Table of Contents
Introduction
In the oil and gas industry, operational safety and efficiency are paramount. The concept of “Fitness For Service” (FFS) refers to evaluating the operational capacity of industrial equipment and components under specific conditions, ensuring they can operate safely and effectively throughout their service life. Asset integrity management (AIM) complements this approach by monitoring and maintaining asset conditions, guaranteeing optimal performance and minimizing risks.
The importance of this article lies in the critical need to implement FFS strategies in the petroleum sector, where assets are exposed to extreme conditions and rigorous operational demands. Understanding and applying FFS not only enhances the safety and reliability of operations but also optimizes costs and efficiency in the long term, providing a competitive edge in a highly regulated and competitive market.
Fundamentals of Fitness For Service (FFS)
Fitness For Service(FFS) is a technical evaluation process that determines whether an industrial equipment or component can continue in service under specific operational conditions without compromising safety. The main objectives of FFS include identifying defects and damages, assessing their impact on structural integrity, and recommending corrective or mitigation actions to ensure the safe operability of the equipment.
The FFS concept has evolved significantly since its introduction in the industry. Initially, it focused on assessing visible and superficial damages. Over time, more sophisticated standards and methodologies have been developed.such as API 579-1/ASME FFS-1, which provides a comprehensive framework for assessing defects and damages in pressurized equipment. This standard incorporates advances in material technology, non-destructive testing (NDT) techniques, and stress analysis, allowing for more precise and detailed evaluations.
The following video summarizes essential aspects of the FFS methodology through API 579-1 and ASME FFS-1, to understand the principles that ensure the safety and efficiency of equipment and structures. Source:
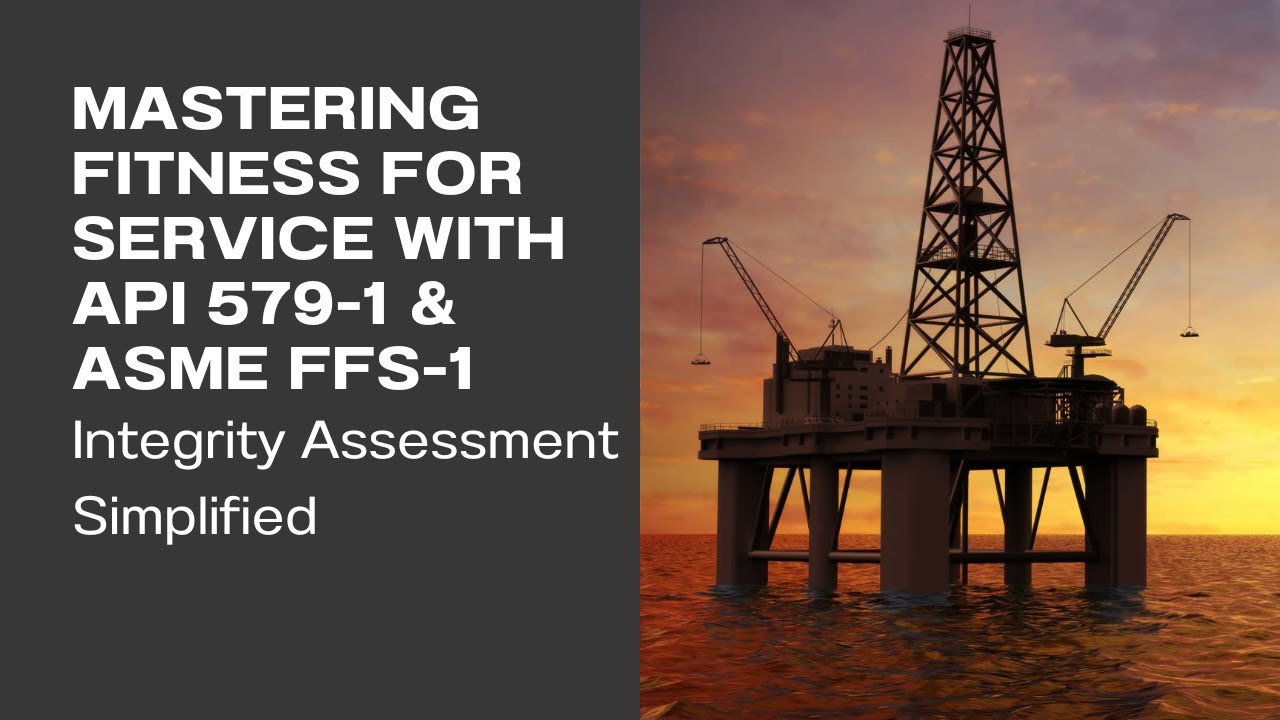
Fitness For Service control with API 579-1 and ASME FFS-1.
