Table of Contents
- What is structural integrity and why is it key?
- International standards applicable to structural integrity
- Common structural failure mechanisms
- Identification and control of structural damage in industrial assets
- Condition-based maintenance based on structural evaluation
- Technologies: NDT, digitization and predictive modeling
- Case studies: tangible impact of structural integrity
- API 2026 Industrial Inspection and Integrity Summit
- Conclusions
- References
Structural integrity is one of the fundamental technical pillars to ensure operational continuity, safety of physical assets and optimization of maintenance costs. Proper assessment and management makes it possible to anticipate damage, prevent failures and extend the service life of critical components.
In industrial environments such as oil & gas, power generation, petrochemical and mining, asset lifecycle management depends on a solid strategy based on data, technical standards and predictive technologies that consider the structural condition of equipment as a decisive variable.
What is structural integrity and why is it key?
Structural integrity refers to the ability of a component, structure or system to withstand loads, stresses and operating conditions without experiencing structural failure. It is not just a matter of avoiding breakage, but of ensuring that the asset maintains its functionality and safety throughout its life cycle.
Why is it key in physical asset management?
Because it allows:
- Preventing unplanned shutdowns: The shutdown of a refinery plant due to a ruptured gasoline pipeline.
- Avoiding catastrophic accidents: Fire of a storage tank in a refinery, with loss of assets and human resources.
- Optimize maintenance investments: Extension of a refinery plant run (longer production time).
- Justify replacements or redesigns: Guarantee the operational reliability of the unit and the safety of personnel and assets.
- Extend the useful life of critical assets.
For this reason, companies such as Aramco, Chevron or TotalEnergies integrate structural capacity criteria into their reliability and operational risk management systems.
International standards applicable to structural integrity
There are multiple standards that regulate and guide the integrity assessment of industrial equipment:
Standard | Organization | Main application |
---|---|---|
API 579 / ASME FFS-1 | American Petroleum Institute | Fitness-for-service analysis (FFS) |
ISO 55000 | International Organization for Standardization | Physical asset management |
NACE MR0103 / MR0175 | National Association of Corrosion Engineers | Stress corrosion evaluation |
ASME B31.8S | American Society of Mechanical Engineers | Pipeline integrity and critical infrastructure |
These standards provide the technical and legal framework to ensure the compliance and safety of assets in operation. You can consult them at:
Common structural failure mechanisms
A structural failure occurs when a component can no longer support the loads for which it was designed, either due to weakening, overloading or accumulated defects. These are some of the most common mechanisms in industrial environments:
1. Mechanical fatigue
- Description: It is produced by repeated cyclic loads that induce progressive cracks, even in materials with stress below the elastic limit.
- Example: Cracks in wind turbine arms after 10,000 load cycles.
- Related standard: ASTM E647 – Measurement of fatigue crack growth.
2. Stress corrosion cracking (SCC)
- Description: Combination of mechanical stress and corrosive environment. Affects alloys such as stainless steel and aluminum.
- Example: Chemical process piping cracked by chlorides and temperature.
- Related standard: NACE TM0177 – Test methods for SCC in H2S environments.
3. Thermal creep
- Description: Slow and progressive deformation of a material subjected to constant heat.
- Example: Deformed boiler tubes after operating >400 °C for long periods.
- Related standard: ASME Section II-D – High Temperature Material Properties.
4. Sudden impact or overload
- Description: Unforeseen or accidental loads exceeding structural capacity.
- Example: Collapse of steel beams after crane fall in loading area.
- Related standard: API RP 2A-WSD – Structural design for offshore platforms.
Identification and control of structural damage in industrial assets
Unlike a complete failure, structural damage represents a localized physical degradation that, although it does not stop operation, reduces the strength of the component and compromises its future integrity.
Common types of structural damage
- Surface cracks: Caused by fatigue, thermofluence or defective welding processes.
- Widespread or localized corrosion: Material wear in areas exposed to moisture or aggressive chemicals.
- Loss of thickness: Due to erosion, abrasion or pitting in liquid/gas environments.
- Permanent deformation: Bending or buckling indicating plasticization due to overloading or accident.
Examples of damaged assets
- Storage tanks with dented walls after overfilling.
- Corroded steel beams in uncoated chemical plant structures.
- Pipeline supports with radial cracks due to atmospheric corrosion in coastal areas.
- Storage tanks with inclined settlement, produced when one side of the tank descends more than the other, generating an angle of inclination with respect to the vertical axis (see figure 1).
