Table of Contents
- Advanced corrosion control technology
- Corrosion monitoring systems
- Non Destructive Testing Equipment for evaluations
- Digital platforms for corrosion control
- Corrosion preventive maintenance
- Corrosion diagnostics using digital technology
- Artificial intelligence applied to corrosion control
- Conclusions
- References
In the oil and gas industry, corrosion represents one of the most significant and costly challenges, affecting not only the integrity and safety of facilities, but also operational efficiency and environmental sustainability. Faced with this challenge, the oil sector has focused on the search for digital solutions with advanced technology for corrosion monitoring and control.
This article explores the emerging and established digital solutions that are making a difference in the fight against corrosion, with a particular focus on nondestructive testing equipment and the digital solution for corrosion control.
Advanced corrosion control technology
Corrosion control technology focuses on the development of tools and platforms that can effectively anticipate, detect and respond to corrosion incidents. This includes everything from predictive analytics software to nondestructive testing inspection devices. These technologies not only enable more accurate corrosion detection and monitoring, but also facilitate the implementation of predictive maintenance strategies.
Among these solutions are real-time corrosion monitoring systems, which use advanced sensors and data collection techniques to provide instant insight into the condition of facilities and pipelines.
Corrosion monitoring systems
Corrosion monitoring systems represent the key to managing the integrity of oil and gas facilities. These systems are based on the use of sophisticated non-destructive testing equipment and the collection and analysis of data generated by that equipment in real time, enabling early identification of problem areas and evidence-based decision making to mitigate the effects of corrosion. Continuous monitoring offers a significant advantage in preventing failures and optimizing maintenance programs.
Currently, there is a great advance in corrosion monitoring systems with the integration of technologies such as artificial intelligence (AI) and the machine learningThese have made it possible to analyze large volumes of data from multiple sources, identifying patterns and predicting corrosion progression with high accuracy. This advanced analytical approach facilitates the implementation of predictive maintenance strategies, where maintenance actions are planned based on the actual condition of the assets and their deterioration forecast.
Non Destructive Testing Equipment for evaluations
This equipment plays a key role in corrosion monitoring and diagnosis without compromising the integrity of the assets being evaluated. Among the most used in permanent evaluations and in the sending of remote information, the following stand out:
Real-time corrosion sensors
These devices are installed at critical points of the infrastructure to measure the corrosion rate continuously, as shown in Figure 1. They use technologies such as ultrasonography, electrochemical impedance and electrochemical noise spectroscopy, among others, to provide accurate data on the corrosion state of materials. And send remote information in real time.
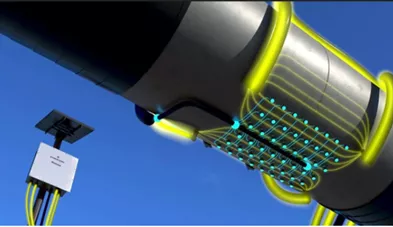
Drones equipped with sensors and HD cameras
For aerial inspections of extensive or difficult-to-access infrastructure, drones are equipped with high-definition cameras and dedicated sensors to detect signs of corrosion, cracks or wear. These drones can transmit images and data in real time to control centers, enabling rapid response to any signs of deterioration (Figure 2).
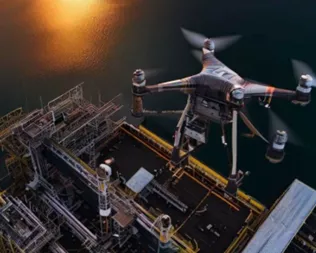
Autonomous inspection robots
Designed to navigate pipelines and other infrastructure, these robots perform visual and ultrasonic inspections, collecting data on wall thickness, cracks, and corrosion (Figure 3). Its ability to operate autonomously and send real-time information facilitates continuous monitoring and reduces the need for manual inspections in potentially hazardous environments.
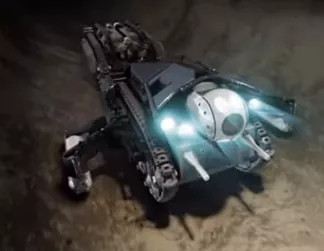
Digital radiography and ultrasound
These technologies allow detailed evaluation of structural integrity without the need to disassemble the equipment. Digital radiography provides high-resolution images of internal areas, while phased array ultrasound provides accurate wall thickness data and detection of internal defects. Both technologies are essential for accurate diagnosis and implementation of timely corrective actions.
Digital platforms for corrosion control
Digital platforms are integrated systems that offer a complete solution for corrosion management. These platforms combine data collection, predictive analytics, visualization and reporting into a single user interface, simplifying the decision-making process and improving operational efficiency. By centralizing corrosion-related information, companies can optimize their maintenance strategies and ensure more effective asset management.
Corrosion preventive maintenance
Predictive corrosion maintenance is based on the use of real-time and historical data to predict when and where corrosion is likely to occur. This approach moves from a reactive to a proactive maintenance model, where interventions are made before corrosion problems become critical. Implementing these strategies not only reduces the costs associated with maintenance and repairs, but also extends the useful life of the assets.
Corrosion diagnostics using digital technology
Generally, it involves the use of digital tools and techniques to assess the severity and extent of corrosion. This may include the use of drones equipped with high-resolution cameras and sensors to inspect hard-to-reach areas, as well as the use of specialized software to analyze images and structural data. This advanced diagnostic capability significantly improves the accuracy of corrosion assessments and facilitates evidence-based decision making.
Artificial intelligence applied to corrosion control
Artificial intelligence applied to corrosion control is becoming an increasingly valuable tool for predicting and preventing corrosion. AI can analyze complex data sets to identify trends, foresee potential failure points and recommend corrective actions. The ability of AI to learn from data and improve its predictions over time offers a unique opportunity to continuously improve corrosion control strategies.
Conclusions
The adoption of digital solutions and advanced technology for corrosion control is marking a before and after in the oil and gas sector. The use of non-destructive testing equipment for ongoing assessment, the ability to transmit information in real time, accurate diagnostics using digital technology, and the application of artificial intelligence are not only optimizing maintenance and safety processes but also opening new avenues for predictive corrosion management.
These digital innovations represent a significant advance towards minimizing the risks associated with corrosion, ensuring the integrity of critical assets and promoting safer, more efficient and sustainable operations in the oil and gas industry.
References
Own source