Table of Contents
- What is cavitation?
- Types of cavitation
- Cavitation-induced corrosion
- Factors influencing cavitation-induced corrosion include
- Types of cavitation corrosion
- How does cavitation affect the processes?
- Indicators that determine to me that a pump is cavitating
- Prevention and mitigation strategies
- Conclusion
- References
Cavitation is an effect that can cause severe damage to hydraulic and mechanical components, generating premature wear and reducing the useful life of the equipment. It is a common problem in pumps, turbines, valves and high-speed fluid handling systems. Without proper control and prevention, the effects of cavitation can lead to failure mechanisms such as corrosion, pitting and material fracture.
This article focuses on failure mechanisms caused by cavitation, with emphasis on cavitation corrosion and its effects.
What is cavitation?
Cavitation is a hydrodynamic process that occurs when a liquid undergoes sudden changes in pressure and flow rate, causing the formation of vapor bubbles in its interior. These bubbles collapse violently generating a back pressure against the metallic surfaces.
This collapse generates mechanical and chemical damage to the materials, initiating a progressive degradation that manifests itself in different types of mechanical and chemical failures. Chemical damage occurs when bubble collapse releases free radicals and high temperatures in localized areas, which can alter the chemical composition of the material and accelerate corrosive processes. In addition, the constant impact causes the removal of the protective layers of the material, exposing it to the aggressive agents present in the fluid1.
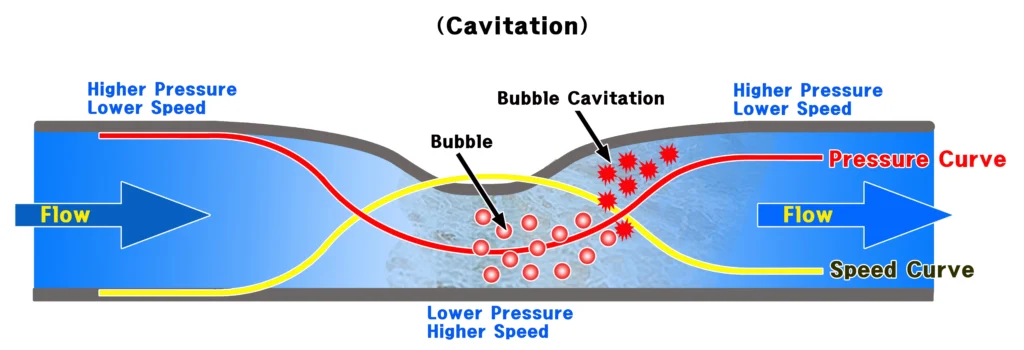
Types of cavitation
- Inertial cavitation: Occurs when bubbles collapse with high energy, producing aggressive impacts on the surface.
- Non-inertial cavitation: This occurs when bubbles persist in the fluid without collapsing violently, although they contribute to the deterioration of the material over time.
- Vortex cavitation: Occurs in rotating flow systems, such as pumps and turbines.
The destructive effects of cavitation are compounded when combined with other factors such as fluid composition, flow velocity and low strength of the exposed material.
Cavitation-induced corrosion
One of the main failure mechanisms associated with cavitation is accelerated corrosion. The collapse of the bubbles produces micro-fractures on the surface of the material, removing the protective layers and exposing the metal surface to oxidation and degradation processes.
This effect is especially corrosive on metallic materials, since the exposure of fresh surfaces to aggressive environments (such as saline water or fluids containing corrosive agents) accelerates the electrochemical corrosion reaction.
Factors influencing cavitation-induced corrosion include
- Nature of the fluid: Fluids with high oxygen content or aggressive chemicals may accelerate the process.
- Material composition: Materials with low corrosion resistance are more prone to deterioration.
- Operating conditions: High speeds and fluctuating pressures contribute to increased cavitation and thus accelerated corrosion.
Types of cavitation corrosion
- Pitting and surface erosions: Pitting on the surface of the material caused by cavitation is the result of the constant impact of collapsed bubbles. Over time, these pittings enlarge and compromise the structural strength of the component. This type of damage is particularly dangerous in critical parts such as pump impellers, valves and turbine casings, as it can lead to leaks or unexpected operational failures. In addition, pitting acts as a stress concentration point, increasing the susceptibility of the material to catastrophic fractures.
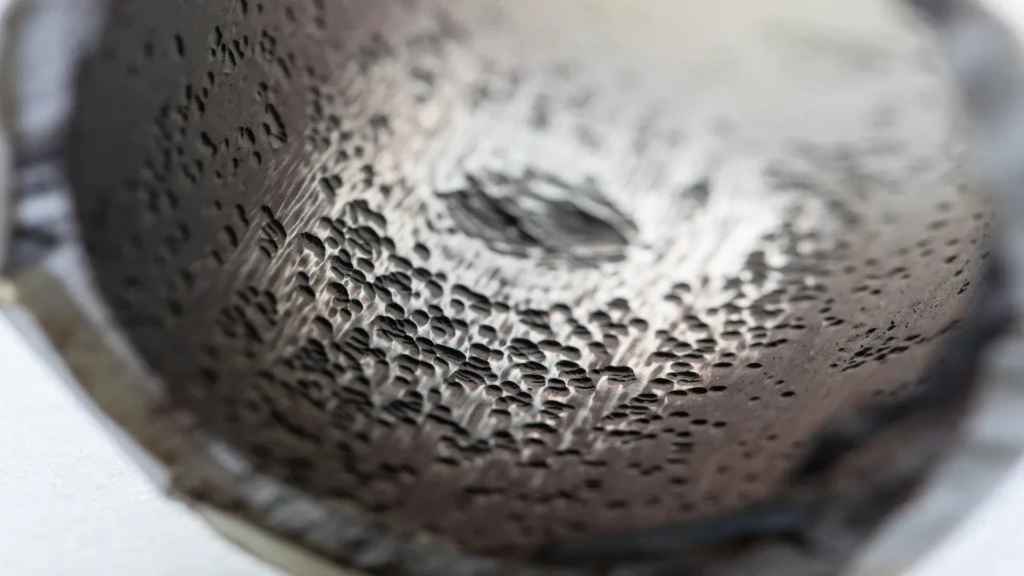
- Cavitation-induced fracture: When cavitation is severe and prolonged, the microcracks generated on the surface can evolve into cracks that affect the structural resistance of the component. This process can lead to complete fractures of the material, especially in those subjected to cyclic stresses or high mechanical loads.
