Introduction
In the complex world of non-destructive testing (NDT), Near Field Array (NFA) tube testing has emerged as a technological breakthrough, especially for the inspection of ferrous and non-ferrous tubes for internal surface inspection, and especially for tubes with air cooler fins.
This innovative method employs electromagnetic testing principles to discover and characterize defects within tube walls, offering unprecedented insights into the health of critical industrial components.
This comprehensive guide delves into the nuances of near-field array tube testing, shedding light on its principles, benefits, applications and the challenges it faces. To understand the NFA technique it is necessary to explain it and compare it briefly with the predecessor and still widely used electromagnetic technique of the Near Field Test or NFT.
Understanding the Near Field Array Assay NFA
Tube testing with NFA is a state-of-the-art technique in the NDT landscape, designed to identify and evaluate internal failures in tubular structures and evolved from the predecessor Near Field Testing (NFT) technique, so we will explain the latter beforehand.
NFT probes for near-field testing measure lift-off or “fill factor” and convert it into amplitude-based signals (without phase analysis)2. NFT technology uses two coils: a transmitter and a receiver. Usually, the receiver coil is close to the transmitter coil, taking advantage of the transmitter’s near-field area. In the area where the magnetic field of the transmitter coil induces strong Eddy currents, axially and radially, in the tube wall, as opposed to the Remote Field Electromagnetic Test (RFT), where the probe is located at a distance beyond two and a half inner diameters of the tube, an area known as remote field.
NFT probes operate within the same frequency range as RFT3 probes. Because eddy current penetration is limited to the inner surface of the tube. They are specifically designed for the inspection of finned carbon steel tube fan coolers, unaffected by fin geometry on the outside of the tube and detection of internal corrosion, erosion or pitting in carbon steel tubes when only these types of failures are expected to be found as a cost-effective solution.2 .
An improvement on the traditional near field method (NFT) is the near field array (NFA) technique in which the probe has an array of coils. NFA uses a technique similar to that of ECA (eddy current array testing) in which it makes use of a series of coils (up to 30 coils) that are activated in sequences. Unlike conventional eddy current tests, NFA tests use additional tangential coils that help to obtain detailed data and discontinuities in all directions.
The following is the video on the detection of small volumetric defects in finned fan air coolers using Near Field Array (NFA) Probes. Source: Eddyfi Technologies.

Near Field Array (NFA) probes.
This is where the information of the NFA matrix comes to light: its additional mapping of the tube provides more information about the defect morphologies and thus a better assessment of the detected indications4.
NFA assessment software allows NFA pipe test data to be displayed and reported in 2D and 3D “C” scan format for corrosion mapping that can help asset owners make informed decisions based on the specific location of the discontinuity and the accuracy of the discontinuity.
At its core, NFA tube testing is based on the interaction between the electromagnetic field generated by a probe equipped with an array and the material under inspection. The probe, composed of several coil elements, is passed through the tube and generates an electromagnetic field which, upon encountering faults (corrosion, erosion, pitting, cracks), undergoes alterations. These changes are detected and analyzed, providing detailed information on the nature of the faults and its major advantage being a presentation of the corrosion mapping in both 2D and 3D.
