Non-Destructive Testing (NDT) is a discipline that greatly contributes to the integrity of materials and is a crucial factor in asset management across various industrial sectors, such as construction, oil and gas, power generation, aerospace, and manufacturing. NDT allows for the inspection, monitoring, and evaluation of materials, components, or assemblies without causing damage, ensuring that they continue to function as expected. Among the frequently tested materials, carbon steel and stainless steel stand out due to their widespread use and the benefits each offers.
Alloys with a high nickel content and copper-based alloys share similarities with austenitic stainless steel, such as a near-polished surface appearance, good resistance to various corrosion scenarios, and good electrical conductivity. Therefore, when highlighting the characteristics of austenitic stainless steel in this article, these considerations also apply to high-nickel and copper alloys.
This article provides a comparative analysis of non-destructive testing on carbon steel vs stainless steel, focusing on the techniques, challenges, and best practices associated with each.
Differences between carbon and stainless steel
Before delving into the details of NDT for carbon steel vs stainless steel, it is crucial to understand the fundamental differences between carbon steel and stainless steel.
Carbon steel: Carbon steel is known for its strength, hardness and affordability which results from a combination of two main elements, iron and carbon. Other elements are present in quantities too small to affect their properties and necessary for their production, such as silicon and manganese1. Carbon steel is susceptible to corrosion in certain scenarios, which can compromise its integrity over time in aggressive environments.
Stainless steel: In contrast, stainless steel contains a significant amount of chromium, which forms a passive layer of chromium oxide on the surface, preventing corrosion. This makes stainless steel ideal for applications that require both mechanical strength and resistance to oxidation and corrosion in various aggressive environments. However, its cost is higher, and handling these materials in the construction of piping systems, equipment, and structures requires greater considerations to ensure their integrity.
Non-Destructive Testing methods and techniques
Several NDT methods and techniques are commonly used to evaluate the integrity of both carbon steel and stainless steel. The choice of technique for carbon steel vs stainless steel often depends on the specific properties of the material and the nature of the defects being inspected. The different stages of material processing and service conditions must be considered to accurately define the type of failure to be detected and, consequently, the appropriate NDT method and technique for detection.
Visual Inspection (VT)
- Carbon steel: Visual inspection is straightforward due to the material’s surface characteristics. Common issues such as corrosion, cracks, and surface irregularities can be easily detected.
- Stainless steel: Although visual inspection is also effective for this type of material, the reflective surface of stainless steel can sometimes hinder defect detection. Proper lighting and surface preparation may be necessary for component inspection.
Ultrasonic Testing (UT)
- Carbon steel: UT is highly effective for detecting internal defects such as inclusions, voids, and cracks. It is also very effective for corrosion assessment through thickness measurement using the pulse-echo technique or more advanced techniques like corrosion mapping with Phased Array Ultrasonic Testing (PAUT). The acoustic properties of carbon steel allow for clear transmission of ultrasonic waves.
- Stainless steel: The coarse grain structure typical of stainless steel can cause greater attenuation of ultrasonic waves, requiring more sophisticated equipment and techniques to obtain precise results. The inspection of austenitic stainless steel welds is a complex challenge that requires special techniques and procedures.
Magnetic Particle Testing (MT)
- Carbon steel: Being ferromagnetic, carbon steel is suitable for MT. This technique can effectively detect surface and near-surface discontinuities.
- Stainless steel: Most industrial-grade stainless steels are austenitic and non-magnetic, making MT ineffective. However, for magnetic grades of stainless steel (martensitic and ferritic), MT can still be applicable.
Radiographic Testing (RT)
- Carbon steel: RT is effective for identifying internal defects such as voids, inclusions, and cracks. The contrast in radiographic images is generally clear due to the material’s density.
- Stainless steel: RT can be used effectively to evaluate various components made from this material. However, it should be noted that this type of material is commonly used in critical applications, leading to stricter application requirements, such as higher resolution recording media (e.g., slower films) and longer exposure times, which can increase safety concerns and inspection costs.
Eddy Current Testing (ECT)
- Carbon steel: ECT is challenging to apply to this material and low-alloy steels due to their low conductivity. However, a variant of this technique known as Pulsed Eddy Current (PEC) or its upgraded version Pulsed Eddy Current Array (PECA) is effective for detecting corrosion under thermal insulation and fireproofing (CUI and CUF).
- Stainless steel: The higher electrical conductivity of austenitic stainless steel compared to carbon steel allows ECT to be applied in the inspection of materials made from this and other high-conductivity materials (high-nickel and copper alloys). Martensitic and ferritic stainless steels have low conductivity, making them difficult to inspect with ECT.
