Table of Contents
- Introduction
- Understanding Pulsed Eddy Current Array (PECA)
- Applications of the Pulsed Eddy Current Array (PECA) technique in maritime terminals
- Pipelines with corrosion scales and blisters
- Advantages of using Pulsed Eddy Current Array (PECA) technique
- Challenges in implementing Pulsed Eddy Current Array technique
- Conclusions
- References
Introduction
The application of the Pulsed Eddy Current Array (PECA) technique has revolutionized the inspection of structures in maritime terminals, allowing for the assessment of large areas in short periods using pulsed magnetic fields that generate Foucault currents. This enables the precise and efficient identification of imperfections and corrosion damage, ensuring the integrity and safety of assets.
These infrastructures represent crucial links in global trade networks, where the structural integrity of facilities such as mooring bollards, port structures, insulated and uninsulated piping systems directly influences operational safety and efficiency.
Traditional inspection methods involving divers and remotely operated vehicles are costly and pose significant safety risks. These include the removal of concrete or fireproof coatings on structures, insulation on piping systems to assess the condition of internal structural steel, and cleaning external rust layers on corroded pipes, aiming for effective visual inspection.
This article discusses the use of Pulsed Eddy Current Array technology in maritime terminals as an innovative, safer, and more cost-effective solution, detailing its application in various structures, benefits, challenges, and applications.
Understanding Pulsed Eddy Current Array (PECA)
The Pulsed Eddy Current Array (PECA) technique utilizes pulsating magnetic fields to generate Foucault currents, assessing wall loss on the surface of ferromagnetic materials such as carbon steel and cast iron. It provides a relative volumetric measurement that, after calibration in a specific area, translates into an average thickness measurement. PECA is derived from and enhances the Pulsed Eddy Current (PEC) technique. Below is a description of the fundamental principles of each of these techniques.
Operating principle of the single-sensor PEC system
A magnetic pulse is generated by a coil placed at a certain elevation (or separation) from the surface of a component under inspection, which must be ferromagnetic and conductive. During an initial excitation phase, the pulse remains active long enough for the magnetic field to penetrate the entire thickness of the component.
Upon the abrupt termination of the pulse, parasitic currents are induced in the metal mass. These currents generate a secondary magnetic field that can be detected by a magnetic sensor and decays over time. In this phase, known as the reception phase, the sensor generates a voltage signal that is recorded and analyzed. The shape and rate of decay of this voltage signal are directly related to the thickness of the component being inspected1.
Operation principle of the PECA system
It is very similar the previously described principle but with a series of excitation coils connected together to generate the excitation pulse simultaneously at all positions covered by the coil array, being recorded by independent magnetic sensors. This generates a C-Scan image of the component, allowing for a better assessment of the internal metal condition, facilitating its evaluation.
Figure 1, shows a C-Scan image (bottom section) with indications of thickness loss, and the upper image shows the abrupt voltage drop corresponding to the point marked by the pointer in the lower image2.
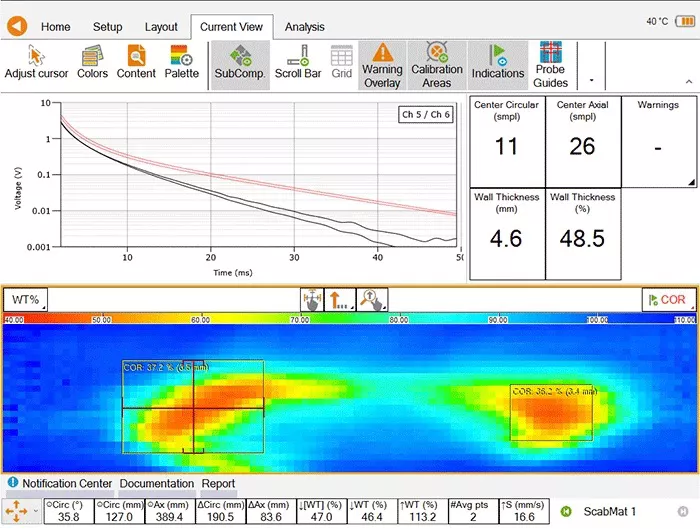
Applications of the Pulsed Eddy Current Array (PECA) technique in maritime terminals
PECA technology is versatile and can be tailored to inspect a variety of structures within maritime terminals, providing a C-Scan image that aids in visualizing the internal condition of the metal. Among its applications in maritime terminals, we can mention:
- Mooring bollards: Mooring bollards, necessary for securing ships during loading and unloading, may suffer from hidden internal corrosion and fatigue damage. PECA enables detailed inspections of these structures, identifying deterioration before it leads to failure.
