In the oil refining process, coke drums play a key role, especially in the delayed coking unit, where the heavy oil residue is converted into lighter hydrocarbon products and petroleum coke. These drums operate under extreme conditions of cyclic thermal stresses, high temperatures and pressures, making them susceptible to various types of service failures.
To maintain operational efficiency and safety, it is important to ensure the integrity and reliability of the coke drums through regular inspection and maintenance. Non Destructive Testing (NDT) methods are indispensable in this regard, offering ways to inspect these vessels without causing damage or disrupting operations1.
Theoretical basis of coke drums
Coke drums are large vertical vessels used in the delayed coking process, a thermal cracking method that converts heavy petroleum residues into lighter products and petroleum coke. They operate under severe temperature and pressure cycles, which can cause material degradation and structural failure. Each cycle is composed of the following phases:
- Preheating of the vessel.
- Filling the vessel with preheated oil.
- Turn off the container with water.
- Unloading of coke products.
Due to the aggressive operating conditions, regular inspection and maintenance of the coke drums is necessary to prevent failures and ensure operational continuity.
Below is a video from RefiningCommunity.com on coke drum life cycle management; in order to expand on the information provided by this article.

Gestión del ciclo de vida de los tanques de coque.
Types of service failures in coke drums
These vessels are exposed to different types of service failures, including:
- Thermal fatigue cracking: Due to the cyclic nature of the coking process, repeated thermal expansion and contraction can lead to fatigue cracking damage, particularly in welds and heat-affected zones (Figure 1)2.
- Buckling and deformation: Constant thermal cycling can cause permanent deformations such as buckling or distortion of the drum shell.
- Corrosion: Although less common, corrosion can occur, especially if corrosive compounds are present in the cargo.
- Drum bowing and tilting: These are major problems that can arise due to a variety of factors related to grout/wedge/anchor bolt failure and skirt deformation due to uneven loading on the base plate resulting from uneven thermal expansion and contraction of the coke drum during the normal operating cycle.
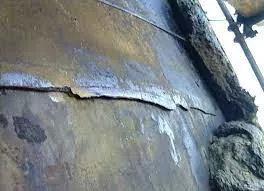
Knowledge of these types of failures is significant in selecting the most appropriate NDT methods for inspection and maintenance of coke drums.
Non-Destructive Testing (NDT) methods for the inspection of coke drums
NDT methods allow inspection and analysis of material properties and structural integrity without causing damage. The main NDT methods recommended by API TR 934-J and WRC Bulletin 556 include:
Visual Inspection (VT)
Visual inspection is the simplest method and the first step in NDT, involving a thorough examination of the drum surface for any visible signs of damage, such as cracks, deformation or corrosion. Technological aids such as the use of high-definition cameras can extend the scope and detail of internal visual inspections by taking advantage of the drum cutting tool.
Penetrant Liquid Examination (PT)
Liquid penetrant testing (PT) can be used to find surface cracks and determine their extent along the drum surface. This test is normally used for non-magnetic materials, such as restoration welds of Ni alloys on coated plates, but can also be used for ferritic steel parts of a coke drum, such as Cr-Mo shells and 12Cr2 coatings.
Nowadays, new technologies allow the application of the PT test from the internal part in an automated way without the need for access to the interior by the examiner.
Magnetic Particle (MT) Inspection
This type of inspection is used to detect surface and shallow subsurface defects in ferromagnetic materials. This technique involves applying a magnetic field to the surface of the drum, followed by the spreading of ferromagnetic particles on it. Defects are identified by the accumulation of particles, visible under proper lighting conditions and can only be used on a magnetic material, so it is not suitable for restoration welds of nickel alloy or weld overlays of nickel alloy or 300 series stainless steel2.
Ultrasonic Testing (UT)
For coke drums, ultrasonic testing (UT) is particularly useful for its ability to inspect welds and thick-walled components, identifying cracks and measuring their size and orientation. There are several ultrasonic examination techniques that can be used to find and size cracks in drums and skirts. The different techniques of the ultrasonic testing method are mentioned below, such as:
Shear Wave Ultrasonic Evaluation (SWUT): This pulse echo-based technique is generally performed from the exterior surface (non-invasively) to detect cracks that initiate on the interior surface and propagate through the wall. SWUT applied to nickel-based solder restorations is normally not effective when the crack propagates through the joint volume due to the high dispersion and refraction produced in the joint, however, it is not a problem when the crack propagates beyond the restoration solder and into the base metal.
