Table of Contents
- What is a pressure vessel?
- Important Regulatory Considerations Governing Pressure Vessels
- Importance of pressure vessel inspection
- Prevention of accidents and catastrophic failures
- Technological advances in the maintenance and inspection of pressure vessels
- The future of pressure vessel inspections
- Conclusion
- References
Pressure vessel inspection is an essential part of the industry that plays a critical role in the safety and performance of industrial equipment. These vessels are found in a variety of environments, from chemical plants and refineries to power plants and processing applications. Their function is to contain fluids or gases under pressure, which makes them vital components for the safe and efficient operation of industrial facilities.
To ensure these vessels operate safely and meet established regulatory standards, it is essential to conduct regular and rigorous inspections. These inspections seek to identify possible defects, damage or wear that may compromise the integrity of the containers and, ultimately, the safety of workers and the environment.
However, the pressure vessel inspection process is not static; It is constantly evolving to adapt to changing industry demands and technological innovations. The need to comply with safety regulations and the quest for operational efficiency drive the development and adoption of new technologies and inspection approaches. From advanced nondestructive inspection techniques to the application of data analytics and machine learning, the field of pressure vessel inspection is in an exciting phase of transformation.
This article will discuss pressure vessel inspection, addressing both regulatory compliance and innovative technologies that are driving significant improvements in the safety, efficiency, and reliability of these critical components in the industry. There will be a brief presentation on how innovations are shaping the future of pressure vessel inspection and enabling a more proactive and effective approach to managing the integrity of this essential equipment.
What is a pressure vessel?
They are containers designed to contain vapors, liquids or gases at a specific pressure (Figure 1). These containers are dangerous and to help mitigate the dangers they pose, almost every country in the world has laws about how they are designed, built and operated.
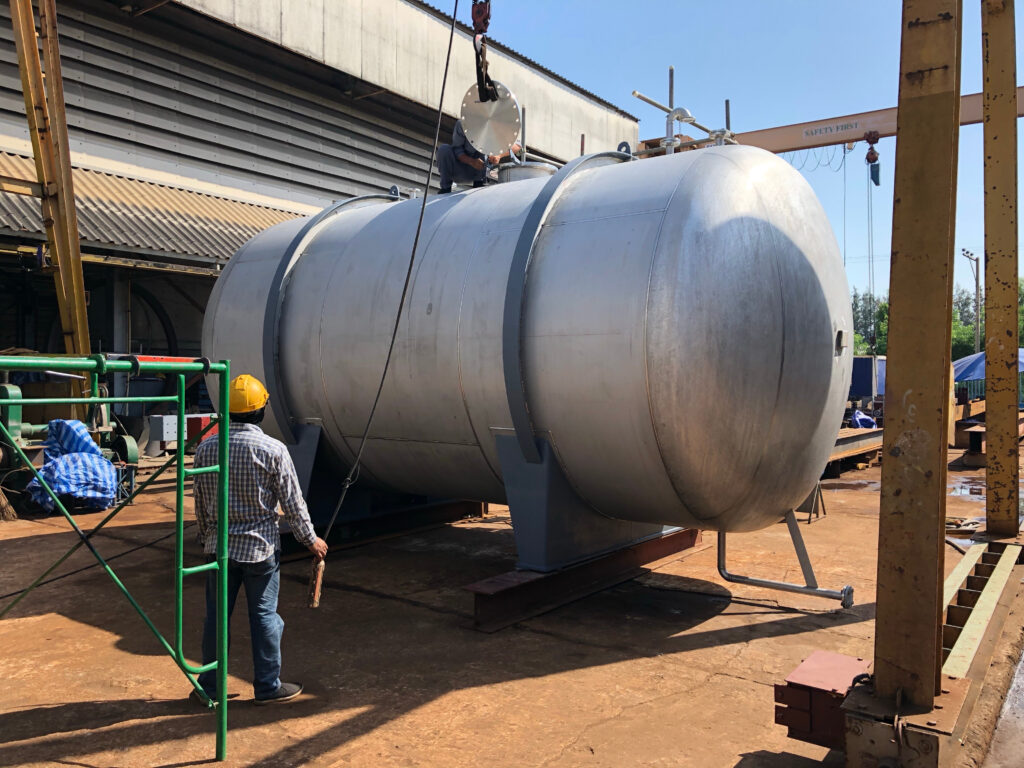
In addition to the general regulatory requirements for pressure vessels, each individual pressure vessel has specific operating limitations, called “design pressure and temperature.” If a pressure vessel is operated beyond the pressure or temperature for which it was designed, the result could be catastrophic failure of the unit. In the worst case scenario, operating outside of design conditions could lead to fires, poisonous gas leaks, or even explosions, all of which could pose extreme danger to the surrounding area.
