Pressure Relief Valves (PRV) are safety components in industrial plants, protecting systems against overpressure situations that could cause damage or even catastrophic consequences. They are designed to release overpressurization in order to protect assets, following international standards and regulations. According to API 576, pressure relief devices must be inspected/repaired as often as necessary “to maintain the device in satisfactory operating condition.”
In this article, we will examine in detail the basics of pressure relief valves and provide the necessary resources for their effective maintenance.
Basics of Pressure Relief Valves (PRV)
Characteristics, parts and operation
Characteristics: Among the most important are listed below:
- Safety device: The PRV is a critical component in pressure control systems, designed to protect equipment and pipelines from damage due to overpressure.
- Adjustability: These valves are adjustable to allow setting of the desired relief pressure.
- Versatility: They are used in a wide variety of applications and in various types of fluids, including gas, steam and liquids.
- Regulatory compliance: They must comply with the regulations and safety codes established by the competent authorities, ensuring their correct operation and reliability.
Parts: The main parts of these valves are as follows: Valve body, disc or cover, adjusting spring, valve seat, relief orifice, inlet and outlet connections, pressure gauge (in some cases), adjusting and control elements (in adjustable PRVs). Figure 1 shows the components of these valves in more detail.
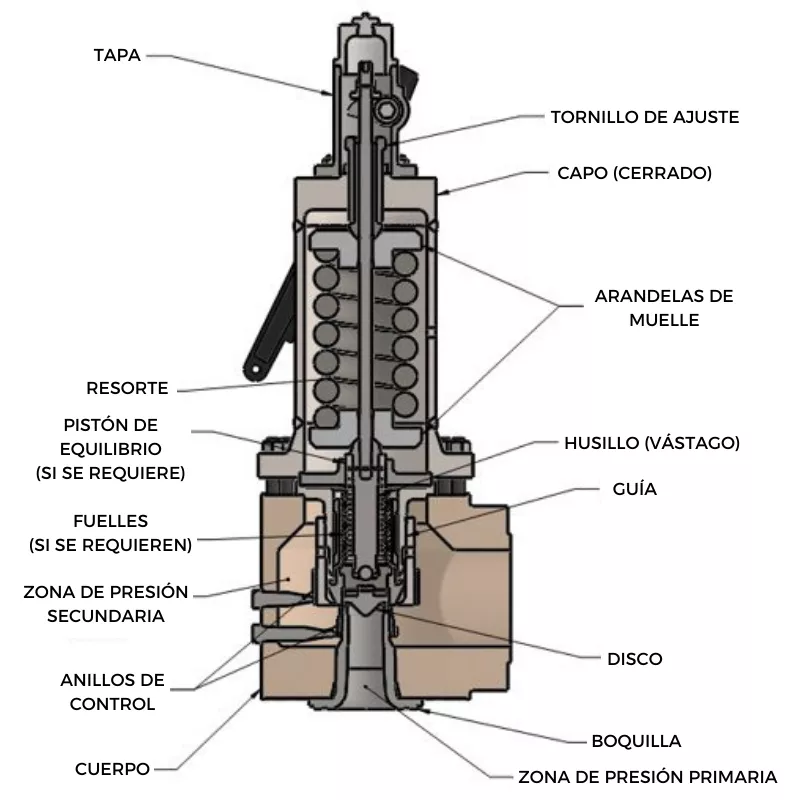
Operation: The following are the operating steps of these valves:
- When the pressure in the system exceeds a safe limit, the valve disc or cover lifts, allowing the fluid to escape.
- The adjusting spring controls the pressure at which the valve opens.
- The excess fluid is released through the relief orifice to an outlet, thus reducing the pressure in the system.
- Once the pressure returns to safe levels, the valve disc or cap closes, restoring equilibrium in the system.
Although PRVs are seemingly simple devices, their operation is more complex than it appears. They consist of an inlet nozzle connected to the process, which is blocked by a disc held firmly in place by the nozzle seat. This disc is held closed by a spring, whose adjustments are carefully made to determine the valve set point.
The “operate until failure” philosophy is not a viable option in the case of the PRV, since its eventual failure could cause material damage and even endanger human lives. Therefore, the minimum acceptable maintenance for the PRV includes periodic testing, internal inspection and repair as dictated by the test results.
Importance of installing and inspecting PRV valves
Installation problems are often the main cause of PRV operational malfunctions. It is essential to have trained and qualified maintenance personnel to identify and correct these problems, as proper installation is the first step in preventive maintenance. Improper installation can not only lead to valve failure and subsequent system shutdown, but can also result in unscheduled emergency repairs.