Cavitation-induced fractures can be classified as follows:
- Fatigue fracture: Occurs when the repetitive action of cavitation causes the propagation of cracks in materials subjected to cyclic stresses.
- Brittle fracture: It occurs in materials with low tenacity, where the collapse of bubbles generates microcracks that propagate rapidly.
- Ductile fracture: In stronger materials, cavitation-induced fracture occurs progressively, with visible deformation before complete failure.
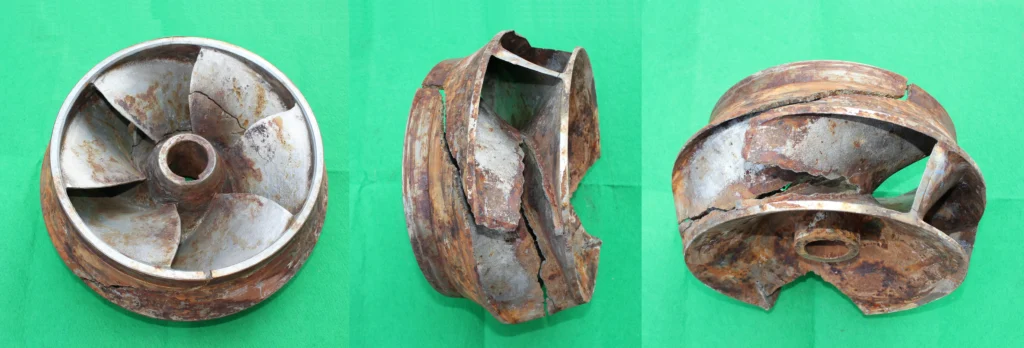
How does cavitation affect the processes?
This type of corrosion adversely affects various industrial processes and hydraulic systems in the following ways:
- Reduced efficiency: The formation and collapse of bubbles generates turbulence and energy losses in pumps, turbines and valves, reducing their operating efficiency.
- Decrease in flow rate: In positive displacement pumps, vapor bubbles displace the fluid in the pumping chamber, decreasing its effective transport volume. This phenomenon not only affects the amount of fluid impelled, but can also cause fluctuations in energy consumption due to the irregular operating conditions generated by cavitation.
- Mechanical and structural damage: Impacts generated by cavitation erode metal surfaces, causing accelerated wear and premature equipment failure.
- Increased maintenance and operating costs: The need for frequent repairs due to component damage affects system availability and reliability, increasing maintenance costs.
- Alteration in product quality: In processes that require controlled conditions, such as in the chemical or food industry, cavitation can generate impurities or affect the homogeneity of the final product.
- Excessive noise and vibrations: The collapse of bubbles produces vibrations that can affect the stability of the equipment, compromising its useful life and increasing the possibility of structural failures.
- Operation interruptions: In critical applications, such as power generation and fluid transport, cavitation can cause failures with unexpected shutdowns, affecting the continuity of the productive process.
Indicators that determine to me that a pump is cavitating
There are several indicators that can reveal the presence of cavitation in a pump during operation. Some of the most common signs include:
- Abnormal noises (knocking or crackling): Cavitation produces a characteristic sound similar to knocking or gravel circulating inside the pump. This occurs due to the collapse of vapor bubbles against the internal surfaces of the equipment.
- Excessive vibrations: The constant impact of cavitation bubbles generates irregular vibrations in the pump, which can affect system stability and accelerate component wear.
- Decrease in flow rate and pressure: When cavitation occurs, the effective volume of fluid conveyed decreases, which causes a drop in flow rate for no apparent reason. In some cases, a reduction in discharge pressure is also observed.
- Loss of efficiency and increased energy consumption: The pump needs to compensate for performance losses caused by cavitation, resulting in an increase in energy demand without an improvement in performance.
- Equipment overheating: Bubble collapse can generate localized heat, which increases the temperature of the fluid and pump components, accelerating material wear.
Prevention and mitigation strategies
Proper design of flow systems and preventive maintenance play an important role in reducing the effects of cavitation. Some key strategies include:
- Optimize hydraulic design: Reduce sudden pressure changes and minimize the generation of bubbles in the flow.
- Use resistant materials: Use alloys with high resistance to cavitation, such as stainless steels and ceramic coatings.
- Control pressure and flow rate: Maintain operating conditions that minimize the formation of cavities in the liquid.
- Apply protective coatings: Use barriers that reduce the impact of cavitation on exposed surfaces.
- Monitor the condition of equipment: Regular inspections and vibration analysis can detect early signs of cavitation.
Conclusion
Cavitation is a highly destructive phenomenon that can trigger different corrosion mechanisms, such as pitting and fracture of materials. Understanding the mechanisms involved and adopting prevention strategies is crucial to extend equipment life and ensure efficient operation. The combination of optimized design, selection of resistant materials and constant monitoring can effectively mitigate the adverse effects of cavitation in hydraulic systems.
References
- DEBEN ; “Pumps cavitation: what is cavitation in centrifugal pump?”. https://www.debem.com/en/cavitation-in-centrifugal-pumps/