Author: Ph.D. Orlando Salas, September 12, 2022.
Introduction
The structural integrity of hydrocarbon transport pipes must be optimally maintained, avoiding leaks or ruptures in the pipes, due to their impact on the ecosystem, society and the economy.
To carry out the cleaning, maintenance and review of the state of the pipelines, a tool known as PIG (Pipeline Internal Gauge) is used. This tool covers the entire interior of the pipes, using the pressure of the fluid being transported to its advantage. It starts from a starting point called the delivery trap, designed for the inclusion of the device in the pipe, to an end point called the receiving trap, which allows the extraction of solids from the pipe and its decoupling without the need to suspend hydrocarbon transport.
In addition to its use as a cleaning tool, this equipment is also used to detect discontinuities; which can cause ruptures or material wear in the pipes, these are known as Smart PIGs which can be equipped with different types of sensors. Below is a video courtesy of Rosin Grupo showing the process of inspecting a pipeline using this smart device.
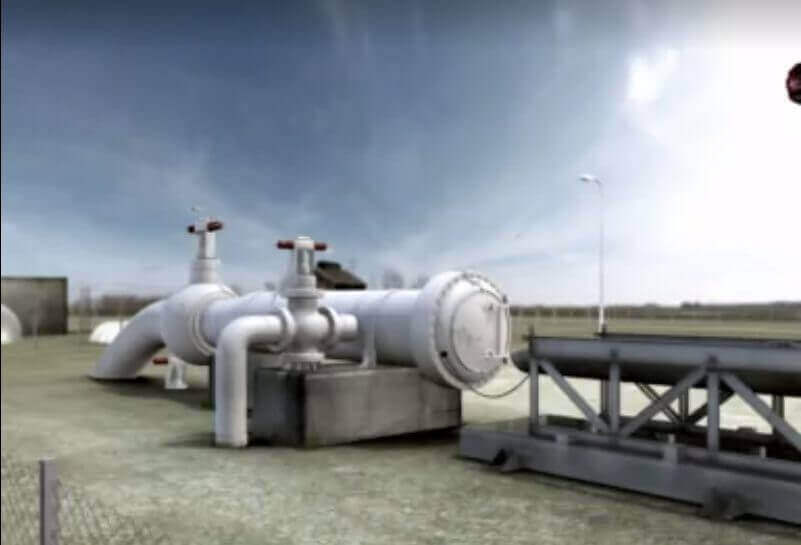
Video Courtesy of ROSEN Group
( https://www.rosen-group.com/global/solutions/services/inspection/Pipeline-Pigging.html)
The ECDA methodology corresponds to what is stated in the NACE RP0502 Pipeline External Corrosion Direct Assessment Methodology standard and is used in those cases in which it is not feasible to carry out the intelligent inspection for reasons such as low flows, lack of launch and/or receipt traps. of scrapers, obstructions in the line, changes in diameter, among others. Operators began looking for a new method to secure their pipelines in Non Piggable sections (pipe sections where a Smart Pig device cannot be placed).
The External Corrosion Direct Assessment (ECDA) methodology, proposed in the NACE SP0502 Pipeline External Corrosion Direct Assessment Methodology standard, represents an option for pipeline sections that cannot be inspected with smart pigs for reasons such as: low flows, no disposal of launch traps, obstructions in the line, changes in diameter, among others. In recent years, External Corrosion Direct Assessment (ECDA) methods have been widely adopted in the oil and gas industry to verify the integrity of pipelines. Therefore the importance in the knowledge and applicability of this standard.
This methodology consists of a structured process; which aims to improve safety by assessing and reducing the impact of external corrosion on the integrity of buried pipelines (oil pipelines, gas pipelines, etc.), by identifying and mitigating corrosion, repairing these defects, preventing and controlling the cause of corrosion of the pipes understanding the mechanism that produces it in order to improve the physical integrity of the structure.
