Introduction
The operating principle of gas turbines is based on a positive feedback process. As the gas turbine increases its speed, it speeds up the compressor, which in turn pushes more air through the combustion chamber. This results in a higher combustion rate of the fuel, sending hot gases at high pressure to the gas turbine, which in turn further increases its speed.
This article discusses the performance characteristics of gas turbines and provides recommendations for minimizing degradation and deterioration through proper maintenance practices, aimed at both operators and maintenance specialists.
Operation and thermodynamic principles of gas turbines
A gas turbine, also known as a combustion turbine, is a machine that extracts energy from moving combustion gases. It consists of a compressor, a combustion chamber and a turbine, which work together. These turbines are used in a variety of applications, from power generation to propulsion of ships, locomotives and helicopters.
The operating process is as follows: Air, enters as a working fluid through the turbine inlet, is compressed in the compressor (adiabatic compression: no heat gain or loss), mixed with fuel and burned in the combustion chamber at relatively constant pressure (heat addition at constant pressure), creating a hot gas that expands. Finally, this hot gas drives the power turbine and generates mechanical energy, a representative image of this process is shown in Figure 1 (Figure 1).
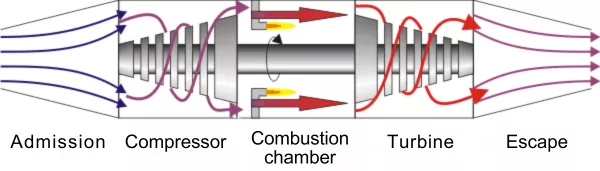
Model of thermodynamic behavior: Brayton (or Joule) Cycle
The Brayton Cycle is a cyclic process generally associated with a gas turbine, as an open system, although for thermodynamic analysis it is convenient to assume that the exhaust gases are reused in the inlet, allowing the analysis as a closed system.
Thermodynamically, the Brayton (or Joule) Cycle models the behavior of a turbine. The following is a description of each of the stages that make up this cycle. It consists of four reversible steps, as shown in Figure 2.
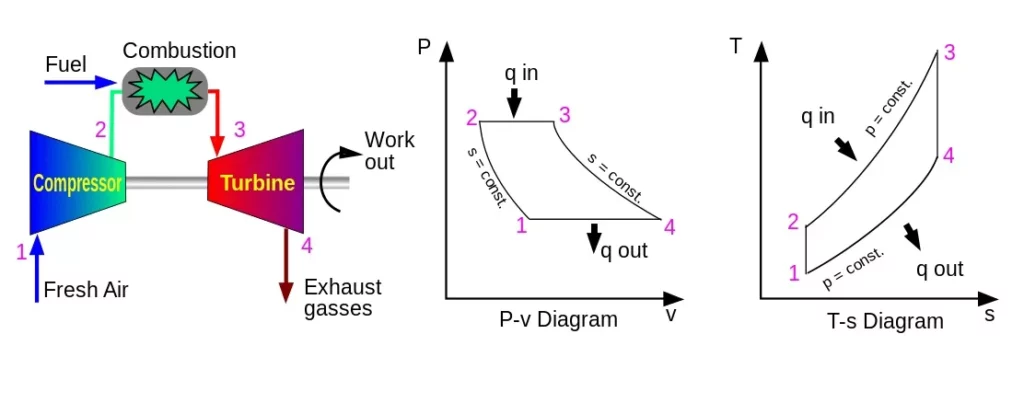
The thermodynamic stages of these processes are described below:
- Air intake: The process begins when air enters the turbine through its intake. This air acts as the working fluid throughout the operating cycle.
- Compression: Once inside the turbine, the air passes through the compressor. Here, the compressor increases the air pressure by compressing the air. This pressure increase prepares the air for entry into the combustion chamber.
- Combustion: After leaving the compressor, the compressed air is mixed with fuel in the combustion chamber. The fuel is then ignited, creating a combustion reaction that generates hot, high-pressure gases.