It can sometimes be difficult to detect cracks that form in the coating due to disunion of the coating from the underlying base metal of the coke drum. SWUT is often used to find and size cracks in the vicinity of the skirt fitting.
Time of Flight Diffraction Inspection (TOFD): It is an ultrasonic technique based on diffraction produced in discontinuities that, in coke drum hull welds, is used to detect cracks and size them. TOFD has advantages over SWUT in that it is little affected by defect orientation and the determination of defect size depends only on being able to measure the arrival time of the signals and not, as in the case of pulse-echo, on measuring the amplitudes of the signals2. TOFD offers highly repeatable results, making it ideal for tracking crack evolution when applying methodologies such as Fitness for Service (FFS).
TOFD cannot detect shallow cracks connected to interior or exterior surfaces due to dead zones in the side and back wall signals. Normally, other UT techniques, such as phased array ultrasonic testing (PAUT) and conventional SWUT, are recommended for detecting surface faults.
Phase Array Ultrasonic Evaluation (PAUT): Commonly used in the inspection of skirt-hull joint welds, the PAUT technique is a process in which UT data is generated by building phases consisting of a single PAUT probe of multiple elements (e.g., 10, 16, 32, 64 elements) controlled by time-delayed pulses precisely for each element2.
PAUT technology has a significant advantage over conventional single crystal (pulse-echo) UT technology in the detection and sizing of defects of variable orientation, especially those of the planar type, such as cracks, as well as in the performance of the service execution requiring great skill on the part of the examiners due to the complexity of the technique.
Modern technologies such as Full Capture Matrix (FMC), Total Focusing Method (TFM) and Phase Coherence Imaging (PCI) offer higher resolution and image quality, ideal for characterization (TFM/FMC) and more accurate measurements (PCI).
Considering that these techniques are a derivation and complement of the PAUT, whose generated images are based on the data collected by the pulsing of each individual element and received by all the elements of the transducer (FMC) and the processing of the same through a special algorithm for each pixel of the screen (TMF), it is ideal in the detection and evaluation of cracks in coke drums. On the other hand, PCI displays accurate diffraction images based on the level of coherence of the FMC/TFM information.
The total focusing method (TFM) is used to obtain the best possible image of the crack propagation trajectory and orientation, while phase coherence imaging (PCI) is used to accurately determine its length by locating the position of the tips with high accuracy.
PCI offers highly repeatable results, making it ideal for tracking crack evolution when applying methodologies such as Fitness For Service (FFS). Unlike TOFD, PCI requires only one transducer and also avoids parallel movement (in the direction of the tandem array of transducers) of the latter for accurate crack location through the wall thickness.
Field Measurement (ACFM)
Alternating current field measurement (ACFM) is an electromagnetic inspection technique that introduces an alternating current into the surface of a component to detect surface cracks. This can be used in the internal inspection of coke drums through modern technologies such as the robotic crack detection system which is a telescopically deployed robotic crawler equipped with an ACFM sensor that is used to quickly and accurately confirm the presence of cracks on the inside surface and accurately size the length and depth of the indication.
Acoustic Emission Testing (AET)
AET detects transient elastic waves generated by the rapid release of energy from cracks or deformations. This method is particularly useful for monitoring the condition of coke drums in service during operating cycles, identifying areas where cracks are actively growing.
The AET method for coke drums employs sensors attached to the vessel shell (mechanically bonded) via waveguides to detect acoustic emission (AE) activity emitted by “active” faults or localized plastic deformations of the vessel during operations2.
Coke drums can be monitored over a short or long-term period.
- Short-term AE monitoring is completed within three to five complete thermal cycles of the coke drums. The objective of short-term monitoring is to detect and locate “active” crack-like failures during the coke drum monitoring period to help determine the health of the drums2.
- Long-term AE monitoring is used to determine if there are indications that faults are growing and pose a potential risk of through-wall penetration and/or leakage. Often, long-term monitoring is used in conjunction with other NDE methods to monitor the condition of known faults near the bulk2.
Laser Test (LT)
Laser scanning provides dimensional measurements and, routinely applied during coke drum downtime, can determine when a bulge occurs during the life of a drum. A laser profile can be applied before or shortly after the initial commissioning of the drum to acquire baseline measurements to improve the accuracy of future measurements and the ability to detect the early onset of bulging and by taking advantage of the drum cutting tool to introduce and map the inside of the drum. Laser profiling can also be used to monitor and determine the degree, arching, and inclination of the drum.
