Introduction
The safe and efficient handling of hydrocarbons is a critical area of focus in the hydrocarbon industry, particularly during the transfer of refined products using floating hoses. These must meet stringent safety and performance specifications to handle products like crude oil and its derivatives, where the risks of contamination and accidents are significant. This article discusses methods in the manufacturing of hoses for hydrocarbons, detailing how petroleum hose manufacturers design and produce solutions that meet the industry’s demanding needs.
What is a floating hose for hydrocarbon loading?
It is a type of flexible pipe used for the transfer or loading of petroleum products and other types of liquid hydrocarbons, especially in applications where mobility and flexibility are essential. These hoses are commonly used in the transfer of crude oil or refined products to or from tankers, single-point moorings, and oil platforms.
The distinctive feature of a floating hose is that it is designed to float on water, which is especially useful in maritime operations, and is engineered to withstand adverse environmental conditions, such as exposure to saltwater.
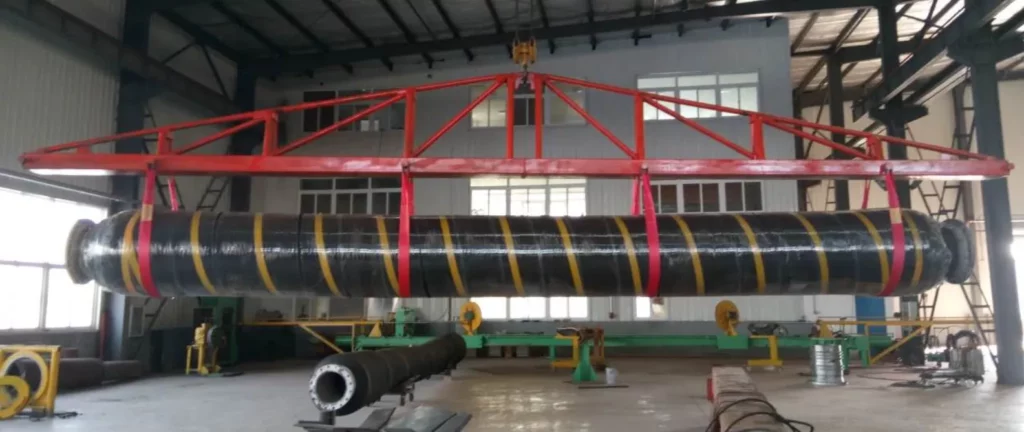
Types of Floating Hoses for Hydrocarbons
Single Carcass Floating Hose: These hoses consist of a sturdy outer carcass that protects the internal tube through which fluids flow. Their design is robust enough to handle adverse marine conditions and handling during operations, while also needing to be buoyant to facilitate handling and avoid excessive stresses at connection points.
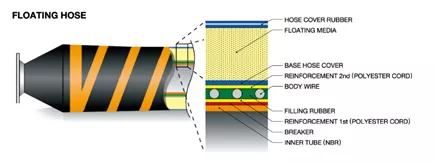
Double Carcass Floating Hose: These hoses incorporate all the features of single carcass hoses but with an additional layer of protection. This double carcass provides greater strength and safety, making the hose more suitable for even more demanding conditions or when handling particularly hazardous products. The additional outer casing protects against physical damage such as cuts or abrasions. In the event of the first carcass failing, the second one retains the product, preventing leakage to the exterior, where there are indicators that the first carcass has failed. Additionally, this construction enhances durability and hose lifespan.
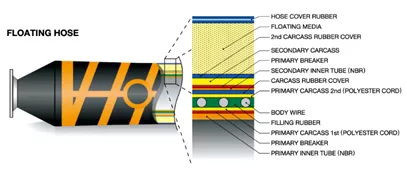
Fundamentals and considerations for the design and manufacturing of floating hoses
There are numerous types of hydrocarbon hoses designed by specialized manufacturers, who must adhere to design and manufacturing specifications dictated by established regulations and guidelines such as the GMPHOM (Guidelines for Manufacturing and Purchasing Hoses for Offshore Moorings) and the OCIMF (Oil Companies International Marine Forum).
