Coatings of graphene, a polymeric nanomaterial, represent an innovative advance in corrosion control. Composed of layers of carbon arranged in a hexagonal structure, graphene is extraordinarily strong and lightweight, promising to transform industries with its versatility and unique properties.
Corrosion, caused mainly by environmental factors such as oxygen, moisture, and electrolytes, represents a significant threat to the durability of metallic materials, reducing their useful life and generating considerable economic costs, as well as posing risks to industrial safety. In response to this problem, scientific studies are currently underway in search of effective solutions to mitigate the harmful effects of corrosion.
Graphene, internationally recognized for its potential properties in different areas, has been the subject of significant investment in research and development projects. This material, used in a wide variety of applications ranging from quantum physics and nanoelectronics to catalysis and materials engineering, has generated great scientific and technological interest1; particularly in the area of corrosion due to its hexagonal structure of carbon atoms that confers a high resistance to wear and abrasion.
In this context, this article presents a brief review of recent advances in the development of graphene as an anticorrosive coating, highlighting its ability to form effective barriers against corrosive agents.
Graphene, its properties and main applications
What is graphene?
Graphene, a material composed of a single layer of carbon atoms arranged in a hexagonal lattice structure, as shown in figure 1, has been recognized as a promising protective coating in various industrial applications. Its structure gives it a number of interesting properties that make it ideal for the prevention of corrosion of various metallic materials.
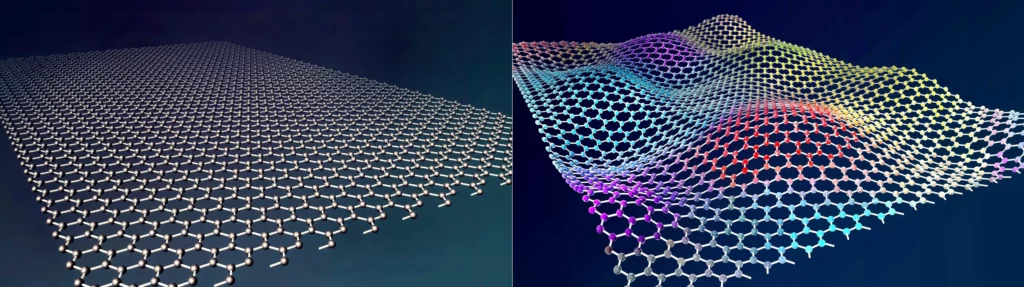
Graphene, an atomically thin two-dimensional film of carbon atoms, exhibits characteristics and properties, which have shown that single or multiatomic layer thick graphene coatings on metals improve their corrosion resistance by up to one and a half orders of magnitude.
Properties of graphene as an anticorrosive coating
This material has a combination of properties that make it highly effective as a protective coating against corrosion. The following is a description of the most outstanding characteristics that qualify this compound as an anticorrosive protective barrier.
- High mechanical strength: It is an extremely tough material, so it can withstand mechanical stresses and protect the underlying substrate from damage.
- Excellent electrical and thermal conductivity: It has a high electrical and thermal conductivity, which allows for uniform current distribution and rapid heat dissipation, helping to prevent the formation of hot spots that can cause high temperature corrosion.
- Waterproof barrier: It is impermeable, a property that prevents the penetration of moisture, oxygen and other corrosive agents, providing an effective barrier against corrosion.
- Environmental compatibility: It is highly resistant to chemical degradation and oxidation, making it suitable for use in a variety of corrosive environments, including marine and industrial environments.
Graphene applications in industry
Its properties such as chemical, moisture, corrosion, UV and fire resistance make it an ideal choice for protecting metal surfaces against mechanical degradation and wear. In industry, graphene coatings act as a protective barrier that prevents the diffusion of corrosive agents, prolonging the useful life of metallic structures and equipment.
Below is a video on the most important applications of graphene. Courtesy of Energeia Graphenemex.
