Introduction
Pipelines are critical components for transporting fluids, liquids, and gases from one location to another in numerous industrial processes such as oil and gas refineries, chemical and food processing. Piping network systems require rigorous attention to ensure integrity and safe operation. Among the numerous assessment techniques, pipeline hydrostatic testing is the most important methodology for verifying structural integrity and detecting leaks, so it is imperative to carry out regular and rigorous assessments.
Hydrostatic tests are presented as a key tool in this context, allowing to verify the resistance and capacity of the pipelines to withstand operating pressures without leaks. This process consists of filling the pipeline with a liquid, usually water, and applying pressure to detect possible structural failures or weak points. Through the application of these tests, product leaks can be identified, thus ensuring operational safety and prolonging the useful life of pipelines in any industrial application.
In this article, we will discuss the hydrostatic tests used to ensure the integrity of piping systems, highlighting their importance, procedures, and benefits.
Concept and fundamentals of pipeline hydrostatic testing
Hydrostatic testing is used for multiple processes, such as pressurizing a section of pipe to failure with the intention of measuring the maximum strength of that particular section. It is important to understand that there is no one-size-fits-all hydrostatic pressure test.
In line with the purpose of this article, these tests are defined as evaluation procedures that are used to verify the structural integrity and strength of pipelines through the application of hydrostatic pressure. This method is based on hydraulics and is performed by introducing liquid, commonly water, into the pipe until a specific pressure is reached. This pressure is maintained for a predetermined period of time, during which time the pipeline is monitored for any changes in pressure that might indicate the presence of leaks or defects.
Leak test and hydrostatic pressure test
Within the context of pipeline hydrostatic testing, there are two terms which are the tightness test and the hydrostatic pressure test. The tightness test focuses on verifying the tightness of the pipeline, ensuring that there is no fluid leakage, while the hydrostatic pressure test evaluates the structural strength of the pipeline under pressure. Both components are necessary to ensure pipeline integrity and must be performed with precision and care.
Test pressure calculation
To determine the appropriate pressures for pipeline hydrostatic testing, the requirements set forth in design codes such as ASME Code B31.3 or equivalent must be met. This is accomplished by applying the following mathematical equations.
1. For new construction piping: They must be designed under the ASME code. The following equation is used.
Where: PT (hydrostatic test pressure), PD (design pressure), ST (allowable stress at test temperature), SD (allowable stress at design temperature).
Note: The maximum allowable value of ST / SD is 6.5
2. For pipes that have been in service: They were designed under the ASME B31.3 code or equivalent, the equation is used.
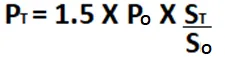
Where: PT (hydrostatic test pressure), Po (working or operating pressure), ST (allowable stress at test temperature), So (allowable stress at operating temperature).
The units of measurement normally used are kg/cm², MPa, Psi, Bar.
When dealing with pipes that have been in operation, their condition history should be taken into account in order to detect possible deviations that could compromise their integrity during the test. It is advisable to conduct additional non-destructive evaluations in order to identify areas of potential concern before proceeding with hydrostatic testing.
Selection of pressure gauges for testing
The proper selection of these devices for hydrostatic testing will significantly affect the accuracy of the results. Here are some steps to follow to select the right pressure gauges:
- Pressure range: The pressure range of the pressure gauges depends on the maximum hydrostatic test pressure. In general, it is recommended that the upper pressure range of the gauge be at least 50% greater than the maximum hydrostatic test pressure. This provides an adequate safety margin and avoids damage to the gauge due to overpressure. However, it should be considered that if the maximum pressure range of the gauge is significantly higher than the hydrostatic test pressure, sensitivity, resolution, and accuracy will be lost.
Accuracy: Use gauges that offer adequate accuracy for your needs. The accuracy of the gauge will influence the accuracy of the measurements obtained during the test. In general, it is recommended to select gauges with an accuracy of 1% or better.
