Introduction
Today we are witnessing a world characterized by fierce competition, where efficiency and productivity are key factors for success, which is why organizations are constantly seeking methodologies that allow them to improve their processes sustainably. Kaizen, a Japanese approach based on continuous improvement, has established itself as one of the most effective strategies to optimize operations, reduce waste and foster innovation at all levels of a company.
This article discusses how Kaizen strategies can be applied to optimize processes and increase productivity in various industries. Throughout the content, we will discuss the fundamental principles of Kaizen, its benefits, the key tools for its implementation and its impact on quality management.
If you are looking for an effective way to boost operational efficiency, reduce costs and foster a culture of continuous improvement in your company, read on to discover how Kaizen can transform your organization.
What is Kaizen and how does it drive continuous improvement?
The term Kaizen comes from Japanese and is composed of two words: Kai (change) and Zen (better), which together mean “change for the better” or continuous improvement. This concept became popular in the business world thanks to the Japanese manufacturing industry, especially with the Toyota Production System, where it became a fundamental pillar for process optimization and operational efficiency.
Unlike other management approaches that seek large-scale improvements at specific times, Kaizen is based on the implementation of small daily improvements that, accumulated over time, generate significant results. This involves the active participation of all levels of the organization, from top management to plant operators, fostering an organizational culture where innovation and efficiency become daily habits.
The key principles of kaizen
To understand how Kaizen drives continuous improvement, it is essential to know its core principles:
- Focus on processes, not on results: This strategy prioritizes process optimization, understanding that good results are a natural consequence of well-managed processes.
- Elimination of waste: One of the main objectives of Kaizen is to reduce waste in all its forms, be it time, materials, energy or human talent.
- Involvement of all employees: Continuous improvement is not the exclusive responsibility of leaders; every employee must be part of the process, contributing ideas and implementing changes in their work area.
