Almost all industries use storage tanks, within which they play a vital role, for the processing of products ranging from crude oil and its derivatives, specialty chemicals and water, among others. Tank maintenance management is essential to prevent catastrophic failures, minimize environmental risks and ensure operational continuity.
What is maintenance management?
It is the practice of effectively managing your company’s maintenance activities, personnel, assets and resources, with the purpose of optimizing your maintenance program.
Importance of tank maintenance management
Below are some reasons that highlight the importance of maintenance management specifically focused on tanks:
- Preventing leaks and spills: Tanks can leak or spill without proper maintenance, which can have significant environmental and safety consequences. Preventive maintenance management helps detect and address problems before they become critical situations.
- Safety: Poorly maintained tanks pose safety risks to workers and the surrounding environment. Maintenance management includes regular inspections, integrity testing and necessary repairs to ensure tanks are safe and meet safety standards.
- Regulatory Compliance: In all industries, there are strict regulations that dictate regular inspection and maintenance of tanks to ensure regulatory compliance. Maintenance management ensures that tanks comply with these regulations and avoids potential legal penalties.
- Structural integrity: Tanks are subject to stress and wear due to factors such as corrosion, internal pressure, and exposure to adverse weather conditions. Maintenance management focuses on ensuring the structural integrity of tanks through inspections, repairs and replacements as necessary.
- Resource Optimization: Maintenance management helps optimize resource usage by scheduling maintenance activities efficiently. This includes labor management, procurement of spare parts, and planning for scheduled outages to minimize the impact on production.
- Prolongation of useful life: Proper maintenance contributes to prolonging the useful life of the tanks. This not only reduces costs associated with frequent equipment replacement, but also ensures continued availability of tanks for their intended use.
- Reduced operating costs: Efficient maintenance management helps reduce operating costs by avoiding costly emergency repairs and minimizing unplanned downtime. A proactive approach can result in more effective management of financial and human resources.
Phases of the maintenance management program
- Inspection and evaluation: The first phase involves detailed inspections to evaluate the current condition of the tanks. Reliability methodologies such as risk-based inspection and advanced technologies such as non-destructive inspections and drones make it easy to collect accurate data without compromising personnel safety.
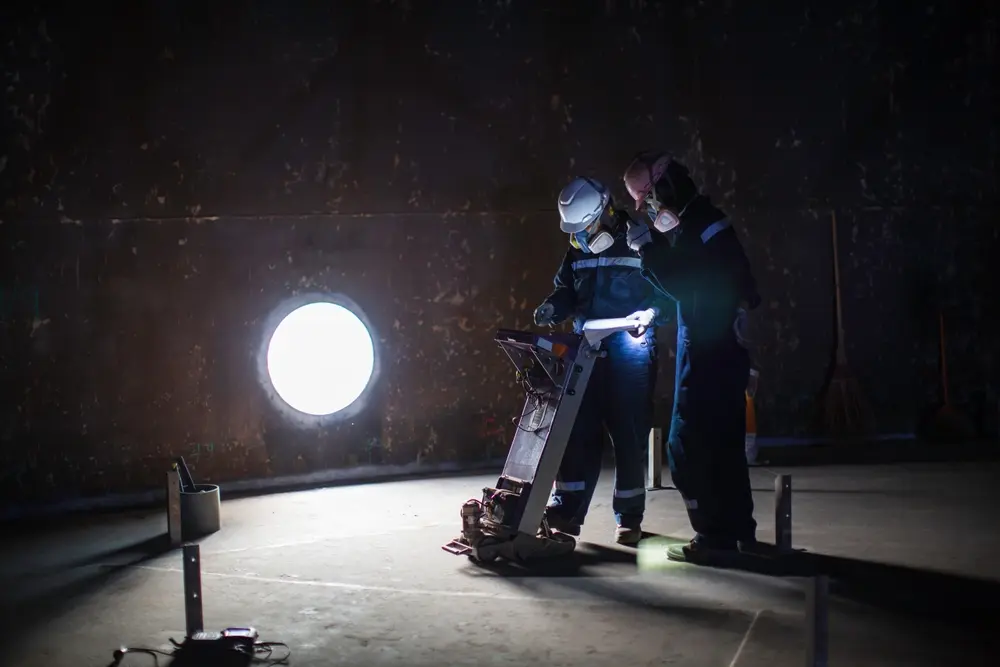
- Maintenance Planning: Based on the results of the inspections, a detailed maintenance plan is developed. This includes scheduling activities such as cleaning, repairs, coatings, technology upgrades, and maintenance strategies so that assets are addressed in a timely manner, reducing costs associated with asset breakdowns.
- Implementation: The execution of the maintenance plan involves the allocation of economic, human, machinery and equipment resources, as well as the coordination of these resources and the implementation of corrective measures. Efficiency in this phase is crucial to minimize downtime.
- Monitoring and Analysis: The final phase includes continuous monitoring of tank performance. Data collection during this stage feeds the continuous improvement cycle of the maintenance management program.
- Tank recovery plan: Even with rigorous maintenance, unforeseen events can occur requiring a quick and efficient response. This is where the tank recovery plan comes into play. This component of the program focuses on developing strategies to address emergency situations, such as leaks, spills or structural damage. The recovery plan must be meticulously prepared, considering various scenarios and adapting to the specific characteristics of each installation. It includes response protocols, intervention teams, and procedures to minimize environmental impacts and protect the safety of workers and the surrounding community.
Emerging technologies in maintenance management
- IoT sensors and remote monitoring : Implementing IoT sensors in tanks allows real-time monitoring of key parameters, such as temperature, pressure and liquid levels. This facilitates early detection of anomalies and proactive maintenance scheduling.
- Artificial Intelligence (AI) and Predictive Analytics: AI algorithms can analyze large data sets to predict the remaining life of tank components. This helps in optimal scheduling of preventative maintenance activities.
- Augmented reality (AR): Used to assist technicians during inspections and repairs. It provides information in real time and facilitates informed decision making. Building on the ability to provide remote instructions, it is enabling new maintenance models, including remote maintenance and maintenance tailored to worker learning and capabilities.
Challenges in tank maintenance management
- Costs: Maintenance management programs involve significant investments. Finding the balance between operational efficiency and costs is a constant challenge.
- Regulatory Compliance: Environmental and safety regulations are constantly evolving. Maintenance programs must be adapted to comply with current regulations.
- Technological complexity: The implementation of emerging technologies can be complex. Staff training and systems integration are critical factors for success.
Benefits of effective implementation
- Reduction of environmental risks: Tank maintenance management minimizes the risk of spills and leaks , thus protecting the environment.
- Resource optimization: An efficient program allows the optimal allocation of resources, avoiding unnecessary expenses.
- Extending useful life: Preventive maintenance and early identification of problems contribute to extending the useful life of tanks.
- Continuous improvement: Data collection and analysis allows for continuous improvements in maintenance management programs.
Conclusion
Storage tank maintenance management is a critical aspect for safety, structural integrity and operational efficiency in various industries. Implementing effective programs, supported by emerging technologies, not only minimizes associated risks, but also optimizes resources and contributes to long-term sustainability. As technology continues to evolve, maintenance management will continue to be a dynamic field, adapting to the changing demands of the industry.
Sources
Own source