Introduction
During the gas transportation procedure, it is important to maintain the integrity of the pipeline and the fluid it transports; which can be achieved through scheduled inspections and cleanings; thus, any solid or fluid that affects the transport process must be eliminated from the interior of the pipe. When the pipeline presents irreparable damage, it is necessary to make the corrections that allow controlling and/or solving the problem; avoiding putting the integrity of the transport system at risk.
Operational problems such as fatigue and rupture of the gas pipeline material, gas leaks or decrease in production; trigger economic loss, equipment damage and/or injury to workers; which makes the use of tools that allow support in the correct selection of the internal cleaning and maintenance tool in accordance with the operational and integrity requirements of the gas pipeline unavoidable.
Currently, the gas industries (figure 1a) require a comprehensive program to improve the safety of their natural gas transmission pipeline systems (figure 1b). A variety of tools are used to check the condition, soundness, and safety of pipelines. These tools range from field leak studies using sensitive detection equipment to online inspections and pressure tests.
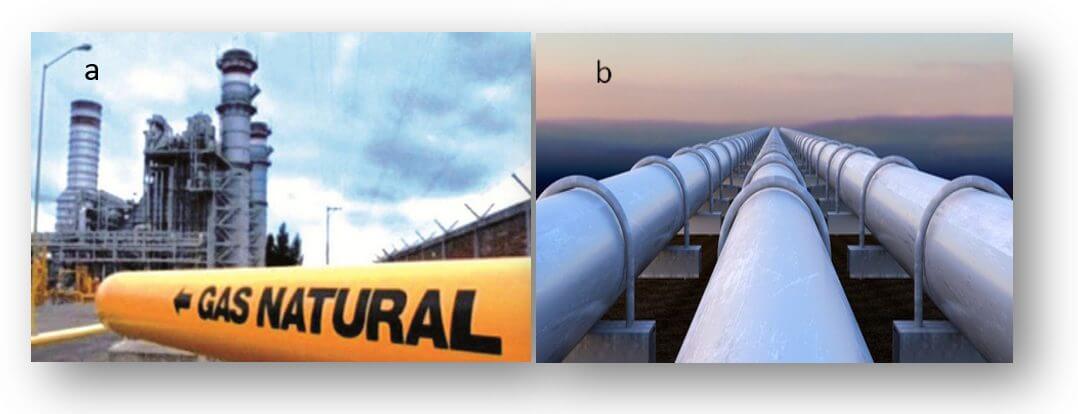
Integrity Assessment
One of the most representative stages to be considered in a Piping System Integrity Management Program for the transport of hazardous fluids is the evaluation of the integrity of the sections that make up a pipeline, in order to identify the deterioration caused, know its condition and determine its remaining useful life to continue in service, and establish the need for measures such as repair or replacement.
It is important to subject the gas pipeline to preventive maintenance that allows avoiding or reducing problems that affect its integrity; One of the ways is using tools for cleaning and internal inspection of the pipeline. The correct selection of these tools allows to obtain an optimal solution to the possible problems that arise in the pipe; thus achieving that the entire system works optimally and can meet the requirements and objectives set
For this integrity evaluation, the Recommended Practice (PR) API 1160 [1] is available, where the techniques to be considered are suggested:
- Hydrostatic test: to carry out this test it is necessary to place the section of pipe to be evaluated out of service, fill it with water or another suitable fluid until reaching a pressure greater than the operating pressure for a certain time. If the section fails because it does not meet the conditions to maintain this pressure, it is necessary to locate, repair the fragment and carry out the test again before putting the pipeline back into operation. These types of tests are widely used when the pipeline cannot be inspected internally.
- Direct evaluation: This type of evaluation integrates specific information on a type of threat (external corrosion, internal corrosion, Stress corrosion cracking (SCC), for example) to determine segments with a high probability of failure, which will later be directly examined with non-destructive techniques that allow an estimated diagnosis of the condition of the pipeline. For which, you must have access to the identified sectors; however, on some occasions this entry is not feasible (for example, in jacketed pipes, river or road crossings, or dangerous excavations).
- In-Line Inspection (ILI): This method also known as Online or In-Line (Smart Pigging) is one of the most used methodologies in the inspection of the real state of the pipeline, it is carried out through the use of tools, which are inserted inside the pipeline, and They travel with the product flow to perform specific cleaning or inspection tasks. Among the most commonly used are magnetic flux leakage (MFL), ultrasound (UT), electromagnetic-acoustic transducers (EMAT) and eddy current transducers (ET).
Gas pipeline inspection and maintenance tools
Hydrostatic test
Method applied with the purpose of guaranteeing the hermeticity and integrity of gas pipes, and locating possible fault weaknesses.
Hydrostatic testing is a proven method to verify the ability of a natural gas pipeline to operate at a safe level of pressure (known as the maximum allowable operating pressure, or MAOP), in order to ensure the reliability of the installation during its normal operation.
