Introduction
Fouling in vacuum columns poses challenges in terms of product quality and flow due to dirt accumulation, resulting in high costs and low efficiency in crude refining processes. This adversely affects both production capacity and product quality, where performance in the separation and purification stages is critical.
During the refining process, once the crude oil has been desalted, it is sent as a feed stream to a processing unit where initial effective separations will take place. The feed charge will pass through the preheating tube bundle, typically on the shell side, absorbing heat from an already processed stream, leading to the formation of a type of refinery coke. It is at this stage where vacuum tower decontamination is necessary. Although temperatures do not reach sufficiently high levels to form carbon, the resulting deposit remains highly resistant to chemical removal.
This article aims to address issues associated with deposits in vacuum distillation towers by providing the most suitable solutions to control and mitigate fouling in vacuum columns.
What is vacuum distillation?
Vacuum distillation is a petroleum refining process in the Oil & Gas industry used to separate and purify high boiling point components such as heavy residues to obtain lighter products. It is conducted under pressures lower than atmospheric to decrease boiling points and prevent thermal decomposition of hydrocarbons1.
Vacuum distillation process
A representative diagram of the vacuum distillation process is shown in figure 1.
- Atmospheric residues: These are fed into the vacuum distillation tower after passing through pretreatment units to remove impurities like water and sediments.
- Vacuum distillation tower: The crude enters the vacuum distillation tower, where it is heated with steam and subjected to high vacuum (reduced pressure) to lower its boiling points.
- Fractional separation: In the vacuum distillation tower, high boiling point components such as heavy residues are separated into different fractions. The heaviest fractions are collected at the bottom of the tower.
- Condensation: The distilled fractions are condensed in condenser units and collected for further processing and refining.
- Products: Vacuum distilled products and intermediates such as lubricating oil, vacuum gas oil, and vacuum residue are collected based on their molecular weight and boiling point at different points in the tower.
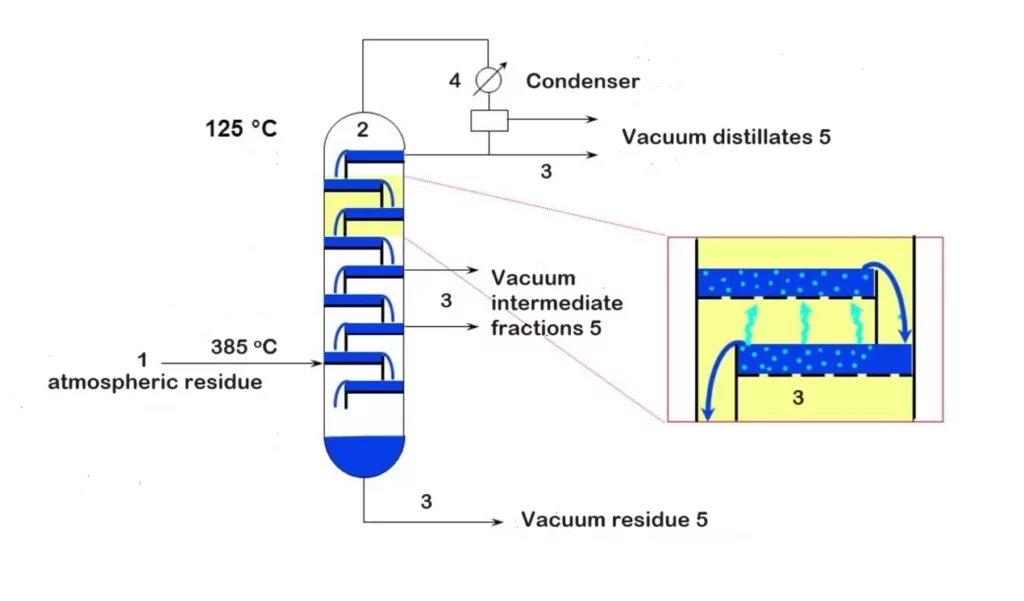
The separation of heavy hydrocarbons can lead to issues such as fouling, impacting operational efficiency and quality. It’s important to understand this process to conduct effective cleaning maintenance. Aiming to identify the causes of fouling in vacuum columns and explore strategies for controlling fouling in vacuum distillation towers, where long-chain hydrocarbons are separated, potentially leading deposits issues that affect operational efficiency and quality.
