Introduction
Storage tanks play an important role in the supply of processed products in the industry, since they allow the collection and availability of raw materials and finished products.
The studies carried out and field experience have revealed that the risks of failure in storage tanks are mainly in the tank bottoms, due largely to the deterioration caused by corrosion on the product side and on the soil side. . To avoid this type of failure, normally the industrial practice is to apply non-invasive monitoring methods, using different inspection techniques, while the tank is in service and thus preserve the integrity of the tanks.
What is tank integrity?
Tank integrity refers to the ability of these devices to operate safely and efficiently, without leaks or environmental risks. This article explores non-invasive methods to assess and ensure such integrity.
Corrosion monitoring in storage tank bottoms
Storage tank bottom corrosion monitoring refers to the continuous monitoring and evaluation of corrosion processes that can affect the structural integrity of the bottom (bottom) of a tank.
Corrosion is a natural process in which metallic materials tend to degrade due to chemical reactions with their environment. Corrosion can be caused by the presence of corrosive substances in the soil, by the stored liquid, by humidity, temperature and other environmental factors that negatively affect the extension of the useful life of storage tanks.
Non-intrusive methods to ensure the integrity of tank bottoms
Monitoring corrosion in a tank bottom while it is operational involves the application of various techniques to evaluate the state of corrosion and take preventive or corrective measures when necessary. Some of the common corrosion monitoring techniques or methods include:
Visual inspection
Direct visual inspection is a common initial method. They are normally used to determine the general external condition of the flange in the critical zone, the behavior of the foundation and the settlement of the tank. However, this method has limitations in terms of access to specific areas.
Acoustic emission (AE)
Acoustic emission testing is a non-destructive testing method used to analyze emitted sound waves caused by defects or discontinuities in the tank. Acoustic sensors detect sound waves caused by events such as corrosion, leaks or the accumulation of gas bubbles. Analysis of special patterns allows you to identify potential problems before they become critical.
Prior to testing, the tank will be maintained at least 50% of its operating level. The AE test involves mounting high frequency sensors on the tank shell (near the bottom).
Data collection is carried out after performing the necessary calibration of the sensors. The recorded data is analyzed by overcoming external noise and characterizing the source of emissions.
The main importance of this technique is that it is carried out with the tanks in service, testing their entire structure at once and detecting leaks at the bottom that would affect the water table.
Magnetic Flux Leakage (MFL)
Magnetic field detection is another innovative technique for tank bottom monitoring. Magnetic sensors strategically placed at the bottom of the tank detect changes in the magnetic field caused by the presence of corrosion or irregularities in the structure. Currently, high-tech software and equipment have been developed for optimal diagnosis in mechanical integrity focused on the new generation magnetic flux loss technique for inspection of tank floors, with high quality in the resolution of the image obtained. and with a power distribution that allows the evaluation of the floor when the sheets are thicker than usual (3/8”).
guided waves
To inspect the critical area in contact with the ground, equipment has been developed that uses ultrasound testing using the qualitative guided wave technique to locate damage in the critical area. The mentioned technique is based on the concept of guided laminar wave impulses that propagate from the transducer towards the annular plate and when there is corrosion, the ultrasonic waves return to the transducer, converting the signal and indicating the discontinuity. The following figure represents how this technique works.
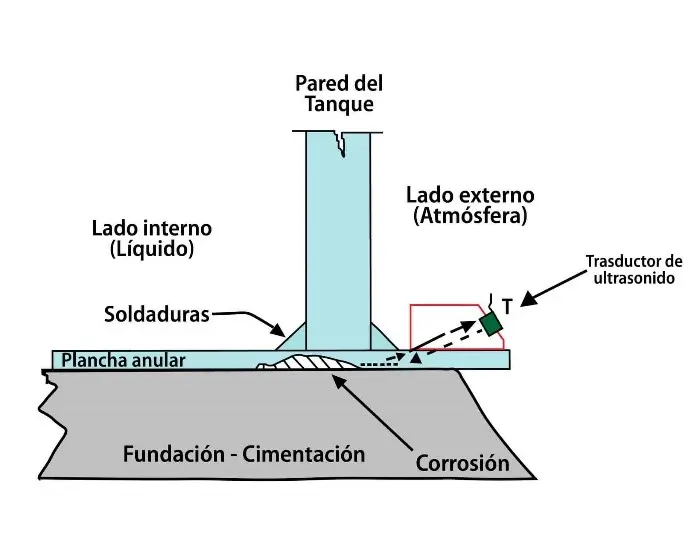
Robotic inspection of tank bottoms
These equipment are designed to access and evaluate the condition of tank floors without the need to empty them or stop their operation. The robots enter the interior of the tank from the roof and land on the floor of the tank, which they evaluate by moving atonically with motorized caterpillars.
The latest generation are equipped with high-resolution video cameras and combined equipment for ultrasonic testing with phase array or pulsed eddy current in high flash point tanks, such as jet fuel, kerosene, distillates or chemicals and Similar refined products, therefore, must be certified to operate in the specific hazardous product environments of Class 1, Division 2, Group D.
Level and pressure sensors
Measuring the liquid level and pressure at the bottom of the tank provides information on sediment buildup. This technique has limitations in the detection of solid contaminants and is not suitable for tanks with viscous products.
Continuous monitoring systems
The implementation of continuous monitoring systems based on the Internet of Things (IoT) allows for the constant collection of data. Connected sensors transmit information in real time, facilitating predictive analysis and early detection of problems.
Integration of technologies for greater effectiveness
Combining different monitoring technologies can offer a more complete assessment of the tank bottom condition. For example, integrating acoustic emission sensors with 3D laser scanners can provide not only information about structural health, but also precise details about sediment accumulation.
Integration Challenges and Considerations
- Technology Compatibility: The integration of various technologies requires careful consideration of compatibility and synchronization between different systems. Effective interoperability is essential for consistent and accurate data.
- Data Analysis: The amount of data generated by multiple sensors can be considerable. It is crucial to implement data analysis systems for tank integrity assessment, such as machine learning and big data, among others, to extract meaningful information and make informed decisions.
- Costs and Return on Investment: Implementing advanced monitoring technologies can entail significant costs. A detailed ROI analysis should be performed to assess long-term economic viability.
Conclusion
The inclusion of methods such as acoustic emission and magnetic field detection in the bottom-hole monitoring of in-service tanks further expands the industry’s capabilities. These advanced technologies offer early detection of potential problems, improving operational security and reducing risks associated with the storage of industrial products. The continuous evolution of these technologies promises a future where tank monitoring is more efficient, accurate and safe.
References
Own source