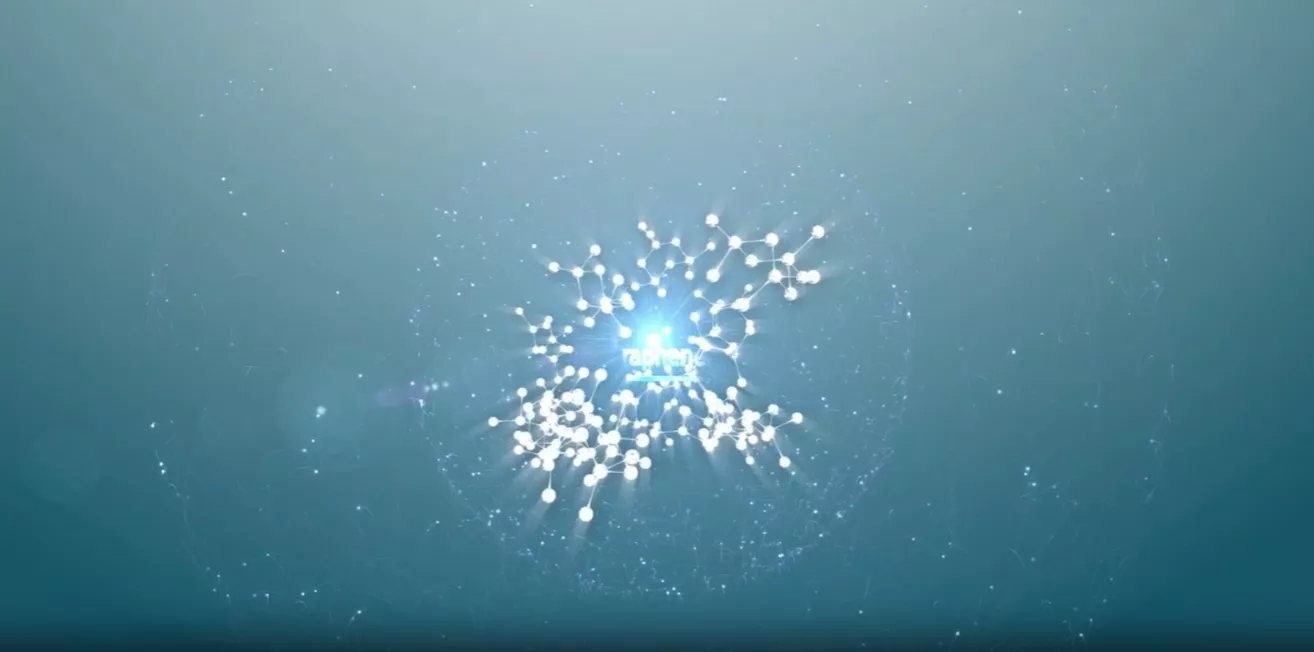
Protection mechanism of graphene barrier coatings
Coatings based on graphene oxide, a new nanotechnological additive that helps control corrosion of metallic materials by forming a barrier that prevents the diffusion of chemical species (barrier effect). The graphene oxide creates labyrinth-like pathways, which prevent the diffusion of oxygen and water molecules through the coating and ultimately do not reach the metal surface, providing protection against corrosion (figure 2). These compounds can act in two ways: (1) by forming a barrier, which largely prevents the penetration of oxygen atoms and water molecules, and (2) by inhibiting the electrochemical reactions of the corrosion process by increasing electrical and ionic resistivity2.
