Autor. Ing. Euclides Quiñonez, 22 septiembre 2023.
Introducción
Garantizar el funcionamiento seguro y confiable a lo largo de la vida útil de los activos industriales requiere de un mantenimiento constante y continuo; sin embargo, la corrosión es un fenómeno natural que puede comprometer la integridad estructural de estos activos. Según la Organización Mundial de la Corrosión, los costos globales relacionados con este fenómeno natural se estiman en 2.2 billones de dólares, lo que representa el 3.5 % del Producto Interno Bruto (PIB) a nivel mundial.
La prevención y la detección inicial de signos de degradación son fundamentales para evitar costosos daños, accidentes catastróficos y pérdidas de producción. En este contexto, las nuevas tecnologías de sensores desempeñan un rol importante en el monitoreo en tiempo real para su gestión y control.
Este artículo se destaca la importancia de la tecnología de estos dispositivos para afrontar la corrosión en la infraestructura industrial
Sensores y la detección de corrosión
La detección y control implica la monitorización continua de los activos industriales y esto se logra a través de una variedad de sensores específicos, diseñados para detectar cambios en las condiciones ambientales y estructurales de los materiales.
En los últimos años, se ha experimentado un significativo avance en la tecnología de monitoreo de la corrosión; lo cual ha posibilitado la implementación de sistemas de monitoreo basados en software, capaces de proporcionar datos en tiempo real y a la adopción generalizada de soluciones, especialmente en la industria del petróleo y gas.
El análisis de datos para el mantenimiento predictivo se ha convertido en una fuente adicional de ingresos, en este sentido los proveedores importantes han desarrollado plataformas basadas en la digitalización, ofreciendo soluciones orientadas a impulsar su crecimiento en este mercado.” Entre estos proveedores, se destaca la empresa Emerson1 utiliza tecnología de sensores de punta y entrega de datos inalámbrica para monitorear continuamente la pérdida de metal en las tuberías debido a la corrosión o erosión en ambientes y entornos corrosivos. Los sistemas Rosemount Wireless Permasense (figura 1), brindan de manera confiable una calidad y frecuencia de datos sorprendente para una toma de decisiones operativas mejor informada y permiten operaciones más seguras y rentables.
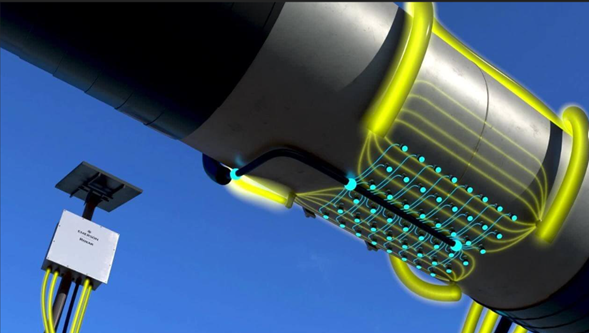
Cada sensor se diseña para una función específica, usando diferentes tecnologías y técnicas de ensayos, pero todos con el objetivo de detectar desviaciones que puedan incidir en una falla o degradación del material. Estos sensores pueden instalarse fijo en un equipo o estructura para realizar monitoreo permanente o emplearlos en equipos portátiles para evaluaciones temporales.
Tipos de sensores para la detección de corrosión
- Resistencia Eléctrica (RE): Tienen como función monitorean la resistencia eléctrica de una superficie metálica y detectan las variaciones de esta propiedad; la cual, indica la presencia de corrosión. A medida que avanza, la resistencia eléctrica aumenta, lo que se traduce en una señal de alarma, estas sondas de RE cumplen una función similar a los cupones, proporcionando una medida básica de la pérdida de metal.
- Ultrasonido: Utilizan ondas sonoras de alta frecuencia para inspeccionar la integridad de los materiales metálicos, detectando la disminución de espesor.
- Electroquímicos: Son dispositivos químicos altamente sensibles que responden a cambios específicos en el potencial o a la corriente eléctrica como consecuencia de la presencia de una especie química; lo cual, es indicio de la formación de productos de corrosión.
