Table of Contents
Introduction
Liquid penetrant testing (PT) is one of the most widely used techniques in the field of non-destructive testing (NDT). This method allows the detection of surface discontinuities in materials such as metals, ceramics, and plastics. The purpose of this article is to highlight the importance of liquid penetrant testing in non-destructive testing (NDT), explaining its operation, types, regulations, and most common applications to ensure the quality and safety of the materials inspected.
How does liquid penetrant testing work?
The fundamental principle of this non-destructive testing methodology lies in capillarity, i.e. the ability of a liquid to infiltrate into surface cavities of the material, such as cracks, pores or fissures. This action occurs when the adhesion forces between the liquid and the internal walls of the defect exceed its surface tension, allowing the liquid to penetrate even very narrow discontinuities.
These fluids are specifically formulated to maximize this infiltration through characteristics such as low viscosity, high adhesion and adequate surface tension. This allows effective liquid penetrant inspection of welds, metal, plastic or ceramic components, ensuring accurate detection of surface defects.
Types of penetrant liquids
There are three main types of liquid penetrant. The choice of penetrant type depends on the material to be inspected, the environmental conditions and the level of sensitivity required.
- Visible penetrants (dyes): Contain pigments (usually red) and require white light for inspection. A white developer is applied which creates high contrast.
- Fluorescent penetrants: Use dyes visible under ultraviolet (UV-A) light. They are highly sensitive and effective in low light environments.
- Dual Penetrants: Combine visible and fluorescent pigments, allowing evaluation under white or UV light as needed.
Penetrant removal methods
Removal of excess penetrant from the surface must be performed to avoid false positives.
There are four main methods:
- Method A – Water washable: Excess is removed directly with water. It is quick and common in general applications.
- Method B – Lipophilic Post-emulsifiable: Requires an oily emulsifier prior to rinsing. High sensitivity, suitable for critical applications.
- Method C – Solvent washable: Excess is removed with a special solvent. Ideal for areas where water is not available.
- Method D – Hydrophilic Post-emulsifiable: Uses a water-based emulsifier. Provides high accuracy in defect detection.
Sensitivity levels
Sensitivity defines the minimum detectable discontinuity size. The levels are classified by international standards:
- ½: Ultra low sensitivity
- 1: Low sensitivity
- 2: Medium sensitivity
- 3: High sensitivity
- 4: Ultra high sensitivity
The choice of the appropriate level depends on the type of material, the industrial process and the required quality standards. Higher sensitivities increase the detection of small defects, but may also increase false indications due to contaminants or surface roughness.
Standard inspection procedure
The liquid penetrant inspection process includes the following steps:
- Surface preparation: Cleaning of the area to be inspected to remove grease, rust, paint, or contaminants.
- Penetrant application: The liquid is applied to the surface and left to act.
- Dwell Time: A specific time is waited to allow the liquid to infiltrate into the discontinuities.
- Removal of excess penetrant: It is carefully cleaned without removing the liquid inside the defects. Removal methods A, B, C or D are used.
- Developer application: Facilitates the migration of the penetrant to the surface, making the defects visible.
- Visual inspection: Evaluation of the indications with white light or UV light depending on the type of penetrant.
- Final cleaning: Removal of penetrant and developer residues to prepare the part for further use.
Types of liquid penetrant inspection
Manual Inspection: Performed by an inspector, who applies the products and visually evaluates the results, it is common in specific or small scale jobs.
The following video shows the steps to follow in the process of manual inspection with penetrant liquids, washable with solvent. Source: EISHIN Kagaku Official.
