Introduction
The maintenance and inspection of wind turbine blades are significant to ensure the life and efficiency of the turbines. Composite materials, preferred for their high strength-to-weight ratio and resilience against environmental factors, are commonly used in the manufacture of these components. However, its complex structure poses challenges for inspection.
Phased Array Ultrasound (PAUT) has emerged as a powerful non-destructive testing (NDT) method to address these challenges, providing deep detail on the internal condition of composite wind turbine blades without causing damage.
The importance of wind turbine blade inspection
Inspecting blades are subject to a variety of stressors such as: wind shear, UV exposure, humidity and temperature fluctuations, which can cause various forms of degradation and failure over time. Regular inspection is crucial for early detection of potential problems, allowing timely repairs or replacements to avoid catastrophic failures and maximize wind turbine efficiency. Traditional NDT methods often fail to effectively detect defects within the complex internal structures of composite blades, making advanced techniques such as PAUT essential.
Sections of wind turbine blades
Wind turbine blades are mixed structures, which mainly include the cladding, the wing and web of the beam (spar) and other structural units. Among them, the flange and web of the beam or spar are the main support structure of the entire blade, which is responsible for controlling the blade’s overall stiffness (deflection performance), ultimate strength (bearing performance) and shear strength performance. In addition, the non-load-bearing or secondary load-bearing structure of the skin casing is mainly used to form the aerodynamic shape of the blade1.
Composite materials in wind turbine blades
Composite materials used in wind turbine blades typically consist of layers of glass or carbon fiber reinforced polymers embedded in a resin matrix. These materials offer excellent mechanical properties but their heterogeneity and anisotropy introduce complexities in defect detection. Delaminations, voids and fiber breakage are common problems that can significantly impact structural integrity and blade performance.
Figure 1 shows the typical shape of a wind turbine blade structure made of composite material2.
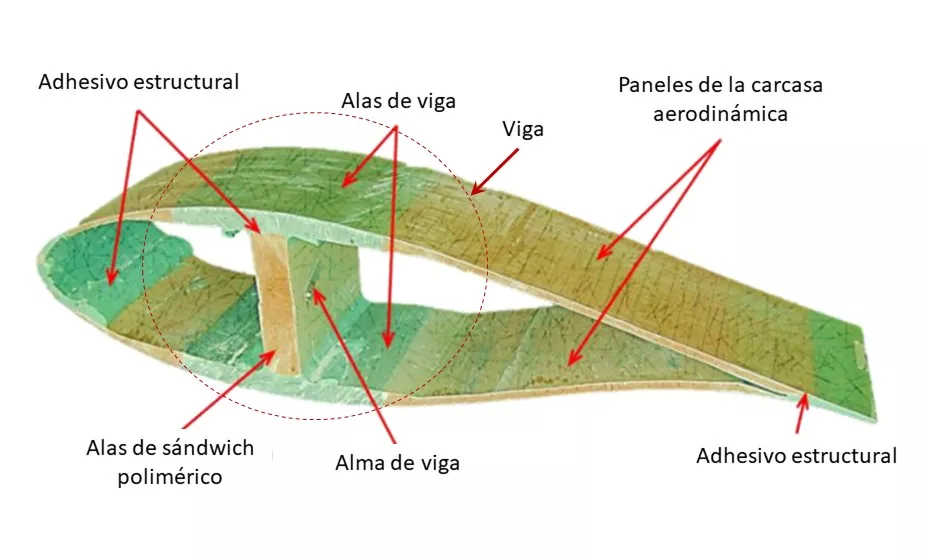
Understanding Phased Array Ultrasound (PAUT)
PAUT is an advanced ultrasound technique that uses multiple ultrasonic elements arranged in an array. Each element can be pulsed individually with controlled timing (phase), allowing the ultrasound beam to be directed, focused and swept across the inspection area. This flexibility allows full coverage of complex geometries, such as those found in composite wind turbine blades, and provides high-resolution images of the internal structure.
The PAUT inspection process
The inspection process with the phased array ultrasonic technique involves several steps:
- Blade surface preparation: The blade surface is prepared to ensure optimal contact with the ultrasound probe, often requiring cleaning and the application of a couplant.
- Calibration of the equipment: The different parameters of the equipment are adjusted so that it shows the different representative views of the component, with the necessary sensitivity and correct location and dimensioning result values. In order to obtain reliable results, a replica of the blade to be inspected is required, including artificially induced flaws such as porosity, non-bonding or delaminations3.
- Scanning: The PAUT probe, connected to sophisticated software, moves over the blade, emitting focused ultrasonic waves that penetrate the composite material.
- Data Acquisition: Echoes returned from defects or features within the material are captured by the probe and processed by the software to create detailed images of the internal structure.
- Analysis: Specialists analyze these images to identify and evaluate any defects, using their characteristics to determine the type and severity of the problems present.
