Welding is a fundamental process in various industries such as construction, manufacturing, energy, and aerospace. The quality of welds can significantly affect the structural integrity, safety, and durability of any project. To ensure that welding is performed properly and meets the required standards, Welding Procedure Specifications (WPS) are used. These specifications are crucial to maintain consistency, ensure compliance with industry regulations, and improve overall weld quality. This article explores the importance of the Welding Procedure Specification in the quality assurance of welding projects.
Introduction to the Welding Procedure Specification (WPS)
A Welding Procedure Specification (WPS) is a formal document that provides detailed instructions on how to perform a specific welding operation1. It serves as a technical guide for welders, detailing the processes, materials, and parameters required in a welding project. Generally, WPSs are developed by experienced welding engineers based on extensive testing and analysis.
The primary objective of a Welding Procedure Specification is to ensure that all welds are performed consistently and to the required quality. This document describes the welding process, including the type of welding (e.g., MIG, TIG, or arc welding), base materials, filler materials, preheat and post-weld heat treatment requirements, and welding positions. By following a WPS, welders can achieve consistent results, minimizing the risk of defects and ensuring the structural integrity of welded components.
Why is a WPS essential in Welding Projects?
Ensuring consistency and quality
Consistency and quality are crucial elements in any welding project. A Welding Procedure Specification helps maintain these aspects by providing a standardized approach to the welding process. When welders follow a WPS, they adhere to specific parameters such as voltage, current, feed rate, and heat input. These parameters are meticulously selected to ensure that the welds are uniform and meet the desired mechanical properties.
Without a WPS, welders could use variable techniques, resulting in inconsistent welds that could compromise the structural integrity of the project. For example, variations in heat input can cause problems such as excessive distortion, cracking, or lack of fusion. By following a Welding Procedure Specification, these risks are minimized, resulting in high-quality welds that meet project specifications.
Compliance with industry standards
In addition to ensuring consistency and quality, a Weld Procedure Specification is essential for compliance with industry standards and regulations. Many industries have strict welding codes and standards that must be followed to ensure the safety and reliability of welded structures. These standards are developed by organizations such as the American Welding Society (AWS), the American Society of Mechanical Engineers (ASME), and the International Organization for Standardization (ISO).
A WPS ensures that the welding process is aligned with these standards, providing a clear path for compliance. This is particularly important in industries where the consequences of welding failures can be catastrophic, such as in pressure vessels, pipelines, and bridge construction. By following a Welding Procedure Specification, companies can demonstrate that they are complying with the necessary standards, reducing the risk of legal and financial liabilities.
How does a WPS improve weld quality?
Process control and error reduction
One of the main advantages of using a Welding Procedure Specification is the ability to control the welding process more effectively. A well-documented WPS details the exact procedures to be followed, leaving little room for deviation. This level of control helps reduce errors, such as the use of incorrect welding parameters or improper material selection, which can lead to weld defects.
For example, a WPS specifies the type of filler material to use based on the base materials being welded. Improper use of filler material can result in a poor quality weld, such as lower tensile strength or lower corrosion resistance. By following a Welding Procedure Specification, welders are less likely to make such errors, leading to high-quality welds that meet project requirements.