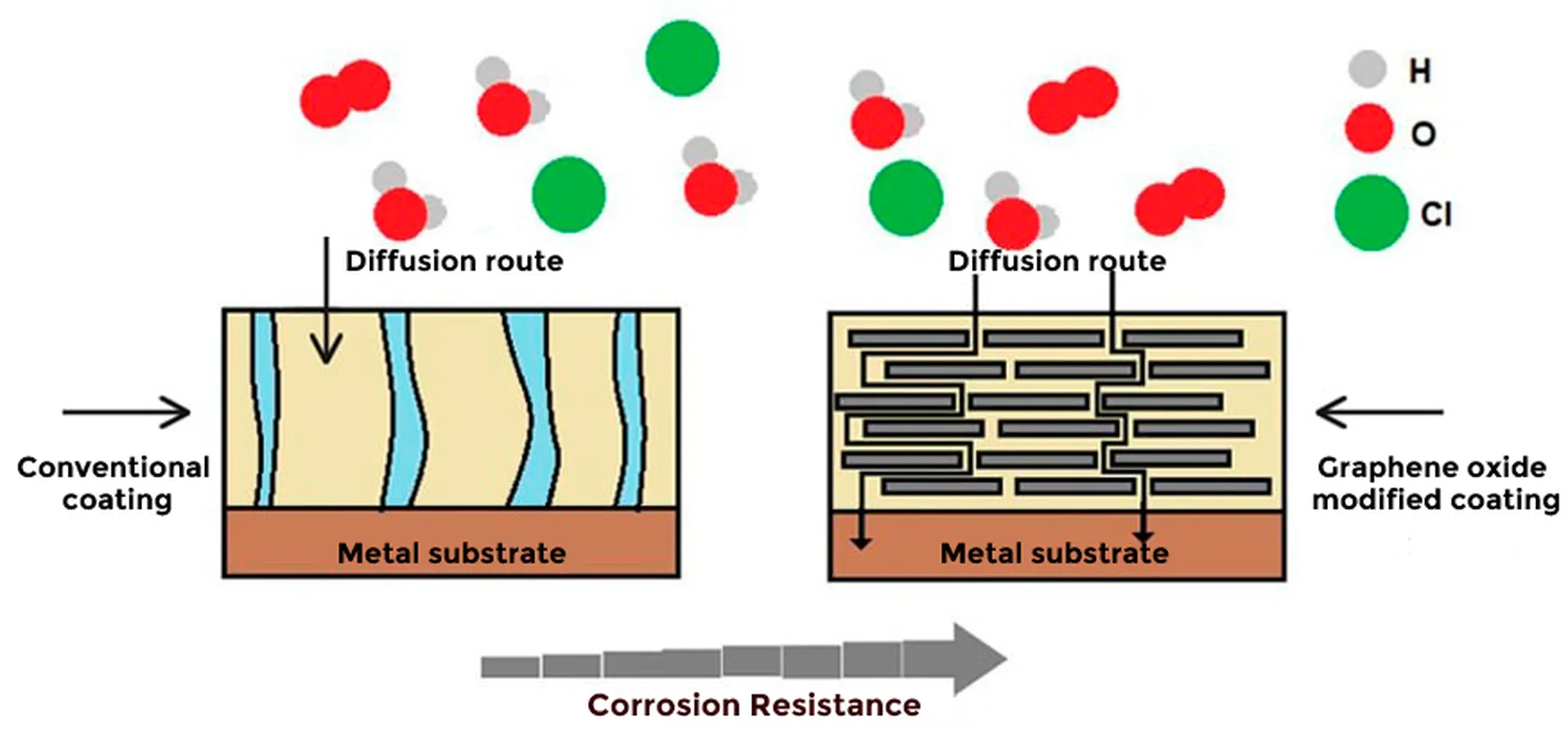
Scientific research on graphene as an anti-corrosion coating
This review summarizes the state-of-the-art knowledge on pure graphene and graphene-based composite coatings, including cathodic protection and self-healing coatings. Special attention is paid to the structure-property relationship and anti-corrosion mechanisms in these systems. Finally, the shared and distinct role of graphene in various coatings and its prospects for future research are also discussed.
Graphene, an extremely thin and tough layer composed of carbon atoms arranged in a hexagonal structure, possesses properties that make it a highly resistant material for use as a protective coating in a wide variety of industrial applications3.
Its layered structure gives graphene exceptional flexibility, while its tensile strength makes it highly resistant to deformation and tearing. In addition, graphene acts as a barrier at the nanometer level, effectively blocking the diffusion of molecules from liquids and gases, making it particularly suitable for application as a coating on metals such as copper, nickel and various alloys3 .
