Detailed and optimal inspection of steel chimneys in the oil industry is essential to ensure efficient, safe operation and compliance with environmental and safety regulations. In this article we will explore the keys to carrying out a comprehensive inspection, addressing topics such as the evaluation of structural conditions, periodic review, safety regulations and other critical aspects that ensure the performance and integrity of these structures.
Concept, installation and innovation of industrial chimneys
Chimneys are tall structures usually made of steel or concrete. They are used in industrial facilities to discharge combustion gases from processes, which may contain N₂, CO₂, SO₂, NO, 0₂, H₂O. These gases must be discharged at a height where there is sufficient exit velocity, so that they and the ashes are dispersed in the atmosphere within the limits allowed by the pollution regulatory authorities, hence the importance of the location for installation of these structures.
For the installation of an industrial chimney it is necessary to know the following aspects: Location, fixings or supports, design and knowledge of regulatory standards for these projects at a national and international level.
The implementation of innovative technology in self-supporting industrial chimneys offers advanced solutions for smoke evacuation. These systems stand out for their versatility by presenting completely independent structures, where the loads are supported by external tubes made of high quality materials, such as carbon steel. Furthermore, the provision of insulation between internal and external components contributes to improving the operability and performance of these systems.
An example of these systems is the simple and intelligent solution of the self-supporting industrial chimney model FSA from Jeremias España SAU , which stands out for its innovative technology. The loads are supported by the outer tube (Windshield) made of carbon steel. They are characterized by their high quality finishes, providing essential construction details for a quick and safe installation.
The following video shows the step by step for the correct installation of the chimney using the lifting means necessary for a quick and safe installation.
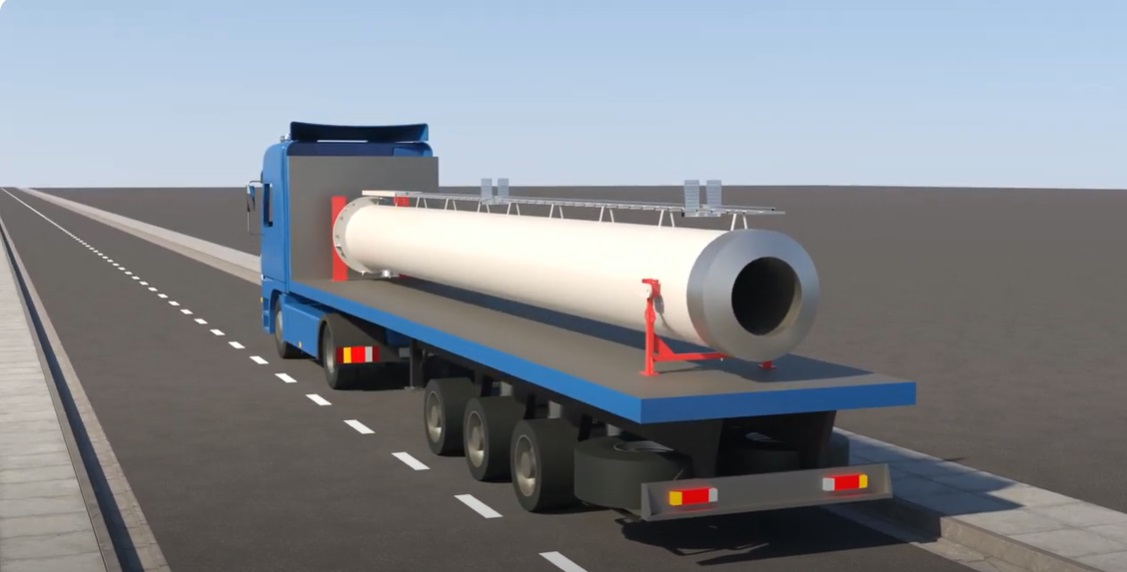
Installation of a self-supporting industrial chimney. Video courtesy of Jeremias España S.A.U.
Displacement of gases to the top of the chimney
There are three forms of movement:
- Natural draft: In this type, no equipment or fan is required to move the gases to the top of the chimney. It works by taking advantage of the push effect suffered by the hot gases at the top surrounded by colder ones from the environment. This draft depends a lot on the height of the chimney.
- Forced draft: In this case, the gases are sucked in by a fan located in the gas duct between the oven and the chimney, which drives the gases towards the chimney. No more chimney height is required than that imposed by environmental pollution regulations.
- Induced draft: It is very similar to forced draft, but the fan is placed at a point outside the gas duct to inject air taken from the environment into a nozzle placed in the chimney, which is driven according to the Venturi effect principle.
Types and characteristics of steel chimneys
Steel chimneys are classified into two main types: as can be seen in figure 1:
- Self-supporting steel chimneys: These chimneys are self-contained and do not depend on external support structures (Figure 2A). They are frequently used in industrial environments to vent gases or emissions produced by various processes. They are built of steel and are designed to resist both wind and seismic forces and are usually tall structures, designed to guarantee structural stability 1 .