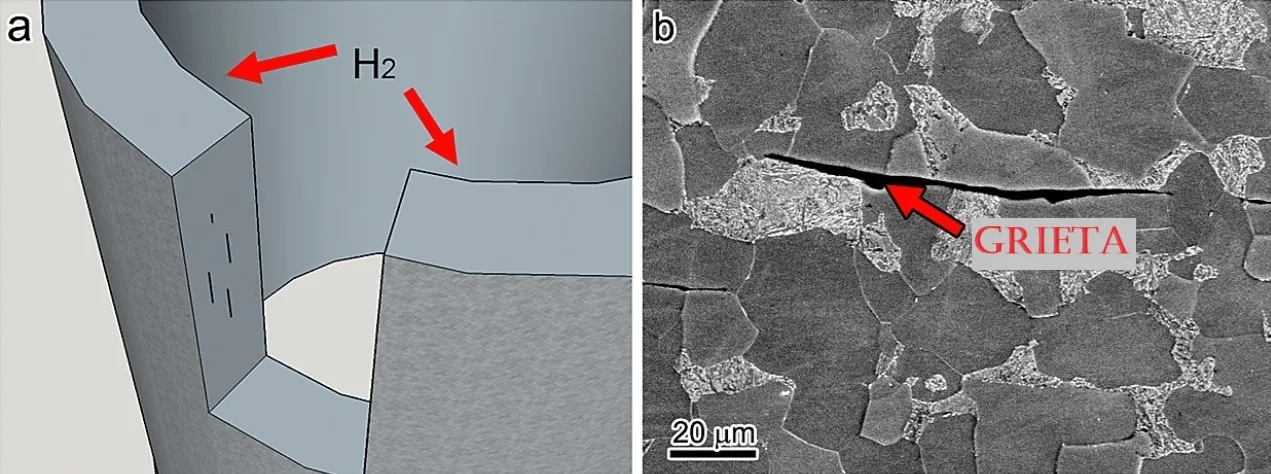
Improving safety and regulatory compliance
Safety is a critical concern in welding projects, as improper welding can lead to dangerous situations, including structural failures and accidents. A Welding Procedure Specification helps to improve facility or construction safety by ensuring that the welding process is performed correctly and consistently in compliance with the requirements of the applicable building code or standard. This also includes testing and acceptance and rejection criteria, minimizing the containment of weld joint failures.
International standards for WPS in the industry
Summary of the main international standards
Several international standards regulate the development and application of Welding Procedure Specifications. These standards provide guidelines for the creation and qualification of WPSs, ensuring that they meet industry requirements. Some of the most important international standards related to WPSs include:
- ISO 15614: This standard establishes requirements for the qualification of welding procedures. It covers various welding processes and materials, and provides guidelines for performing welding procedure tests to validate the Welding Procedure Specification.
- ASME Section IX: This section of the ASME Boiler and Pressure Vessel Code specifies requirements for the qualification of welding and brazing procedures. It is widely used in industries where pressure-containing components, such as boilers and piping, are welded.
- AWS D1.1: Developed by the American Welding Society, this standard provides guidelines for welding structural steel. It includes requirements for WPS qualification and is commonly used in the construction industry.
- EN ISO 9606: This standard specifies qualification requirements for welders, ensuring that they are competent to perform welding tasks according to the Welding Procedure Specification. It is commonly used in Europe and other regions.
- API 1104: This standard, developed by the American Petroleum Institute (API), focuses on the welding of piping and related components in the oil and gas industry. It is a crucial standard in the qualification of welding procedures and welders, ensuring that pipeline weld joints are safe and meet industry requirements.
Application of standards in different regions and industry sectors
The application of these standards varies by region and industry. In the United States, ASME Section IX, AWS D1.1, and API 1104 are widely used in industries such as construction, oil and gas, and power generation. These standards are often required by regulatory bodies and are considered essential to ensure the safety and reliability of welded structures.
In Europe, ISO 15614 and EN ISO 9606 are most commonly used. These standards are often required by the European Union and are widely adopted in industries such as automotive, aerospace and shipbuilding. Companies operating in these industries must ensure that their Welding Procedure Specifications comply with these standards to meet regulatory requirements and remain competitive in the marketplace.
In other regions, such as Asia and the Middle East, a combination of international and local standards may be used. For example, in countries such as China and India, industries often adopt a mix of ISO, ASME, and local standards to meet the specific requirements of their markets. This approach allows companies to ensure compliance with international best practices and regional regulations.
Conclusions
Welding Procedure Specifications (WPS) are essential tools in the quality assurance of welding projects. They provide a standardized approach to the welding process, ensuring consistency, compliance with industry standards, and improved weld quality. By following a Welding Procedure Specification, companies can reduce errors, improve safety, and meet regulatory requirements, ultimately leading to the successful completion of welding projects.
As industries continue to evolve and new technologies emerge, the importance of Weld Procedure Specifications will only grow. Companies that implement these specifications rigorously will be better positioned to meet international standards and ensure quality in their welding projects.
References
- GIIS GAMMA UK. The Importance of Welding Procedure Specification; Accessed on August 21, 2024. https://gammax.co.uk/the-importance-of-welding-procedure-specification/#:~:text=A%20WPS%20is,throughout%20a%20project.