Table of Contents
- What is Oxyfuel cutting equipment?
- Oxyfuel cutting equipment components
- Gases used in oxyfuel cutting equipment: advantages and disadvantages
- Comparative table of gases
- Oxyfuel cutting equipment process
- Oxyfuel welding process
- Recommended materials for oxyfuel cutting equipment
- Recommended materials for oxyfuel welding
- Conclusion
- References
Oxyfuel cutting equipment is a system widely used in the metalworking industry. Its versatility makes it an indispensable tool in the maintenance and construction industry. This system, which combines combustible gases and oxygen to generate a high temperature flame, allows carrying out both cutting and welding tasks, adapting to different industrial and artisan applications.
In this article, the operation and components of this equipment are described, as well as the cutting and welding processes, the types of gases used, their advantages and limitations. The materials that can be worked with this technique, and those that are not suitable.
What is Oxyfuel cutting equipment?
It is a set of tools and components designed to make cuts and welds in metals by means of the controlled combustion of a combustible gas, such as acetylene, and oxygen. This system, which can be manual or automatic, generates a high temperature flame capable of melting and oxidizing the material, allowing its separation or joining.
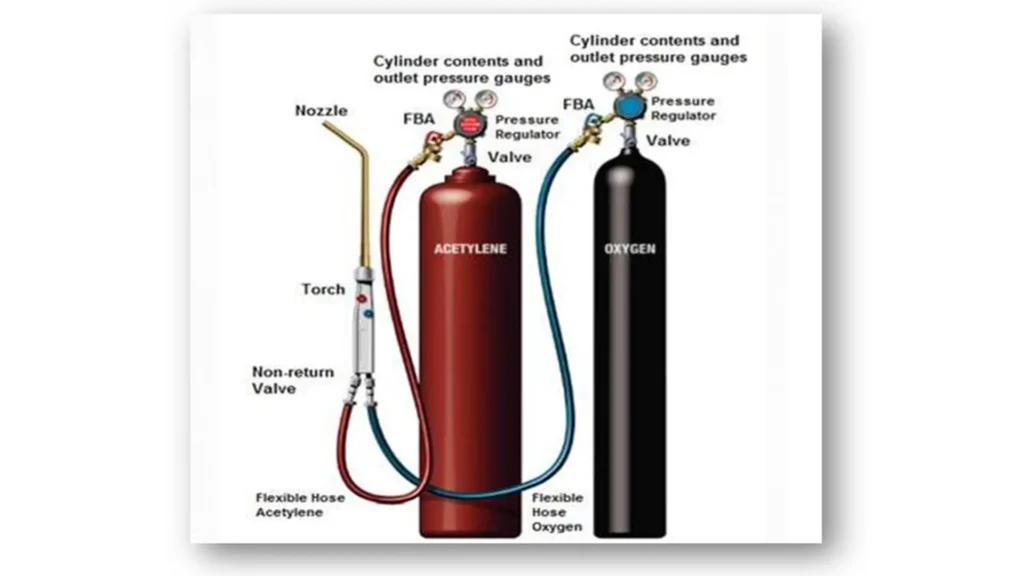
Oxyfuel cutting equipment components
To ensure safe and efficient operation, an Oxyfuel cutting equipment includes the following elements:
Oxygen cylinder: provides the oxygen needed to intensify gas combustion and reach the required high temperatures. This gas is stored in steel cylinders at high pressure.
Fuel gas cylinders: It can be acetylene, propane, natural gas, MAPP or hydrogen, depending on the type of application. Acetylene is the most common, since it generates the highest temperature flame.
Pressure regulators: These are devices connected to the cylinders that control the pressure and flow of gases into the system. Each cylinder has its own regulator, designed to maintain a precise ratio between oxygen and fuel gas, ensuring stability and safety during the work.
Hoses: Transport the gases from the cylinders to the torch. These hoses are flexible, resistant to high pressures. To avoid confusion, they are color-coded green for oxygen and red for fuel gas.
Oxyfuel torch: The torch is the centerpiece of the equipment and is used to mix the gases and generate the flame. It has two main functions:
- Preheating flame: heats the metal material to its ignition temperature.
- Oxygen flux: Facilitates cutting by reacting with the hot metal, forming oxides that are expelled as slag.
Here are different types of torches, including the acetylene torch for welding and the cutting torch for separating materials.
Nozzles or nozzles: These are interchangeable accessories located at the tip of the torch that control the shape and size of the flame. There are specific nozzles for straight cuts, grooves, welding, or angle cuts.
Automated torches: Similar to manual torches, but mounted on motorized equipment.
Programmable controllers: For automatic systems. They allow predefining trajectories and parameters, such as feed speed, gas pressure and temperature.
Motors and rails: Elements of the automatic system that facilitate the uniform movement of the torch along the material.
Sensors: Monitor critical variables in the automatic system such as gas flow and distance between the torch and the material.