Type of pressure gauge: There are different types of pressure gauges, such as diaphragm, bourdon and digital, among others. The one that best suits the specific requirements should be used, taking into account factors such as ease of reading, corrosion resistance, and compatibility with the environment in which the test will be performed.
Certifications and regulations: Verify that the selected gauges are certified and comply with the applicable regulations and safety standards, to ensure their quality and reliability.
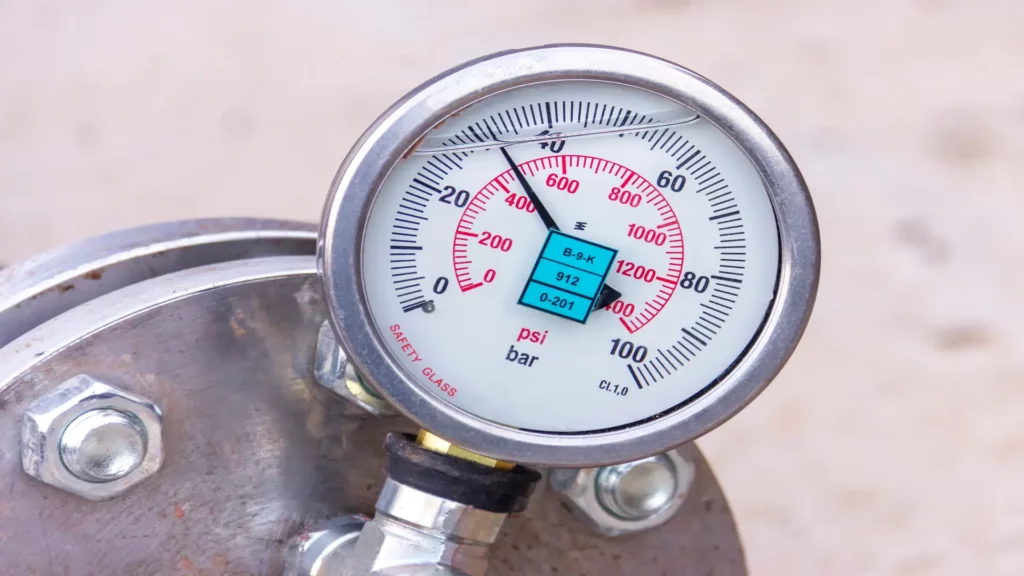
Why should hydrostatic tests be performed on pipelines?
The most important reasons that justify the performance of these tests are the following:
- Verification of integrity and strength: The test allows verifying if the pipeline is able to withstand the pressure for which it was designed. This ensures that the pipeline can operate safely and reliably under normal operating conditions.
- Detection of defects and leaks: The application of hydrostatic pressure can reveal defects in the pipeline, such as cracks, corrosion, defective connections or poor welds. It also helps detect potential leaks that could compromise system efficiency and cause damage or loss.
- Compliance with safety regulations and standards: In many cases, hydrostatic testing is a regulatory requirement or is specified in industry standards and building codes. Complying with these regulations is critical to ensure the safety and quality of the piping system.
- Quality assurance and reliability: Hydrostatic testing is part of Inspection and Quality Control testing procedures during the installation of new pipelines or modification of existing systems. It ensures that pipelines meet the required quality standards and are reliable for long-term use.
- Accident and damage prevention: By identifying and correcting potential structural integrity problems or leaks prior to commissioning, hydrostatic testing helps prevent accidents, economic loss and environmental damage.
Practical application of hydrostatic testing in pipelines
Hydrostatic tests are applied to validate the resistance and tightness of pressurized pipelines. This process consists of filling the system with a liquid, generally water, and applying a pressure higher than the operating pressure to detect possible structural failures or leaks before putting the system into service. To ensure that these tests are carried out safely and in accordance with international standards, it is essential to have specialized personnel, certified procedures and appropriate equipment.
In this type of critical operations, companies like Acuren are fundamental to the industry. With a strong track record in industrial inspection, non-destructive testing (NDT) and asset integrity services, Acuren offers specific solutions for hydrostatic testing of piping systems. Its approach combines technical expertise, advanced technology and regulatory compliance for the evaluation of critical systems, ensuring reliable and safe results.
