Table of Contents
- Introduction
- Pitting corrosion: Concepts and features
- Pitting corrosion mechanism
- How to identify pitting corrosion?
- How to prevent pitting corrosion?
- Corrosion Under Insulation (CUI) and pitting formation
- API 579 and localized pitting corrosion assessment
- Importance of identifying and preventing pitting corrosion
- Conclusion
- References
Introduction
Pitting corrosion is a localized form of corrosion in which cavities or “holes” are produced in the material. It is considered as one of the most dangerous forms of corrosion because they are more difficult to detect, predict, and prevent, causing critical damage to infrastructures.
In this context, accurate detection of pitted corroded areas is crucial during monitoring due to the significant damage it causes to the properties of metals and alloys, especially Stainless steel. These materials are known for their high corrosion resistance due to the formation of a passive oxide film on their surface. However, in certain environments, the properties of this protective layer can be compromised, leading to breakdown and triggering localized attack1.
This article provides a concise overview of pitting corrosion, addressing the mechanism by which it occurs and the problems it causes in metallic structures and other components. In addition, the most advanced techniques for its identification and the most effective control methods are presented.
Pitting corrosion: Concepts and features
Pitting corrosion is a form of localized corrosion, characterized by the formation of small holes on the surface of the metal or alloy. It is difficult to observe because of the small diameter of the pits and because they are often covered with corrosion products, as shown in figure 1. These holes, known as pits, can be very small, but penetrate deep into the material, making them difficult to detect and control in time2.
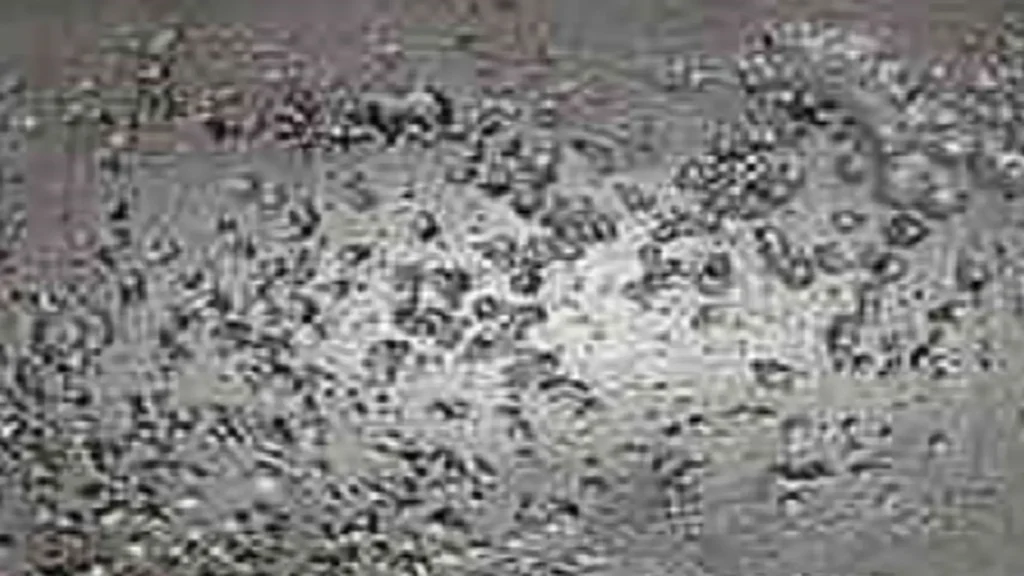
When this corrosion has advanced, it becomes visible to the naked eye and is sometimes found in open areas that are easier to identify, although this is not always the case. Pitting corrosion does not follow a regular pattern and may affect one area of the steel while another remains intact on the same surface. Without adequate protection of the metal surface, small pits begin to develop in the steel when it is exposed to large amounts of chlorides, hypochlorite (chlorine), or bromide ions in the environment.