It is specially designed to test buried pipelines made of ferrous materials. Users of this standard should be familiar with all pipeline safety regulations applicable to the jurisdiction in which the pipeline operates. This standard is intended for use by pipeline operators and others who must manage pipeline integrity. It is a continuous evaluation process, through which a pipeline operator should be able to identify and evaluate the places where corrosive activity has occurred, is occurring or may occur. One of the advantages of this technique is that it allows you to locate areas where defects may arise in the future, rather than just areas where defects have already formed.
It was developed as a process to improve pipeline safety, its main purpose being to prevent future damage from external corrosion. This standard assumes that external corrosion is a threat that must be evaluated and allows other threats to the integrity of the pipes to be detected, such as mechanical damage, stress corrosion cracking (SCC) and microbiologically influenced corrosion (MIC). When these threats are detected, additional evaluations or inspections must be carried out. The pipeline operator must use appropriate methods such as ASME B31.4.1, ASME B31.8.2, ASME B31.8.S.3, and API STD 11604 to address risks other than external corrosion.
The provisions of this standard must be applied under the direction of competent persons: engineers, registered professionals or persons recognized as specialists in corrosion or cathodic protection by organizations such as NACE, or engineers or technicians with appropriate levels of experience, if their activities Professionals include external corrosion control in buried ferrous piping systems.
