This document represents a guide to guide the reader in the review, selection and inclusion of pipes and static equipment for an ongoing inspection program, for any Oil and Gas Industry; taking into account their criticality, construction materials, analysis and selection of process and laboratory variables that directly affect the degradation of equipment and lines (Operational Windows), mechanisms of deterioration of the materials that make up the pipes and static equipment and the maintenance program. Inspection that the owner has on these assets.
Introduction
By definition “ A piping/Equipment circuit or Corrosion loop ”. It is a section that includes the following points:
- All exposed points in a similar corrosive environment, similar design conditions and material of construction. Example “the discharge pipe of a pump to a heat exchanger”, carries the same product and where the material is carbon steel”.
- The same design operational conditions (temperature and pressure)
- The operational control variables are the same.
- The deterioration mechanisms always have the same behavior throughout the circuit, unless you have some restrictions that vary.
- It has the same direction of flow of the product or service it provides.
- Generally, in an Asset Inspection plan, it is represented through a plan that differentiates the ties or circuits by colors; in order to have them under strict control by installed metallurgy; as represented in Figure 1.
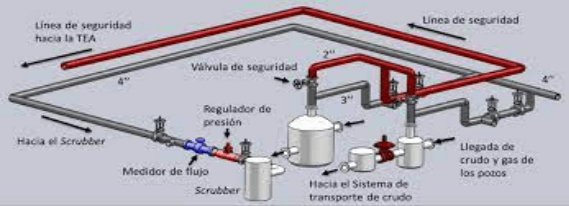
The piping system/equipment owner shall have control of the piping system inspection program, inspection frequencies, maintenance, and is responsible for the function of an authorized inspection body in accordance with the provisions of API 570. The owner’s inspection organization will also monitor activities that relate to the reassessment, repair, and alteration of its piping systems.
Identification of the Circuit or Corrosion Loop
- Name of the owner and of the plant where the circuit is installed.
- Identification number of the circuit according to the nomenclature of the owner. It is recommended that it be as complete as possible (company – plant-process – numbering).
- Circuit service (example: catalytic naphtha, gases, reduced oil, others)
- Circuit design and operation specifications and conditions (design and operation temperature, design and operation pressure, construction material and SCH. or commercial thickness, admissible corrosion, withdrawal thickness).
- Flow direction of the service or product transported by the circuit.
- The coordinates or sense of location.
- Limits of the operational windows. (for humidity control in Alkylation Units, fluid speed in any unit, operating temperatures, naphthenic acids in crude oil and others according to the processes managed by the owner.
Selection of the circuit or loop for the service provided
API 570 is applicable to piping systems for process fluids, hydrocarbons, and flammable or toxic fluid services similar to the following:
- Crude, intermediate and final petroleum products.
- Intermediate crude and finished chemicals.
- catalyst lines
- Hydrogen, natural gas, fuel gas
- Sour water and the flow of hazardous waste that are above the beginning of the limits defined by jurisdictional regulations.
- Hazardous chemicals above the beginning of the limits defined by jurisdictional regulations.
Circuit or Loop Selection by Operational Window
The objective of the operational window is to establish a direct relationship between the process that manages the circuit and the associated deterioration/degradation mechanisms, in order to be able to predict their effect on the mechanical integrity of the elements of the piping and equipment. plant.
To control this variable, a counter is used; which will control the maximum number of times that the variable can be outside the established limits, producing a level of degradation that can be detected by the inspection method used. Once this occurs, the loops affected by the variable must go from a normal inspection regime to an alarm regime, based on the predetermined criteria.
Inspection Plan according to the behavior of the Operational Windows
As you can see in this document-Guide, another element of vital importance is incorporated to preserve the useful life of the assets in a circuit; as is the inspection priority of one circuit with respect to another, by the activation of one of the components of the operational windows that are under control. Some owners define it as Measurement Regime and hence the names of “Critical Circuits with Special Measurement Regime”.
Shared responsibility of an organization for managing this inspection process
- The process engineer is responsible for preparing the list of circuits to be included in an ongoing inspection program under this model or guide described in this document, and this in accordance with the process variables indicated by the corrosion engineer.
- The Corrosion Engineer reviews the list of circuits issued by Process Engineering and selects the circuits to be included in the inspection program, assigning them control points, TML, CML or Inspection Zones.
- The Maintenance Engineer will support the work of the Equipment Inspector with the facilities required to execute the inspection program. These are: scaffolding, manlift, cranes, insulation removal and installation, others.
The Inspection Engineer, a qualified and certified professional according to the ASNT, will execute the inspection program according to the planning of the inspection program.
Conclusion
A good inspection program, supported by an analysis platform, good quality software and highly qualified and certified personnel to operate it; guarantees through this Inspection System: Operational reliability of the assets, safety and protection of the environment, planned marketing in the delivery of products, cost reduction by preventing failures that would generate unplanned expenses, zero penalties for late delivery of products and higher business profitability.
Bibliographic references
API 570 Code for Inspection of Pipelines
API 510 Code for Inspection of Pressure Vessels
API RP 571 Mechanisms of Deterioration that affect equipment
API RP 574 Inspection of Piping System Components
ASME B31.3 Process Piping
ASNT SNT-TC-1A Qualification and certification of personnel in non-destructive tests.
Visit our website to read more articles https://inspenet.com/en/articles/