Backflow preventers: These are safety devices that prevent the flame or gases from returning to the interior of the hoses or cylinders, which could cause explosions. They are installed on torch connections and regulators.
Igniter or spark igniter: Used to safely ignite the gas mixture in the torch. This device generates a spark, eliminating the need for matches or lighters, which could be hazardous in flammable gas environments.
Personal Protective Equipment (PPE): Although not a direct part of the Oxyfuel cutting equipment, it is necessary for operator safety. It includes welder’s goggles or face shields, heat-resistant gloves, flame-resistant clothing and safety boots.
Rails and guides (in automatic systems): On automatic oxyfuel equipment, guides, or rails are included to ensure precise torch movements. These accessories are especially useful for long or repetitive cuts.
Gases used in oxyfuel cutting equipment: advantages and disadvantages
The operation of Oxyfuel cutting equipment is based on the combination of combustible gases and oxygen. The main gases used are:
Acetylene (C₂H₂): this is the hottest gas available for oxyfuel, with a maximum flame temperature of approximately 3,160°C (5,720 °F). This makes it ideal for cutting thick materials and making precise cuts quickly.
Disadvantages: It is chemically unstable, especially at high pressures or when compressed without a suitable solvent such as acetone. This makes it a gas that requires careful storage and handling. In addition, its cost is considerably higher than that of other gases.
2. MAPP (Mixture of methylacetylene and propadiene): It has a hot flame, although slightly lower than acetylene, reaching approximately 2,900°C (5,252°F). It is safer than acetylene, as it is not as unstable and can be stored at higher pressures.
Disadvantages: Its availability has decreased in recent years due to reduced production. Also, it does not produce as precise cuts as acetylene in certain jobs.
3. Hydrogen: It is a gas of high availability and low cost compared to some gases. It produces a clean flame, with no carbon residue and is lighter than other gases. It is used for cutting reactive materials or for applications where flame cleanliness is required, such as in aerospace or electronic environments. It is used for underwater cutting and welding:
Disadvantages: The 2,800°C (5,072) temperature of its flame is lower than that of acetylene; therefore, it is less efficient for cutting thick materials. It is highly flammable and explosive, which requires extreme safety measures during storage and handling.
4. Propane (C₃H₈): More economical than acetylene and MAPP, it offers cleaner combustion, leaving less soot residue. In addition, its wide availability makes it a popular choice in a variety of applications.
Disadvantages: Its flame has a lower maximum temperature, around 2,825°C (5,117°F), which makes it difficult to cut thicker materials quickly or accurately.
5. Propylene (C₃H₆): It is an alternative to propane, with competitive thermal performance, although less available. It combines a balance of good temperature, cleanliness and moderate cost.
Disadvantages: Maximum flame temperature in oxygen is 2,870 °C (5,198 °F). The total calorific value of the may make it difficult to cut thicker materials quickly or accurately.
6. Natural gas or methane (CH₄): It is the cheapest gas among the available options for oxyfuel and is widely available in most regions. It is an environmentally friendly option as it produces fewer emissions compared to other gases.
Disadvantages: Its maximum temperature is 2,800°C (5,072°F), its low supply pressure (when sourced directly from urban networks) limits its use for large-scale industrial applications. In addition, its flame temperature is the lowest of all, which reduces its effectiveness for thick and fast cuts.
Comparative table of gases
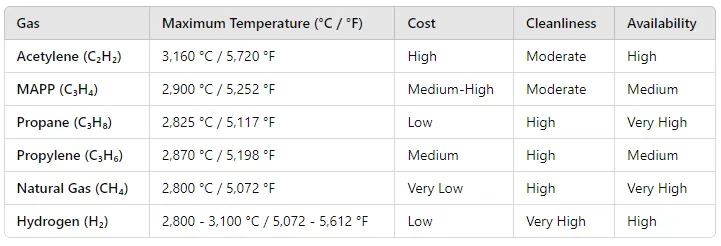
Oxyfuel cutting equipment process
This process can be performed manually or automatically and is based on heating the metal to its ignition temperature and then rapidly oxidizing it with a jet of oxygen.
- Manual systems: These are the most traditional and are operated directly by a technician, who controls all the variables of the process, from the handling of the torch to the quality of the cut or weld.