- Braced Steel Chimneys: These chimneys are supported by a network of cables, as shown in Figure 1B. These cables anchor the chimney to the ground, providing it with stability. Wind chimneys are typically used when the height of the chimney exceeds the practical limit of the free-standing design. They are often found in applications such as telecommunications and certain industrial chimneys 1 .
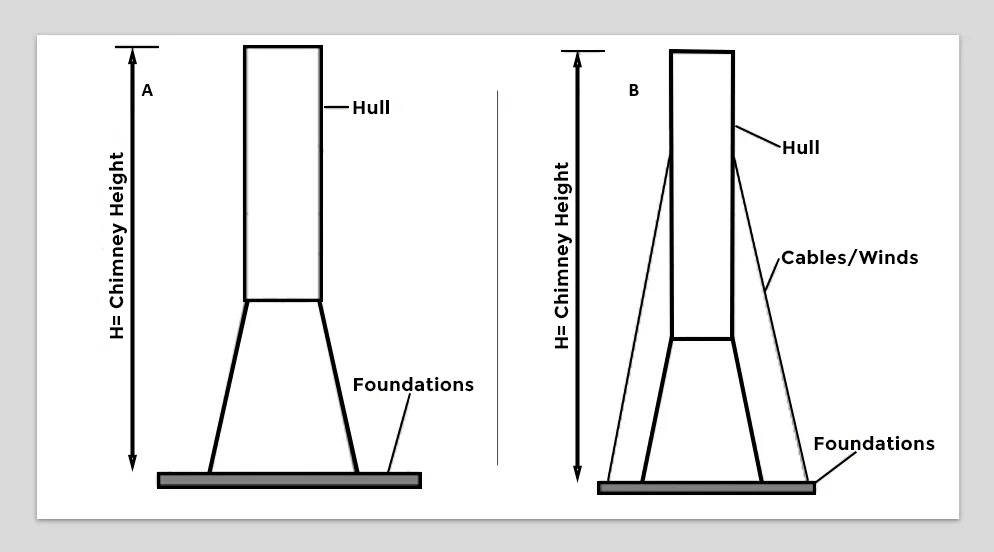
Parts of a fireplace
The types and quantity of parts or components of a steel chimney for the oil industry depend on the purpose for which they were designed. Each part of an industrial chimney has a specific function, which is described below:
- Foundation: It is the part of the structure that extends below or the chimney floor and is responsible for transmitting and distributing the loads to the ground in a safe and stable manner. The foundations provide the support necessary to support the weight of the structure and resist external forces, such as wind speed, earthquakes or live loads. Likewise, the studs used to attach and adjust the hull are embedded in the foundation. In the case of some chimneys that are placed on the oven, the function of the foundation is fulfilled by the structures of those ovens.
- Hull: It is the main part of the chimney. It is the highest section, positioned vertically. Its function is to carry and discharge combustion gases upwards. It has a cylindrical or trick cone shape made of carbon steel sheets or tubes. It also provides the height necessary for effective dispersion of pollutants in the atmosphere.
- Hull flange: Serves as a connection between the hull and the foundations. This flange is welded to the lower part of the body, where it is coupled and adjusted with nuts to the studs that are embedded in the foundation, as indicated in figure 2.
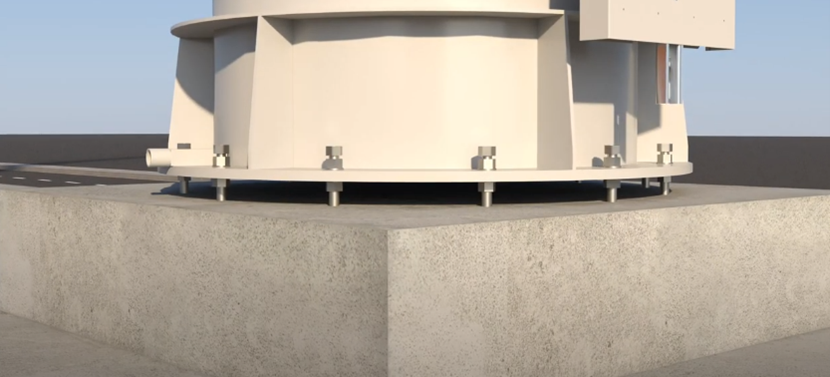
- Gas duct flange: Serves as a connection between the hull and the gas ducts coming from the oven. This flanged joint must use gas corrosive-resistant gaskets.
- Inner liner: Protects the internal walls of the hull against high combustion gas temperatures, erosion and corrosion. Normally, it is a silicoaluminous refractory that is applied anchored to the internal part of the hull. In the case of very acidic gases, borosilicates are recommended. For gases produced by the combustion of natural gas , special steels can be used that resist the aggressiveness of the combustion gases well, considerably reducing the cost of construction.
