Introduction
The quality of a weld must be of very special attention in any industrial application, since welding defects can compromise the structural integrity of a project. The identification and correction of surface defects in welds is an essential aspect to ensure the durability and strength of the joints. This article explores the main surface defects that affect weld quality, such as undercut welds, porosity, and cracks, and how weld inspection can help prevent these problems.
What are welding defects?
They are imperfections that occur during the metal joining process. These defects can range in severity from small discontinuities that do not affect the functionality of the joint, to serious defects that compromise the structural integrity of the welded component. The quality of the weld depends largely on the skill of the welder, the preparation of the material, and the welding parameters used.
Surface defects are easy to detect during a visual inspection. These include undercut welds, porosity, cracks or fissures, among others. The most common defects, their causes, and how they affect weld quality will be discussed below.
Undercut weld
This refers to a depression or channel in the base metal, right next to the weld bead. This defect occurs when the energy of the welding arc is too high, resulting in excessive melting of the base metal and a lack of fillers in the affected area.
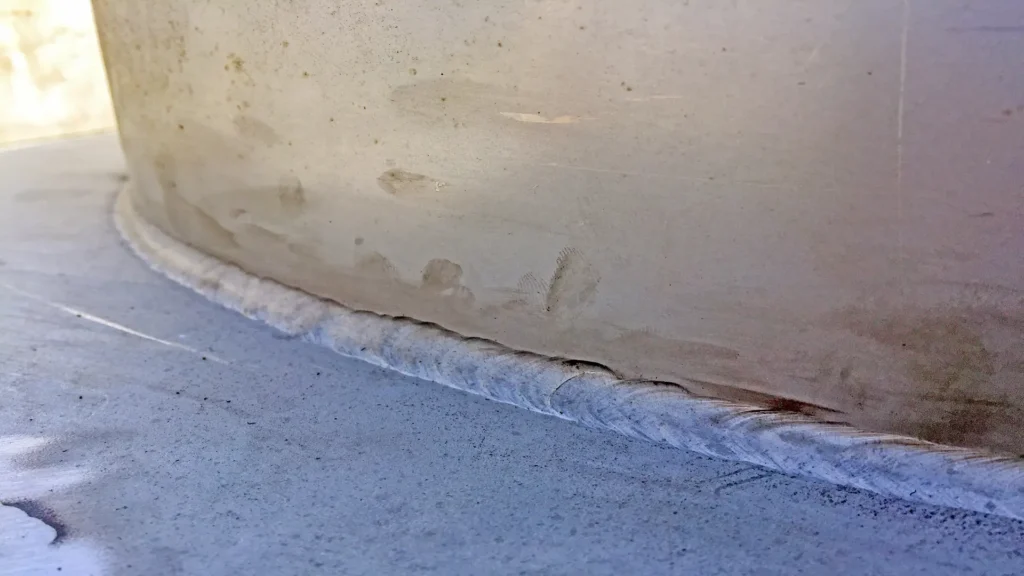
Causes of undercut welding
- Excessive heat: When the welding current is too high, it can cause excessive melting, leading to undercutting.
- Feed speed: Improper feed speed, either too fast or too slow, can cause undercutting.
- Electrode angle: Incorrect electrode angle can direct heat improperly, increasing the risk of undercut.
Effects on weld quality
Undercutting reduces the strength of the weld, creating weak spots that can cause failure under loads. This defect is particularly critical in structures subjected to cyclic stresses, such as bridges or heavy machinery, where it can lead to crack initiation.
Weld porosity
Weld porosity is one of the most common defects in welds and refers to the presence of cavities or gas bubbles trapped in or on the surface of the weld. This defect occurs when gases fail to escape from the weld pool before it solidifies.
Causes of porosity
- Contaminants: The presence of oxides, grease, moisture, or paint on the surface of the metal or electrodes can generate gases that become trapped in the weld.
- Inadequate shielding gas: Lack of adequate shielding gas or poor coverage can allow pores to form.
- Environmental conditions: Factors such as wind or high humidity can affect arc stability and shielding gas, leading to porosity.
Effects on weld quality
Porosity weakens the weld by reducing the effective cross-section of the metal. In addition, pores can act as stress concentration points, increasing the likelihood of cracking under load.
Cracks in welds
Cracks are fractures or separations in the welded material, and can be superficial or internal. This defect is one of the most dangerous as it can seriously compromise the structural integrity of the component.
Types of cracks
- Hot cracks: Occur during rapid cooling after welding, usually due to shrinkage of the molten metal.
- Cold cracks: Develop after the weld has cooled completely, often due to residual stresses or the presence of hydrogen.
- Surface cracks: These are visible on the surface and may extend into the metal.
Causes of cracks
- Material composition: Metals with high carbon content or complex alloys are more prone to cracking.
- Residual stresses: Stresses induced during solidification and cooling can lead to cracking.
- Hydrogen: The presence of hydrogen in the metal can lead to cracking, especially in steels.
Effects on weld quality
Cracks, especially internal cracks, are extremely detrimental to weld quality, as they can propagate under load, eventually leading to complete fracture of the component.