- Data-driven decision-making: Kaizen encourages the use of performance indicators, metrics, and analysis tools to identify areas for improvement and evaluate the impact of changes.
- Flexible and constantly evolving standards: Instead of considering standards as immovable, Kaizen promotes their constant review and adjustment to adapt to the needs of the environment.
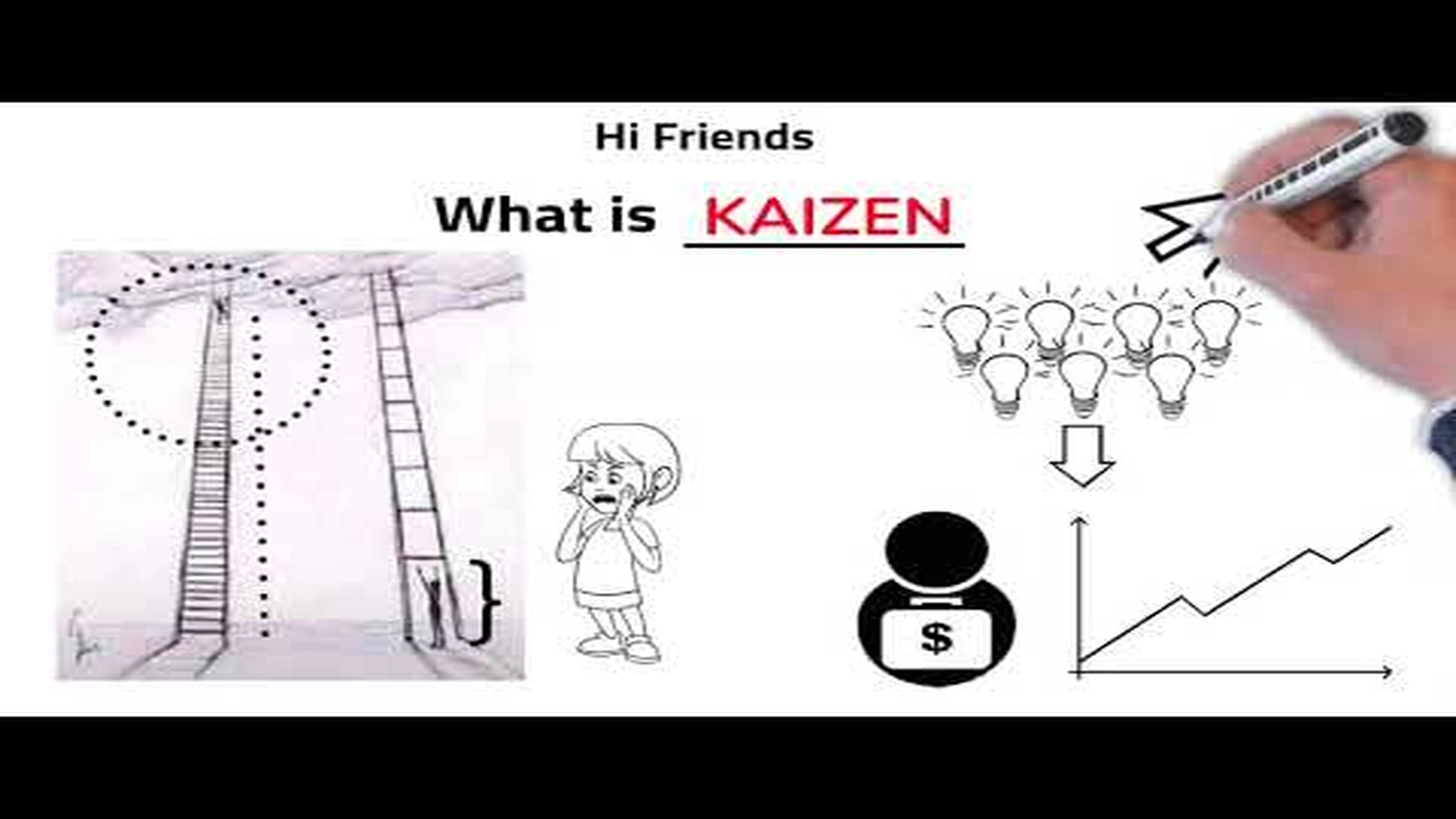
What is Kaizen?
Benefits of applying Kaizen in organizations
The implementation of Kaizen in an organization generates a significant impact on the operational efficiency, the quality of products or services and the commitment of the work team. In this sense, the kaizen philosophy is an excellent strategy to integrate into formal quality management programs, such as the ISO 9001 quality management systems.
Unlike improvement approaches based on radical changes, Kaizen promotes a progressive and sustainable transformation, ensuring lasting results.
The following are the main benefits of applying Kaizen in organizations:
- Increased operational efficiency: Kaizen optimizes production and administrative processes, eliminating unnecessary activities and reducing waste (Muda). By identifying and correcting inefficiencies, a more agile production is achieved with less consumption of resources.
- Cost and waste reduction: One of the pillars of Kaizen is the elimination of waste (Muda), which has a direct impact on the reduction of operating costs. These wastes can be of materials, time, human effort or overproduction.
- Improved product and service quality: Kaizen drives the early identification and correction of process problems, which translates into continuous improvement in the quality of the final product or service. It fosters a culture of error prevention instead of defect correction.
- Increased team engagement and participation: Kaizen involves all employees in process improvement, which fosters a sense of ownership and responsibility for their work. When workers see that their ideas are valued and implemented, their motivation and commitment to the organization increases.
- Adaptability and rapid response to change: In a dynamic business environment, adaptability is key. Kaizen enables organizations to be more agile and flexible, continuously adjusting processes to respond to market challenges.
- Strengthening the organizational culture: Companies that implement Kaizen develop a culture of continuous improvement, where innovation and the search for efficiency become part of the corporate DNA. This not only impacts productivity, but also talent satisfaction and retention.