These hoses are designed to handle a wide range of products, from heavy crude to refined derivatives. This variety demands especially robust structures capable of withstanding adverse marine environments, high operating pressures, corrosive effects of hydrocarbons, and fluid and weather temperatures. Below are some recommendations to be taken into account in the design and manufacture of hoses:
- Chemical compatibility: Floating hoses must be compatible with the types of hydrocarbons they will handle, resisting selection: Materials must be selected that not only resist the chemical action of hydrocarbons and external environments but also maintain their structural integrity under varied operational conditions. Internal layers are often made of hydrocarbon-resistant elastomers or plastics such as nitrile or polypropylene, providing an impermeable barrier and chemical resistance. External layers must be resistant to abrasion, weathering, and in some cases, flames. Materials such as neoprene and polyurethane are common in these applications.
- Pressure and mechanical strength: They must withstand maximum working pressure without risk of rupture or deformation, including adequate safety factors.
- Tensile and fatigue resistance: Hoses must withstand mechanical forces they will be exposed to during use, such as tension, torsion, and cyclic loads.
- Buoyancy and stability: Ensure the hose floats properly under all operational conditions. This may involve the use of materials with specific densities or the incorporation of flotation devices.
- Maneuverability: The hose must be sufficiently flexible and maneuverable to facilitate operations without compromising its buoyancy or functionality.
- Abrasion and wear resistance: Hoses must be capable of withstanding physical wear caused by contact with other objects, the seabed, or handling.
- Aging and environmental Resistance: It is crucial that hoses are designed to resist degradation from exposure to UV light, temperature, and the marine environment.
- Compliance with standards: The design must comply with relevant international regulations and standards and undergo the required processes to obtain GMPHOM 2009 certification.
- Safety features: Include features such as anti-static cables to prevent sparks and high-visibility elements to facilitate nighttime operations or low-visibility conditions.
- Ease of maintenance: The design should facilitate regular inspections and maintenance, including easy access to all critical parts.
- Economic viability: In addition to initial costs, the cost over the hose’s lifespan must be evaluated, including maintenance, repairs, and replacement.
Considerations for manufacturing
The manufacturing of oil hoses is a semi-artisanal process where design considerations must first be met, followed by the assembly of each part following the step-by-step process below3:
Assembly of the inner layer: The first layer is a polymer tube, such as nitrile or polypropylene, manufactured by extrusion, which is placed on a special lathe that will rotate at low speeds to facilitate the winding of each layer. This tube will be in direct contact with the hydrocarbon and must have the necessary chemical resistance to prevent degradation or dissolution when in contact with the fuel. Additionally, it maintains the structural integrity of the hose under different temperature conditions.
Incorporation of reinforcement layers: Adding layers of fabric or metal meshes to provide mechanical strength. These materials contribute mechanical strength to the oil hose, allowing it to withstand high internal pressures without bursting or collapsing. Additionally, they contribute to resistance against external abrasions and cuts.
Spiral or Weaving Winding: The spiral can be made of fibers or wires that are spirally wound or woven around the inner layer, connected with end flanges. This reinforcement structure helps maintain the hose’s flexibility while offering robust resistance to torsion and pressure, and also provides electrical continuity for electrically continuous hoses.
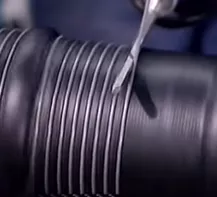
Wire winding process for hydrocarbon hoses
- Outer layer: This outer layer of modified rubber is resistant to abrasion, UV rays, and adverse marine conditions. It also provides flexibility and additional resistance to wear.
- Accessories and final assembly: Connections such as couplings and flanges at the ends of the hose will facilitate connection to hydrocarbon loading systems.

- Buoyancy: Incorporating buoyant elements, such as polyethylene foam within the hose structure or attaching external flotation devices, ensures that the hose can float on the water surface during loading operations. Facilitating handling and reducing the risk of submersion and damage from seabed dragging.
- Vulcanization: This process uses heat and pressure to bond the floating hose components, improving their elasticity and chemical resistance, and ensuring that all materials function as a cohesive unit.