The design codes for equipment and piping systems Integrity according to API 1160 / ASME B31.8, among others, clearly establish the recommended practices on how to perform hydrostatic testing, in order to guarantee the physical integrity of people and equipment . Figure 2 shows the Hydrostatic test equipment and the installation of the connections that will be used to raise pressure.
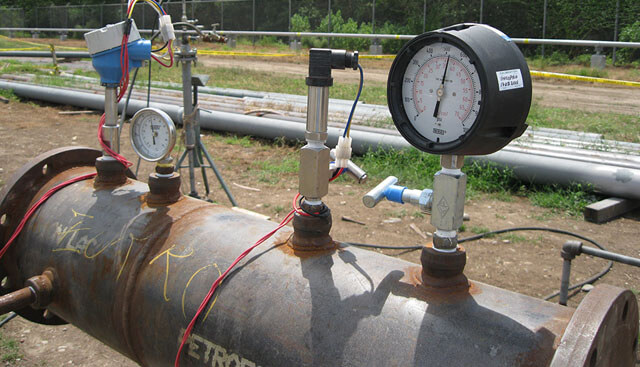
Steps to perform Hydrostatic Tests
Performing a hydrostatic test involves the following steps:
- The section of pipeline to be tested is removed from service and purged of all natural gas, and the interior is mechanically cleaned.
- The section is sealed at both ends and completely filled with water.
- The water is pressurized to the test pressure.
- The test pressure is maintained and monitored for a set period of time, typically 8 hours. If there is no pressure loss, then the section of pipe is emptied, dried completely and returned to service.
- If a section does not reach or hold pressure, that means hydrostatic test pressure has caused the pipe to leak or rupture. If that happens, the leak is located, repaired, and the section of pipe is retested.
All new equipment must be subjected to a pressure test (hydrostatic), in the workshops or in the same way it is carried out in the field in the case of a construction or industrial project.
The hydrostatic test also applies when existing lines are replaced or repaired and allows: determining the quality of the execution of the work of manufacturing or repairing the line or equipment, checking the operating conditions to guarantee the safety of both people and installations and finally detect leaks.
Internal inspections of lines or pipes
Internal line inspection or in-line inspection (ILI) devices available, there are devices called “Smart Pigs” (Intelligent Pigs) can be equipped with robotic cameras and sensors to verify the thickness of the pipe and welds, also detect flaws by corrosion (figure 3).
The main disadvantage of Smart Pigs is that the line must be designed to accommodate these devices (i.e. Smart Pig insertion and removal points, smooth transitions between pipe segments, minimum radius turns, same diameter pipe segments, valves without stopper, etc.). The vast majority of pipelines in gas industries were designed and built before the Smart Pigs technology was developed. These lines would require significant reconstruction to accommodate line inspections.
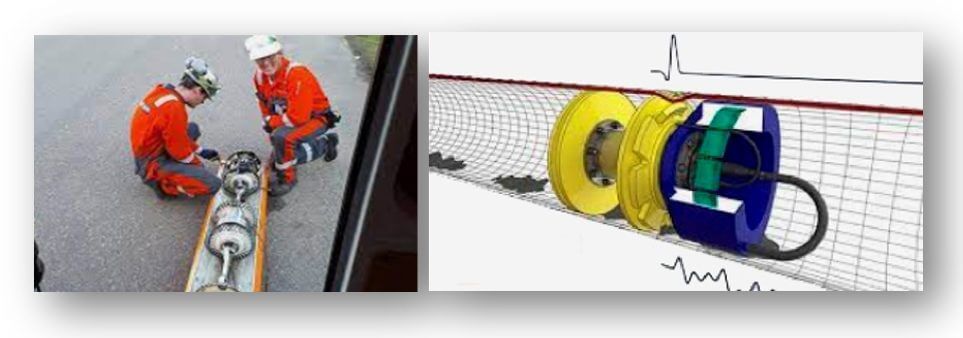
Quest Integrity Group’s InVista™ Online Inspection Tool[3]
Quest Integrity uses smart pig technology to inspect and assess pipelines in refineries and chemical plants. InVista™ technology, based on ultrasound, represents an innovative evaluation option for the Inspection Program of pipes or ducts of industrial plants.
inspection results and reporting formats are tailored to match established plant schedules per API 570 and 574 [2]; and the information obtained during the inspections can be applied to perform an assessment of remaining useful life and adequacy using Life Quest software proprietary to Quest Integrity Group.
Older designed pipelines, including those located in high population areas, have geometries such as small radius bends and diameter changes; which, have led to classifying them as “non-inspectable”. Quest Integrity Group’s InVista™ inspection tool is capable of inspecting such pipes and providing 100% surface information, which cannot be inspected by other ILI tools.