- Reporting: Findings are documented in detailed reports that include the location, type and severity of defects detected, along with recommendations for future action.
Figure 2 shows the PAUT test setup for the inspection of composite wind turbine blades (upper part) and the results of the sweep (lower part).
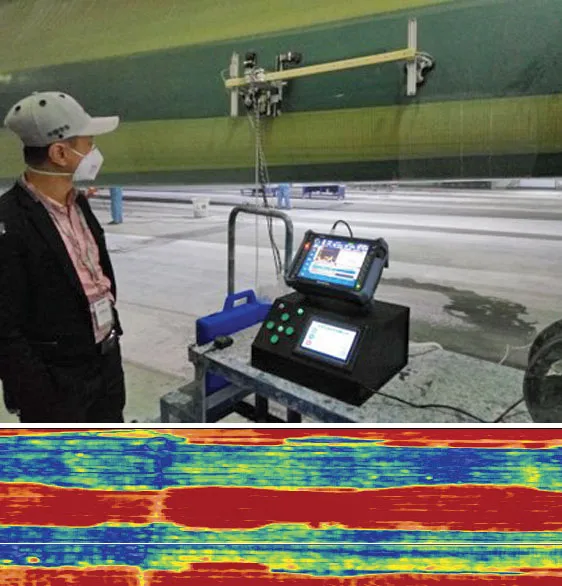
Types of failures in composite wind turbine blades
Composite turbine blades are prone to failures that can result from the blade design or the manufacturing process. Understanding the types of failures that can occur in composite shovels is crucial for effective inspection and maintenance:
- Delamination: Separation between layers of composite material, often caused by fatigue or impact, which can lead to a loss of structural integrity.
- Fiber breakage: Breaks in the reinforcement fibers, resulting in a reduction of the strength and stiffness of the blade.
- Wrinkles: Wrinkles are defects that usually appear during the manufacturing process of wind turbine blades. Wrinkles can arise at various locations on the structure, exhibiting a variety of different shapes.
- Matrix Cracks: Cracks in the resin matrix, which can allow moisture to enter and lead to further degradation.
- Voids and Porosity: Air pockets or voids within the composite material, which can occur during manufacturing and weaken the blade structure.
- Leading and Trailing Edge Erosion: Wear on blade edges due to environmental exposure, impacting aerodynamic performance.
It is important not only to identify and size these defects but also to characterize the width of the adhesive and its position between the beam and the casing4.
Advantages of PAUT in the inspection of wind turbine blades
The phased array ultrasonic technique offers several benefits over traditional inspection methods, particularly when dealing with composite materials in the evaluation of wind turbine blades:
- Enhanced detection capabilities: The ability to focus and steer the ultrasound beam allows the detection of small, complex defects that might be missed by other methods.
- High Resolution: The detailed images produced by PAUT provide a clear view of the internal structure, allowing an accurate assessment of the type and severity of defects.
- Versatility: PAUT can be adapted to inspect blades of various sizes and complexities, making it suitable for a wide range of turbines.
- Efficiency: Faster inspection times and the ability to process and analyze data immediately streamline the maintenance process, reducing downtime.
Below is a video explaining how to perform a robotic ultrasonic scanning of wind turbine blades (Source. Courtesy of: Aerones).
