Table of Contents
- Introduction
- Causes of the Deepwater Horizon disaster
- Blowout Preventers (BOPs)
- Inspection and maintenance protocol:
- Technologies for the prevention of catastrophic events
- Lessons learned from the Deepwater Horizon case
- Education and training (Courses, Diplomas, Specializations)
- Some of the rules and recommendations that arose or were revised in the aftermath of the disaster include
- Conclusions
Introduction
It was one of the most significant events in terms of environmental and industrial disasters in history. The event involved the explosion and collapse of the platform.
This disaster not only resulted in the death and injury of workers, but also caused millions of barrels of oil to spill into the Gulf, with devastating consequences for the environment and the local economy.
Deepwater Horizon was a fifth-generation, semi-submersible, dynamically positioned, ultra-deepwater, RBS-8D design oil rig whose drills drilled into the seabed, while other types of rigs and platforms are used to extract oil from already-drilled wells.
Causes of the Deepwater Horizon disaster
Among the various factors that contributed to the disaster, one of the main ones was the lack of proper inspection and poor maintenance of critical equipment. Subsequent investigation revealed that blowout preventers (BOPs), an essential safety device on the platform, had faulty components and had not been properly inspected and maintained.
In addition, the pressure tests carried out before the explosion were not correctly interpreted, leading to erroneous decisions. Figure 1 shows an image of the disaster that occurred on the platform. Platform supply ships can be seen fighting against the burning remains of the platform.
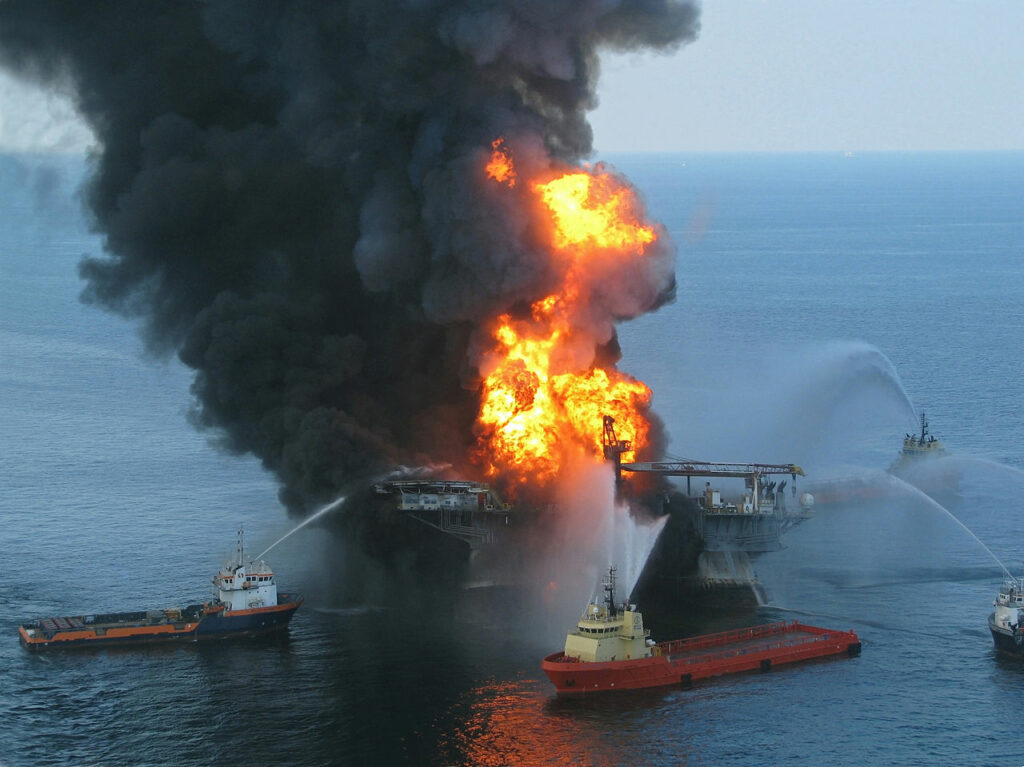
Blowout Preventers (BOPs)
Blowout Preventers (BOPs) It is a critical safety device used in the drilling of oil and gas wells to prevent the uncontrolled release of crude oil or natural gas, known as a “blowout”. These devices are essential to ensure the safety of drilling operations and protect the environment. In figure 2, an image of this device is shown.