- Sensores de Imagen: Son como las cámaras termográficas, pueden identificar patrones de calor anormales en la superficie de los activos industriales, indicando daños o desviaciones en la operación de un activo.
Uso de sensores en el monitoreo de corrosión
El uso de estos dispositivos depende del tipo de daño a evaluar. A continuación, se presentan algunas aplicaciones:
Corrosión Bajo Aislamiento (CUI): Son instalados permanentemente en las tuberías o recipientes debajo del aislamiento térmico. Proporciona información sobre el estado de los activos en tiempo real, respecto a la corrosión o la presencia de humedad, (figura 2)
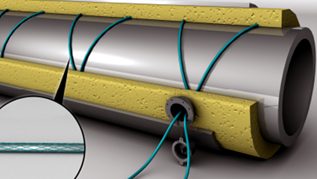
Perdida de espesores en tuberías: Las mediciones de espesores con ultrasonido es el método de Ensayo No Destructivo más utilizado para monitorear la perdida de espesores en equipos y tuberías, así mismo se utilizan otras técnicas no destructivas como corrientes Eddy y Fuga de Campo Magnético, con el mismo fin o para detectar grietas y deformaciones. A continuación, alguno de los equipos y sondas desarrolladas para tal fin:
- Herramienta instrumentada: Estos equipos, también conocidos en la industria como cochino inteligente, integran una selección de sensores ultrasónicos (UT) o de Fuga de Campo Magnéticos (MFL) y herramientas de limpieza. Son de diferentes diámetros y se introducen en las tuberías en servicio, realizando su recorrido impulsado por el flujo de líquido o gas, realizando limpiezas e inspecciones a largas distancias. Estos pueden recopilar datos sobre corrosión o perdida de espesor, grietas y anormalidades en los cordones de soldadura.
- Ondas guiadas: Esta tecnología utiliza collarines con múltiples sensores y software avanzados que permiten realizar barrido del 100 % del volumen de la tubería cubriendo distancia de hasta 100 m en una sola intervención. Detecta perdida de espesores en tuberías enterradas o asiladas térmicamente. Empresa como Guided Ultrasonics Limited y Eddyfi Tecnologices han desarrollados equipos de ondas guiadas muy versátiles, de repuesta en tiempo real y de alta precisión. (figuras 3 y 4).
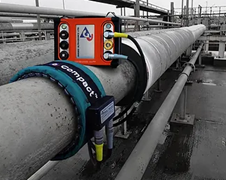
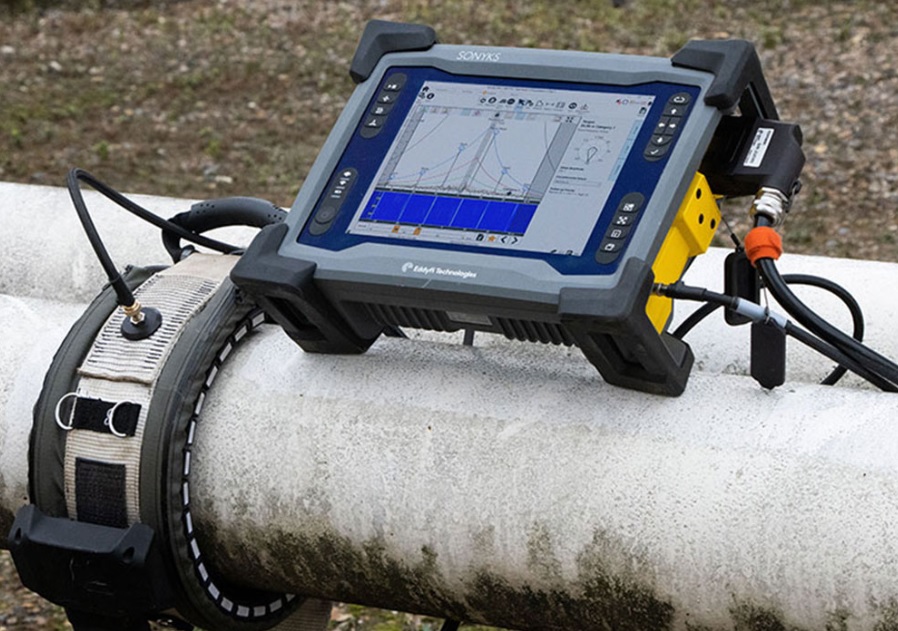
Monitoreo de corrosión en estructuras civiles
Se han desarrollado sensores especiales para controlar el riesgo de corrosión del refuerzo en estructuras de hormigón debido a la penetración de cloruro y la carbonatación del hormigón, (figura 5).