Causes of fouling in vacuum distillation
Scale service implies the need to have an understanding of the mechanism of scale formation and how it affects the process. Contamination presence can lead to increased energy consumption, reduced process heat transfer, and decreased column production capacity, necessitating chemical additives and sometimes extended downtime.
Key causes include:
- High temperatures at furnace outlet leading to severe cracking and coking in the washing zone and column bottom.
- Reduced reflux in the washing zone.
- Poor washing zone design.
- Extended residence times favoring coke formation.
- Deposits from corrosion.
In figure 2, various types of corrosion in different regions of the vacuum distillation tower due to naphthenic acid attack are depicted2.
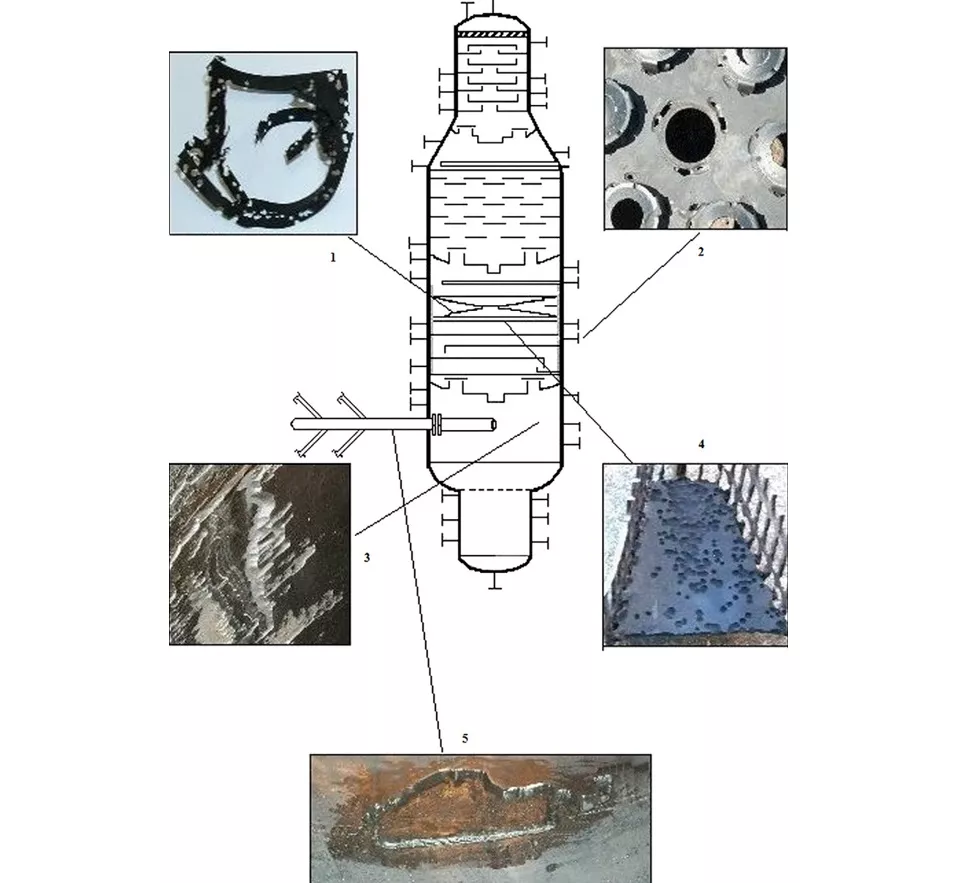
What problems does scale deposits cause in the vacuum tower?
Scale deposits in the vacuum distillation tower poses challenges in terms of product quality and flow due to the presence of contaminants. Deposits form during the processing of heavy crude. The feed into the tower contains not only refining products but also organic and inorganic deposits. Among these deposits, heavy waxes and asphaltenes accumulate, contributing to contamination and fouling of the vacuum tower.
Deposits from atmospheric towers lead to several issues. For instance, preheat exchangers can become fouled with heavy organic deposits and coke, reducing heat transfer efficiency. Similarly, tube bundles in the exchangers can become obstructed with a mixture of iron, silica, and organic compounds, including asphaltenes, waxes, and certain linear and branched polymers. Consequently, crude flow through the exchangers is reduced.