The evolution of FFS reflects the increasing complexity of industrial equipment and the need for more rigorous and precise evaluation methods. Today, FFS is an essential discipline in asset integrity management, helping companies maximize the service life of their assets, improve operational safety, and comply with increasingly stringent regulations in the oil and gas industry.
Key Standards and Regulations in FFS
The API 579-1/ASME FFS-1 standard, developed jointly by the American Petroleum Institute (API) and the American Society of Mechanical Engineers (ASME), is a comprehensive guide for assessing the structural and operational integrity of pressurized equipment. This standard applies to a variety of situations, including corrosion, cracks, deformations, and other types of damage in components such as pressure vessels, pipelines, and storage tanks. The standard is divided into multiple levels of evaluation, allowing engineers to perform both qualitative and quantitative analyses, from basic assessments to advanced analyses using finite element methods.
While API 579-1/ASME FFS-1 is widely used in North America, other international standards also regulate Fitness For Service evaluations. For example, the BS 7910 standard from the British Standards Institution (BSI) in the United Kingdom provides guidelines for assessing the structural integrity of metallic structures with defects. Similarly, the European standard EN 13445-4 includes procedures for evaluating pressure equipment. Although these standards share similar objectives with API 579-1/ASME FFS-1, there are differences in methodological approaches and specific requirements. API 579-1/ASME FFS-1 is known for its detailed and structured approach, while other standards may offer more flexibility in certain aspects of the evaluation.
Evaluation methodologies in FFS
In the realm of Fitness For Service, various methodologies are employed to assess the integrity of equipment. The most common methods include:
- Stress analysis: This method evaluates a component’s capacity to withstand operational loads without failing. It uses mathematical models and simulations to determine the internal and external stresses affecting the structure.
- Corrosion evaluation: This involves inspecting and quantifying damage caused by corrosion. Techniques such as ultrasonography and visual inspection are used to identify affected areas and measure the residual thickness of the material.
- Fatigue analysis: This method examines the material’s ability to withstand repeated cyclic loads. It focuses on crack propagation and the component’s lifespan under fluctuating operating conditions.
FFS evaluations are supported by advanced technologies and specialized tools
- Simulation Software: Tools like ANSYS and ABAQUS allow for detailed finite element analysis, simulating the behavior of materials under various load and damage conditions.
- Non-destructive testing (NDT) Techniques: Methods such as ultrasonography, radiography, magnetic particle inspection, and eddy currents are essential for detecting and evaluating internal and surface defects without damaging the equipment. These techniques provide precise data on material integrity, facilitating informed decisions about service suitability.
Integrating these methodologies and technologies into a robust FFS program allows engineers to ensure the safety and operational efficiency of assets in the oil and gas industry, optimizing both the performance and the lifespan of critical components.
Implementation of FFS in petroleum assets
The implementation of Fitness For Service (FFS) in petroleum assets is a structured and meticulous process involving several key steps:
Initial Assessment
- Identification of critical assets and preliminary evaluation of their current conditions.
- Collection of historical operation, maintenance, and failure data.