The ECDA process consists of 4 stages, and integrates information on the physical characteristics of a pipeline and its operational history (1. previous assessment) together with data obtained from multiple field inspections (2. indirect inspection) and surface evaluations of the pipe (3.direct examination) to provide an evaluation of the integrity with respect to external corrosion (4.post evaluation).
Steps of the ECDA methodology
Pre-assessment
Historical and current data are collected to determine if the ECDA methodology is feasible, ECDA regions are defined and indirect inspection tools are selected.
2. Indirect inspection
Covers inspections from the ground surface to identify and classify the severity of coating failures, other anomalies and areas where corrosion has occurred or may occur
3. Direct evaluation
Includes analysis of indirect survey data to select sites for excavations and pipeline evaluations. Direct Inspection data is combined with Indirect Inspection data to identify and evaluate the impact of external corrosion on the pipeline.
4. Post-assessment
It covers analyzes of the stored data from the previous three steps to evaluate the effectiveness of the EDCA process and determine re-evaluation intervals.
Figure 1 shows a general diagram in summary form of the procedure to be followed during the 4 stages or steps of the ECDA methodology.
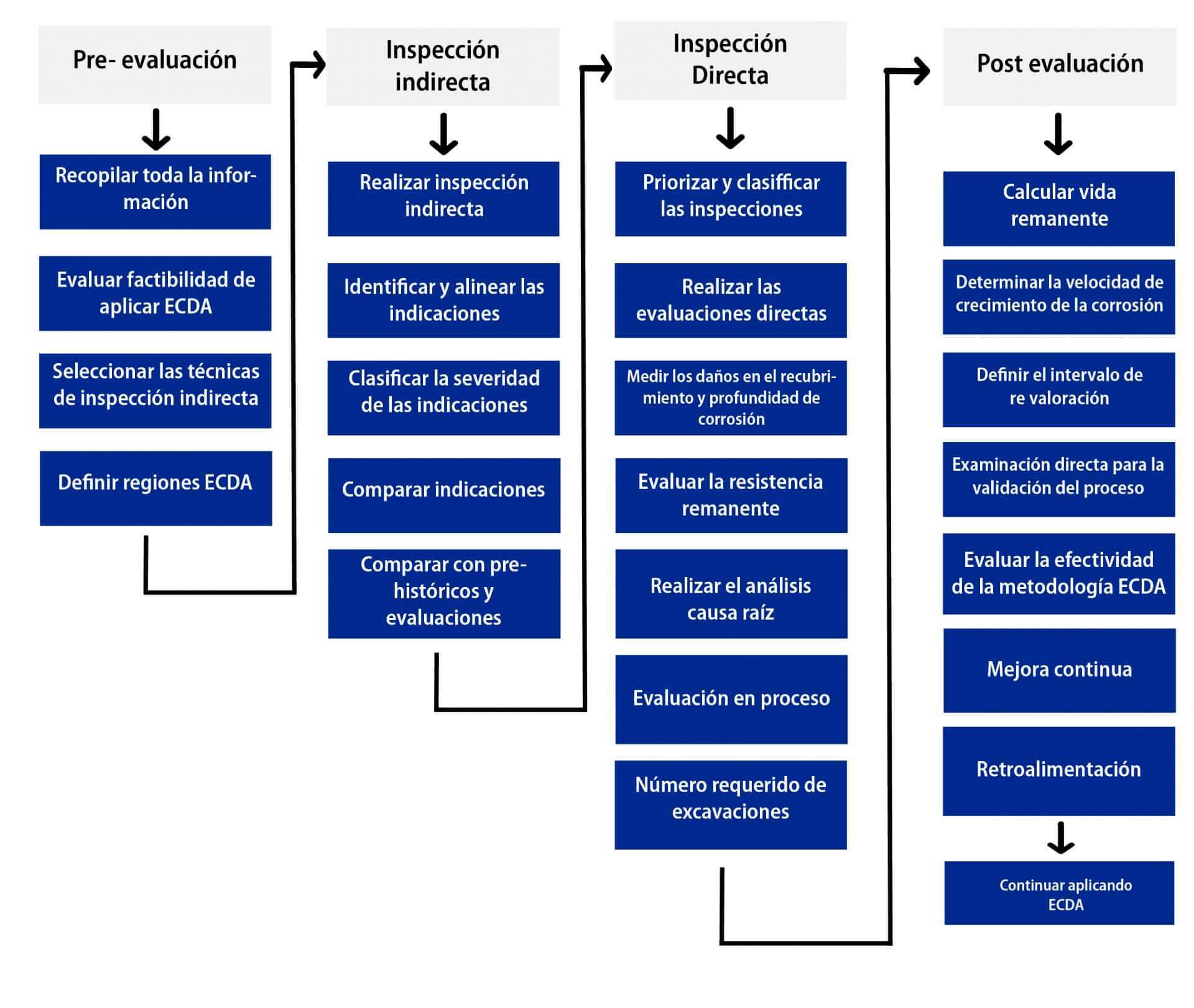
Figure 2 shows an illustrative image of the 4 stages of the methodology to be followed during the Direct External Corrosion Assessment (ECDA). However, in the following forum we will delve a little more in detail in the explanation of this cathodic protection evaluation method.
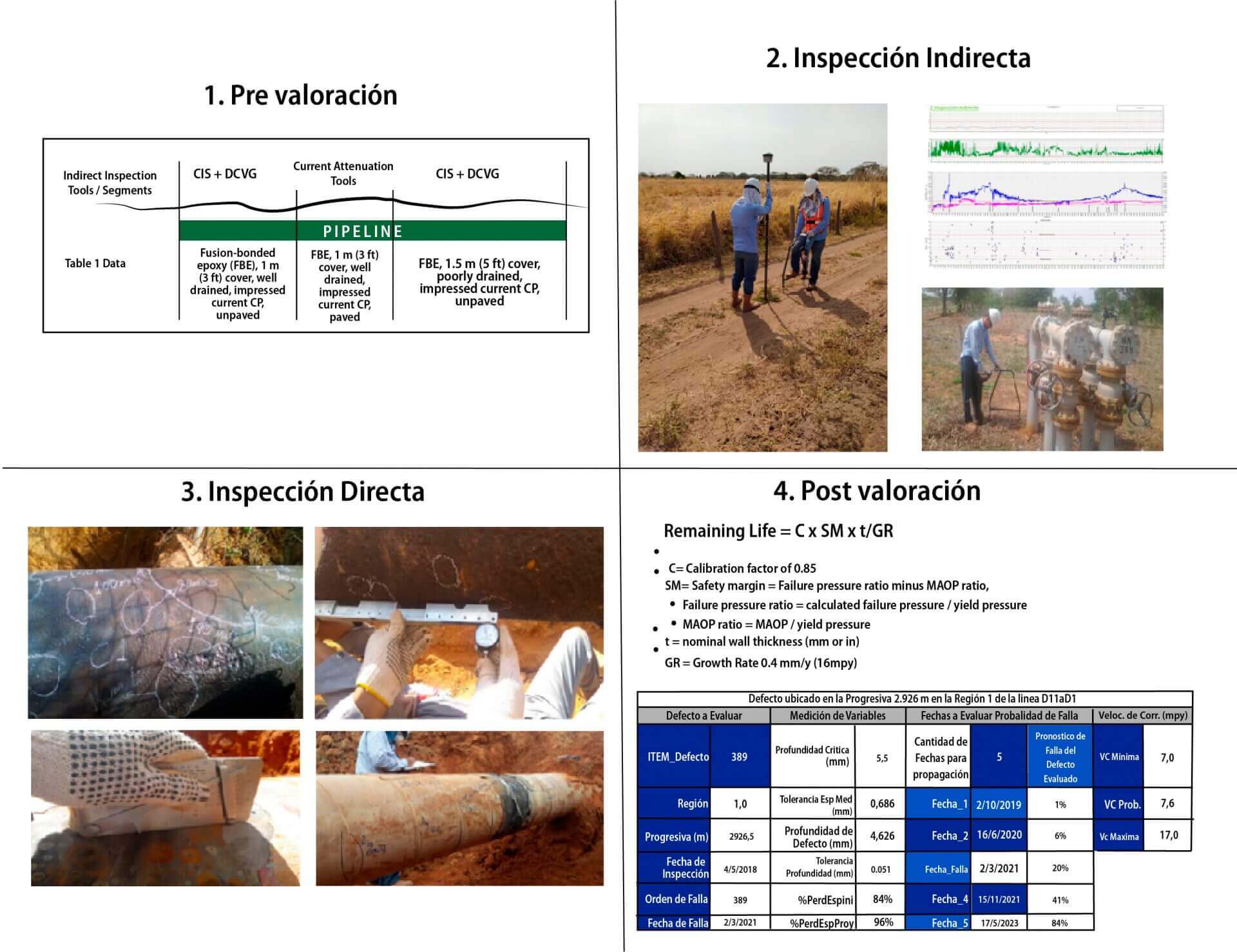
Conclusion
Currently, the intelligent piston inspection is one of the most reliable tools to know the state of the integrity of a pipeline. However, it is very common that either due to piping design problems, system operation restrictions or simply due to economic problems, the operator must look for alternatives to the intelligent piston passage.
Bibliographic references
- SP0502-2010 ANSI NACE SP0502-2010 Pipeline External Corrosion Direct Assessment Methodology.
- ASME B31G-2012.Manual for Determining the Remaining Strength of Corroded Pipelines
- American Petroleum Institute, API. STD 1160 Managing System Integrity for Hazardous Liquid Pipelines. 2013.
- Kim, Y. G., Won D. S., Song H. S., 2008. Validation of external corrosion direct assessment with inline inspection in gas transmission pipeline. In: 2008 NACE Corrosion Conference & Expo. Paper 08136.
- Pachon J. (2020). Tecnología Total. Presentación Webinar Julio 16,2020
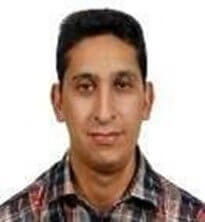
Author: Orlando Salas Ing. Chemist, M.Sc. Corrosion, Ph.D. NACE CP3 Cathodic Protection Technologist #9622. Instructor NACE CP1 and CP2. Email: orlandosalasa@gmail.com
Para más artículos https://inspenet.com/articulos/