Kaizen strategies to optimize processes and increase productivity
Implementing Kaizen in an organization involves applying effective strategies to optimize processes, reduce waste and improve productivity on a continuous basis. Below, we explore the main Kaizen strategies that can make a difference in a company’s performance and operational efficiency.
Eliminating waste with the 5S methodology
The 5S methodology is one of the fundamental tools of Kaizen and focuses on organizing the work environment to improve efficiency and reduce waste. The 5S include:
- Seiri (Classification): Eliminate unnecessary items from the work area.
- Seiton (Order): Organizing materials and tools for ease of use.
- Seiso (Cleanliness): Maintain a clean space to prevent failures and improve safety.
- Seiketsu (Standardization): Create standards to maintain order and cleanliness.
- Shitsuke (Discipline): Encourage discipline to sustain improvement over time.
Implementation of the PDCA Cycle for continuous improvement
The PDCA (Plan-Do-Check-Act) cycle is a key tool in Kaizen that allows structuring improvements in a cyclical and sustainable way. Its application is based on:
- Plan: Identify the problem and develop a plan of action.
- Do: Implement the solution on a small scale.
- Check: Evaluate results and compare with objectives.
- Act: Standardize the improvement if it was successful, or adjust the plan if necessary.
Use of quality circles for problem resolution
Quality circles are groups of employees who work in the same area and meet regularly to analyze problems and propose improvements. The advantages of this strategy include:
- Encourages teamwork and employee participation.
- Helps identify difficulties from the perspective of those involved in the process.
- Allows to implement solutions with greater acceptance.
Waste reduction with Lean Manufacturing
Kaizen is complemented by the principles of Lean Manufacturing, which seek to reduce waste in production processes. The 7 wastes identified by Lean are:
- Overproduction: Manufacturing more than necessary.
- Waiting time: Processes stopped due to lack of materials or information.
- Unnecessary transportation: Unnecessary movement of products or materials.
- Excess inventory: Accumulation of raw materials or finished products.
- Unnecessary movements: Displacements of operators that do not add value.
- Defects: Products that do not meet quality standards.
- Overprocessing: Performing more steps in a process than necessary.
Standardization of processes to sustain improvement
For the changes introduced with Kaizen to be sustainable, it is necessary to document and standardize processes. Key activities to standardize processes include:
- Identify best practices in each area.
- Create clear and easy-to-follow procedures.
- Train employees on new methodologies.
- Continuously monitor and update standards.
Conclusions
The implementation of Kaizen as a continuous improvement strategy has proven to be a fundamental tool for optimizing processes, increasing productivity and fostering an organizational culture based on efficiency and innovation.
One of the most outstanding aspects of Kaizen is its focus on the participation of all levels of the company, from top management to operators, promoting a collaborative work environment where each employee contributes ideas and solutions to improve processes. This principle has a positive impact on team morale, strengthens the sense of belonging and promotes operational excellence.
Kaizen is not an isolated initiative, but a work philosophy that, when adopted systematically and sustainably, enables organizations to achieve higher levels of efficiency, quality, and innovation. Companies that integrate Kaizen into their organizational DNA will be better prepared to face the challenges of the future and ensure their long-term competitiveness.
References
- Deming, W. E. (1986). Out of the crisis. MIT Press.
- Imai, M. (1986). Kaizen: The key to Japan’s competitive success. McGraw-Hill.
- Ohno, T. (1988). Toyota Production System: Beyond large-scale production. CRC Press.
- Juran, J. M., & Godfrey, A. B. (1998). Juran’s quality handbook (5ª ed.). McGraw-Hill.
- Ramos, J. (2023 ). El método Kaizen. XnnXi
- Shingo, S. (1989). A study of the Toyota production system: From an industrial engineering viewpoint. Productivity Press.
- Womack, J. P., & Jones, D. T. (1996). Lean thinking: Banish waste and create wealth in your corporation. Free Press.