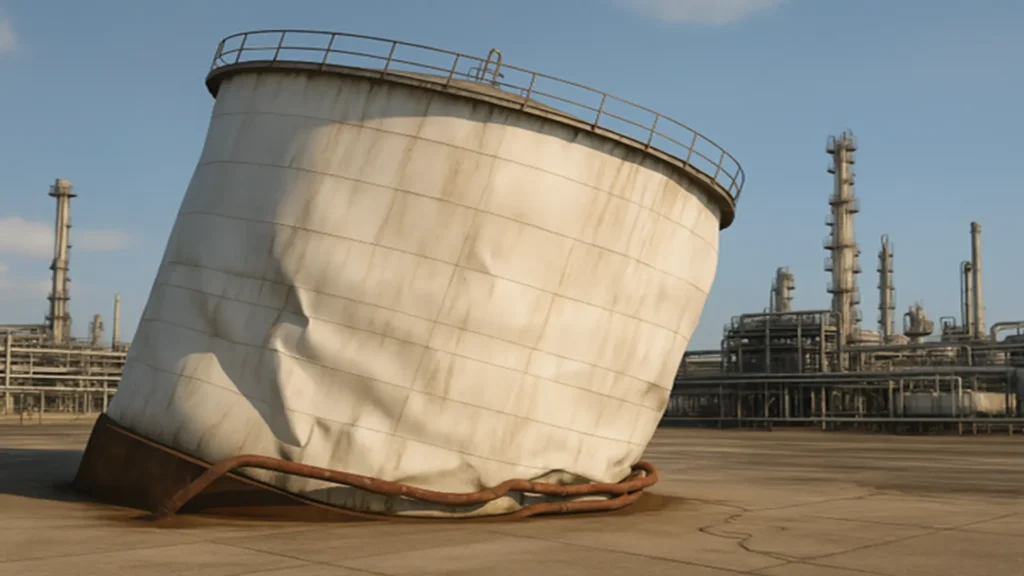
Recommended inspection methods
- A-scan/B-scan ultrasound to measure thickness loss.
- Digital radiography to identify internal defects.
- Acoustic emission to detect crack propagation activity.
- 3D laser scanner to compare actual geometry vs. design.
Applicable norms and standards
Norm / Standard | Technical approach |
API 653 | Storage tank inspection and repair. |
API 570 | Inspection of pipelines in service. |
ISO 9712 | Qualification of personnel for NDT. |
ASME PCC-2 | Repair methods for pressurized components. |
Condition-based maintenance based on structural evaluation
Structural evaluation as a basis for maintenance decisions is a widespread practice in the most advanced industries. It consists of:
- Apply non-destructive testing (NDT) to detect cracks, loss of thickness or hidden defects.
- Use finite element analysis (FEA) simulations to calculate critical stresses.
- Compare against codes such as API 579 to determine if the component is “fit for service”.
This approach facilitates the optimization of the life cycle of critical components, aligning maintenance decisions with the actual condition of the asset.
Technologies: NDT, digitization and predictive modeling
The integration of NDT and computational modeling into asset strategy has improved the way industrial equipment is managed. Some outstanding tools:
- Advanced phased-array ultrasound: for volumetric inspection of welds.
- Eddy current and TOFD techniques: for crack detection in metallic components.
- CFD and FEA models: to simulate extreme conditions and predict critical points.
- SCADA + IoT + AI: to perform predictive maintenance from real-time operational data.
Companies such as Schlumberger and Wood integrate these technologies into their integrity management platforms, reducing costs and improving decision making.
For a practical overview of how asset integrity management is implemented in the industry, we recommend the following video courtesy of DGC Africa: Behind the Process: Asset Integrity Management.