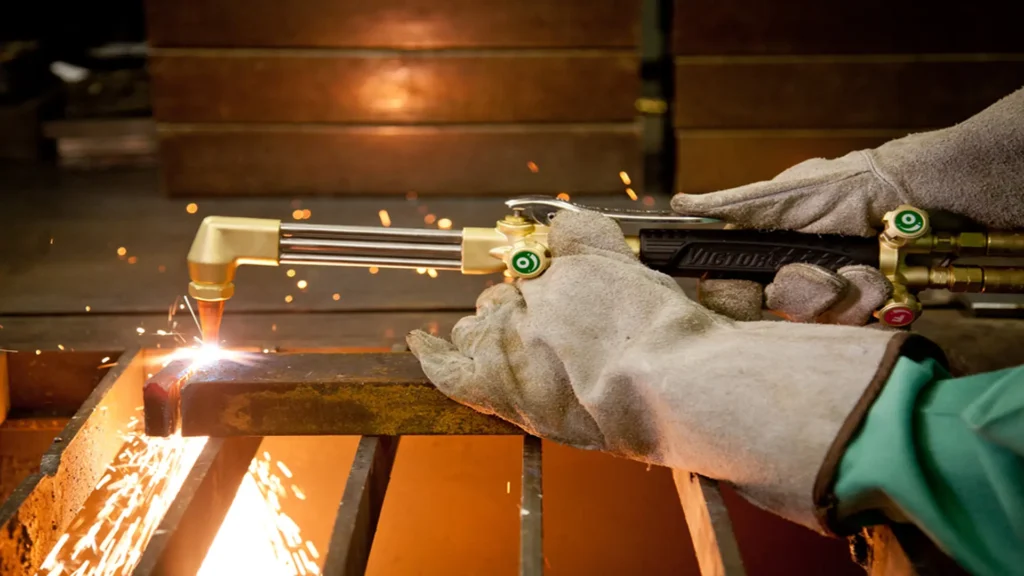
Automatic system: The world of metal fabrication has been revolutionized by the advent of automatic gas cutting machines. These sophisticated devices are designed to improve precision in the cutting of various types of metals, offering a perfect combination of technology and efficiency.
These processes include the following steps:
- Prepare equipment: Check the cleanliness of the cutting torch nozzles and adjust the torch kit regulators to ensure proper fuel gas and oxygen pressure.
- Install equipment: In the case of the automatic system, calibrate, position and align the motor and rail on the part to be cut.
- Ignition and flame adjustment: Ignite the acetylene torch and regulate the flame until a neutral proportion (balanced mixture of oxygen and acetylene) is obtained.
- Initial heating: Apply the flame to the material at the starting point until it reaches ignition temperature.
- Cutting: Activate the flow of pure oxygen and move the cutting torch along the desired line, ensuring uniform movement.
- Tip: Maintain a constant angle and proper torch speed to ensure clean, precise edges.
Oxyfuel welding process
This is a manual process that uses the heat generated by the welding torch to melt the edges of the metals and create a joint with or without filler material.
- Equipment preparation: Check the cleanliness of the cutting torch nozzles and adjust the torch kit regulators to ensure proper fuel gas and oxygen pressure.
- Preparation: Clean surfaces to be welded to remove contaminants.
- Filler material: Select the appropriate welding rod for the base material.
- Torch ignition: Adjust the flame to obtain a slightly carburizing mixture, suitable for most welds.
- Applying the filler material: Melt the rod into the weld puddle and move it evenly across the joint.
- Solidification: Allow the metal to cool slowly to avoid internal stresses.
Recommended materials for oxyfuel cutting equipment
It is ideal for materials that form low density oxides and can be easily removed as slag during cutting. Among them, the following stand out:
- Carbon steel: It is the most common material for oxyfuel cutting. It has a moderate carbon content that facilitates cutting without producing fractures or damage.
- Mild or structural steel: Used in the construction of structures, bridges and machinery. It has a good cutting capacity and is easily worked with this method.
- Low alloy steel: These are alloys with elements such as chromium, manganese, silicon or nickel, which allow oxyfuel cutting without difficulties.
- Cast iron: Although more difficult than the aforementioned steels, it can be cut by applying preheating to avoid cracks or breakage during the process.
Recommended materials for oxyfuel welding
Oxy-fuel or autogenous welding is suitable for materials that melt uniformly and have good weldability:
- Carbon steel: Excellent weldability, especially in thin to moderate thicknesses. Requires flame control to avoid oxidation or overheating.
- Copper and its alloys (brass and bronze): Requires higher temperatures and the use of specific welding rods to avoid embrittlement.
- Aluminum and its alloys (limited): Not the preferred welding method for this material due to the high thermal conductivity of aluminum, but can be feasible with proper technique and auxiliary materials.
Conclusion
Oxyfuel cutting equipment is a versatile and efficient tool for cutting and welding on various materials. The possibility of using gases such as acetylene and propane, combined with specialized tools such as the cutting torch and welding torch, establishes it as a reliable solution in the metalworking industry. To optimize its performance, it is essential to understand the properties of the materials, choose the appropriate gases and apply precise techniques.
References
- https://rskr.irimee.in/sites/default/files/gas%20cutting_0.pDF
- Travis Ham; “Oxyfuel advice from the Annual Ironworker Instructor Training Program” October 11, 2016 · in Welding Productivity.
- https://www.mathey.com/Products/pipe-flame-cutting-and-bevelling/e-z-pipecut-manual