The tool is capable of navigating elbows or curves of 1 diameter, it is a very easy tool to modify to the need of the pipe, Inspections carried out on pipes with 6 “/8” diameter and another of 8 “/10” diameter , have shown that the tool can not only navigate the pipe, but is also capable of collecting the complete information of a pipe with multiple diameters.
InVista is designed to detect and quantify the problem of corrosion under insulation CUI and each of the deterioration mechanisms prevalent in piping or vertical circuits internal deterioration mechanisms are also recorded with the same level of precision since a large percentage of piping circuits or ducts are not accessible due to external insulation, high heights or because they are buried lines.
Accurate detection and quantification of defects are critical elements in ensuring plant operation continues smoothly without experiencing a sudden loss of content in addition to the loss of metal from the walls. The tool also detects dents, blisters, deformations, and validates the information collected, also during the inspection process if there is no access to the interior of the pipe or duct at the end of the route. This tool has the technology to travel back and be collected at the same launch point only by reversing the flow.
Once the inspection is finished; it is checked to verify any potential contamination of dangerous substances, the external shape of the tool allows an easy decontamination; if so, it is required after verifying and removing the contaminants the information collected is immediately downloaded to a computer and the results of the inspection are analyzed by a certified technician, the results of the inspection are generated and delivered to the client some hours after the inspection inspection reports are modified in their formats to adapt them to the inspection programs of pipes or ducts of the plants according to API 570 or API 574.
Being the tool capable of collecting all the information in a single pass, the tool lowers the operational cost associated with online inspection. Additionally, the InVista™ tool’s high-fidelity ultrasound-generated database can be rapidly evaluated using the company’s LifeQuest™ Pipeline software to deliver an API evaluation of the pipeline. 579 Level 2 in the final inspection report.
Below is a video of the InVista device, courtesy of QuestIntegrityGrp.

Process Pipeline Inspection for Refineries and Chemical Plants.
Visual inspection in pipes with Video Cameras in gas lines
Visual inspection inside pipes can be performed remotely through guided video cameras or through the use of videoscopic probes (Figure 4). Camera inspection involves digging several holes along the transmission line in order to insert a tethered camera that will record the internal conditions of the pipeline. The video images from the camera will be transmitted to a nearby monitoring and recording device, which will then be analyzed by trained professionals and will determine if further action is necessary.
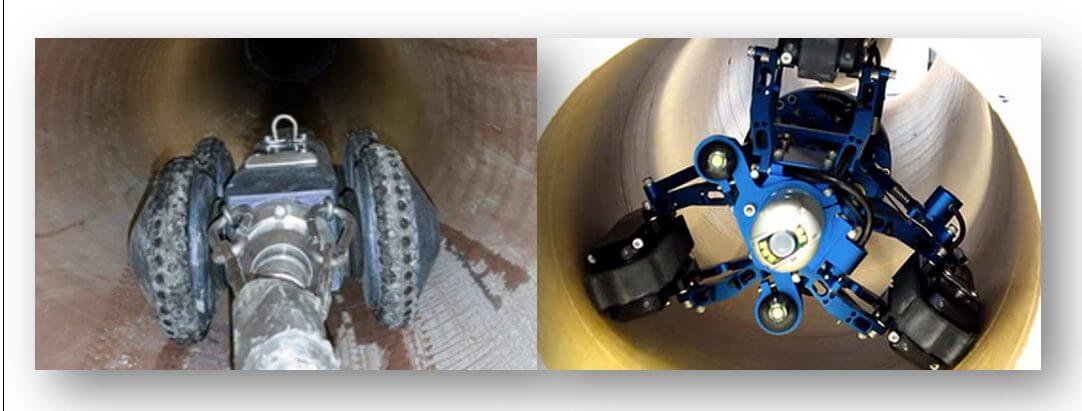
To perform an inspection with cameras, it involves the following steps:
- Various holes or pits will be dug along the transmission line to access the underground pipeline.
- The pipeline is temporarily taken out of service and sealed from the rest of the system.
- Once the pipeline is closed at both ends, it will be purged of natural gas so operators can safely open and work inside the pipeline.
- At this point, a camera will be inserted into the pipe to record internal conditions.
Conclusion
Pipeline integrity involves ensuring that the pipeline and all of its related components are working properly. It is important to establish a Pipeline System Integrity Management Program for the transport of gases, hydrocarbons and dangerous fluids, in order to identify deterioration, establish the need for measures such as repair or replacement, subject the gas pipeline to preventive maintenance to avoid o reduce the problems that affect its integrity; that guarantees that pipelines are designed, built and operated to be safe, reliable and sustainable.
References
- API RP 1160 (2013) Managing System Integrity for Hazardous Liquid Pipelines.
- API 570/574 Piping Inspection Code.
- Quest Integrity Group: https://www.youtube.com/watch?v=OLqqWq88GlM