Furthermore, numerous internal trays and packed sections of the atmospheric tower can become contaminated with heavy organic deposits, leading to poor contact between rising vapors and liquid. This diminishes overall product quality. Additionally, reboilers and reflux condensers can suffer from similar deposit issues.
The tower may also contain high levels of H2S and pyrophoric iron, along with potentially flammable organic substances. These pose significant safety concerns due to the risk of fire.
Strategies to control fouling in vacuum columns
One of the most challenging aspects of scale deposits is that contaminants and processes are often unique to the specific process. To address a fouling problem, it is imperative to understand the fouling components in the process and the mechanism creating the fouling issue. Several methods are analyzed below to combat fouling.
Keeping scale deposits out of the column
Prevention is often more effective than post-treatment for many issues, including column contamination. Keeping contaminants out of the process and equipment is the preferred solution, with filtration commonly used, such as in amine contactors and regenerators. However, filtration can be costly and time-consuming to monitor, replace, or clean filters.
Sometimes, the amount of material to filter may be excessive, or contaminants may not solidify until formed within the column. Although filtration is an effective method for treating contaminants, it can often be impractical as a solution due to system filtration pressure drop.
Process control to prevent fouling
If fouling results from reaction or degradation of feedstock within the column, prevention involves controlling process conditions to avoid entering the problematic operational region. This can be inefficient and costly, as deviating from optimal conditions can negatively impact product quality, performance, and energy consumption. For example, in a refinery’s vacuum column, the lowest possible vacuum pressure is used in the washing section to prevent heavy hydrocarbon cracking.
The reliability of auxiliary equipment can also pose issues. A temporary pump failure can lead to a section of the tower becoming too hot or dry, causing rapid fouling or coking. Once fouling starts, it tends to grow quickly and can lead to serious and irreversible problems, reducing plant operability in a short time.
Use of antiscalants
In selected applications, antiscalants can be effectively utilized. In processes like olefin production, the use of antiscalants is quite common and often effective. The primary goal of antiscalants is to inhibit polymerization within the process that would lead to scaling. Corrosion inhibitors could also be termed antiscalants, as corrosion products can form scales and other materials that can foul the interior of the column.
Generally, the use of antiscalants is quite specialized and can be beneficial in certain services, including:
Scale-resistant internals
If scaling cannot be avoided in the feed or through operational adjustments, then addressing the scaling material within the column is necessary. A preferred strategy involves designing internals that allow the scaling material to pass through the column without accumulating. In some cases, open and less efficient devices like deflector trays or grid packing are used, designed so that scaling material has no opportunity to build up.
Trays: Fluted trays can be used to prevent solids from accumulating on the trays. These are conventional trays with down comers for liquid, but have directional vapor slots on the tray deck. Forward-directed vapor flow from the slots can be quite effective in pushing solids from one tray deck to another and eventually down to the column bottom.
Packings and distributors: When packing are used in scaling services, grid packings are typically employed because they have large openings and lower surface areas. The large openings are difficult to plug and therefore allow solids to pass through the bed. The low surface area ensures that the entire packing surface is fully wetted and prevents solids from drying on the surface and causing scaling.
Surface treatment
Surface treatments such as coatings or electropolishing can also be employed. Dual-flow trays lack downcomers and are typically highly active on the tray deck, causing contaminants to pass through them. Electropolished surfaces are very smooth and limit the ability of contaminants to adhere to the trays.
Conclusions
Effective fouling management in vacuum columns is critical for maintaining efficiency and profitability in oil refining operations. Various strategies have been developed to address this challenge, from prevention through operational condition control to the design of internals that allow free passage of scale formationmaterials. However, each strategy has its considerations and limitations, such as the energy cost associated with creating vacuum or the reduced efficiency of open devices.
It is important to implement a comprehensive approach that combines prevention, monitoring, and maintenance techniques to optimize column performance and extend their operational life. Furthermore, ongoing advancements in design and control technologies offer opportunities to enhance fouling management and ensure efficient operation of refining facilities in the future.
References
- Alan S. Foust, Leonard A. Wenzel, Curtis W. Clump, Louis Maus, L. Bryce Andersen; “Principles Of Unit Operations”,” 2Nd Ed 2008.
- Alvisi P. Pío, Lins VFC; “An overview of naphthenic acid corrosion in a vacuum distillation plant”; Engineering Failure Analysis; 18(5):1403-1406, junio 2011, July 2011.