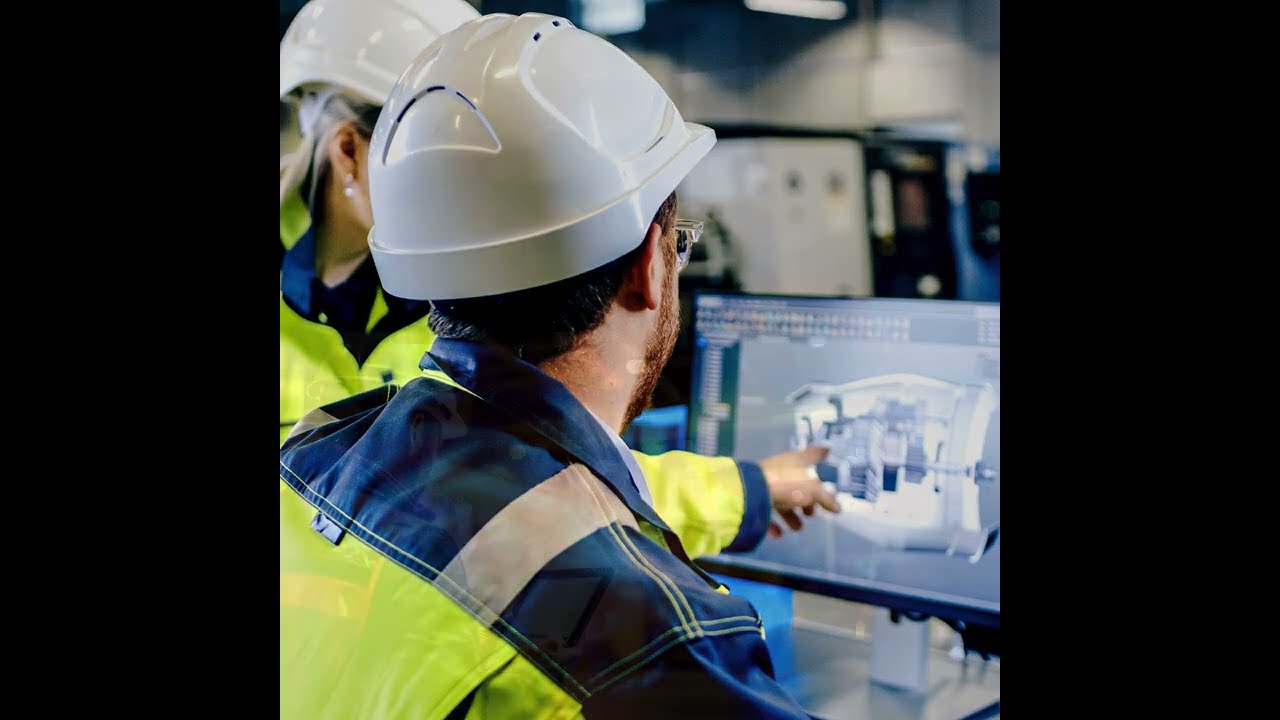
Asset integrity management.
This resource provides a clear perspective on modern strategies for maintaining structural integrity in industrial environments.
Want to see how these practices are applied in real scenarios? Watch this video and share your opinion with us in the Inspenet Community: together we build knowledge.
How is it linked to asset management?
ISO 55001 defines this management as the coordinated activity to obtain value from assets. Structural integrity directly influences:
- Reliability of physical assets.
- Safety of people.
- Business continuity.
- Regulatory compliance.
Therefore, keeping detailed records of inspections, mechanical failure histories, and service life projections is critical to efficiently manage complex industrial facilities.
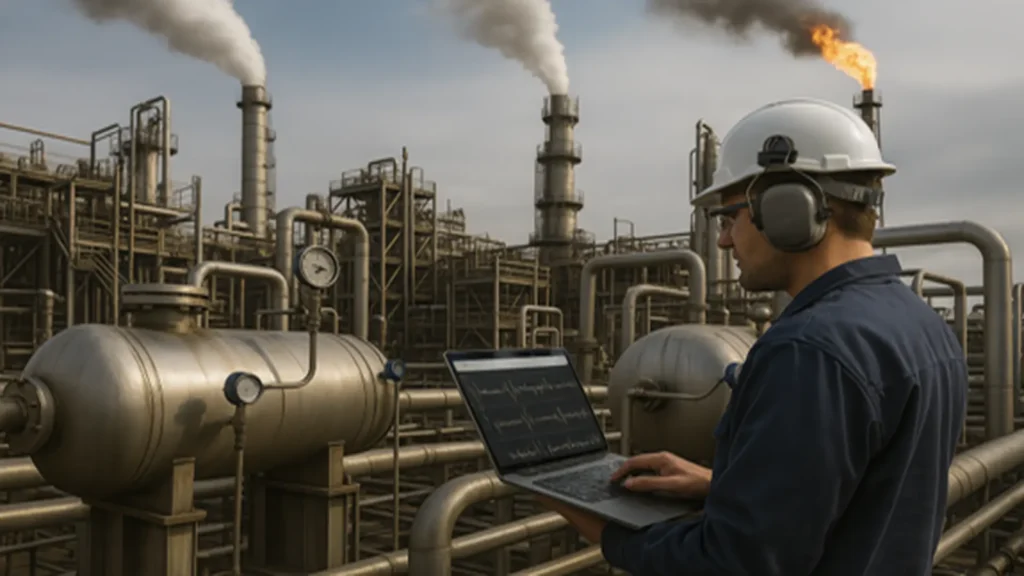
Case studies: tangible impact of structural integrity
Ensuring operational continuity, safety of physical assets and optimization of maintenance costs in industrial facilities depends on proper assessment and management of structural reliability. This makes it possible to anticipate damage, prevent catastrophic failures and extend the useful life of equipment. However, when this aspect is neglected, risks materialize with technical, economic and human consequences of great magnitude.
The following are three real cases that illustrate the direct impact of effective or poor structural reliability management:
Cooling tower collapse in Mexico (2022)
On March 1, 2022, a cooling tower at the Merida II thermoelectric plant, operated by the Federal Electricity Commission (CFE), partially collapsed. Workers had previously reported the urgent need for maintenance on the structure. Fortunately, no injuries were reported, but Unit 2 of the plant was temporarily out of service. The CFE initiated an investigation to determine the causes of the accident.