Inspection and data collection
- Use of non-destructive testing (NDT) techniques such as ultrasound, radiography, and eddy currents to collect precise data on asset conditions.
- Structural integrity evaluation through detailed measurements.
Analysis and evaluation
- Application of stress, corrosion, and fatigue analysis models using advanced software like ANSYS or ABAQUS.
- Determination of the asset’s residual capacity to continue in service under current operating conditions.
Development of mitigation strategies
- Definition of corrective and preventive actions to mitigate identified risks.
- Planning necessary repairs, replacements, or modifications.
Integration with existing systems
- Integration of FFS results with asset integrity management (AIM) systems and predictive maintenance programs.
- Updating databases and asset management systems to reflect FFS evaluations.
Case studies and practical examples
A notable example of successful FFS implementation is the management of subsea pipelines on a North Sea oil platform. A combination of remote visual inspection and ultrasound was used to assess the integrity of corroded pipelines. Detailed data analysis identified critical segments requiring immediate attention. The application of FFS prioritized repairs, avoiding a potential catastrophic failure and optimizing maintenance resources.
Another relevant case is a refinery in the Gulf of Mexico, where implementing FFS in hydroprocessing reactors helped identify incipient cracks caused by thermal fatigue. This allowed for planned interventions during scheduled shutdowns, avoiding costly unplanned downtime.
Benefits of Implementing FFS
Implementing FFS significantly improves operational safety by identifying and mitigating risks before they become critical failures. By detecting structural problems at early stages, preventive actions can be taken, reducing the likelihood of accidents and protecting both workers and the environment.
FFS enables more efficient management of maintenance resources. By focusing on the actual integrity of assets, repairs and replacements can be prioritized based on precise data, avoiding unnecessary expenses on components that still have considerable service life. This results in long-term operational cost savings.
The application of FFS ensures that assets operate in optimal conditions, increasing operational efficiency and reliability. Identifying and correcting defects before they cause interruptions allows for continuous production, minimizing unplanned downtime. Additionally, improving equipment reliability increases confidence in operations, favoring the planning and execution of large-scale projects.
Implementing FFS not only improves operational safety and efficiency but also optimizes resource use and ensures operational continuity, providing significant value for oil and gas companies.
Challenges and Solutions in FFS Implementation
Key Challenges
1. Technological
- Implementing FFS requires advanced inspection and analysis technology, which can be costly and difficult to integrate into existing systems.
- The precision and reliability of non-destructive testing (NDT) techniques can vary, affecting the quality of data obtained for FFS evaluations.
2. Operational
- Interrupting operations to perform inspections can be costly and impact production.
- Integrating FFS results into daily operations requires efficient coordination between different departments.
3. Organizational
- Resistance to change within organizations can hinder the adoption of new methodologies and technologies.
- The lack of trained personnel in FFS techniques and the use of advanced tools can be a significant obstacle.