Test procedures and integrity assessment
Hydrostatic testing of piping systems follows a standardized test procedure involving the following three steps:
Prior to hydrostatic testing
- Test planning: Develop a detailed plan for the test, including the maximum pressure to be applied, test duration and safety procedures.
- Cleaning: Piping should be thoroughly cleaned to remove any debris, obstructions or foreign material that may affect the hydrostatic test results.
- Water quality for testing: The appropriate fluid is potable water, unless there is a possibility of damage from freezing or other adverse effects. In this case, another adaptable non-toxic liquid may be used, if its flash point is greater than 120°F (49°C). For austenitic stainless steels at risk of corrosion cracking due to polychromic stress corrosion, as referred to in NACE RP0170-2004.
- Blocking of pipe sections: The piping to be tested should be blocked or isolated from the rest of the system by installing blind discs or other retaining device that are clearly identified for later removal.
- Visual inspection: Perform direct visual inspection to verify that all planned work is completed, and that quality tests, mainly weld tests, are executed and approved.
- Equipment preparation: Ensure that all equipment necessary to perform the test is in good condition and working properly. This includes water pumps, calibrated pressure gauges, pressure chart recorder, shut-off valves, hoses, among others. For redundant control, it is advisable to install at least two pressure gauges with appropriate ranges.
- Safety considerations: Before starting the test, make sure that all necessary safety measures have been taken. This includes the use of appropriate personal protective equipment, training of the personnel involved and implementation of emergency procedures.
During hydrostatic testing
Fill the pipeline with the test fluid from the lowest point of the piping system and drain or pulse the air at the highest point of that system. Subsequently, the following is performed:
- Apply pressure: Pressure is gradually applied to the system in a stepwise manner. First at 50% of the test pressure for 5 minutes perform a visual inspection of the pressurized system, then take it to 75% for 5 minutes with another visual check and finally take it to 100% of the test pressure for 60 minutes.
- Continuous monitoring: Closely monitor the test at all times to detect any deviations or leaks immediately.
- Pressure control: Carefully adjust the pressure applied to the piping in accordance with design specifications and safety regulations. Consider that elevated ambient temperature may heat the piping and increase the pressure.
- Data logging: Record pressure data and any relevant observations during the test for later analysis.
After hydrostatic testing
- Controlled depressurization: After completing the test, be sure to depressurize the piping in a controlled manner to avoid damage or injury. This may involve gradually opening valves and gradually releasing pressure.
- Gradual pressure relief: Upon completion of the test, release pressure in a gradual and controlled manner to avoid damage to piping or equipment.
- Post-test inspection: Perform a final inspection of the pipeline for any signs of damage or deformation caused by the test.
- Blind disc removal: Ensure that all blind discs are removed at the end of the test.
- Documentation of results: Document the results of the test, including any anomalies detected and corrective actions required.
- Follow-up recommendations: If problems are identified during hydrostatic pressure testing, recommendations should be followed to repair or replace the affected parts of the pipeline.
- Documentation and record keeping: It is important to document all relevant details of the test, including the pressures applied, the duration of the test, any incidents or anomalies observed, and the results obtained. These records are necessary for future reference or safety audits.
Below is a video on the procedures for hydrostatic testing of pipelines. Source: APS (American Pipelines Solutions).

Hydrostatic test 12″ steam line.
Conclusions
Pipeline hydrostatic testing plays an indispensable role in maintaining the structural and operational integrity of pipeline systems. By providing an accurate assessment of pipeline strength and tightness, these tests contribute significantly to the safety and reliability of industrial operations.
While there are challenges associated with hydrostatic testing, its importance in accident prevention and environmental protection justifies its continued application and the development of improved techniques in the future. Investing in pipeline hydrostatic testing is a proactive measure that benefits both business and society at large, ensuring a safe and sustainable working environment.
References
Own source