Tabla de Contenidos
- ¿Que son los defectos de soldadura?
- Inspección de soldadura
- Métodos de inspección
- Inspección visual (Visual Testing, VT)
- Líquidos penetrantes (Liquid Penetrant Testing, PT)
- Partículas magnéticas (Magnetic Particle Testing, MT)
- Corrientes inducidas (Eddy Current Testing, ET)
- Inspección ultrasónica de superficie (Surface Ultrasonic Testing, UT)
- Prueba de emisión acústica (Acoustic Emission Testing, AET)
- Técnicas de imágenes térmicas (Thermographic Testing)
- Métodos láser (Laser Testing Methods)
- Técnicas de inspección automática y robótica
- Importancia de la inspección
- Métodos de inspección
- Conclusiones
- Referencias
La calidad de una soldadura debe ser de atención muy especial en cualquier aplicación industrial, ya que los defectos de soldadura pueden comprometer la integridad estructural de un proyecto. La identificación y corrección de defectos superficiales en las soldaduras es un aspecto esencial para asegurar la durabilidad y resistencia de las uniones. Este artículo explora los principales defectos superficiales que afectan la calidad de la soldadura, como la soldadura socavada, la porosidad, y las grietas y cómo la inspección de soldadura puede ayudar a prevenir estos problemas.
¿Que son los defectos de soldadura?
Son imperfecciones que ocurren durante el proceso de unión de metales. Estos defectos pueden variar en severidad, desde pequeñas discontinuidades que no afectan la funcionalidad de la unión, hasta defectos graves que comprometen la integridad estructural del componente soldado. La calidad de la soldadura depende en gran medida de la habilidad del soldador, la preparación del material, y los parámetros de soldadura utilizados.
Los defectos superficiales son fáciles de detectar durante una inspección visual. Estos incluyen la soldadura socavada, porosidad, grietas o fisuras, entre otros. A continuación, se analizarán los defectos más comunes, sus causas, y cómo afectan la calidad de la soldadura.
Soldadura socavada
Se refiere a una depresión o canal en la base del metal, justo al lado del cordón de soldadura. Este defecto ocurre cuando la energía del arco de soldadura es demasiado alta, lo que provoca una fusión excesiva del metal base y una falta de relleno en el área afectada.
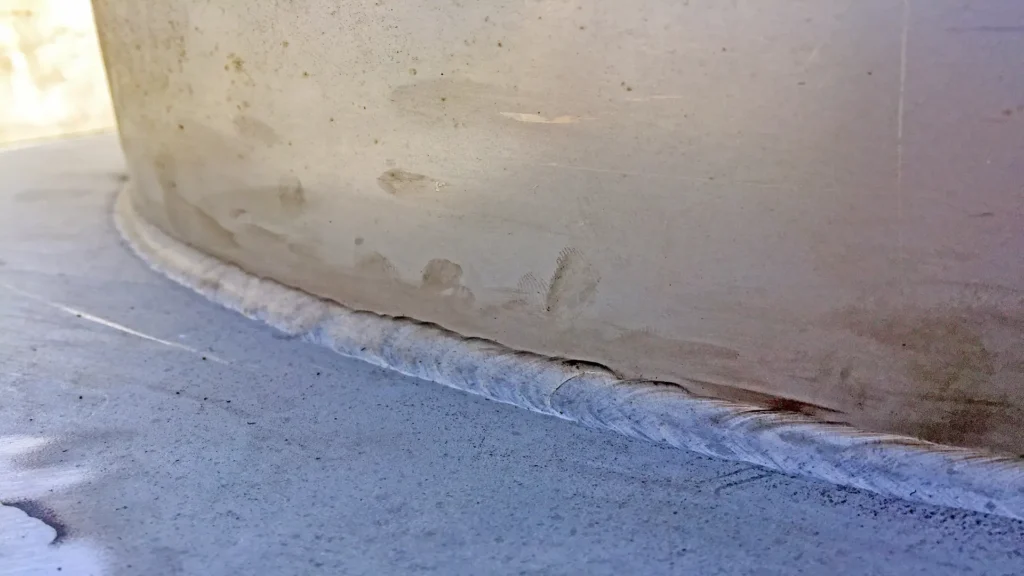
Causas de la soldadura socavada
- Exceso de calor: Cuando la corriente de soldadura es demasiado alta, puede provocar una fusión excesiva, lo que lleva al socavado.
- Velocidad de avance: Una velocidad de avance inadecuada, ya sea demasiado rápida o demasiado lenta, puede causar socavado.
- Ángulo del electrodo: Un ángulo incorrecto del electrodo puede dirigir el calor de manera inadecuada, aumentando el riesgo de socavado.
Efectos en la calidad de la soldadura
El socavado reduce la resistencia de la soldadura, creando puntos débiles que pueden provocar fallas bajo cargas. Este defecto es particularmente crítico en estructuras sometidas a tensiones cíclicas, como en puentes o maquinaria pesada, donde puede conducir a la iniciación de grietas.
