Table of Contents
- Operating principle of a rotary kiln
- Advantages of a rotary kiln
- What are the differences between a direct-heat and an indirect-heat rotary kiln?
- How does the rotational speed influence the thermal efficiency of the kiln?
- Rotary kiln models
- What are the main industries that use rotary kilns and for which processes?
- Innovations and trends in rotary kiln design
- Conclusion
- References
The rotary kiln is a continuous thermal processing equipment widely used in industrial operations requiring high temperatures and uniform treatment of the material. Its design, based on a rotating cylindrical drum with precise control of parameters such as rotation speed, inclination and heat flow, allows calcination, drying, sintering or incineration processes with high thermal and operational efficiency. This type of kiln plays a crucial role in industries such as cement, mining, chemical and waste treatment, standing out for its versatility, scalability, and adaptability to different operating conditions.
This article analyzes in a technical and detailed manner the principle of operation of a rotary kiln, the available models, their industrial applications, as well as the most recent innovations in their design. It will answer questions about its usefulness, operational advantages and design criteria that directly affect its thermal performance and the quality of the final product. Industrial applications. Through a technical and updated approach, the aim is to offer a complete vision of their importance and evolution in thermal production processes.
Operating principle of a rotary kiln
The operating principle of a rotary kiln is based on heat transfer through a rotating cylindrical drum, slightly inclined with respect to the horizontal. The drum rotates slowly about its longitudinal axis, allowing the processed materials to mix and be uniformly exposed to the heat sources. Continuous heat treatment is achieved by the application of direct or indirect heat, depending on the design of the equipment.
The kiln body is composed of an internal refractory lining that protects the external metal structure from extreme heat and improves thermal efficiency by maintaining a constant temperature during processing. The general parameters you handle are as follows:
- Rotation system: The cylindrical body of the kiln is mounted on bearings or support wheels (tyres) resting on support wheels (rollers). An electric motor, coupled through a speed reducer, drives a pinion that meshes with a ring gear mounted on the kiln cylinder. This mechanism converts the movement of the motor into a slow but constant rotation of the drum.
- Rotation speed: Generally varies between 0.2 and 5 revolutions per minute (rpm), depending on the process and type of material being treated. Slow rotation allows adequate residence time and ensures that all material is uniformly exposed to heat.
- Slope effect: The kiln is inclined with a slope of 1% to 4%, which facilitates that, as it rotates, the material advances by gravity from the charging end (cold) to the discharging end (hot).
- Heat flow: In most cases, the kiln operates with counterflow, i.e. the hot gases from the burner move in the opposite direction to the load. This improves thermal efficiency and allows a gradual heat utilization.
- Burner and combustion zone: At the discharge end is the main burner, which can operate with liquid, solid or gaseous fuels, generating high temperatures necessary for calcination, melting, sintering or incineration processes.
- Kiln zoning: The kiln can be thermally divided into several zones (drying, preheating, calcining, cooling) depending on the industrial process, each of which is designed to achieve specific reactions.
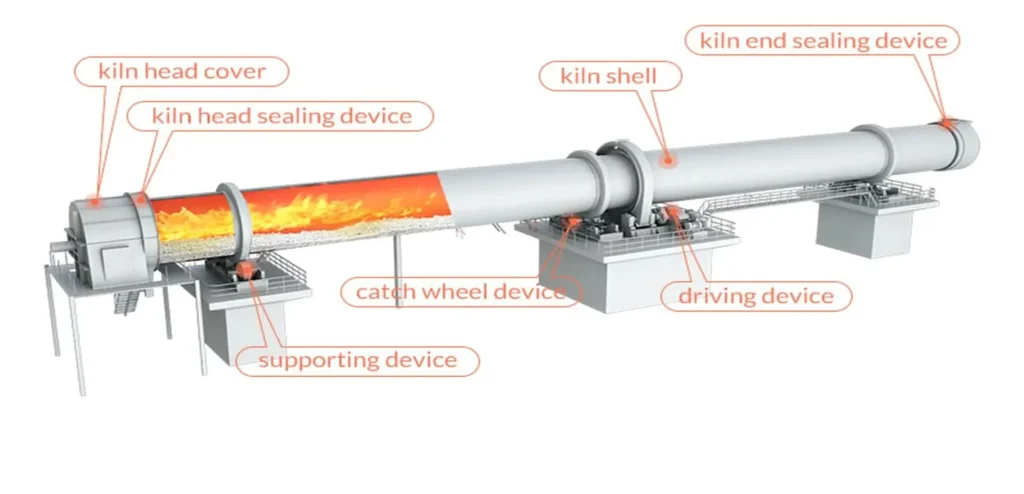
Advantages of a rotary kiln
Rotary kilns offer numerous technical and operational advantages:
- Continuous heat treatment: Facilitates constant material flow and uninterrupted production.