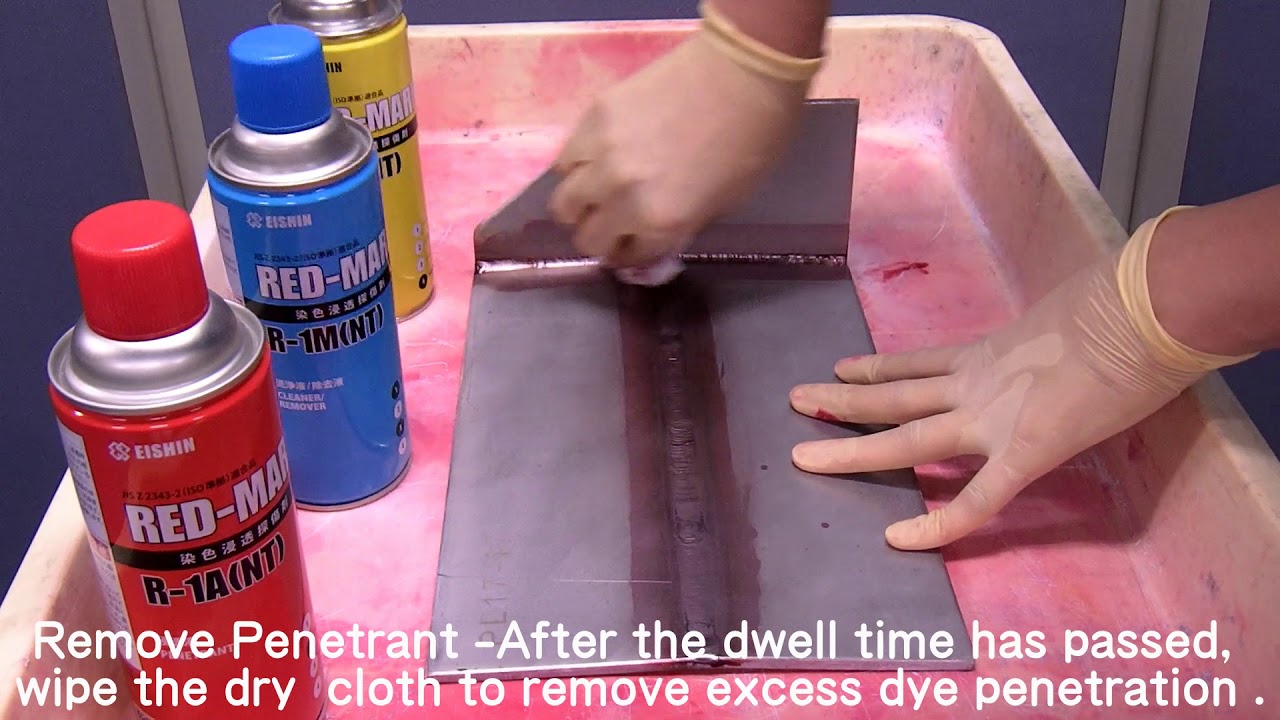
How to do visible dye penetrant testing.
Automated Inspection: Uses robotic or mechanized systems with sensors, cameras, and analysis software. This mode is ideal for mass production and components with complex geometries. It offers advantages such as:
- Uniform liquid distribution
- Better control of penetration time
- Efficient removal of excess liquid
- Reduced human error.
The following video demonstrates automated application with penetrating dyes. Source: NDTChannel.