Selection of NDT Methods
The selection of the appropriate NDT method for coke drum inspections is influenced by the expected type of defects, accessibility of the inspection area, and material properties. Often, a combination of methods is used for a comprehensive evaluation. Recommendations given in API TR 934-J and WRC Bulletin 556, based on the specific conditions and history of the drum, serve as a guide for the selection and application of different NDT methods in the inspection of coke drums. The following flow chart shows the general protocol for evaluating the inspection of coke drums1.
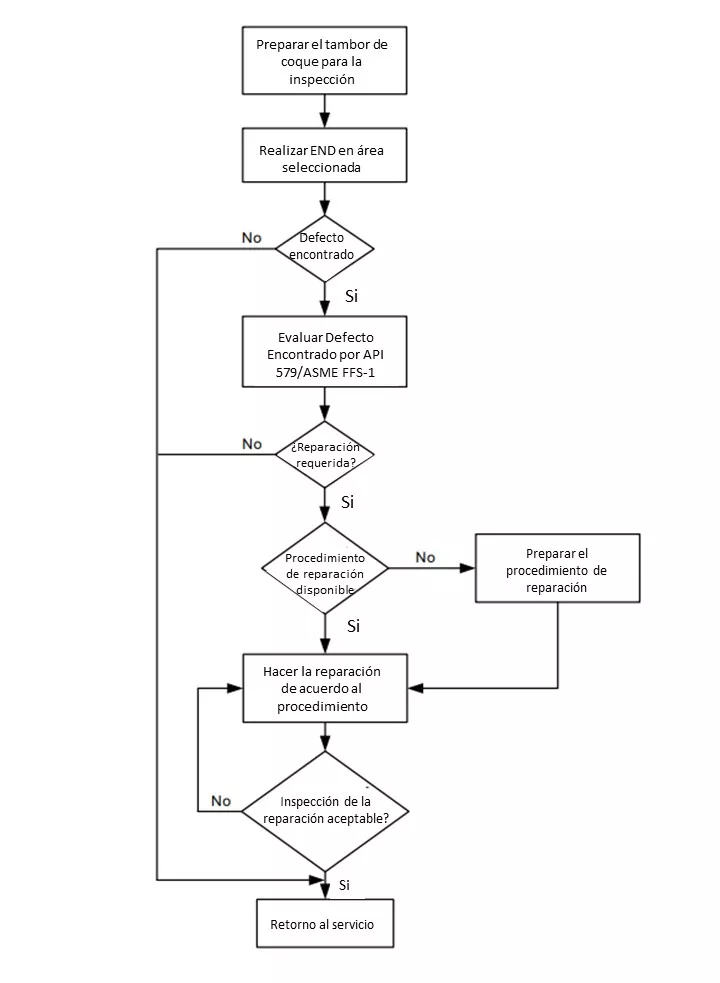
Conclusions
Non Destructive Testing methods are indispensable tools for the inspection and maintenance of coke drums in delayed coker units. By employing a combination of NDT techniques, operators gain a comprehensive understanding of the condition of their coke drums, detecting faults before they lead to failures. Adhering to the recommendations provided by documents such as API TR 934-J and WRC Bulletin 556 further enhances the reliability and longevity of these critical assets.
As technology advances, the adoption of more sophisticated NDT methods and integration with digital monitoring systems will continue to improve the safety and efficiency of delayed coking operations.
References
- J.E. SIMS, D.J. CHRONISTER, M. PRAGER. WRC Bulletin 556: Repair Manual for Coke Drums; Accessed March 21, 2024; Welding Research Council.
- BOBBY WRIGHT. Using Acoustic Emission Testing to inspect Coke Drums; Accessed March 23, 2024; https://refiningcommunity.com/wp-content/uploads/2017/07/Using-Acoustic-Emission-Testing-to-inspect-Coke-Drums-Allevato-Stress-Engineering-Services-DCU-Rio-de-Janiero-2009.pdf.
- API. API 934-J: Inspection, Evaluation and Repair of Coker Drums and Peripheral Components in Delayed Coking Units; Accessed March 20, 2024; AMERICAN PETROLEUM INSTITUTE.