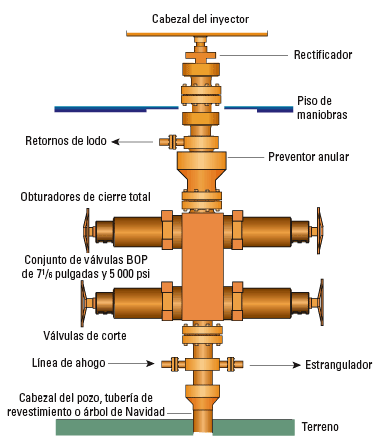
How does it work?
The BOP is designed to seal, control and monitor oil and gas wells to prevent any unexpected release of fluid. It operates by applying hydraulic pressure to shut in the well in the event of an anomaly. There are two main types of BOP:
- Annular BOP: Uses a rubber ring that can close around anything in the hole, or even close completely if the hole is empty.
- Shear Ram BOP: It is designed to cut and seal the drill pipe in an emergency.
Inspection and maintenance protocol:
Given the critical importance of BOPs, it is essential that they undergo regular inspection and maintenance. These protocols include:
- Visual inspections: To identify any external damage or wear.
- Function Tests: To make sure that all parts of the BOP work correctly.
- Pressure tests: To ensure that the BOP can withstand the pressures to which it could be exposed.
- Component Replacement: Any worn or damaged component must be replaced immediately.
- Lubrication: The moving parts of the BOP must be lubricated regularly to guarantee its correct operation.
Technologies for the prevention of catastrophic events
With technological advances, there are several solutions that can be implemented to improve the safety and efficiency of BOPs:
- Advanced sensors: These can continuously monitor the status and operation of the BOPs, sending alert signals in real time if anomalies are detected.
- Automated systems: These systems can automatically close the well in case of detecting an anomaly, without the need for human intervention.
- Robotics: Specialized robots can be used for inspections and maintenance in hard-to-reach places.
- Simulations and modeling: Computer simulations can predict how the BOP will react under different scenarios, allowing for better preparation and training.
Lessons learned from the Deepwater Horizon case
Extensive investigations that followed the incident revealed a number of failures and shortcomings, both technical and organizational. Several crucial lessons emerged from these investigations:
- Equipment Integrity: The Blowout Preventer (BOP) did not perform as expected due to maintenance issues and faulty components. This underlined the need for regular and rigorous inspections and maintenance of critical equipment.
- Data Interpretation: Pressure tests performed prior to the explosion were not correctly interpreted. Staff need to be adequately trained to interpret the data and act accordingly.
- Safety culture: The investigation revealed that a culture existed in which safety concerns were often secondary to production and cost concerns. Companies must prioritize security over economic benefits.
- Communication and decision-making: There were communication breakdowns between rig staff and executives on the ground, leading to wrong decisions. Clear and effective communication is essential in high-risk operations.
- Emergency Preparedness: The response to the oil spill was slow and often ineffective. Businesses should have robust and well-practiced emergency response plans.
- Design and technology: Deficiencies were identified in the design of the well and in the technology used. The industry needs to invest in research and development to ensure that the best technologies and practices are used.
- Regulation and Supervision: Regulatory agencies did not adequately supervise the operations of Deepwater Horizon. A stricter regulatory framework and more rigorous supervision is essential.
- Corporate Responsibility: Companies must take responsibility not only for their operations, but also for their contractors and subcontractors. Responsibility cannot be outsourced.
- Education and training: Staff must receive regular and up-to-date training, not only in technical operations, but also in security and emergency response.
- Risk Assessment and Management: Businesses need to take a proactive approach to identifying and managing risks, rather than reacting after an incident occurs.
The lessons learned from these experiences have resulted in significant changes in the hydrocarbons sector, focusing more on aspects such as safety, training, regulations and emergency response. However, the industry must maintain its constant learning and adjustment momentum to avoid potential disastrous crises.
Education and training (Courses, Diplomas, Specializations)
The Deepwater Horizon disaster underscores the critical importance of the Deepwater Horizon Disaster (2010) .. The Deepwater Horizon disaster was not only a human and environmental tragedy, but also a wake-up call for the oil and gas industry. It highlighted the urgent need to acquire competence in critical fields in order to safeguard safety and optimize the effectiveness of operations. Let’s dive into the reasons behind the importance of specializing in inspection, reliability and maintenance.”