Porosidad en soldadura
La porosidad en soldadura es uno de los defectos más comunes en las soldaduras y se refiere a la presencia de cavidades o burbujas de gas atrapadas dentro o sobre la superficie de la soldadura. Este defecto se produce cuando los gases no logran escapar del baño de soldadura antes de que se solidifique.
Causas de la porosidad
- Contaminantes: La presencia de óxidos, grasa, humedad o pintura en la superficie del metal o electrodos puede generar gases que quedan atrapados en la soldadura.
- Gas de protección inadecuado: La falta de un gas de protección adecuado o una mala cobertura puede permitir la formación de poros.
- Condiciones ambientales: Factores como el viento o la humedad alta pueden afectar la estabilidad del arco y la protección del gas, provocando porosidad.
Efectos en la calidad de la soldadura
La porosidad debilita la soldadura al reducir la sección transversal efectiva del metal. Además, los poros pueden actuar como puntos de concentración de tensiones, aumentando la probabilidad de agrietamiento bajo carga.
Grietas en soldadura
Las grietas son fracturas o separaciones en el material soldado, y pueden ser superficiales o internas. Este defecto es uno de los más peligrosos ya que puede comprometer seriamente la integridad estructural del componente.
Tipos de grietas
- Grietas en caliente: Ocurren durante el enfriamiento rápido después de la soldadura, generalmente debido a la contracción del metal fundido.
- Grietas en frío: Se desarrollan después de que la soldadura se ha enfriado completamente, a menudo debido a tensiones residuales o a la presencia de hidrógeno.
- Grietas superficiales: Son visibles en la superficie y pueden extenderse al interior del metal.
Causas de las grietas
- Composición del material: Metales con alto contenido de carbono o aleaciones complejas son más propensos al agrietamiento.
- Tensiones residuales: Las tensiones inducidas durante la solidificación y el enfriamiento pueden provocar la aparición de fisuras.
- Hidrógeno: La presencia de hidrógeno en el metal puede llevar a la formación de grietas, especialmente en aceros.
Efectos en la calidad de la soldadura
Las grietas, especialmente las internas, son extremadamente perjudiciales para la calidad de la soldadura, ya que pueden propagarse bajo carga, llevando eventualmente a la fractura completa del componente.
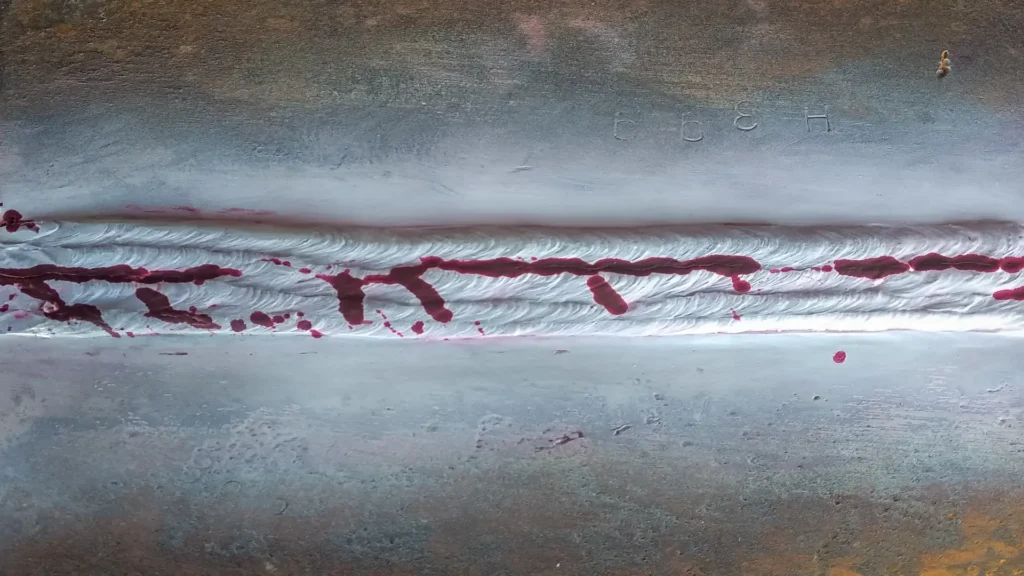
Inspección de soldadura
La inspección de soldadura es un proceso determinante para garantizar que las soldaduras cumplan con los estándares de calidad requeridos. Existen varios métodos de inspección, tanto destructivos como no destructivos, que se utilizan para detectar defectos de soldadura superficiales y subsuperficiales.