It has also been shown in other studies that graphene is stable and chemically inert. This indicates that it does not react with oxygen when exposed to aerated environments4. It also has a high substrate protection capacity due to its high barrier energy to the diffusion of oxygen atoms5.
In studies conducted by researchers at Rensselaer Polytechnic Institute, South Dakota School of Mines and Technology, Oklahoma State University and Shenyang National Materials Science Laboratory showed that graphene coatings offer enhanced protection against microbially induced corrosion compared to conventional polymer coatings.6.
Specifically, the results of this study showed that the nickel dissolution in a corrosion cell with graphene-coated Ni electrodes was considerably lower than that of parylene-C (PA) and polyurethane (PU) coated electrodes, despite the fact that the graphene coating was much thinner compared to commercial PA and PU coatings. This was attributed to the resistance of graphene to microbial attack and the high conformability and absence of defects in the graphene coating.
As a result, it is suggested that graphene coatings could have great potential in corrosion protection in harsh microbial environments. However, additional research is needed to evaluate the performance of these coatings on other metals and in large-scale applications in the construction industry, especially in adverse atmospheric conditions.
Challenges and future directions
- Identification of the main obstacles in the large-scale implementation of graphene as an anticorrosion coating, such as production cost and standardization.
- Discussion on the need to address issues related to long-term durability and abrasion resistance of graphene coatings.
- Reflection on future prospects for research and development of graphene-based technologies in the field of corrosion protection, including integration with other corrosion prevention techniques and application in new industrial sectors.
- One of the challenges in the development of commercial-scale graphene coatings has been the development of methods for the fabrication of defect-free, large-area graphene films suitable for industrial use. Researchers at the University of Manchester have addressed this problem by first applying graphene oxide laminates and then chemically reducing them to graphene using hydroiodic and ascorbic acids7.
Conclusions
Based on the review made in this article regarding the advances in research on graphene as an anticorrosive coating, it is clear that the results obtained have been significant, demonstrating the ability of this material to function as a protective layer and diffusion barrier against corrosion. These advances have opened up new possibilities for the development of more effective coatings against corrosion in metallic materials.
Despite the great potential of graphene’s properties, significant challenges remain in the successful creation of high-quality coatings. It is important that companies and academic institutions continue to invest in research and development to overcome these obstacles and take full advantage of the benefits of graphene as an effective, corrosion-resistant coating.
Bibliographic references
- Kun Zhou; “Recent progress on graphene-analogous 2D nanomaterials: Properties, modeling and applications”; Progress in Materials Science; Volume 100, February 2019, Pages 99-169.
- Ollik K, Lieder M; “Review of the application of graphene-based coatings as anti-corrosion layers”; Coatings 2020 , 10 (9), 883; https://doi.org/10.3390/coatings10090883
- J. hu, Y. Ji, Y. Shi, F. Hui, H. Duan, and M. Lanza, “A Review on the use of Graphene as a Protective Coating against Corrosion,” Ann J Mater. Sci Eng, vol. 1, p. 16, Nov 2014.
- U. Mogera, N. Kurra, and D. Radhakrishnan, “Low cost , rapid synthesis of graphene on Ni : An efficient barrier for corrosion and thermal oxidation,” Carbon N. Y., vol. 78, no. Cvd, pp. 384-391, 2014.
- M. Topsakal, H. Aahin, and S. Ciraci, “Graphene coatings: An efficient protection from oxidation,” Phys. Rev. B – Condens. Matter Mater. Phys. vol. 85, no. 15, 2012.
- Ghosh Tuhin and Karak Niranjan. Mechanically robust hydrophobic interpenetrating polymer network-based nanocomposites of hyperbranched polyurethane and polystyrene as an effective anticorrosive coating. New J. Chem., 2020, 44, 5980-5994.
- 4. Nair, RR, et al, Nature Communications, 5, article no. 4843 (2014); doi:10.1038/ncomms5843.