Pipeline explosion in Tlahuelilpan Mexico (2019)
On January 18, 2019, a clandestine outlet in a Pemex pipeline in Tlahuelilpan, Hidalgo, exploded while dozens of people were collecting fuel. The incident resulted in at least 66 dead and more than 70 injured. This tragic event underscored the dangers associated with clandestine outlets and the need for rigorous pipeline integrity management.
Extending the useful life of turbines in Chile
A study on the optimization of Francis turbines in Chile was presented at the World Congress on Maintenance 2025. Using 3D scans, finite element analysis (FEA) and computational fluid dynamics (CFD) simulations, areas of wear and cavitation were identified. These techniques allowed adjusting maintenance programs and extending the useful life of critical components.
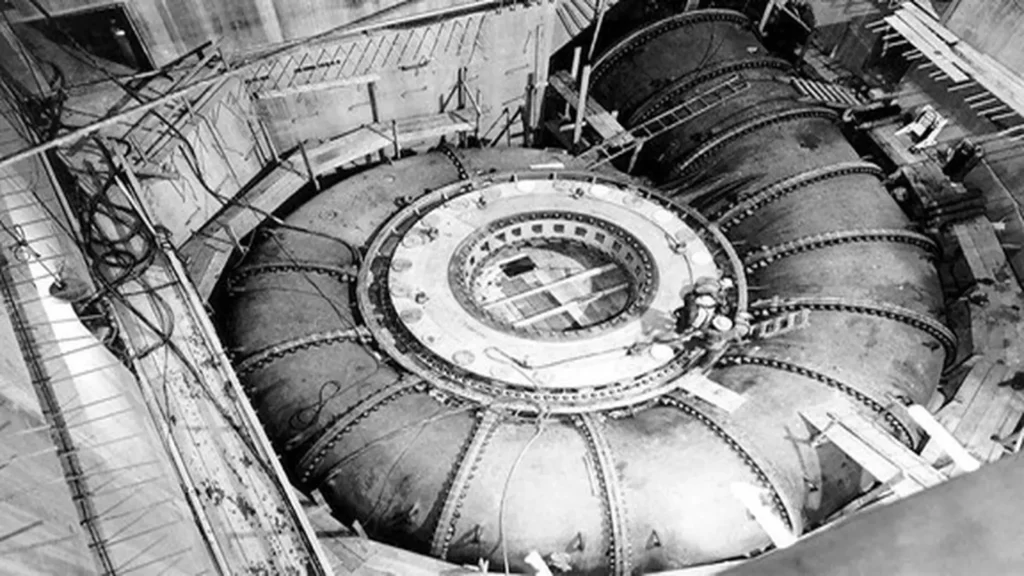
API 2026 Industrial Inspection and Integrity Summit
Topics such as structural capacity assessment, mechanical damage, fatigue failures or predictive inspection strategies will be protagonists in the next API Inspection and Mechanical Integrity Summit 2026, the most relevant international technical conference on inspection and mechanical integrity. This event brings together professionals from around the world to discuss experiences, key standards such as API 579, API 570 and API 653, digital twins, remote monitoring and industrial asset management. Learn more about the official event here.
Conclusions
Structural integrity represents an operational necessity. In an industrial environment where margins, safety and sustainability are crucial, anticipating structural damage and preventing structural failure translates into clear competitive advantages. Adopting predictive technologies, aligning with international standards and making data-driven decisions enables organizations to optimize asset management and maximize the return on infrastructure investment.
“A safe, reliable and long-lasting asset starts with a structure of integrity.”
This article is part of the editorial line of Inspenet, official media partner of global events such as API, AMPP, ASNT, GASTECH and others. If you found it useful, we invite you to share it on LinkedIn or WhatsApp, leave your opinion in the Inspenet community, or sign up for our specialized technical courses to learn more about these topics.
References
- Energy & Commerce: Cooling tower collapses at CFE thermoelectric plant: sipse.com+6energyandcommerce.com.mx+6fersalvador.com+6
- France 24: Explosion at a clandestine fuel pipeline leaves several dead and injured in Mexico: france24.com
- World Maintenance Congress: Optimization of Francis turbines through computational modeling.
- American Petroleum Institute (API). (2021). API 579-1/ASME FFS-1: Fitness-For-Service. 3rd Edition. API Publishing Services. Key standard for fitness-for-service (FFS) evaluation.
- American Society of Mechanical Engineers (ASME). (2022). ASME B31.8S: Managing System Integrity of Gas Pipelines. New York: ASME. Pipeline integrity and critical infrastructure.
- International Organization for Standardization (ISO). (2014). ISO 55000: Asset management – Overview, principles and terminology. Geneva: ISO. International base standard for physical asset management.