Currently, the wireless ultrasonic sensor is an advanced technology that has revolutionized the measurement of corrosion. These sensors are composed of low-cost nodes, which include the sensor, the interface to perform communications, and a microprocessor.
A Non-Destructive Test (NDT) by ultrasound (UT) is a method used to detect the thickness or internal structure of different materials. Through this technique, defects in materials, such as subsurface defects, can be identified. Ultrasound testing is performed by sending high-frequency acoustic waves through a material and analyzing the return echoes. By examining this information, you can evaluate the thickness of the material or identify if there is internal damage, such as corrosion 1 from cracks or defects.
In this context, the implementation of ultrasonic wireless sensor networks has proven to be an effective tool for the efficient monitoring of corrosion in pipes and metallic structures in real time and the timely detection of material failures; which translates into a reduction in operating costs and greater safety in industrial processes.
This article describes the features and specifications of a Wireless UT system for monitoring the corrosive process. Likewise, a technical description of the operation of these wireless devices and their impact on corrosion control is presented.
How does a wireless ultrasonic sensor work?
The development of wireless sensor networks composed of low-cost nodes has allowed the creation of real-time corrosion monitoring and detection systems. They are autonomous devices that can take data from the medium, process it and transmit it to the rest of the network.
The radio signal emitted by the sensors is captured by a receiver that subsequently converts it into a specific output according to the requirements, whether it is an analog current or data analyzed through computer software.2, Figure 1 shows a diagram of the operation of these wireless systems.
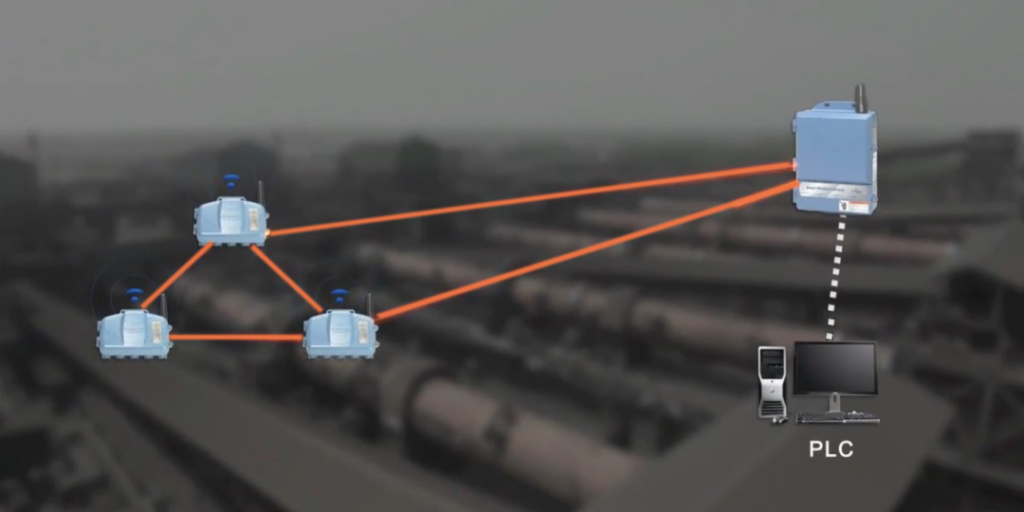
The sensor spokes form a network that ensures that each sensor establishes multiple connections and therefore multiple signal paths. This configuration has several advantages, such as eliminating the need for a direct line of sight to the base station (node), extending the communication range between individual sensors, even at considerable distances from the base station, and ensuring stable communications thanks to redundant signal paths.
The receiver integrates into the client’s data network and transforms the information flow into TCP/IP (network protocols) format, allowing it to be transmitted to the server through the software infrastructure. Data is securely stored in a database and is accessible through the Data Manager from any computer connected to the customer’s network, or can be easily exported from the database.
The functionality of these sensors is based on the emission of ultrasonic waves that propagate through the material under analysis. These ultrasonic waves bounce off the surface of the material and are collected by the sensor. The captured signal is subjected to an analysis process to determine the thickness of the material and detect possible corrosion problems.
Impact of wireless ultrasonic sensors on corrosion detection
Throughout production, companies face the problem of corrosion of metal surfaces in pipes, boilers and tanks. This deterioration process causes a decrease in the original thickness of the metal, which can cause leaks or losses of substances or fluids.
Internal corrosion is sometimes not detectable by visual inspection, because the pipe, boiler or tank would have to be cut or dismantled. If left to act over time undetected, it will weaken surfaces and possibly cause serious structural failure. Both safety and economic considerations require that metal structures be inspected regularly3.
Wireless UT sensor technology has revolutionized the way corrosion detection is approached. Regarding their impact on corrosion processes, these sensors can be used to monitor corrosion in real time and detect any changes in the process.
This allows engineers to take preventive measures before significant damage occurs. Additionally, these sensors can be used to monitor the structural integrity of materials and detect any changes in material quality.
Some of the most notable impacts include:
- Continuous monitoring: Wireless UT sensors allow continuous, real-time monitoring of corrosion, providing a detailed view of the evolution of corrosive processes. This is critical to making informed and timely decisions about asset management and maintenance scheduling.
- Greater precision: Ultrasonic technology is recognized for its accuracy in evaluating the thickness of a material. Wireless UT sensors are precision-based by eliminating errors, avoiding human error, and ensuring consistent and reliable measurements.
- Cost reduction: By eliminating the need for periodic manual inspections, costs associated with production stoppages and hiring personnel to perform inspections are reduced. This translates into significant savings over time.
- Increased Safety: By enabling inspections without coming into direct contact with structures, wireless UT sensors improve inspector safety by reducing exposure to potentially hazardous environments.
- Historical Data: Wireless technology makes it easy to collect and store data over time. This creates a valuable data set that allows for long-term analysis and identification of corrosion trends.
- Integration with management systems : Data collected by wireless UT sensors can be integrated with asset and maintenance management systems, allowing for more informed decision making and efficient planning.
Conclusions
Advances in wireless UT sensor technology are transforming the way we approach corrosion detection and monitoring in critical infrastructure. This has a significant impact on industrial process safety, efficiency and operating costs, ensuring the integrity and useful life of infrastructures.
Wireless networks of electronic sensors represent an interesting solution when acquiring several variables in different places, without having to implement wiring or channeling that increases the costs of the systems.
References
- APPLUS; “Corrosion evaluation”; consulted on October 22, 2023. https://www.applus.com/global/es/what-we-do/service-sheet/evaluacion-corrosion;
- Emerson; consulted 10-22-2023; https://www.emerson.com/es-es/automation/measurement-instrumentation/corrosion-erosion-monitoring/about-advanced-wireless-corrosion-erosion-technology
- Ferrer, R; “Non-Destructive Testing (NDT): What are they?”; Automotive Magazine; 07/29/2019