- Expansion and power generation: The hot gases resulting from combustion are expanded through the power turbine. This expansion drives the turbine blades, which are connected to a shaft. The mechanical energy generated by the rotation of the turbine is converted into electrical energy through a generator coupled to the turbine shaft.
Maximizing Brayton Cycle efficiency in gas turbines
The thermodynamic process known as the Brayton cycle is fundamental in the operation of gas turbines, optimizing their performance in a manner similar to the Carnot cycle. This cycle maximizes efficiency by increasing the pressure difference across the turbine, in contrast to the temperature difference in the Carnot cycle.
The power generated by gas turbines depends on multiple factors, including speed, firing temperature and management of secondary control elements. In the case of single-shaft gas turbines, the fuel flow control maintains a constant speed, while twin-shaft gas turbines allow the speed to be adjusted according to the needs of the process.
Restrictions on power output are usually linked to the maximum ignition temperature and the maximum speed of the gas generator. However, the efficiency of these turbines is less affected by ambient temperature variations compared to their power output.
For more information on this part of the topic I invite you to watch the following video courtesy of Solar Turbines, on the operation of a gas turbine using the Bryton Cycle.
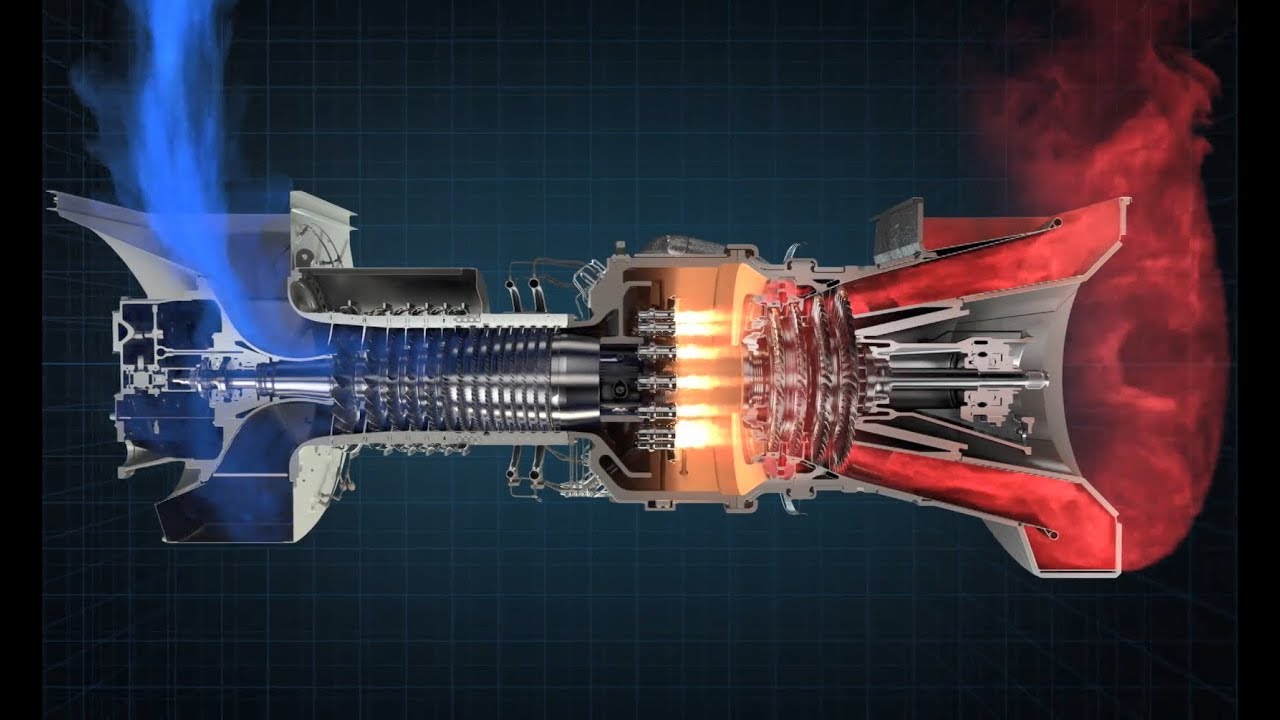
Operation of Gas Turbines.