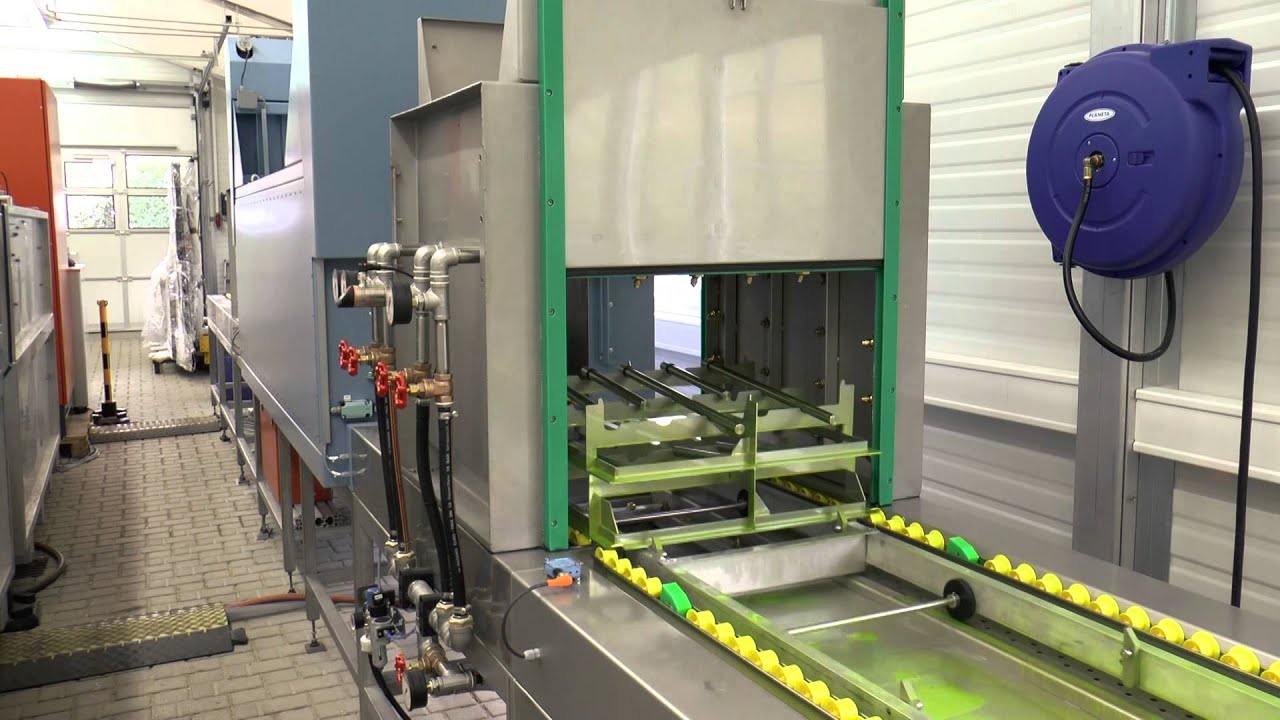
Automated liquid penetrant inspection.
Benefits of liquid penetrant testing
This methodology offers a number of advantages including:
- Early detection of defects: They identify discontinuities that could compromise the structural integrity of critical components.
- Cost-effectiveness: They are economical techniques, with accessible equipment and relatively simple procedures.
- Versatility of application: Suitable for various materials (metals, plastics, ceramics).
- Complementary to other NDT techniques: Can be combined with ultrasound, radiography, or magnetic particles for more complete analysis.
- Regulatory compliance: Required in various industries such as aerospace, automotive, energy and petrochemical.
Detectable defects
This method detects discontinuities open to the surface, including:
- Cracks: Due to thermal stresses, fatigue, corrosion or mechanical stresses.
- Porosities: Caused by gas inclusions during welding or casting.
- Welding failures: As lack of surface fusion or non-metallic inclusions.
- Surface laminations: In hot worked materials.
- Cracks: Caused by stress corrosion or localized deformation.
Types of defects by nature
These defects detectable with Penetrant Liquids (PT) are mainly classified into two categories:
- Linear defects: They include cracks, fissures, bites, and lack of fusion. They are considered more critical, since their geometry favors stress concentration, increasing the risk of failure.
- Rounded defects: Such as porosity, cavities, and blowholes. They have less structural severity, but their acceptance will depend on the size, quantity, and location.
Defects by their nature can originate during manufacturing processes (cracks due to solidification, shrinkage, rolling or machining) and service (fatigue cracks, stress corrosion cracking, thermal cracks).
Types of defects according to material
Each material tends to present characteristic surface defects. The most common ones that can be detected with Penetrating Liquids (PT) are summarized below:
MATERIAL | TYPICAL DETECTABLE DEFECTS |
---|---|
Carbon / Alloy steel | Cooling cracks, bites, inclusions, lack of fusion |
Stainless steel | Thermal cracks, surface porosity, heat-affected zone (HAZ) cracks |
Aluminum and alloys | Hot cracks, porosity, laps |
Nickel alloys (Inconel) | Intergranular cracks, thermal fatigue cracks, open porosity |
Copper and alloys | Quenching cracks, solidification cracks |
Titanium | Overheating cracks, surface contamination |
Advantages
- High sensitivity to detect surface discontinuities.