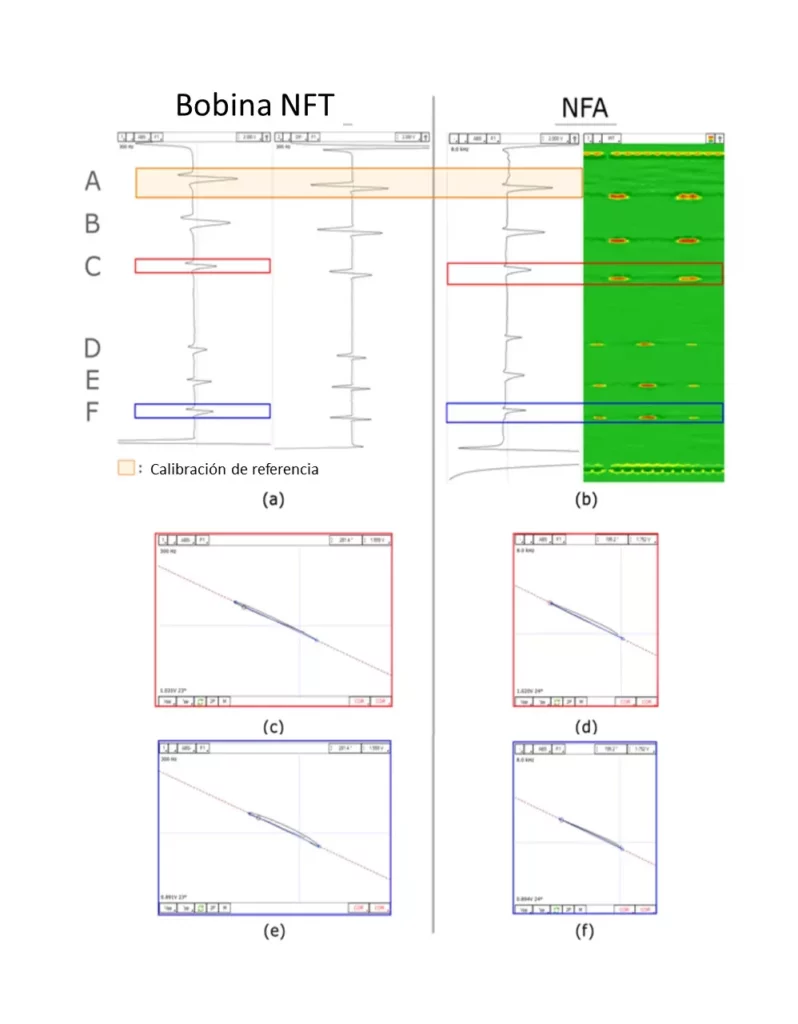
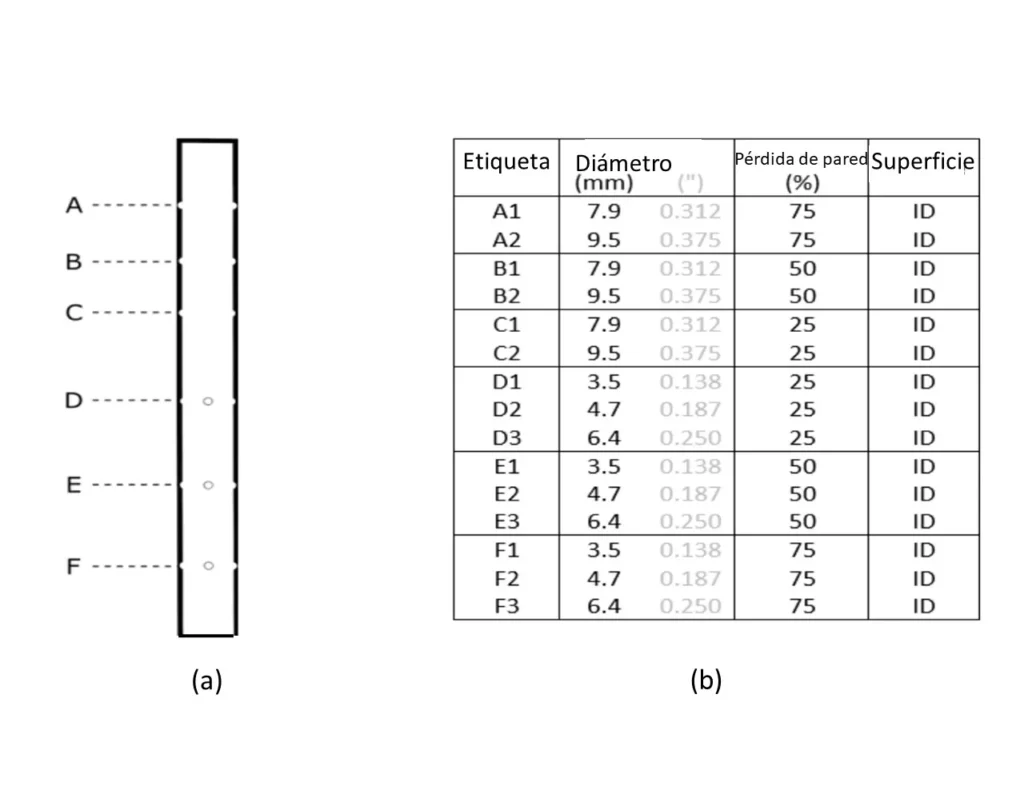
Key Components of the Near Field Array Assay
- NFA Probe: Incorporates multiple coils in an array, each capable of independently emitting and receiving electromagnetic signals, allowing high-resolution imaging of faults.
