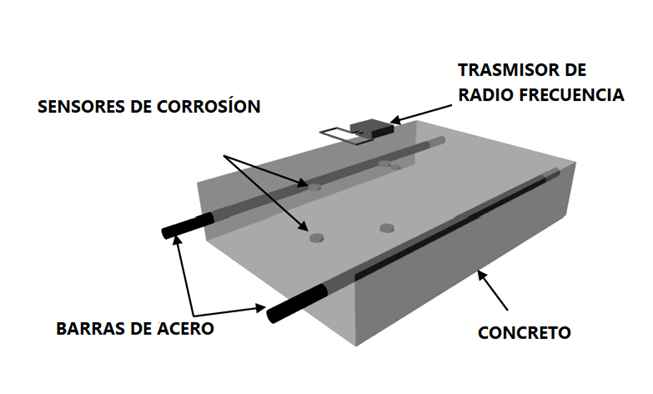
Advantages of continuous corrosion monitoring
- Early detection: The evaluation of this phenomenon in its initial stages is essential to schedule preventive maintenance interventions, thus protecting the integrity of the assets.
- Cost reduction: Detection enables timely repairs and maintenance, reducing overall costs by preventing costly damage or the need to replace assets.
- Safety: The safety of workers and protection of the surrounding environment is important, through continuous monitoring of corroded assets.
- Service life extension: Preventative maintenance based on sensor data can significantly extend the useful life of assets, increasing return on investment for industries.
- Optimization: The results of the controls carried out allow the efficient allocation of maintenance resources, since interventions can be scheduled.
Challenges and future of advanced sensor technologies
- Startup costs: These advanced systems can be expensive to implement, which can be a barrier for some industries, especially small and medium-sized businesses. However, the long-term benefits often outweigh the initial costs, clearly justifying the investment.
- Maintenance: They require proper maintenance to ensure their accuracy and reliability. This may include periodic calibrations and replacement of faulty sensors.
- Data Integration: Managing large amounts of collected information can be challenging. Industries must develop effective data management systems to make the most of the results provided by these devices.
- Continuous technological development: The continuous evolution of this technology alerts industries that they must be willing to invest in constant updates and improvements to keep up with the latest innovations.
Despite these challenges, the future of sensor technologies in corrosion detection is promising. Research and development is expected to continue improving the accuracy, durability, and accessibility of these systems, allowing for their broader adoption across various industries.
Conclusions
As these technologies continue to evolve and overcome technical and economic challenges, they are expected to play an even more important role in asset protection and sustainability. Investing in these technologies is not only a sensible measure from an economic point of view, but also a responsibility towards safety and the environment. Detecting corrosion early can make the difference between success and failure in the world of industrial infrastructure.