Table of Contents
- Introduction
- How does the surge occur?
- Causes of surge in centrifugal compressors
- Consequences of surge on industrial compressors
- How to mitigate surge in centrifugal compressors?
- How do liquid and gaseous fluids interact with a control valve and what phenomena can occur in each case?
- Phenomena to consider in gas control valves
- Types of sonic chokes
- Basic definitions
- Relationship with rotating equipment
- Practical applications
- Conclusions
- References
Introduction
In centrifugal compressors, the phenomenon most commonly associated with pressure and flow fluctuations in gases is surge, not cavitation. The key difference is that cavitation occurs in liquids when the pressure drops to the point of evaporation, generating vapor bubbles that collapse violently. In contrast, in a centrifugal compressor, where the fluid is gas, there is no similar phase change.
Surge in centrifugal compressors is an unstable phenomenon where the gas flow through the compressor is cyclically reversed due to an imbalance between discharge pressure and suction system capacity. This causes vibrations, pressure variations and possible mechanical damage to impellers and bearings.
Although the correct terminology in compressors is “surge” or “loss of flow stability”, some engineers may mistakenly refer to certain instabilities in the gas as “cavitation”, as both phenomena share symptoms such as noise, vibration and loss of efficiency.
How does the surge occur?
Surge is a flow instability phenomenon that occurs in centrifugal compressors when the amount of gas entering the compressor is insufficient to maintain the discharge pressure. This causes a cyclic oscillation of the flow, in which the gas flows forward and then intermittently reverses1.
Unlike cavitation in pumps, where there is formation and collapse of vapor bubbles, in surge there is no phase change. Instead, the compressed gas is forced backward due to an imbalance in pressure between the suction and discharge of the compressor. This oscillating flow generates strong vibrations and can cause severe damage to bearings, impellers and mechanical seals.
To further complement the information on the subject, I recommend watching the following video courtesy of: Mr. Engineer7277.

How does surge occur in centrifugal compressors?
Causes of surge in centrifugal compressors
Surge occurs when the compressor operates near its minimum flow limit, i.e., when the gas demand decreases below the capacity of the equipment. Common causes include:
- Fluctuations in the process demand, which reduce the inflow to the compressor.
- Poor design of the control system, which does not properly regulate the discharge pressure.
- Excessive increase of the back pressure in the discharge line, which prevents the gas from flowing properly.
- Low operating speed of the compressor, which reduces its ability to maintain a stable compression.
- Failures in control valves or bypass systems, which prevents correct flow conditions.
Consequences of surge on industrial compressors
Surge is an extremely damaging phenomenon for centrifugal compressors in refineries and petrochemical plants. Its effects include:
- Severe vibrations, which can cause fatigue in mechanical components.
- Temperature increase in bearings and mechanical seals, which reduces their service life.
- Accelerated wear of impellers, due to unstable forces in the flow.
- Efficiency losses and risk of compressor emergency shutdown.
- Damage to the piping system, as pressure changes can generate water hammer.
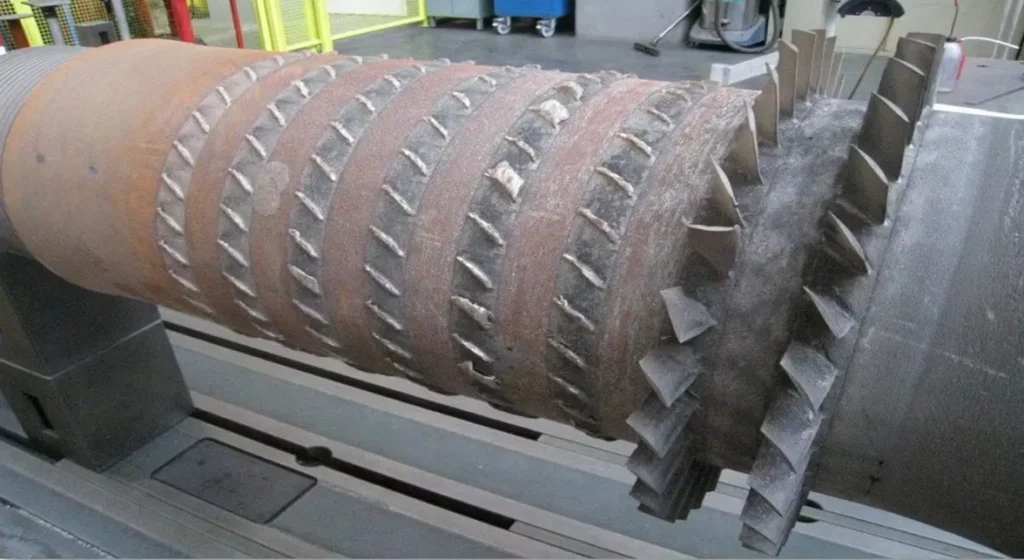
How to mitigate surge in centrifugal compressors?
To prevent the compressor from surging, several design and control strategies are implemented:
Anti-surge control systems
Anti-surge control systems use pressure and flow sensors to monitor compressor operation and prevent the compressor from operating in the instability zone.
These systems:
- Detect when flow drops to dangerous levels.
- Activate recirculation valves to increase inlet flow.
- Adjust compressor speed to stabilize compression.
Recirculation or bypass valve
When it is detected that the gas flow is being reduced too much, a recirculation valve opens and redirects some of the discharge gas back to the suction. This prevents the flow from dropping below the surge threshold and maintains compressor stability.