In advanced stages, pitting can aggressively erode thick steel, leading to leaks. Figure 2, below, shows the different types of pitting corrosion3:
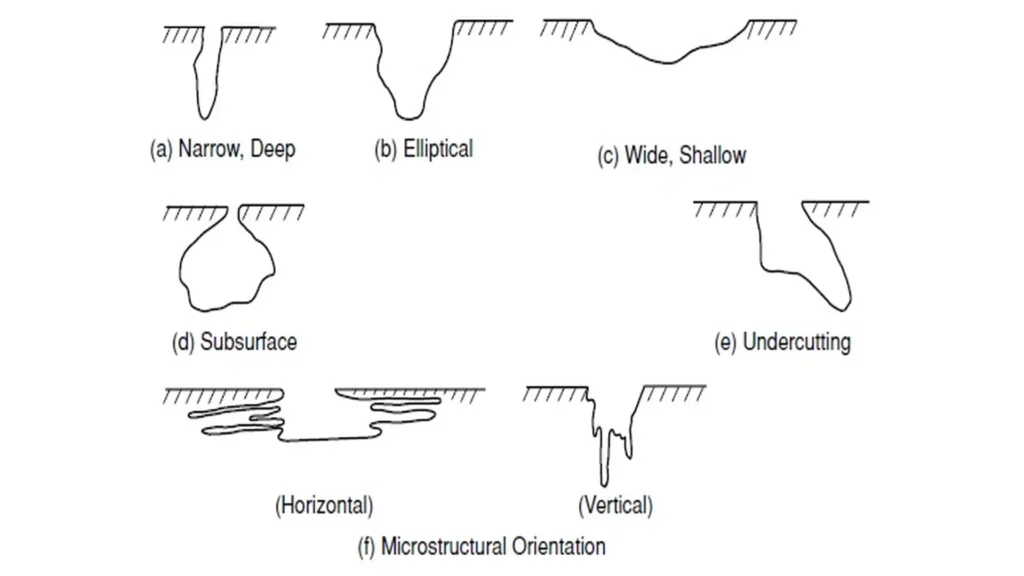
Pitting corrosion mechanism
Steel alloys with an active-passive behavior are particularly sensitive to pitting corrosion, which is generally observed in spaces where there are small amounts of stagnant electrolyte solution, for example, between flanges, bolts, nuts, etc. The presence of chloride ions ( Cl- ) greatly favors the formation of this type of corrosion, it can also occur under corrosion products and other deposits and is then known as under-deposit corrosion.
Chloride attacks the surface of stainless steel by dissolving the passive chromium oxide film producing chromium chloride salt and hypochlorous acid or hypochlorite CLO. The hypochlorite, the active ingredient in the bleach, attacks the base metal, deepening the pitting and forming iron oxide particles. This is the cyclic process that releases chloride as it oxidizes the iron and continues to attack the surface. The iron oxide particles accumulate on the surface around the pit and migrate into the fluid.
The following video shows an animated rendering of the pitting corrosion mechanism in stainless steel, in seawater, which are often used as coolants. Source: Astro Pak.

Stainless steel pitting corrosion mechanism.
How to identify pitting corrosion?
Pitting is incredibly small. Most are invisible (or nearly invisible) to the human eye. In addition, they are frequently covered by a layer of corrosion, which makes them even more difficult to detect.
Identifying pitting corrosion with the naked eye is nearly impossible; however, there are reliable ways to detect it. High-resolution inspection tests, can prevent pitting from causing critical damage to metal structures, so it is advisable to test susceptible materials often. Commonly used testing methods for pitting corrosion include:
Corrosion monitoring techniques
- Visual examination: using a microscope, a professional will count the number of pitting in a given area. This helps them determine their size and distribution, as well as intensity.
- Sonic testing: During sonic testing, ultrasonic sound energy is transmitted through a couplant onto metal. These ultrasonic pulses bounce off the metal and are converted into electrical signals. These signals will show the location of pitting and other imperfections in the metal.
- Electromagnetic testing: This test method is used to locate surface irregularities in conductive metals such as steel and iron.
- Electrochemical testing: Electrochemical testing is another way to test the corrosion rate of metals. During the test, an electric current is applied to the working electrode of the metal.
- Immersion test: A piece of metal is immersed in a solution and left to stand for a few days. After removal, the corrosion rate is determined and the pitting is examined under a microscope to better determine its extent and intensity.
