Introduction
Corrosion Under Insulation (CUI) is a condition that produces deterioration and damage due to corrosion, which manifests itself on the surface of equipment covered with insulating materials, mainly caused by the accumulation of moisture.
This problem generally occurs due to a variety of factors and is likely to occur in equipment that operates at ambient, low, or elevated temperatures. One of the main complications of CUI is that, being hidden under insulation, it is difficult to detect, especially on computers that, even if temporarily down, could resume operation in the future.
This problem generally occurs in industries such as the petrochemical, oil and gas sector, and extends to both onshore and offshore operations. Despite being one of the most researched and documented problems in the refining and chemical processing industry, CUI remains a significant cause of maintenance expenses.
It is important to consider the implementation of advanced engineering practices from the design stage and throughout the entire operation of the equipment is essential. It is important to select highly durable coatings and thermal insulators that offer resistance to water, complemented with efficient protection and drainage systems.
The CUI can manifest itself in various ways, among which are
- Galvanic corrosion: Occurs when wet insulation facilitates an electrical flow between two metals of a different nature, such as the base metal and some component of the outer coating.
- Acid or alkaline corrosion: This occurs when the insulation contains substances with extreme pH, either alkaline or acid.
- Chloride Corrosion: Arises from the interaction between insulators with soluble chlorides and certain stainless steels, especially when temperatures exceed 60 °C.
A particularly concerning subtype of CUI is External Chloride Stress Corrosion (ESCC), which affects 300 series stainless steels. These steels, despite their resistance to corrosion, can develop small leaks before complete rupture. Prevention of ECSCC is essential and is achieved through the use of suitable, insulating, low chloride coatings and efficient weather barriers.
Consequences of Corrosion Under Insulation (CUI)
Corrosion Under Insulation (CUI) has multiple consequences in the aforementioned industries, ranging from oil and gas to petrochemicals and other related industries. These consequences can be both direct and indirect:
- Structural failures: Significantly weaken the structural integrity of equipment and piping, which can lead to catastrophic failures such as ruptures or explosions, especially under high-pressure conditions.
- Leaks and spills: Before total failure occurs, small leaks are likely to develop, which may result in the release of chemicals, hydrocarbons, or gases, with the potential to cause fires or explosions.
- High maintenance costs: Detection and repair requires removal of the insulation, repair or replacement of the affected equipment, and reinstallation of the insulation. These processes are expensive and time consuming, which can result in unplanned downtime.
- Reduced equipment life: The presence of this condition can significantly shorten the expected life of equipment and piping, leading to premature replacements.
- Compromise of operating efficiency: Affects the operating efficiency of systems and equipment. For example, a corroded pipe can restrict flow, affecting the efficiency of the process.
- Health and safety risks: Leaks and spills resulting from CUI can expose workers and the environment to hazardous or toxic chemicals.
- Environmental impact: In addition to direct health and safety risks, leaks and spills can have an environmental impact, contaminating soil, groundwater, or releasing harmful gases into the air.
- Reputation and liability: CUI-related incidents, especially those that result in spills, fires, or injuries, can damage a company’s reputation and result in litigation and penalties.
- Increased inspection costs: Failure to detect this damage on time can cause additional costs when implementing more frequent inspections or more advanced inspection techniques.
- Operational interruptions: Operations may need to be stopped or reduced during related inspections, repairs or replacements.
Prevention and programs to attack the problem
Corrosion Under Insulation (CUI) is a persistent problem in many industries, and its prevention and detection is important to minimize the associated risks. Here are some preventative measures and recommended inspection schedules to address this issue:
Precautionary measures
- Material Selection: Use corrosion resistant materials or apply protective coatings to susceptible surfaces.
- Proper Design: Design systems with adequate drainage to prevent water accumulation and design joints to minimize water ingress.
- Quality insulation: Use insulation that repels water or that does not absorb moisture. Avoid isolates containing chlorides or sulfates.
- Barriers and Sealants: Apply waterproof barriers and sealants at insulation interfaces to prevent water ingress.
- Regular maintenance: Carry out periodic inspections and maintenance of the insulation and barriers to ensure that they are in good condition and do not allow moisture ingress.
- Environmental Control: In areas prone to high humidity or condensation, consider using dehumidifiers or heating systems to keep surfaces dry.
Inspection programs
- Visual Inspection: Perform regular visual inspections to look for signs of insulation damage or areas where water may collect.
- Radiography: Use radiography techniques to examine areas under insulation for signs of corrosion.
- Pulsed Eddy Current (PEC) : This technique can detect corrosion under insulation without the need to remove the insulation (See figure 1).
- Ultrasound: Guided wave ultrasound can detect areas of thickness loss in pipes or equipment.
- Thermography: Infrared cameras can detect areas of moisture under insulation, which are potential points for CUI.
- Risk Analysis: Prioritize areas for inspection based on risk factors, such as equipment age, corrosion history, environmental conditions, and other relevant factors.
- Inspection after significant events: After events such as flooding, heavy rain, or liquid releases, perform inspections to ensure that the insulation is not compromised.
- Sampling and analysis: In high risk areas, consider taking samples of the material under the insulation and analyzing it for signs of corrosion.
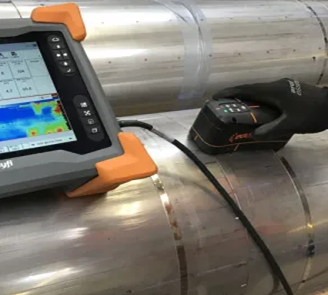
Implementing these preventative measures and inspection programs can help industries detect and address CUI before it causes significant problems. A combination of prevention, early detection and corrective action is essential to effectively manage the risks associated with CUI.
Despite the advances, we still do not have a definitive method for its detection, so the combination of multiple techniques is usually the most recommended strategy. It is crucial that the professionals in charge understand the capabilities and limitations of each technique, in order to make informed decisions about the integrity and reliability of the inspected equipment and guarantee the safety and efficiency of operations.
Conclusion
Corrosion Under Thermal Insulation (CUI) represents one of the stealthiest and most persistent corrosion damage in the industry , with implications ranging from elevated maintenance costs to significant health, safety and environmental risks. Despite technological advances and in-depth research in the field, early detection remains a challenge, underlining the need for strong prevention and constant surveillance.
Industries, especially those in sectors such as oil and gas and petrochemicals, must take a proactive approach, combining multiple inspection techniques and prioritizing the implementation of advanced engineering practices from the design stage. Only through a combination of prevention, early detection, and corrective action can one hope to effectively address this “silent danger” and ensure safe and efficient operations well into the future.
References
Own source
Learn about Corrosion Under Insulation and protect your assets! I invite you to read our article at www.inspenet.com.