- Port structures and piers: Including piers and their piles, are continually exposed to harsh marine environments. PECA can assess metal integrity and corrosion under concrete or fireproof coatings (CUI), without the need to remove protective coatings, which is often labor-intensive and costly.
- Corrosion Under Insulation (CUI): Is a significant concern for any hydrocarbon pipeline system, particularly in areas with few escape route options in the event of a flammable gas leak and fire, a potential scenario in maritime ports. PECA is especially effective for detecting CUI, as it can penetrate insulating materials and provide a clear C-Scan image that facilitates interpretation of the metal condition underneath.
Pipelines with corrosion scales and blisters
Removing scales is potentially hazardous for evaluating remaining thickness in pipelines in critical service using traditional methods like Ultrasonics. The Pulsed Eddy Current Array (PECA) technique has been recognized for its ability to detect and size corrosion through blisters and scales in wall thicknesses of up to 100 millimeters (4 inches).
Figure 2, shows an instrument, PECA probe, and semi-rigid pad for constant separation during sensor acquisition.
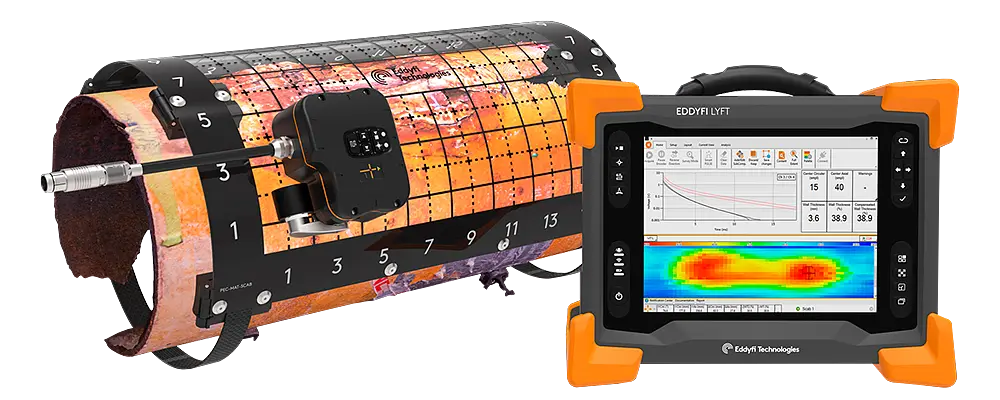
Advantages of using Pulsed Eddy Current Array (PECA) technique
- Non-destructive and safe: The non-destructive nature of PECA allows inspections to be conducted safely from a distance, which is ideal for evaluating hard-to-reach or underwater components.
- Penetration capabilities: Unlike some other non-destructive testing methods, PECA can penetrate several millimeters of non-conductive materials such as marine growth, paint, or rust, reducing preparation time and costs.
- Complete and quantitative data: The pulsed eddy current array (PECA) technique provides quantitative data with an easy-to-interpret C-Scan image that can guide maintenance decisions.
- This capability enhances preventive maintenance strategies, extending the lifespan of critical infrastructure components.
The following video, courtesy of Eddyfi Technologies, shows the High Resolution Pulsed Eddy Current Flaw Detector as a complete solution designed to provide the best estimate of remaining wall thickness on corrosion crusts and blisters that form on the surface.