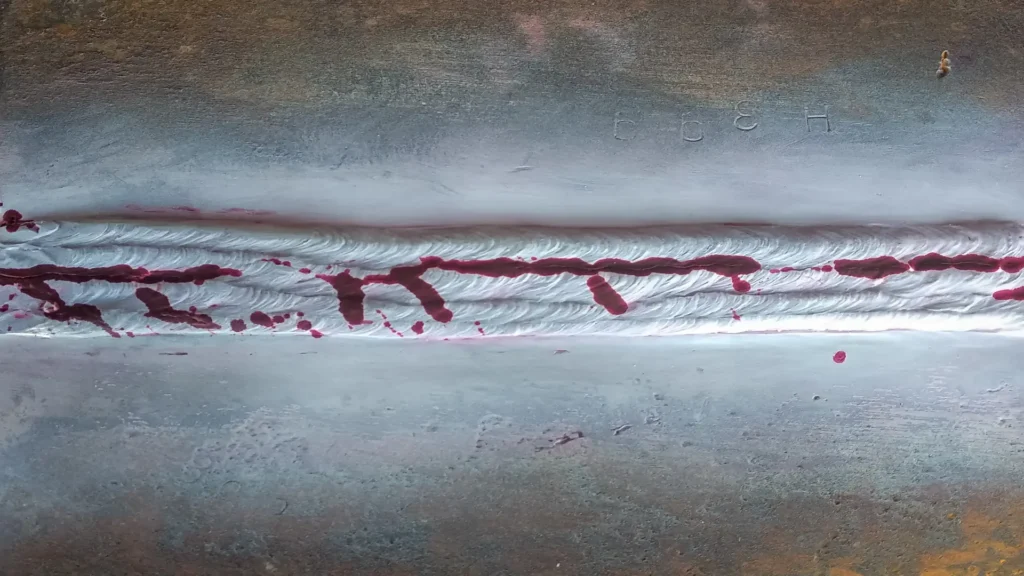
Weld Inspection
Weld inspection is a critical process to ensure that welds meet the required quality standards. There are several inspection methods, both destructive and non-destructive, that are used to detect surface and sub-surface weld defects.
Inspection methods
Visual Testing (VT)
This is the first line of defense against surface defects. A trained inspector can identify defects such as undercutting, porosity and surface cracks. Although it is the most basic and common method, with the help of advanced tools, such as high-resolution cameras and automated inspection systems, visual inspection can be carried out with much greater accuracy. Images can be magnified and analyzed with specialized software to detect small surface discontinuities that might be missed in a standard visual inspection.
Liquid Penetrant Testing (PT)
This method is highly effective for detecting surface discontinuities such as porosity, cracks or fissures. The process involves the application of a highly capillary penetrant liquid to the welded surface. After allowing the liquid to penetrate any discontinuities, the excess penetrant is removed and a developer is applied, which causes the remaining penetrant in the discontinuities to glow under visible or ultraviolet light, depending on the type of developer used.
Magnetic Particle Testing (MT)
This method is used on ferromagnetic materials. The weldment is magnetized, and then ferromagnetic particles are applied, either in dry form or suspended in a liquid. If there are surface or sub-surface discontinuities, the magnetic field is distorted, and the particles accumulate in those areas, revealing the location of the defects.
Eddy Current Testing (ET)
Eddy current testing is a non-destructive method that uses electromagnetic induction to detect surface discontinuities in conductive materials. When a coil carrying an alternating current is placed near the surface of the material, currents are induced in the material. Variations in these currents due to discontinuities affect the impedance of the coil, allowing the detection of surface and internal defects.
Surface Ultrasonic Testing (UT)
Ultrasonic technology can also be used to inspect surface discontinuities. This method involves the generation of ultrasonic waves that reflect off defects on the surface of the material. The echoes of the reflected waves are analyzed to identify and locate discontinuities. Advanced methods such as angle beam ultrasonography allow for more accurate flaw detection.
Acoustic Emission Testing (AET)
This is an advanced method that detects the energy released by the formation or growth of defects within a material during loading. It is useful for monitoring structures in real time, as it can detect crack propagation or other discontinuities. Although more common in detecting internal defects, acoustic emission can also detect certain types of surface defects.
Thermal imaging techniques (Thermographic Testing)
Thermography uses infrared cameras to detect temperature variations on the surface of the material, which can be indicative of surface defects. During the cooling or heating process, surface discontinuities such as cracks or porosity can alter heat distribution, which is reflected in the thermal image.
Laser testing methods
Laser techniques, such as 3D laser scanning and laser interferometry, are used to measure the topography of the welded surface with high accuracy. These techniques can detect small surface irregularities and discontinuities with high accuracy. Laser Shearography is another method that uses a laser to create an interference pattern on the weld surface, which is altered in the presence of discontinuities.
Automated and robotic inspection techniques
With the advancement of automation, robotic inspection systems have become an effective tool for detecting surface discontinuities in welds. These systems can integrate multiple inspection methods, such as indirect visual for accurate and repeatable inspections, even in harsh environments or on components with complex geometry.
Importance of inspection
Proper inspection ensures that defects are identified and corrected before the weld enters service. This is vital to avoid catastrophic failures, especially in critical applications such as bridge construction, aircraft, and industrial structures.
Conclusions
Identifying and correcting surface defects in welds is critical to ensure the integrity and durability of welded joints. Defects such as undercut welds, porosity, and cracks can seriously compromise weld quality, and it is critical that rigorous weld inspection procedures are implemented to detect and correct these problems before in-service failures occur.
In addition, it is essential that welders are properly trained and that the correct welding parameters are used to minimize the occurrence of defects. The quality of a weld depends not only on the equipment and materials used but also on the skill and knowledge of the welder.
References
Own source