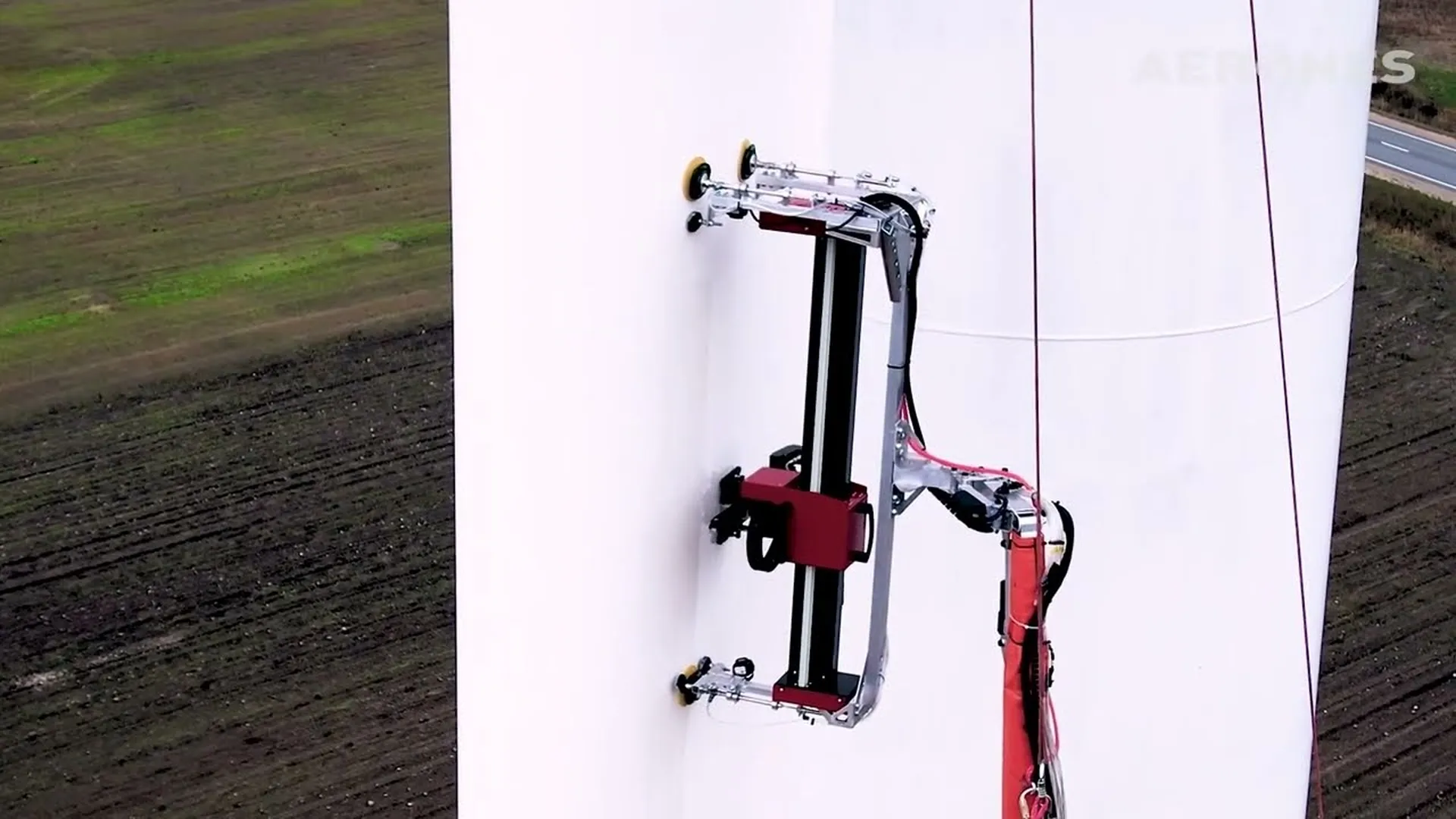
Escaneo ultrasónico robotizado de palas de turbinas eólicas | Aerones
Challenges and considerations
Despite its advantages, PAUT also presents challenges. The technique requires specialized equipment and trained operators, representing a higher initial investment than some traditional methods. In addition, interpretation of PAUT data can be complex, requiring expert analysis to accurately identify and assess defects in wind turbine blade evaluation.
Future Directions
As wind energy continues to grow, the demand for efficient and reliable blade inspection methods will increase. Innovations in phased-array ultrasound technology, including advances in transducer design and data processing algorithms, are expected to further enhance its capabilities. In addition, integrating PAUT with other NDT methods and data analytics could provide a more complete understanding of blade condition, enabling predictive maintenance strategies that minimize downtime and extend blade life.
Conclusion
Phased Array Ultrasound represents a significant advance in the inspection of composite wind turbine blades. Its ability to provide detailed and accurate assessments of internal structures makes it an invaluable tool for ensuring the safety, reliability and efficiency of wind energy production. As technology evolves, PAUT is destined to play an increasingly vital role in the maintenance and operation of wind turbines, supporting the sustainable growth of renewable energy.
References
- Hanwei Teng, Shujian Li, Zheng Cao , Shuang Li 1, Changping Li, and Tae Jo Ko. Carbon Fiber Composites for Large-Scale Wind Turbine Blades: Applicability Study and Comprehensive Evaluation in China; Accessed as of March 08, 2024; https://www.mdpi.com/2077-1312/11/3/624
- SOMIM. Mechanical Engineering Driving National Development and Innovation; Accessed on March 11, 2024; https://somim.org.mx/publicaciones/Libro_Ingenieria_Mecanica_Impulsando_el_Desarrollo_Nacional_ISBN.pdf.
- WAYGATE TECHNOLOGIES. 6 ways to simplify ultrasonic wind blade inspection; Accessed March 11, 2024. https://dam.bakerhughes.com/m/30fbda04e28b2eb0/original/BHW-13970_UTSP_WindBlade_e-Book_Final.pdf
- ANDRÉ LAMARRE. Inspection of Composite Turbine Blades with Ultrasonic Phased Array Technology; Accessed March 08, 2024. https://www.windsystemsmag.com/inspection-of-composite-turbine-blades-with-ultrasonic-phased-array-technology/#:~:text=Conclusion-,Ultrasonic%20phased%20array%20can%20be%20used%20to%20inspect%20wind%20blades,can%20be%20detected%20and%20sized.