Important Regulatory Considerations Governing Pressure Vessels
1. Compliance with safety regulations
Evaluation of pressure vessels is imperative to ensure compliance with safety standards and regulations, such as the renowned American Society of Mechanical Engineers (ASME) Boiler and Pressure Vessel Code.
Through thorough inspections carried out both during initial installation and at regular intervals throughout the life of the equipment, it is verified that the equipment operates safely and that no unacceptable damage has occurred during transport or use.
2. Regulations in the application of Non-Destructive Testing
Pressure vessel inspection helps companies meet legal obligations while fostering a culture of quality and safety. Inspections typically involve Non-Destructive Testing techniques , such as ultrasonic testing, radiographic testing, and visual inspections.
Pressure vessels are generally subject to periodic inspections to ensure their safety and integrity. These inspections are performed at specific intervals based on industry standards and guidelines.
NDT methods are used to evaluate vessel condition without disassembly or destructive testing, in accordance with American Society of Mechanical Engineers (ASME) standards. It is important to note that it is recommended that you consult relevant codes and standards for specific inspection intervals for different types of pressure vessels. This will ensure that inspections are carried out appropriately and meet established safety standards.
Inspection of pressure vessels is a prerequisite prior to commissioning, as well as during any major repair or alteration. In addition, external inspections are required to be carried out every 5 years and internal inspections every 10 years following the standards established by the American Petroleum Institute (API) 510.
3. Compliance with occupational health and safety regulations
Inspection of pressure vessels is performed in accordance with various regulations, including those established by the Occupational Safety and Health Administration (OSHA). These regulations impose the obligation to subject pressure containers to inspection and maintenance processes, with the purpose of ensuring the safe operation of this equipment and preventing the occurrence of incidents and injuries.
Inspection of pressure vessels is an integral part of modern industrial processes, allowing substances to be safely stored and transported under high pressure. Its diverse applications and critical role in various industries underline the need for proper design, manufacturing and maintenance.
By complying with safety standards and adopting technological innovations , we can guarantee the continuous, safe and efficient use of these containers. Pressure vessel inspection and periodic maintenance are necessary to detect and address potential problems before they lead to failure. This practice extends the life of pressure vessels and ensures their reliable performance.
Importance of pressure vessel inspection
This equipment is an integral part of various industries and plays a fundamental role in processes that involve containing liquids, gases and vapors at high pressure. These vessels are used in various applications, from energy production to chemical manufacturing. However, ensuring the safety and integrity of pressure vessels is of utmost importance due to the potential risks associated with accidents, leaks, and catastrophic failures.
Prevention of accidents and catastrophic failures
Periodic inspection of pressure vessels is vital to identify any signs of corrosion, material fatigue or structural weakness that could compromise their integrity. These problems can lead to accidents, leaks and even catastrophic failures, endangering human lives, causing environmental damage and disrupting operations.
Below are some safety concerns and examples of catastrophic pressure vessel failures include:
1. Overpressure: When a pressure vessel is exposed to pressures beyond its design limits, it can cause overpressure failure. The container may rupture, causing a potentially dangerous release of stored fluid or gas.
2. Corrosion: External corrosion from environmental factors or internal corrosion due to stored product can cause thinning of container walls and increase the risk of failure.
3. Fatigue: Repeated cycles of pressure variation can cause fatigue failure of pressure vessels. This is common in equipment subjected to frequent starts, stops and temperature fluctuations.
4. Welding Defects: Poor welding practices or defects in welds can compromise the integrity of pressure vessels, causing failure of welded joints.
5. Brittle Fracture: Exposure to low temperatures can make some materials more susceptible to brittle fracture. Sudden impacts or rapid changes in temperature can trigger this type of failure.
6. Material defects: Inadequate material quality or defects in the manufacturing process can cause pressure vessels to have weak points that are prone to failure.
Technological advances in the maintenance and inspection of pressure vessels
Innovative technologies, such as drones, assist with inspections by providing a safer, more efficient and cost-effective way to inspect pressure vessels. Major energy companies use environmental mitigation techniques to allow drone access to spaces that would otherwise be restricted to intrinsically safe equipment.
Using drones to collect visual data 1 inside a pressure vessel improves the overall safety of people involved in the inspection process (Figure 2). Inspectors do not have to enter the confined space, which can be risky, and they can [G2] control the drone remotely outside the structure, avoiding the risk of injury.