- Data acquisition system: Collects, processes and displays signals from the NFA probe, using specialized software for data analysis.
- Tube guide and encoder: Facilitates precise navigation of the probe inside the tube and tracks its position, ensuring accurate location of detected faults.
Advantages of the Near Field Array Assay
The NFA tube tests stand out for their:
- High sensitivity and resolution: Detects minor faults, outperforming conventional methods. It can accurately measure volumetric discontinuities of approximately 3 mm in a single pass.
- Efficiency: Allows faster inspections, examining tubes in a single step. It can comfortably scan at 6 meters per minute, reducing heat exchanger maintenance time.
- Improved fault characterization: Provides detailed information on the size, shape and orientation of faults through corrosion mapping. It can detect both axial and circumferential cracks.
- Material versatility: Effective on both ferrous and non-ferrous materials, broadening its scope of application.
- Inspection of finned tubes: As Eddy currents are concentrated on the inner surface of the tube, they are not affected by the fins attached on the outside, making it ideal for the inspection of air cooler tubes.
Challenges and Limitations of the Near Field Array Assay
Despite their advantages, NFA tests face limitations such as:
- They only detect internal discontinuities.
- Applicable only in ferromagnetic materials.
Industrial areas of application
NFA tube testing is invaluable for industries where tube integrity is crucial, including:
- Power generation: For inspections of boiler tubes to prevent failures.
- Petrochemical: In the revision of heat exchanger tubes in refineries to prevent leaks due to corrosion or erosion.
- Chemical manufacturing: To maintain the integrity of the process tubes, avoiding contamination and process interruptions.
Future perspectives
The future of Near Field Array finned tube inspections is promising, with continued developments in probe design, data processing algorithms and automation to further enhance its capabilities. Integration with other NDT methods could offer a detailed approach to industrial inspections, raising safety and operational efficiency to new heights.
Conclusions
Inspections of finned or ferrous tubes where internal imperfections are expected to be found with near-field matrix testing represent a significant advance in nondestructive tube examination, offering a blend of accuracy, efficiency and comprehensive diagnostics that is unmatched in the industry. Its ability to provide fast, accurate and detailed fault detection has made it an indispensable tool for maintaining the integrity of critical infrastructure.
As technology evolves, NFA testing is destined to play an increasingly important role in ensuring the safety, reliability and efficiency of industrial operations worldwide, safeguarding both assets and lives. With the continued development and refinement of this technology, NFA testing will contribute to safer, more reliable and efficient industrial operations for years to come.
References
- EDDYFI. Sizing Small Volumetric Defects in Fin-Fan Air Cooler Tubes; Accessed March 23, 2024. https://www.eddyfi.com/en/appnote/sizing-small-volumetric-defects-in-finfan-air-cooler-tubes
- APLUS. Remote Field Testing and Near Field Testing; Accessed March 24, 2024. https://www.applus.com/dam/PDFServices/Energy-and-Industry/GLOBAL/near-field-testing-and-remote-field-testing_en.pdf#:~:text=Typically%2C%20the%20receiver%20coil%20is%20close%20to%20the,within%20the%20same%20frequency%20range%20as%20RFT%20probes.
- EDDYFI: Near-Field Testing (NFT); Accessed March 25, 2024; https://www.eddyfi.com/en/technology/nearfield-testing-nft.
- ANTOINE GRÉGOIRE & DAVID AUBÉ. The Power of Near Field Array for Air Cooler Fin Fan Tube Inspection; Accessed March 26, 2024; https://blog.eddyfi.com/en/the-power-of-near-field-array-for-air-cooler-fin-fan-tube-inspection.
- EDDYFI. Near-Field Array (NFA); Accessed March 27, 2024; https://www.eddyfi.com/en/technology/nearfield-array-nfa.