- Stairs and platforms: Provides ease of safe access to the top of the chimney for inspection, maintenance and repairs. Figure 3 shows these very useful components for carrying out these works.
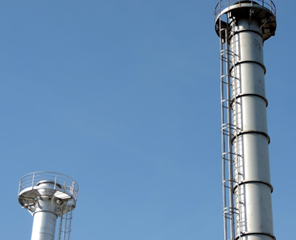
- Tension cables: Tension cables are installed in chimneys to share seismic and wind loads. The number and location of guy wires depend on stack height, structural design, geographic location, wind forces, and seismic estimates. Depending on these factors, chimneys may be provided with one or more sets of cables placed at different heights.
- Lightning rod: This system is installed to protect chimneys and nearby facilities against atmospheric electrical discharges.
- Marking lights: They provide air safety in the area to aviation as they help aircraft identify and avoid obstacles during flight, especially at night or in low visibility conditions.
- Gas analyzers: They are placed at different heights of the chimney to take gas samples for analysis.
- Operational variables monitoring system: They are installed to monitor and control parameters such as temperature, pressure and gas emissions to guarantee safe operation and comply with environmental regulations.
- Lighting System: Provides lighting to facilitate night-time inspection, operations and maintenance activities.
Optimal inspection of furnace chimneys in the oil industry
In order to maintain the operational reliability of industrial steel chimneys, it is essential to carry out periodic inspections by qualified chimney inspectors, who must have the physical conditions required for work at height. Knowledge about the operation and design of industrial chimneys will help identify signs of problems such as: wind load, lightning and constant contact with the internal and external aggressive atmosphere, in order to avoid damage to structural components and to the refractory.
Classification of steel chimney inspections
The types of inspection can be various, depending on the time in service of the chimney, the regulations of the facilities, explosions, the history of the chimney and natural events, among others. Below are four of the most relevant inspection types based specifically on the author’s experience.
Type I inspection.
This type of non-specialized direct visual inspection will be performed by plant operators to detect macro deviations. This inspection is high frequency as part of the daily tours of plant operators.
Type II inspection.
It is a direct or indirect visual inspection with a frequency of no more than one year that is carried out with the chimney in service as follows:
- Inspection from the ground, observing the accessible parts. The flange on the hull floor should be inspected for possible corrosion on the studs, nuts, etc.
- Inspection from the external high parts with the help of binoculars. Evaluation of the visible parts of the hull from the ladder.
- Evaluation of the visible parts of the hull from the ladder.
- Visual inspection of the entire external part using drones equipped with cameras.
- Perform evaluations with infrared thermography to detect hot spots due to possible refractory detachments or failures.
- Perform ultrasound inspection to measure thickness of the hull walls, using remote robotic equipment that scales the hull walls.
Type III inspection.
This is done with the chimney out of service, the frequency depends on the furnace’s major maintenance plan. Here the same evaluations of the type II inspection are carried out and the condition of the refractory is evaluated. Generally, during major maintenance, scaffolding was installed along the entire internal length of the chimney, but with current technology the inspection can be carried out with drones and depending on the result, scaffolding would be installed for internal repairs and temperature control.
Type IV inspection
This is the most in-depth level of inspection, performed in unique circumstances that require a comprehensive structural and stability examination. In cases in which the chimney was exposed to damage due to severe weather conditions, explosions, overheating, earthquakes, settlement, or other severe exposure, a type IV inspection is required immediately, just as if structural modification such as increasing the height, place additional parts such as platforms. Additionally, this type of inspection should be performed before making any significant structural modifications, such as increasing the height or adding more platforms or bedrooms. The application of the Fitness for Service methodology is very useful for these cases.
- Operational safety: Chimneys play a fundamental role in the management of gases and emissions produced during industrial processes. A detailed inspection ensures that these structures are in optimal condition to avoid potential risks and operational failures.
- Regulatory compliance: Environmental and safety legislation imposes strict requirements for the control of polluting emissions. The inspection ensures compliance with these regulations, avoiding sanctions and contributing to environmental sustainability.
- Energy efficiency: Fireplaces in good condition contribute to efficient combustion and energy conservation. The inspection allows you to identify and correct possible heat losses and optimize the energy performance of the ovens.
Conclusion
Optimal chimney inspection in the oil industry is a necessary practice to ensure safe, efficient and sustainable operations. The combination of structural assessments, periodic reviews and regulatory compliance contributes to a responsible and resilient industrial environment. Finally, detailed smokestack inspection is not only a preventative measure, but also an investment in the safety, efficiency and long-term sustainability of the oil industry.
References
- www.jetir.org (ISSN-2349-5162).