- Hydrostatic testing and visual inspection: These tests ensure that the hose meets required safety and functional standards, verifying the effectiveness of materials and techniques used in previous steps. Visual inspection should be conducted throughout the manufacturing process, with hydrostatic testing performed at the end to ensure the hose can handle operating pressure without failure.
Below is a video showcasing information about the manufacturing of hoses for hydrocarbons, courtesy of Premierhose.
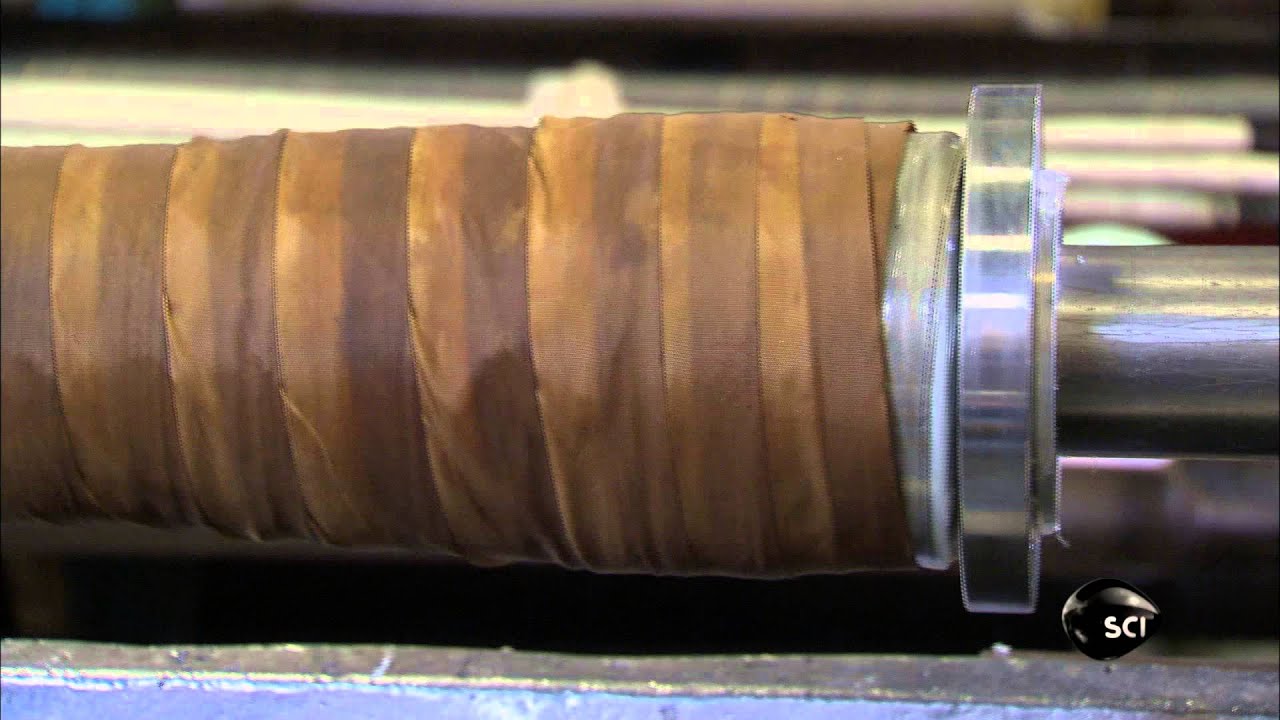
How are hoses for hydrocarbons manufactured?
Conclusions
The manufacturing of hoses for hydrocarbons is a specialized engineering area that plays a critical role in the safety and efficiency of the oil industry. From material selection to manufacturing processes, each step is vital to develop products that not only meet industry standards but also withstand the extreme conditions encountered in marine and offshore applications. Manufacturers of oil hoses continue to innovate in techniques and materials to enhance the functionality and safety of their products worldwide.
References
- https://www.floatinghosesllc.com/product/the-arctic-extreme-low-temperature-ice-protecton-marine-floating-hoses-for-crude-oil
- https://www.y-yokohama.com/global/product/mb/marine-hoses/design-features/
- GMPHOM-2009: Guide to Manufacturing and Purchasing Hoses for Offshore Moorings