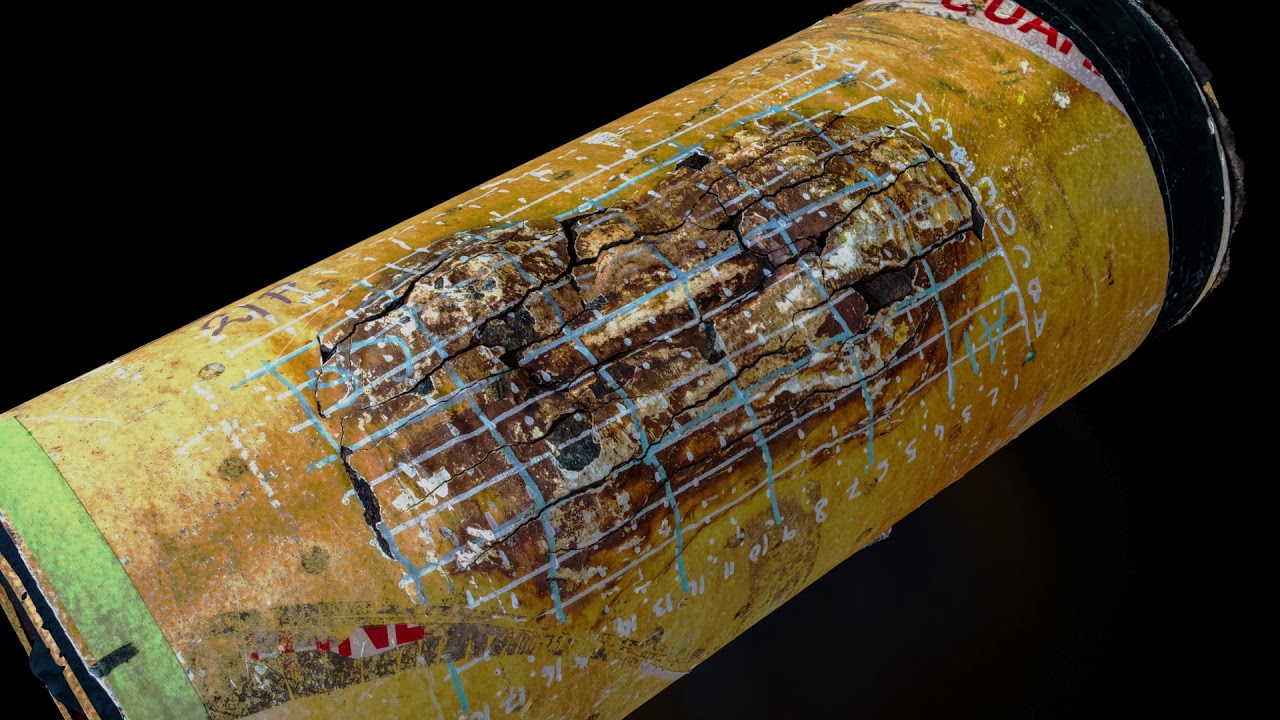
New PECA solution for scale inspections.
Challenges in implementing Pulsed Eddy Current Array technique
- Technical limitations: The penetration depth and sensitivity of PECA can vary depending on the pulse frequency and material properties, which may limit its use in certain situations.
- Environmental influences: Variables such as water salinity, temperature fluctuations, and biological growth can affect the accuracy of PECA measurements. Special calibration and advanced techniques are required to mitigate these issues.
- Expertise required: Interpreting PECA data demands a high level of expertise in both technology and maritime structural engineering. Incorrect interpretations can lead to erroneous assessments, resulting in unnecessary or inadequate maintenance work.
Conclusions
Pulsed Eddy Current Array (PECA) technology significantly enhances inspection processes in maritime terminals. By providing a non-destructive, safe, and efficient method for assessing the integrity of various metallic structures, PECA supports the continuous operation of these vital facilities.
As technology advances, the adoption of PECA in the maintenance routines of maritime terminals is expected to increase, enhancing the reliability and safety of the infrastructure. Overcoming challenges related to technical limitations, environmental conditions, and data interpretation will be key to maximizing the benefits of this advanced inspection method.
References
- GRUPO PIASEC. Pulsed Eddy Currents. Consulted on April 15, 2024; https://www.piesadec.net/?page_id=1983
- VINCENT DEMERS-CARPENTIER, MAXIME ROCHETTE, CHARLES TREMBLAY, MARCO MICHELE SISTO, ANDRÉANNE POTVIN. Pulsed Eddy Current Array design and applications; Consulted on April 15, 2024; https://www.ndt.net/article/nde-india2018/papers/cp059.pdf
- CHARLES TREMBLAY. See Beyond the Corrosion Scab; Consulted on April 15, 2024; https://blog.eddyfi.com/en/see-beyond-the-corrosion-scab?_gl=1*z9rsus*_ga*MTM4NjAxMjA4MC4xNzA1MzMzMzcx*_ga_Q4YHE7GCQH*MTcxMzI5MzI1MS41MC4xLjE3MTMyOTM4MTIuNS4wLjA