- Final product homogeneity: The rotary action promotes uniform mixing.
- Design flexibility: Can be adapted to different types of processes and materials.
- Thermal efficiency: Modern designs minimize heat loss and reduce energy consumption.
- Emission control: Equipped with filtration and gas control systems.
What are the differences between a direct-heat and an indirect-heat rotary kiln?
- Directly heated rotary kiln: Heat is applied directly to the material by internal combustion of gases, ideal for materials that are not chemically altered by contact with the hot gases.
- Indirectly heated rotary kiln: Heat is transferred through the drum wall, without direct contact with the combustion gases; this model is preferred for processes where an inert atmosphere is required or for sensitive materials.
How does the rotational speed influence the thermal efficiency of the kiln?
The rotation speed of the rotary kiln directly affects the residence time of the material inside the drum, and therefore its thermal efficiency. Too high a speed reduces the heat exposure time, preventing proper treatment. Conversely, too slow a rotation can lead to material build-up and cold spots. The balance between these factors allows for optimal heat transfer and consistent quality of the final product.
Rotary kiln models
There are different models of rotary kilns designed for specific applications. The most common include:
- Direct flame: Uses burners inside the drum. High efficiency for processes such as cement and lime production.
- Indirect flame: Designed with an external combustion chamber. Ideal for the treatment of waste or delicate materials.
- With heat exchanger: Includes energy recovery systems that reuse waste heat.
- Modular: Compact and flexible designs, used in laboratories or pilot plants.
These rotary kiln models respond to the need to optimize thermal processes with different requirements of temperature, time, and type of material.
What are the main industries that use rotary kilns and for which processes?
This equipment has applications in multiple industries due to its continuous operation, controlling extreme temperatures and ensuring homogeneous mixing of materials during heat treatment. The following is a description of the main industries that use them, along with the specific processes:
- Cement industry: For calcining the raw material (a mixture of limestone, clay and other additives) and obtaining clinker. The raw material is subjected to temperatures exceeding 1400 °C, causing sintering and the formation of clinker, the main component of Portland cement.
- Mining and metallurgy: In pyrometallurgy for the reduction of ores and transformation of metallic minerals such as iron, nickel, copper and lithium. They are also essential for smelting and agglomeration of metal concentrates.
- Chemical industry: For dehydration, chlorination, sulfation and pyroprocessing. Rotary kilns enable chemical reactions to be carried out at high temperature, such as the production of metal oxides, the manufacture of fertilizers (e.g. ammonium nitrate or ammonium sulfate), and the heat treatment of intermediates in industrial synthesis.
- Waste management: Incineration, gasification or carbonization of urban, industrial or hospital waste. It is used to destroy hazardous waste under controlled conditions of temperature and time. Thanks to its closed design and constant rotation, it ensures a homogeneous and complete combustion.
- Ceramics and refractory industry: Heat treatment to harden, stabilize or modify physicochemical properties for sintering ceramic materials, firing of refractory bricks, thermal activation of clays and formation of stable mineral phases. Operating temperatures vary between 900 and 1600 °C, depending on the final product.
Innovations and trends in rotary kiln design
Recent technologies have enabled the development of more efficient, sustainable and adaptable rotary kilns:
- Automation and digital control: SCADA systems allow real-time monitoring of the thermal process.
- Advanced refractory materials: Improve lining durability and reduce heat losses.
- Energy efficient design: Use of alternative heat exchangers and fuels.
- Emission reduction systems: Scrubbing technologies that minimize environmental impact.
- Modularity and mobility: Compact equipment for temporary or research installations.
Conclusion
The rotary kiln is a significant tool in industrial calcination, waste treatment and thermal processes in multiple sectors. The diversity of rotary kiln models and their ability to operate continuously with high efficiency make them an indispensable resource in modern industry. The incorporation of technological innovations ensures its relevance in an increasingly demanding and sustainability-oriented industrial context.
References
Own source