If installation problems are not corrected, recurring PRV failures could be experienced, shortening the life of the PRV and increasing costs associated with unscheduled shutdowns, additional repairs, spare parts, and even fines for fugitive emissions. These fugitive emissions are a type of non-channelized emissions. Leakage or gradual loss of product that occurs through different equipment or components. These are the most difficult emissions to quantify, detect and correct.
Repair and periodic testing of Pressure Relief Valves (PRV)
Considering pressure relief valve testing as a maintenance task will increase the likelihood of periodic testing, which will ensure the safety of the organization and the durability of boilers equipped with these safety valves.
It is recommended that valves be tested at least once every six months, especially to mitigate leaks caused by mineral buildup and corrosion. The scheduling of these biannual tests allows problems to be identified and solved quickly and effectively. It is critical that the company document all of its relief valve testing activities.
When testing relief valves, it is significant to take into account their dual function. First, these valves are activated when the pressure exceeds their safety threshold, opening to release the excess pressure until the pressure drops to the minimum set level.
There are three key times to consider valve repair or replacement: after a discharge, in accordance with local legal requirements, and depending on the specific service or application. After a discharge, it is important to recognize that pressure relief valves are designed to open automatically to release pressure and then close.
During this process, particles and debris may enter the valve seat, preventing proper closure. Therefore, after a discharge, the valve should be inspected for leaks. If they exceed the original parameters, repair is required.
Importance of in-service testing of pressure relief valves
In-service testing of pressure relief valves (PRVs) is a critical aspect of pressure vessel protection in the oil and gas industry. These devices are essential to quickly detect and relieve overpressure conditions, thus avoiding catastrophic damage during process operations.
When the process pressure reaches the set level, the upward force exerted by the process media (distillation, conversion and treatment) counteracts the downward force of the spring, allowing the disc to lift off the valve seat.
At this point, the process media are released through the valve outlet until the pressure drops below the set point. At this point, the downward force of the spring overcomes the upward force of the process fluids, and the valve closes.
In-service testing of relief valves is generally conducted during scheduled maintenance outages in accordance with guidelines established by ASME.
To perform these in-service tests, also known as in-situ tests, lift assist devices that are connected to the valve stem via adapters, along with other test equipment, are used to verify that the PRV operates properly at the set point, within the allowable tolerances.
To ensure proper operation of PRVs when necessary, the American Society of Mechanical Engineers (ASME) requires that functional checks be performed on a periodic basis.
Implementation of a Relief Valve Maintenance Program
Maintenance of pressure relief valves is crucial to ensure the safety of the equipment. The implementation of a proper maintenance program will help to extend the service life of the valves, reducing the need for frequent valve replacement.
The following are some maintenance recommendations:
- Verify that the protected cap located on the valve is securely tightened.
- Inspect the pressure relief valve spring for signs of deterioration and corrosion.
- Check for leaks in the seat area.
- Dirt, paint and other foreign particles can obstruct proper drainage of the valve body. If signs of corrosion or contamination are detected, the valve must be replaced.
Importance of Reliable Relief Valve Testing
Reliable testing of safety relief valves is critical to ensure the integrity and safety of the facility. These valves play a crucial role in relieving excess pressure in the system, thus protecting machinery, equipment and, most importantly, the safety of employees and facilities.
Given the importance of these valves, it is imperative to ensure that they perform optimally, which requires accurate and reliable testing. Although there are several test methods available on the market, here are five reasons why in-line safety relief valve testing is the most reliable method for your installation:
- Quality testing of in-line safety relief valves eliminates the possibility of human error when evaluating valves.
- Compared to traditional bench testing that requires manual manipulation of each individual valve, and in-line hydraulic testing that relies on a hand pump, both methods that can lead to a wide range of human error, systems are available that use a software-controlled electric motor to apply constant, uniform pressure during in-line testing.
- This approach eliminates the possibility of human error and provides accurate reports for technicians to perform their work efficiently.
- If you are looking for reliable results from your valve testing method, the online method offers another significant advantage. It is not necessary to remove the valves and test them at an external facility. In contrast, with in-line test equipment, valves are tested in your system, allowing you to observe exactly how they perform within your facility.
- This ability to keep the system running during testing makes the process more cost effective and efficient. Accurate and convenient valve testing is critical, and in-line safety relief valve testing is one of the few options that offers both of these features.
conclusion
In today’s market, in-line safety relief valve testing stands out as one of the most reliable testing methods. Exceptional accuracy, repeatable results and the ability to keep production running are just some of the reasons behind the choice of inline testing whenever feasible.
References
- www.powermag.com/in-service-testing-of-pressure-relief-valves/
- www.linkedin.com/pulse/ Pressure-safety-valve-testing-maintenance