Variable Speed Drives (VFD)
Some compressors use variable frequency drives (VFD) to adjust their operating speed and adapt to changes in gas demand without surging.
Proper piping system design
It is recommended to design the compressor suction and discharge piping with optimum dimensions and restrictions to minimize pressure variations and avoid surge conditions.
Avoid operating near the surge limit
It is essential to operate within the safe performance curve of the compressor, avoiding low flow working points.
How do liquid and gaseous fluids interact with a control valve and what phenomena can occur in each case?
- If the fluid is a liquid
- In a control valve, if the pressure drops below the vapor pressure of the liquid, vapor bubbles can form within the fluid.
- When these bubbles pass through the valve and the pressure recovers, they implode violently, causing cavitation.
- This generates erosion of the valve internals, noise and vibrations.
If the fluid is a liquid, an abrupt pressure drop can cause cavitation in a control valve.
- If the fluid is a gas
- Unlike liquids, gases do not have a defined vapor pressure, since they do not undergo phase changes due to a pressure drop under typical operating conditions.
- However, a sudden pressure drop across a control valve can generate rapid gas expansion and supersonic velocities, which can cause shock waves and turbulent flow.
- If the compressed gas at the compressor discharge encounters a restriction (e.g., the control valve closing too tightly), this can excessively reduce flow and lead to compressor surge.
Phenomena to consider in gas control valves
While cavitation occurs only in liquids, in gases there are other effects to consider:
Choked flow: If the downstream pressure is too low, the gas velocity can reach the velocity of sound in the narrowest vein of the valve, limiting the flow rate.
Sonic choking occurs when some location in the pipeline experiences a local velocity equal to the sonic velocity of the gas.
Types of sonic chokes
Sonic choke can occur in three geometric configurations in a piping system.
End-point choke: Occurs at the end of a pipeline when it exits into a large vessel or the atmosphere. In this situation, the gas cannot reduce its pressure to equal that of the discharge without accelerating to sonic velocity, resulting in a choke point at the end of the pipeline. This leads to a pressure discontinuity across which the discharge pressure condition is met.
Expansion choke: Occurs when the flow area of the pipe increases rapidly. For example, this occurs when the pipe expands from a two-inch pipe to a three-inch pipe. Another example is when a pipe enters a flow divider where the sum of the areas of the pipes on the side of the divider exceeds the area of the supply pipe.
A choke point is formed at the end of the supply pipe and a pressure discontinuity is established.
Restriction choke: This can occur when gas flows through a restriction in the pipeline, such as an orifice or valve. In such a case, the flow area of the gas is reduced, resulting in a local increase in velocity that can reach sonic velocity. A choke point is formed at the restriction, with a pressure discontinuity similar to the first two cases.
Sonic flow (also known as choked flow or critical flow) is a fundamental phenomenon in compressible fluid dynamics. Some definitions are given below:
Basic definitions
- Sonic flow: Condition where the fluid velocity reaches the speed of sound (M=1M = 1M=1) at a specific point in the system, usually at a geometric constraint (valve, nozzle or orifice).
- Choked flow: A limit state where the mass flow rate cannot increase even if the downstream pressure decreases, because the fluid reaches sonic velocity at the restriction.
- Critical flow: Point at which the downstream pressure gradient does not affect the mass flow rate. It is governed by the critical pressure ratio.
Relationship with rotating equipment
Centrifugal compressors can experience throttled flow in their discharge valves or diffusers when:
- The discharge pressure drops below 47-58% of the suction pressure (depending on the gas).
- Shock waves are generated which limit the flow rate, affecting the isentropic efficiency.
However, the phenomenon is not exclusive to this equipment. Fans, gas turbines and cooling systems are also subject to these conditions.
Practical applications
Component | Function | Example |
---|---|---|
Laval Nozzles | Accelerate flows to supersonic | Rocket engines |
Sonic Venturis | Flow control without moving parts | Chemical industry |
Relief valves | Limit flow in emergencies | Nuclear power plants |
Critical orifices | Flowmeter calibration | Laboratories |
This technical development integrates thermodynamic principles, fluid mechanics and industrial applications, being fundamental for the safe design of systems handling gases at high pressures.
- Rapid expansion and cooling: When a gas expands abruptly, its temperature decreases (Joule-Thomson effect), which can cause condensation in certain gases with hydrocarbons.
- Vibrations and noise: Turbulence in the valve can generate pulsations that affect the stability of the compressor.
- Compressor surge: If the valve reduces the flow too much, it can cause reverse flow and oscillations in the compressor, causing it to surge.
Conclusions
In systems that handle gases, such as centrifugal compressors used in refineries and petrochemical plants, it is essential to differentiate between phenomena such as cavitation and surge, since their causes, consequences and mitigation strategies are different. While cavitation is typical of liquids and occurs when the pressure drops below the vapor point, surge is associated with compressed gases and can be triggered by an excessive drop in flow rate, causing operational instability, mechanical damage and even unscheduled shutdowns.
It is important to implement anti-surge control systems, well-calibrated recirculation valves and a comprehensive design that takes into account the dynamic conditions of the process. This not only protects the integrity of the equipment, but also optimizes energy performance and ensures operational continuity in critical facilities.
References
- https://en.wikipedia.org/wiki/Choked_flow
- Justin Miller, Loyd Hilliard; “Enhanced anti-surge protection with engineered flow deadband” May 4, 2021; processingmagazine. https://www.processingmagazine.com/valves-actuators/article/21217099/enhanced-anti-surge-protection-with-engineered-flow-deadband