1. Inspection: Inspection is the first line of defense against possible failures. Through inspection, problems can be identified in their early stages, long before they become catastrophic. Without regular inspections, problems can go undetected until it’s too late.
Specialization: These programs train engineers in the best practices for inspecting drilling equipment, including BOPs. Inspection specialists don’t just look for obvious signs of wear or damage. They are trained to detect subtle anomalies that a lay observer might miss. In addition, with the advancement of technology, such as non-destructive testing (NDT), specialists can assess the integrity of equipment without compromising its functionality.
2. Reliability: In the oil and gas industry, failure can not only result in economic loss, but also environmental disaster and loss of life. Reliability ensures that systems and equipment work as expected, without unexpected failures.
Specialization: Reliability specialists focus not only on the equipment itself, but on the entire system. They analyze data, perform tests, and use advanced tools to predict and prevent failures. Its goal is to design and operate systems that are inherently safe and robust, minimizing the risk of unexpected failures. These Reliability Engineering training programs focus on the reliability of equipment and systems, teaching engineers to design and maintain equipment to maximize its useful life and minimize failures.
3. Maintenance: It is what keeps equipment running, prolongs its useful life and ensures that it operates efficiently and safely. Without proper maintenance, even the most reliable equipment can fail.
Specialization: Maintenance specialists go beyond reactive repairs. They implement preventive and predictive maintenance programs, using advanced tools and technologies to anticipate and prevent failures before they occur. In addition, they are trained to perform high-quality repairs that not only fix problems, but also prevent future failures.
4. BOP Certification: Many organizations offer specific certification courses for BOPs that cover their operation, maintenance, and inspection.
5. Advanced drilling technologies: Technology in the oil and gas industry is constantly evolving, it is necessary for engineers to be aware of the latest innovations, especially those related to safety.
6. Robotics and automation in the oil and gas industry: It is necessary to update technological knowledge in this sector by participating in valuable courses to understand how these technologies can be used to improve inspection, maintenance, safety and efficiency.
7. Industry Regulations and Standards: It is important for engineers to be familiar with national and international regulations and standards related to oil and gas drilling and production. After the Deepwater Horizon disaster, there was a significant push in the industry and among regulators to review, update, and strengthen existing rules and regulations. Several organizations, including API (American Petroleum Institute), ASME (American Society of Mechanical Engineers), NACE (National Association of Corrosion Engineers), and ASNT (American Society for Nondestructive Testing), have worked to create or revise standards related to corrosion. offshore drilling and equipment safety.
Some of the rules and recommendations that arose or were revised in the aftermath of the disaster include
- API RP 53: This is an API Practice Recommendation that addresses drilling control systems for drilling rigs. Revised to include best practices in the operation and testing of BOPs.
- API RP 96 : This practice recommendation was developed specifically to address the design and operation of deepwater production systems, with a focus on blowout prevention.
- API Standard 65-2: Focuses on well cementing technology, which was one of the contributing factors to the Deepwater Horizon disaster.
- NACE SP0208-2008: This NACE standard provides practices for monitoring and mitigating corrosion in blowout control systems.
- ASME PCC-2: Although not specifically developed in response to the Deepwater Horizon disaster, this ASME standard on repair of equipment and pipelines may be relevant to the integrity of equipment on offshore platforms.
- ASNT: Although ASNT did not create specific standards in direct response to the disaster, its non-destructive testing techniques are essential to ensure the integrity of equipment in the oil and gas industry. Training and certification in ASNT techniques became even more critical after the disaster.
In addition to these standards, there has been an industry push to develop and adopt advanced monitoring and diagnostic technologies, as well as well and equipment integrity management systems.
Conclusions
The Deepwater Horizon incident stands as a grim historical event in the oil and gas industry, acting as a strong warning about the devastating consequences that can be unleashed by a lack of expertise and a lack of attention to inspection processes, reliability and maintenance.
However, in the midst of this tragedy, it is important to issue a call to action to companies and regulatory entities, urging them to recognize the importance of training in these areas and the implementation of preventive maintenance procedures, with the aim of preventing repetition of similar events in the future. The burden of responsibility falls on each layer of the industry, in order to achieve safety and sustainability, in a tribute to the memory of those affected by this event.
References
Own source