Implementation of condition monitoring techniques in gas turbines.
Gas turbine operating processes are characterized by a number of attributes that reflect their functional state. In industrial environments, continuous data collection by means of numerous sensors makes it possible to observe the evolution of multiple variables over time, which facilitates the identification of different operating modes.
Traditionally, the definition of these modes has been based mainly on the expected energy production, often considering only one variable, such as the active load, or by assuming a predefined number of states and building. Predictive models to classify new situations within these predefined states, which allows the identification of operating modes that may not have been previously recognized. Furthermore, for effective gas turbine management, it is crucial to detect these modes in real time.
The selection of an appropriate set of condition monitoring technologies is based on failure modes, detailed engineering studies, and an assessment of the importance of the information in making critical decisions related to machinery operation. For large-scale and critical gas turbines, it is generally necessary to implement a combination of technologies to obtain optimal results.
Successful maintenance practices in gas turbines
- Periodic inspection program: Establish a regular inspection program to identify wear, corrosion, leaks and other problems on turbine components, including blades, casing, seals, bearings, and controls.
- Oil analysis: Periodically sample and analyze the turbine lubricating oil. Oil analysis provides information on the condition of bearings, gears and other components. Detecting abnormal contaminants or wear particles through this analysis can help address difficulties in a timely manner.
- Temperature monitoring: Monitor temperature trends throughout the turbine. High temperatures may indicate problems such as excessive friction, inadequate lubrication, among others. Addressing temperature irregularities in a timely manner can prevent damage and extend component life.
- Cleaning and fouling prevention: Keep turbine components free of debris, dirt, and deposits. Perform periodic cleaning of blades, inlet filters and cooling systems to ensure efficient operation and prevent performance degradation.
- Alignment and balancing: Ensure proper alignment and balancing of turbine components. Misalignment or imbalance can cause increased stress, wear and decreased efficiency. Periodically check and correct alignment to extend component life.
- Seal inspection: Monitor and replace worn or damaged seals in a timely manner. Proper seals are critical to prevent air or gas leaks, which can affect turbine efficiency and cause increased wear.
Strategies to maximize gas turbine operating life
- Component upgrades: Consider upgrading individual components, such as blades, seals and bearings, using more durable materials or designs. Upgraded components can offer superior performance and longer service life.
- Control system upgrades: Upgrade the control system to integrate advanced monitoring and automation features. This will allow real-time optimization of performance and early detection of potential problems.
- Improve the cooling system: Improve the cooling system to effectively regulate operating temperatures, preventing overheating, reducing thermal stress and extending component life.
- Increased efficiency: Explore upgrades focused on improving efficiency, such as aerodynamic improvements or flow optimization. Improved efficiency reduces stress on components and can extend overall turbine life.
- Materials upgrade: Upgrade turbine components with materials that offer increased resistance to corrosion, erosion and fatigue, which can significantly extend the life of critical parts.
By combining successful maintenance practices with strategic upgrades, it is possible to maximize the operational life of turbines, optimize performance and minimize unplanned downtime.
Conclusion
Gas turbines play a key role in the energy industry by providing a reliable and efficient source of power generation. They are designed to convert thermal energy into mechanical energy, and eventually into electricity, making them indispensable to meet the growing demand for energy worldwide.
References
- Meherwan P. Boyce; “Gas Turbine Engineering Handbook”; Fourth Edition.
- GAS TURBINE PERFORMANCE AND MAINTENANCE- Rainer Kurz Manager, Systems Analysis Solar Turbines Incorporated, San Diego, CA, USA. Klaus Brun, Director, Machinery Program Southwest Research Institute® San Antonio, TX, USA
- Gas Turbine Working Principals – © Springer International Publishing AG 2018.
B. Zohuri, P. McDaniel, Combined Cycle Driven Efficiency for Next Generation
Nuclear Power Plants.