Liquid Penetrant Testing (PT)
- Carbon steel: PT is effective for detecting surface-breaking defects such as cracks, provided the material is non-porous to avoid high retention and difficulty in removing the penetrant. The process is straightforward and cost-effective.
- Stainless steel: PT is equally effective for stainless steel, without being affected by electromagnetic properties, surface condition, grain structure, etc. However, it is important to ensure that the halide content (chlorides and fluorides) is very low when applied to austenitic stainless steels. This requirement also applies to Titanium. Additionally, for high-nickel alloys, the sulfur content in the penetrant liquids must be very low.
Infrared Thermographic Testing (IRT)
- Carbon steel: The oxidation state of the surface affects the emissivity of the material being evaluated, requiring certain procedures to correct this parameter when evaluating skin temperatures in this material and in low-alloy steels.
- Stainless steel: The typical reflectivity of stainless steel surfaces affects the readings obtained from thermographic evaluations, necessitating adjustments to correct the obtained results.
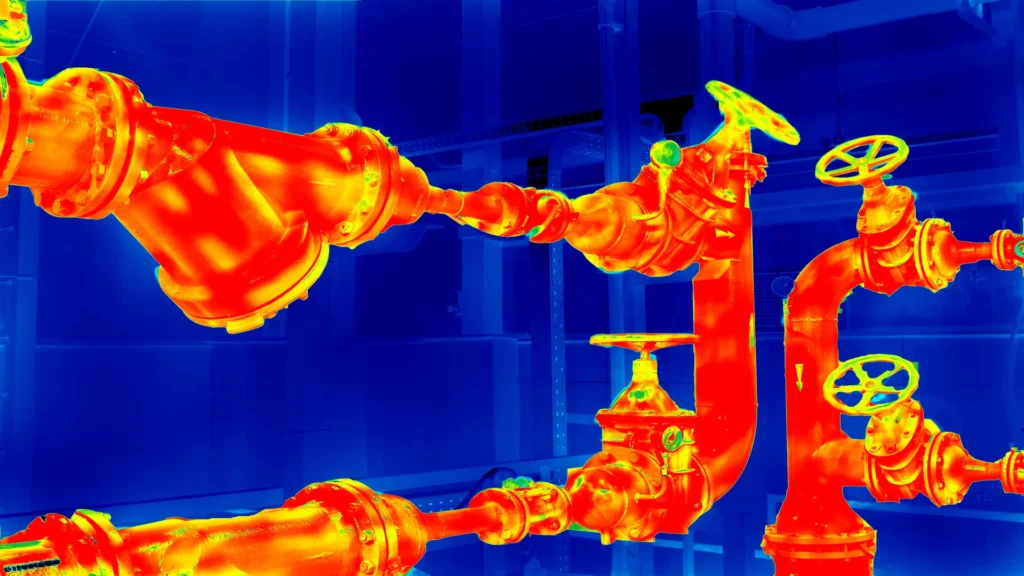
Magnetic Flux Leakage Testing (MFL)
- Carbon steel: Being ferromagnetic, carbon steel and low-alloy steels, like MT, are also suitable for MFL. This technique can effectively detect surface and near-surface discontinuities.
- Stainless steel: Most industrial-grade stainless steels are austenitic and non-magnetic, making MFL ineffective, just like MT. However, for magnetic grades of stainless steel (martensitic and ferritic), MFL can still be applicable.
Carbon steel vs. stainless steel: Challenges for NDT
The unique properties of carbon steel and stainless steel present different challenges in NDT.
Carbon steel
- Corrosion: Carbon steel’s susceptibility to corrosion can sometimes complicate NDT. Corroded areas can affect the application of some testing methods, such as UT, by hindering transducer scanning. In other cases, removing scales and coarse corrosion products from pipes or containment equipment in high-risk services can pose a significant risk, so alternatives for non-destructive evaluation of these areas must be carefully considered. PEC is an alternative for this scenario.
- Magnetic properties: Although beneficial for MT and MFL, the ferromagnetic nature of carbon steel makes it unsuitable for ECT. However, a variant known as Pulsed Eddy Current (PEC) is effective for detecting corrosion under thermal insulation and fireproofing (CUI and CUF). Other tests are not affected.
- Surface condition: In thermographic evaluations, parameters such as emissivity and reflected temperature are key to obtaining reliable results. For example, an oxidized surface tends to increase emissivity, requiring adjustment of this parameter during inspection.

Pulsed Eddy Current Array Solution.