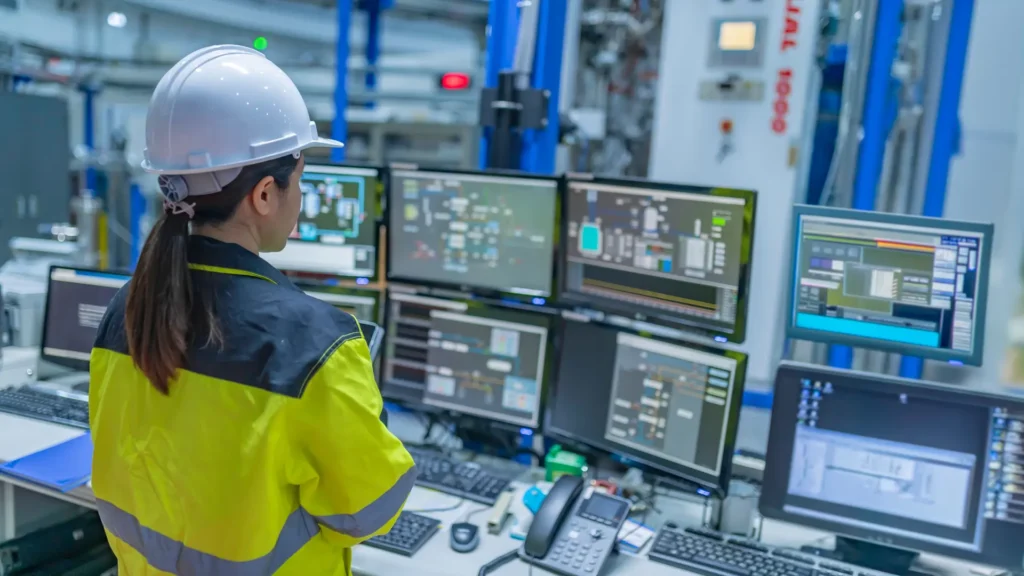
Solutions and best practices
1. Strategies
- Gradual Integration: Implement FFS gradually, starting with critical assets and expanding to other equipment over time.
- Automation: Use software tools to automate data analysis and facilitate integration with asset integrity management systems.
2. Training
- Training Programs: Develop specialized training programs for engineers and technicians in FFS techniques and the use of NDT technologies.
- Certification: Promote professional certification in relevant standards and norms, such as API 579-1/ASME FFS-1, to ensure knowledge and competence in FFS implementation.
Future of FFS in the oil and gas industry
Emerging trends
1. Artificial Intelligence (AI)
- AI is revolutionizing the ability to analyze large volumes of inspection data, improving the precision and efficiency in defect detection and failure prediction.
- Machine learning algorithms can identify patterns and anomalies that traditional methods may overlook.
2. Internet of Things (IoT)
- IoT-connected sensors allow continuous monitoring of asset health, providing real-time data on their condition and performance.
- The integration of IoT with FFS systems facilitates the implementation of predictive and proactive maintenance, reducing the risk of unexpected failures.
3. Digitization
- Digitizing inspection records and data improves accessibility and analysis of historical information, supporting more informed and rapid decisions.
- Digital platforms and digital twins enable the virtual simulation and evaluation of assets, optimizing maintenance strategy planning and execution.
Technological innovations
1. New inspection techniques
- Industrial Computed Tomography: Provides detailed images of the interior of components, allowing precise detection of internal defects.
- Infrared Thermography: Identifies thermal variations that can indicate structural or insulation problems.
2. Advanced methodologies
- Finite Element Analysis (FEA): Enhances precision in the evaluation of stresses and deformations in complex components.
- Predictive Modeling: Uses historical data and advanced algorithms to predict the remaining life of assets and plan maintenance interventions more effectively.
The adoption of these emerging trends and technologies is transforming the field of FFS, enhancing safety, efficiency, and profitability in the oil and gas industry, and ensuring that critical assets can operate reliably and safely throughout their lifespan.
Conclusion
Implementing Fitness For Service (FFS) in the oil and gas industry offers a wide range of critical benefits. First, it enhances operational safety by allowing the early detection of potential defects and failures, thereby reducing the risk of accidents and protecting both workers and the environment. Second, it optimizes costs and maintenance by enabling companies to prioritize repairs and replacements based on precise and detailed data, avoiding unnecessary expenses. Finally, it increases the efficiency and reliability of operations, ensuring that assets operate under optimal conditions and minimizing unplanned downtime.
The adoption of FFS is not just a recommendation; it is an imperative necessity for any company seeking to remain competitive and safe in the industrial sector. We invite all professionals and organizations in the oil and gas industry to collaborate and share knowledge in the implementation of FFS. This collaboration can lead to faster and more effective innovations, further enhancing the safety and efficiency of our operations.
Do not underestimate the power of FFS in transforming your industrial operations. Act now to integrate these advanced methodologies into your asset management strategy.
References
Own source