Métodos de inspección
Inspección visual (Visual Testing, VT)
Es la primera línea de defensa contra los defectos superficiales. Un inspector capacitado puede identificar defectos como socavado, porosidad y grietas superficiales. Aunque es el método más básico y común, con la ayuda de herramientas avanzadas, como cámaras de alta resolución y sistemas de inspección automatizados, la inspección visual se puede llevar a cabo con una precisión mucho mayor. Las imágenes pueden ser ampliadas y analizadas con software especializado para detectar pequeñas discontinuidades superficiales que podrían ser pasadas por alto en una inspección visual estándar.
Líquidos penetrantes (Liquid Penetrant Testing, PT)
Este método es altamente efectivo para detectar discontinuidades superficiales como, porosidad grietas o fisuras. El proceso implica la aplicación de un líquido penetrante de alta capilaridad sobre la superficie soldada. Después de permitir que el líquido penetre en cualquier discontinuidad, se retira el exceso de penetrante y se aplica un revelador, que hace que el penetrante remanente en las discontinuidades resalte bajo luz visible o ultravioleta, dependiendo del tipo de revelador utilizado.
Partículas magnéticas (Magnetic Particle Testing, MT)
Este método se utiliza en materiales ferromagnéticos. Se magnetiza la pieza soldada y luego se aplican partículas ferromagnéticas, ya sea en forma seca o suspendidas en un líquido. Si hay discontinuidades en la superficie o sub superficiales, el campo magnético se distorsiona y las partículas se acumulan en esas áreas, revelando la ubicación de los defectos.
Corrientes inducidas (Eddy Current Testing, ET)
El ensayo por corrientes inducidas es un método no destructivo que utiliza la inducción electromagnética para detectar discontinuidades en la superficie de materiales conductores. Cuando una bobina que transporta una corriente alterna se coloca cerca de la superficie del material, se inducen corrientes en el material. Las variaciones en estas corrientes debido a discontinuidades afectan la impedancia de la bobina, permitiendo la detección de defectos superficiales e internos.
Inspección ultrasónica de superficie (Surface Ultrasonic Testing, UT)
La tecnología ultrasónica también se puede utilizar para inspeccionar discontinuidades superficiales. Este método implica la generación de ondas ultrasónicas que se reflejan en defectos en la superficie del material. Los ecos de las ondas reflejadas se analizan para identificar y localizar discontinuidades. Métodos avanzados como la ultrasonografía de haz angular permiten la detección de defectos con mayor precisión.
Prueba de emisión acústica (Acoustic Emission Testing, AET)
Este es un método avanzado que detecta la energía liberada por la formación o crecimiento de defectos dentro de un material durante la carga. Es útil para monitorear estructuras en tiempo real, ya que puede detectar la propagación de grietas u otras discontinuidades. Aunque es más común en la detección de defectos internos, la emisión acústica también puede detectar ciertos tipos de defectos superficiales.
Técnicas de imágenes térmicas (Thermographic Testing)
La termografía utiliza cámaras infrarrojas para detectar variaciones de temperatura en la superficie del material, que pueden ser indicativas de defectos superficiales. Durante el proceso de enfriamiento o calentamiento, las discontinuidades superficiales como grietas o porosidad pueden alterar la distribución del calor, lo que se refleja en la imagen térmica.
Métodos láser (Laser Testing Methods)
Las técnicas láser, como el escaneo láser 3D y la interferometría láser, se utilizan para medir con alta precisión la topografía de la superficie soldada. Estas técnicas pueden detectar pequeñas irregularidades y discontinuidades superficiales con gran exactitud. El Laser Shearography es otro método que utiliza un láser para crear un patrón de interferencia en la superficie de la soldadura, que se altera en presencia de discontinuidades.
Técnicas de inspección automática y robótica
Con el avance de la automatización, los sistemas de inspección robótica se han convertido en una herramienta eficaz para la detección de discontinuidades superficiales en soldaduras. Estos sistemas pueden integrar múltiples métodos de inspección, como la visual indirecta para realizar inspecciones precisas y repetibles, incluso en entornos difíciles o en componentes de geometría compleja.
Importancia de la inspección
Una inspección adecuada asegura que los defectos sean identificados y corregidos antes de que la soldadura entre en servicio. Esto es vital para evitar fallos catastróficos, especialmente en aplicaciones críticas como la construcción de puentes, aviones, y estructuras industriales.
Conclusiones
La identificación y corrección de defectos superficiales en las soldaduras es fundamental para garantizar la integridad y durabilidad de las uniones soldadas. Defectos como la soldadura socavada, la porosidad, y las grietas pueden comprometer seriamente la calidad de la soldadura, y es determinante que se implementen procedimientos de inspección de soldadura rigurosos para detectar y corregir estos problemas antes de que ocurran fallos en servicio.
Además, es esencial que los soldadores estén adecuadamente capacitados y que se utilicen los parámetros de soldadura correctos para minimizar la aparición de defectos. La calidad de una soldadura no solo depende del equipo y los materiales utilizados, sino también de la habilidad y conocimiento del soldador.
Referencias
Fuente propia