Stainless steel
- Attenuation and reflection: The coarse grain size of stainless steel can lead to greater attenuation of ultrasonic waves, making UT more challenging. For decades, evaluating austenitic stainless steel welds has been a challenge for ultrasonic testing due to difficulties such as beam redirection (shear waves) and limitations in inspecting the first leg with longitudinal waves, as a large percentage of the beam changes to shear waves upon hitting the inner wall (mode change), which attenuate easily within the joint’s tank structure.
- Non-magnetic nature (austenitic stainless steels): For most grades of stainless steel, the lack of magnetic properties limits the use of MT and MFL, requiring alternative methods such as PT, ECT, and RT.
- Surface condition: The reflective and often polished surface of stainless steel must be considered when performing visual inspections, as excessive lighting and thus increased reflection can affect the clarity of the evaluation. Thermographic inspections are also affected by this condition, as reflective surfaces are poor emitters2.
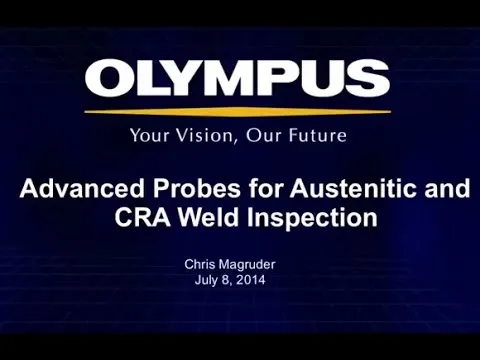
Advanced Probes for Austenitic and CRA Weld Inspection Webinar.
Best Practices for NDT in carbon steel and stainless steel
To achieve reliable and accurate results for carbon steel vs stainless steel, specific practices must be followed when conducting NDT on each of these materials.
For carbon steel
- Surface preparation: Ensure surfaces are clean and free of corrosion and scales to improve the accuracy of visual inspections, penetrant testing, magnetic particle testing, and transducer movement and coupling for ultrasonic inspections.
- Frequency adjustment for Ultrasonic Testing: Depending on the grain structure and thickness of the component, use the appropriate frequency for the transducer to minimize attenuation effects.
- Frequency adjustment for Eddy Current Testing: Based on the material’s conductivity, use the ideal frequency to assess the full thickness or the required depth of the component.
- Equipment calibration: Have available the necessary calibration patterns and procedures, duly approved for various NDT equipment calibrations. For MT and MFL inspections, obtain the required magnetic field strength to ensure inspection of different areas of the component.
- Parameter adjustments for Thermographic Evaluations: Adjust parameters affected by the metal surface’s oxidation condition to obtain reliable results.
For stainless steel
- Lighting adjustment: Adjust the lighting to avoid excessive reflections that may interfere with surface evaluations through methods like VT, PT, MT, and LT.
- Advanced UT techniques: Use phased array ultrasonic testing (PAUT) and linear transducers in dual or matrix arrays, and other advanced techniques to overcome challenges posed by attenuation, anisotropy, beam redirection, and mode change in austenitic weld evaluation. 2D matrix technology provides the ability to optimize focus and beam direction3. Lower frequency transducers are required for these applications.
- Low-energy RT: For radiographic testing in highly critical components, consider using lower energy sources and recording media that offer higher resolution to achieve better sensitivity.
- Frequency adjustment in ECT: Adjust frequency and use advanced signal processing methods in ECT to obtain precise results.
- Parameter adjustments for Thermographic Evaluations: Adjust parameters affected by the high reflectivity of the metal surface to obtain reliable results.
Conclusion
In the realm of non-destructive testing, understanding the differences between carbon steel vs. stainless steel is crucial for selecting the appropriate methods and techniques and overcoming inherent challenges. While both materials are essential to various industries, their distinct properties require customized NDT approaches to ensure accurate and reliable evaluations. By following best practices and leveraging advanced technologies, professionals can effectively assess the integrity of these materials, safeguarding the safety and longevity of critical structures and components.
References
- WIKIPEDIA. Carbon Steel; Accessed on July 16, 2024. https://simple.wikipedia.org/wiki/Carbon_steel
- FLUKE. Understanding and Troubleshooting Thermography on Reflective Surfaces; Accessed on July 16, 2024. https://www.fluke.com/en-us/learn/blog/thermal-imaging/fixing-thermography-reflectivity
- ZETEC. NDT for Austenitic Stainless Steel: The Shift to Phased Array Ultrasonic; Accessed on July 17, 2024. https://www.zetec.com/blog/ndt-for-austenitic-stainless-steel-the-shift-to-phased-array-ultrasonic/