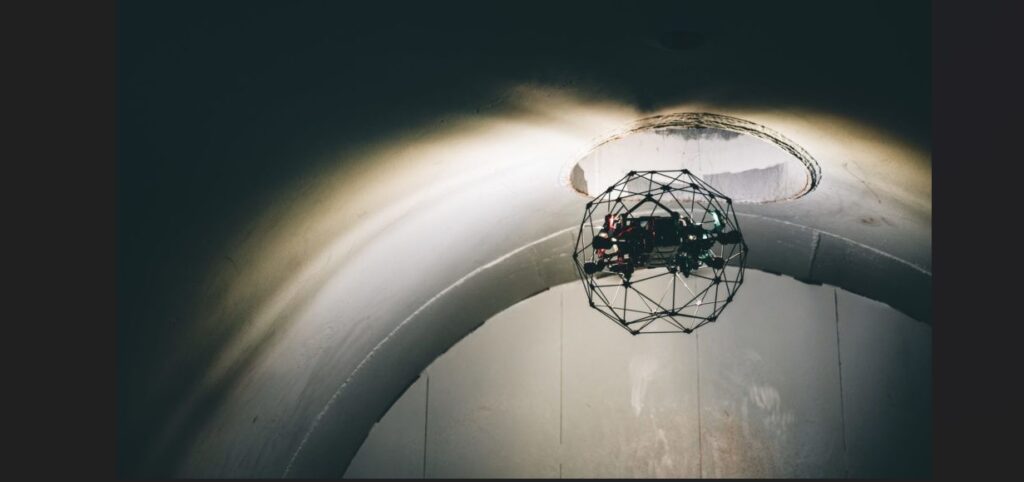
Technological advances in periodic maintenance and inspection of pressure vessels have completely revolutionized the way the industry approaches the safety and performance of these critical components. In a world where safety and operational efficiency are top priorities, the ability to perform accurate and effective inspections is essential to prevent catastrophic failures and ensure equipment integrity.
The introduction of robots and autonomous vehicles equipped with advanced inspection systems has taken automation to new heights. These devices can access hard-to-reach areas and perform detailed inspections efficiently and safely, significantly reducing downtime and operating costs.
Additionally, data analytics and machine learning are transforming the way inspection results are interpreted and managed 2 . Advanced algorithms can identify patterns and anomalies in large data sets, allowing you to anticipate potential problems and proactively schedule maintenance interventions.
Technological advances in pressure vessel maintenance and inspection are driving the industry toward a safer, more efficient future. These innovations not only improve equipment reliability and safety, but also reduce operating costs and increase the ability to anticipate and prevent problems before they become crises. Investment in these technologies represents a step forward towards a more advanced and sustainable industrial landscape.
In the field of pressure vessel inspection, significant technological advances have been implemented, most notably the widespread adoption of cutting-edge non-destructive inspection (NDT) technologies. These techniques allow industrial assets to be evaluated without compromising physical integrity, minimizing the risks associated with traditional inspections that required disassembly and destructive testing.
Some of the NDT techniques with notable technological advances include the use of advanced Ultrasound to detect internal defects and evaluate wall thickness, Digital Radiography that improves defect detection and evaluation accuracy, Eddy Current inspection that evaluates the integrity of metal surfaces, Infrared Thermography to identify temperature changes that may indicate problems and Magnetic Particle Testing with advanced particles and more sensitive detection systems.
These advanced techniques contribute significantly to the safety and efficiency of pressure vessel inspections, ensuring accurate evaluations without requiring disassembly or destructive testing, in accordance with relevant standards and codes.
The future of pressure vessel inspections
The future of pressure vessel inspections is constantly evolving as inspection technologies advance and the industry seeks to improve its operations. In an increasingly demanding industrial environment and with increasing energy demand, maintaining pressure equipment and systems in optimal conditions has become a key priority.
However, the way these inspections are carried out is undergoing significant changes. From process automation to the application of advanced detection techniques, the industry is taking innovative approaches to ensure inspections are efficient. Additionally, solutions based on data and real-time analytics are being explored to anticipate and prevent potential failures before they occur, which promises to reduce costs.
Conclusion
Its multiple applications and critical role in various industries underscore the need for proper design, manufacturing and maintenance. Performing an inspection of pressure containers using NDT techniques is a meticulous process that requires experience and a structured approach. By meeting standards and adopting technological innovations, we can ensure the continued utilization of pressure vessels.
References
- Drone inspecting flyability.com/casestudies/ Pressure-vessel
- https://www.screeningeagle.com/es/inspection/inspecci%C3%B3n-datos-entrevista-con-marcel-poser