The New Zealand company Aurora Labs has managed to improve the goals of lightweighting and performance proposals for its 200N class 3D micro-gas turbine, created using advanced printing technology.
The manufacture of the 200N model
The manufacture of microturbines , offering a viable option for their implementation in small-scale propulsion systems and in generators for drones and other small aerial vehicles.
Ahead of its market launch next month, the 200N model is designed specifically for light propulsion systems , spanning a diversity of market applications. Aurora Labs is developing a more robust model, the Class 400N, expanding its layout and technological offering.
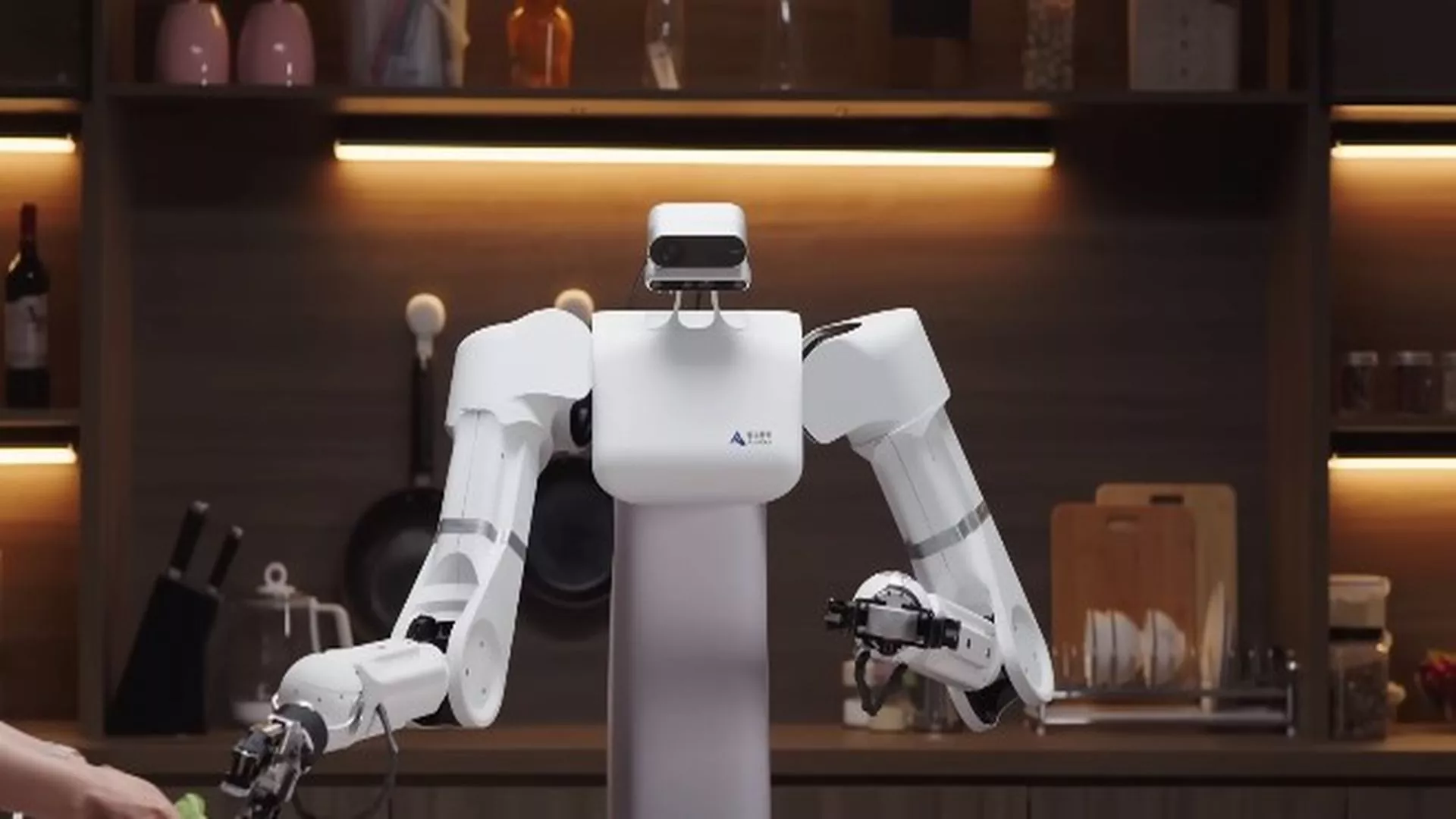
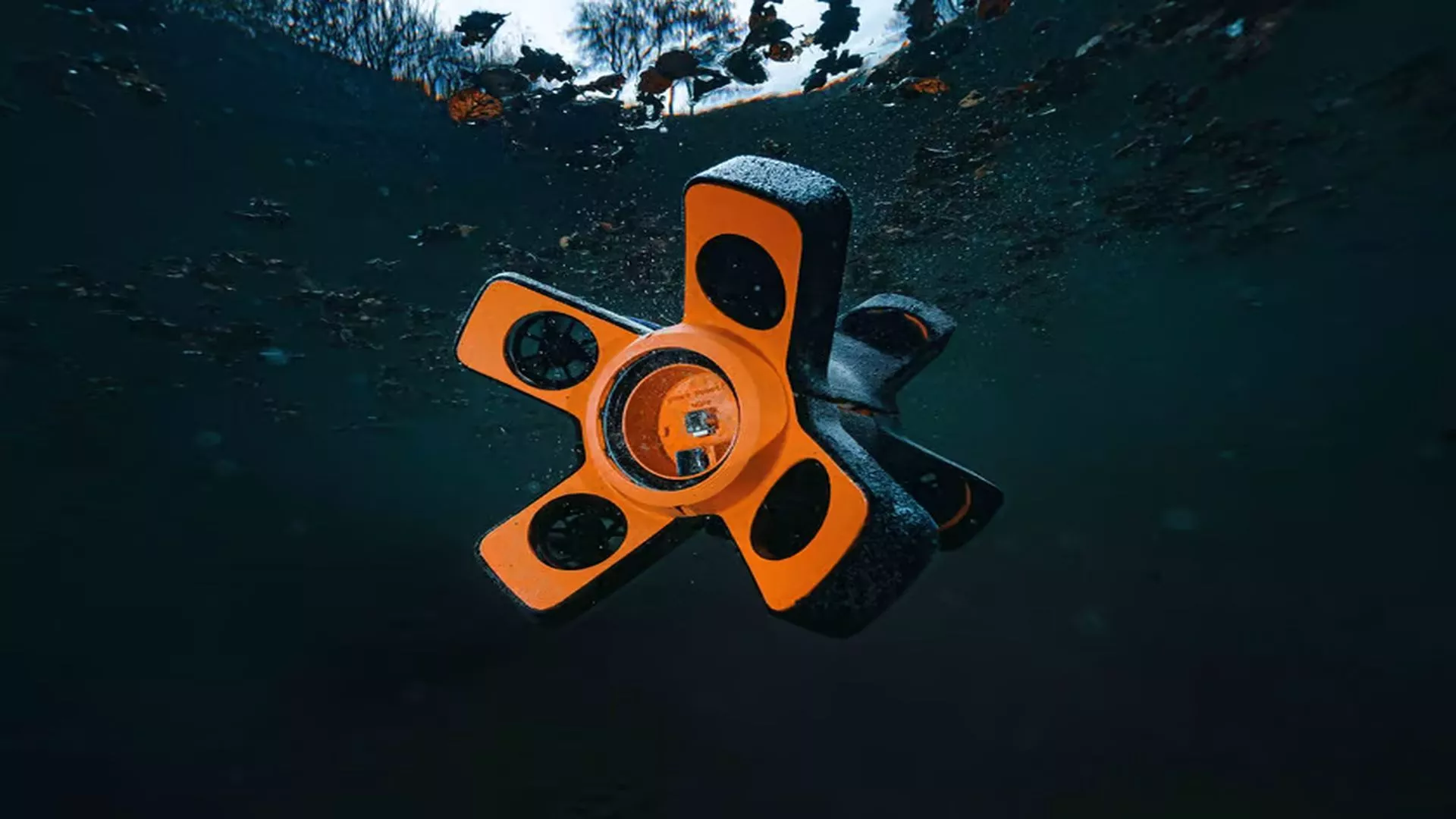
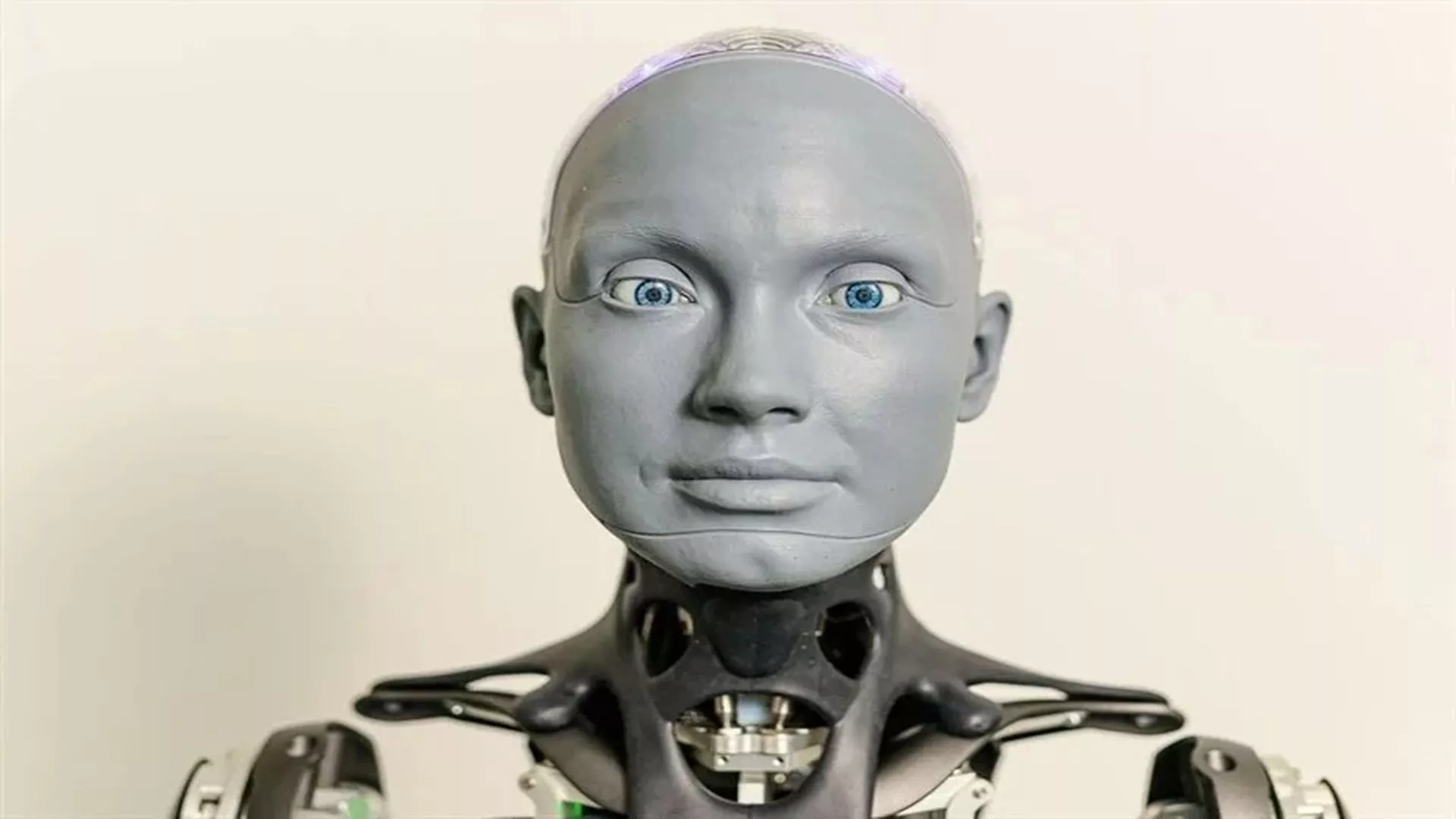
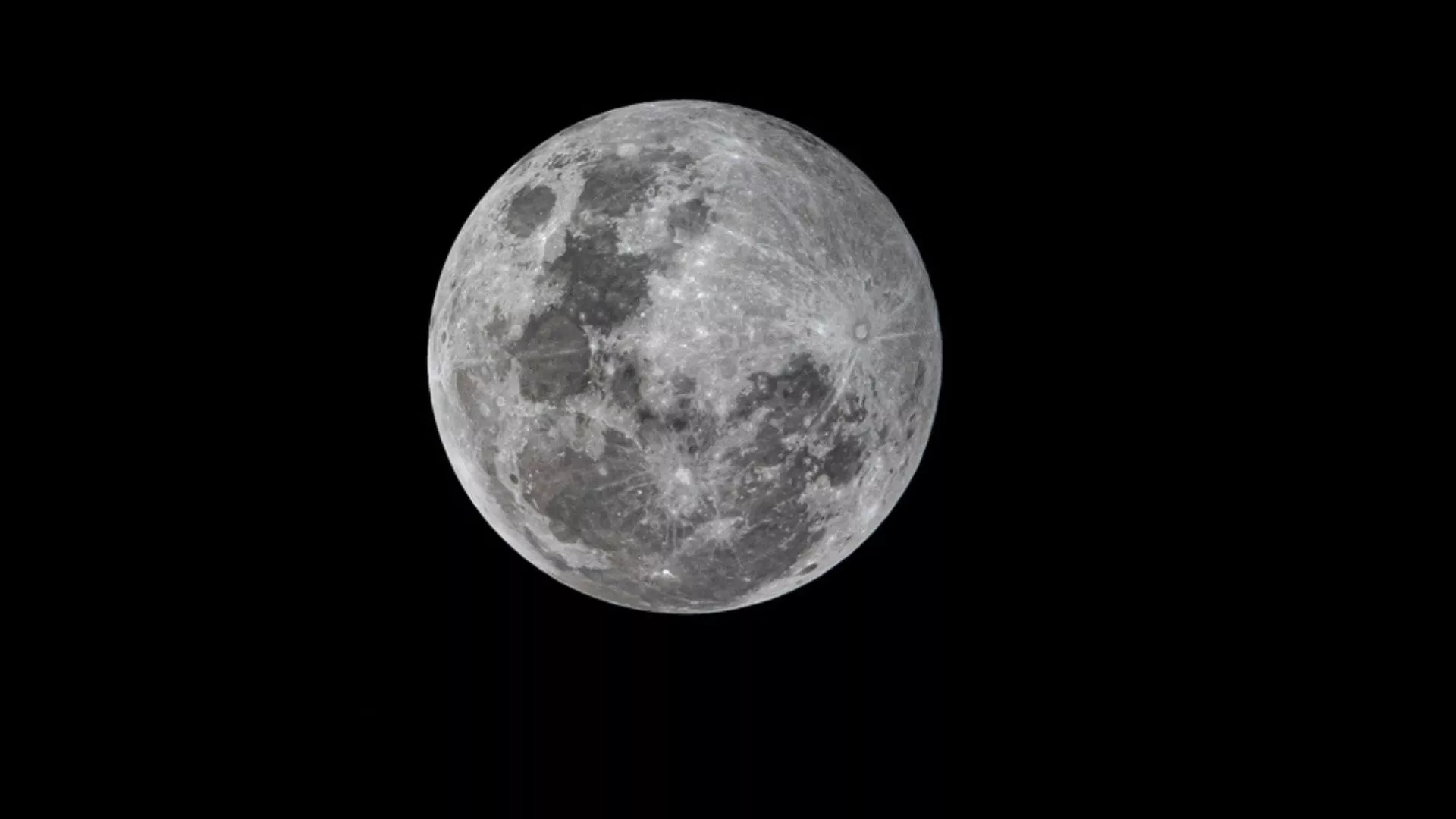
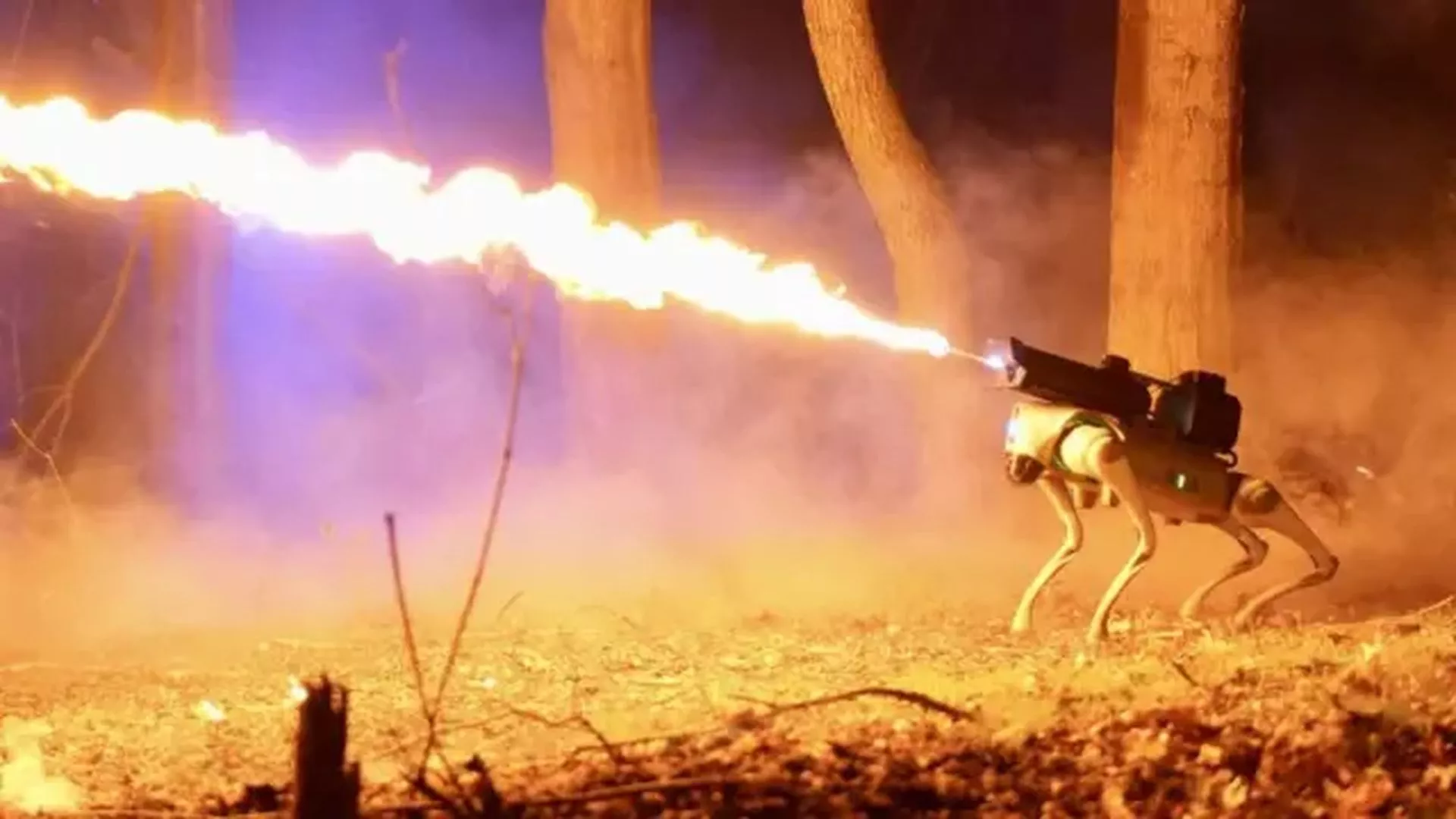
The manufacturing process of the 200N model, carried out in less than four months, was possible thanks to the use of Aurora Labs’ advanced 3D printer (A3D). Rebekah Letheby, CEO of the company, highlighted the efficiency of printing to accelerate the development of the engine prototype , meeting laboratory testing standards. Testing will continue under real-world conditions, installing the engine in a remotely operated fuselage.
3D gas turbine design
The A3D results meet expectations for thrust and energy efficiency and managed to overcome previous weight and fuel consumption limitations, with potential for future improvements through generative designs possible only with 3D printing . This is evidenced by the reduction in the number of parts required, which facilitates faster and more reliable assembly.
The engineering team has demonstrated the 3D printer’s ability to fuse multiple parts into one, achieving weight reductions of up to 20% compared to traditional methods. The robustness of the printed components was validated in tests that simulate extreme operating conditions.
Finally, the turbine has been designed to operate with conventional fuels such as Jet-A1 , kerosene and diesel, showing its adaptability to different operating environments for the company .
Follow us on social networks and don’t miss any of our publications!
Inspenet.com YouTube LinkedIn Facebook Instagram X
Source and photo: Aurora Labs