- Easily implemented, low-cost non-destructive testing technique.
- Compatible with a wide variety of metallic and non-metallic materials, including ferrous/non-ferrous, conductive/non-conductive and magnetic/non-magnetic.
- Can be used to inspect large areas quickly.
- Findings can be seen visually on the surface of the materials and can show the dimensions of the defect.
Limitations
- Only detects surface discontinuities (or “open” to the surface)
- Porous or rough materials cannot be inspected with penetrant dyes.
- Requires thorough cleaning before and after testing
- Direct access to the material is required.
- Limited for high temperatures
- There are several steps in the inspection process, each of which could affect the quality of the findings.
- Chemicals are involved, so inspectors must follow established safety protocols for handling and disposal.
Technical standards
Tests with penetrant liquids are regulated by several international standards that guarantee their correct application and evaluation:
- ASTM E165: Procedure for PT on metallic materials.
- ISO 3452: General requirements for liquid penetrant testing.
- ASME Section V: Guidelines for inspection of welds and critical components.
- EN 571-1: European standard for non-metallic materials.
Acceptance criteria
The acceptance or rejection of defects is established according to applicable codes and standards such as ASME Section V, AWS D1.1 or ISO 23277 which may vary according to the sector (petrochemical, nuclear, food, mining, etc.) and the level of operational severity. In general terms:
- Linear defects are rejected because of their structural criticality.
- Rounded defects may be acceptable if they comply with the established limits in terms of quantity, size, and location.
Technical personnel certification
In liquid penetrant testing (PT) there are several certifications that accredit the competence of professionals in this technique, the most recognized being those granted by ASNT (The American Society for Nondestructive Testing) and ISO (International Organization for Standardization). These certifications are granted to the technicians who perform the tests, after meeting specific training, experience and examination requirements. The accredited levels are as follows:
ASNT (SNT-TC-1A or CP-189
- Level I: Technician trained to perform tests under the supervision of a Level II or III certified professional.
- Level II: Professional with advanced skills to perform and interpret results, in addition to supervising Level I technicians.
- Level III: Technical expert with the ability to develop procedures, train personnel and lead NDT programs.
ISO 9712 (International Organization for Standardization)
- Certification: Level I, II and III, with characteristics very similar to those of ASNT.
Recent advances in liquid penetrant testing
Recent advances in liquid penetrant testing (PT) have significantly improved both the sensitivity and efficiency of the process. Innovations such as new formulations of more environmentally friendly biodegradable developer penetrants have also improved visibility and reduced drying times, increased resistance to high temperatures, addressing the limitations of traditional methods that were prone to inconsistencies and subjectivity. In addition, the integration of automated systems has revolutionized the testing process.
Conclusion
In a context where safety, reliability, and regulatory compliance are industrial priorities, liquid penetrant testing is a fundamental technique within non-destructive inspection procedures. Its efficient implementation in evaluation processes allows ensuring the structural integrity of metallic and non-metallic components without compromising their functionality and service life.
References
- ASTM International. (2021). ASTM E1417/E1417M-21: Standard practice for liquid penetrant testing. ASTM International.
- International Organization for Standardization. (2021). Non-destructive testing — Penetrant testing — Part 1: General principles (ISO 3452-1:2021). ISO.
- American Society of Mechanical Engineers (ASME). (2023). ASME Boiler and Pressure Vessel Code, Section V – Nondestructive Examination. New York, NY: ASME.
- American Society for Nondestructive Testing. (1999). Nondestructive Testing Handbook: Liquid Penetrant Testing (Vol. 2, 3rd ed.). Columbus, OH: ASNT.