- Characterization tests: Notable among these techniques are: Atomic Force Microscopy (AFM). AFM consists in the detection of forces on the topographic surface of the sample to be studied by scanning, where the previous iteration reflects laser light with a deflection detected by the photodetector and interpreted by the device control system. And the SEM (Scanning Electron Microscope) technique, uses an electron beam instead of a light beam to form an image. Both techniques allow the visualization of a topographical image of the sample surface, they are widely used in the characterization and identification of pitting corrosion.
How to prevent pitting corrosion?
The prevention of pitting corrosion can be achieved through the application of different control methods, among which the use of corrosion-resistant materials is one of the first preventive measures to be taken. Alloys containing titanium, chromium, and molybdenum resist pitting well. Another effective prevention method is cathodic protection, which prevents corrosion by turning a metal surface into an electrochemical cell. Ideally, This metal will act as an anode and will corrode in place of the original metal, preventing pitting.
Other methods to prevent pitting include the use and maintenance of a protective coating and control of exposure to fluids and dust. Applying protective coatings and improving maintenance practices, implementing surface treatments such as passivation and zinc or epoxy paint coatings can significantly reduce susceptibility to corrosion. In addition, maintaining controlled environmental conditions such as reduced humidity, temperature, chloride, acid pH, and corrosive ion levels are also important factors in prolonging the life of metallic components.
To prevent pitting corrosion, it is essential to perform periodic inspections to detect early signs of deterioration. Companies like Acuren provide continuous monitoring and structural integrity assessment services using advanced inspection techniques, ensuring timely detection and reducing the risk of catastrophic failure.
Corrosion Under Insulation (CUI) and pitting formation
Corrosion Under Insulation (CUI) is a condition for the formation of localized corrosion that develops in equipment and pipes covered by insulating material. This type of corrosion occurs when water seeps under the insulation, remaining in contact with the metal surface, creating an environment conducive to corrosion. The presence of moisture and contaminants, such as chlorides, sulfates, and acids, can trigger the formation of pitting, which are small cavities or perforations in the surface of the metal.
The mechanism of pitting under insulation is related to the accumulation of aggressive ions at the metal-insulation interface, which perforate the protective passive film of the metal, initiating the pitting process. As pitting deepens, it can compromise the structural integrity of the equipment, leading to failures if not detected and corrected in time.
API 579 and localized pitting corrosion assessment
API 579 provides guidelines for the assessment and management of damage to industrial equipment due to corrosion, including pitting corrosion. This standard is instrumental in assessing the severity of pitting on components affected by CUI, helping to determine whether equipment can continue to operate safely or whether it requires repair or replacement.
API 579 considers factors such as depth, distribution and size of pitting to classify corrosion severity and provides methods in corrosion control to calculate the reduction in equipment life. In the context of CUI, early detection and evaluation of pitting through proper inspection techniques are essential to ensure the safety and reliability of industrial systems.
Importance of identifying and preventing pitting corrosion
Identifying and preventing pitting corrosion is significant in ensuring the safety, efficiency, and longevity of metallic equipment and structures. Early detection of pitting allows corrective measures to be implemented before significant damage develops. Using advanced inspection techniques, such as ultrasound, visual inspection with high-resolution technology, and electrochemical analysis, is essential for early identification of this type of corrosion. In addition, continuous monitoring and assessment of the operating environment, especially in the presence of chlorides, hypochlorites, or bromides, is critical to anticipate and mitigate risks.
Conclusion
The correct identification and prevention of pitting corrosion are fundamental to ensure the safe and efficient operation of metallic structures. The adoption of detection, protection, and maintenance methods is essential to mitigate the risks associated with this type of corrosion and to extend the useful life of industrial equipment and components. Therefore, it is important to understand the mechanisms associated with pitting corrosion in order to apply the most appropriate control method.
The relationship between CUI and pitting is critical in assessing the condition of insulated equipment, and the use of standards such as API 579 is essential to effectively manage this type of localized corrosion.
References
- Mars G. Fontana; “Corrosion Engineering”; November 1985.
- Edited by. Fuad Khoshnaw, Rolf Gubner; Corrosion Atlas Case Studies: 2021.
- NACE CORROSION;” Engineer’s Reference Book”; Third edition, 2002.