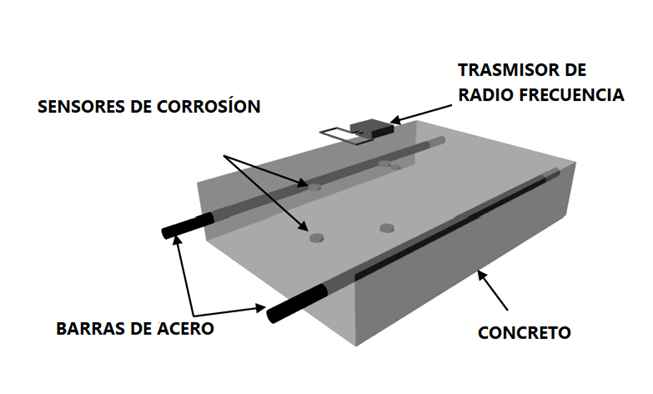
Ventajas de la monitorización continua de la corrosión
- Detección temprana: La evaluación de este fenómeno en sus etapas iniciales es fundamental para programar intervenciones de mantenimiento preventivo, protegiendo de esta forma la integridad de los activos.
- Reducción de costos: La detección permite reparaciones y mantenimientos oportunos, lo que reduce los costos totales al prevenir daños costosos o la necesidad de reemplazar activos.
- Seguridad: Es importante la seguridad de los trabajadores y protección del medio ambiente circundante, a través del monitoreo continúa de activos corroídos.
- Extensión de la vida útil: El mantenimiento preventivo basado en datos de sensores puede extender significativamente la vida útil de los activos, lo que aumenta el retorno de la inversión para las industrias.
- Optimización: Los resultados de los controles realizados, permiten la asignación eficiente de recursos de mantenimiento, ya que las intervenciones pueden programarse.
Desafíos y futuro de las tecnologías de sensores avanzados
- Costos iniciales: La implementación de estos sistemas avanzados puede ser costosa, lo que puede ser una barrera para algunas industrias, especialmente las pequeñas y medianas empresas. Sin embargo, los beneficios a largo plazo suelen superar los costos iniciales, justificando claramente la inversión.
- Mantenimiento: Requieren un mantenimiento adecuado para garantizar su precisión y confiabilidad. Esto puede incluir calibraciones periódicas y reemplazo de sensores defectuosos.
- Integración de datos: La gestión de grandes cantidades de información recopilada puede ser un desafío. Las industrias deben desarrollar sistemas de gestión de datos efectivos para aprovechar al máximo los resultados proporcionados por estos dispositivos.
- Desarrollo tecnológico continuo: La evolución continua de esta tecnología, alerta a las industrias que deben estar dispuestas a invertir en actualizaciones y mejoras constantes para mantenerse al día con las últimas innovaciones.
A pesar de estos desafíos, el futuro de las tecnologías de sensores en la detección de corrosión es prometedor. Se espera que la investigación y el desarrollo continúen mejorando la precisión, la durabilidad y la accesibilidad de estos sistemas, lo que permitirá su adopción más amplia en diversas industrias.
Conclusiones
A medida que estas tecnologías continúen evolucionando y superando desafíos técnicos y económicos, se espera que desempeñen un papel aún más importante en la protección y la sostenibilidad de activos. La inversión en estas tecnologías no solo es una medida sensata desde el punto de vista económico, sino también una responsabilidad hacia la seguridad y el medio ambiente. La detección de la corrosión a tiempo puede marcar la diferencia entre el éxito y el fracaso en el mundo de la infraestructura industrial.