Deterioration of valve internals can cause critical failures, affecting the safety, operational efficiency and profitability of alkylation plants, which are of great importance in the oil industry. High-octane gasoline components are produced in these units by chemical synthesis of the olefin-isobutane alkylation reaction using hydrofluoric acid (HF) or hydrogen fluoride as a catalyst.
This process involves technical and safety challenges for handling, maintenance and equipment integrity, especially for process valves.
This article addresses the mechanisms of internal deterioration of process valves, focusing on hydrofluoric acid (HF) as a catalyst for the reaction, and in turn proposes strategies to mitigate these risks.
What is an alkylation plant?
Alkylation plants are where conversion processes are carried out in the petroleum industry to convert isobutane and alkenes (mainly propylene and butylene) into alkylate, which is a component of high-octane gasoline, where hydrofluoric acid (HF) acts as a catalyst. This acid is a very dangerous chemical compound that can cause burns and is highly corrosive, being more aggressive if operated outside the recommended limits, such as when the percentage of humidity is equal to or greater than 2.0 %.
These plants are delimited in two general zones which are: The non-acidic zone and the acidic zone, the latter being the focus of this article.
Main causes of deterioration in valve internals due to HF
The causes of corrosion in alkylation plants are mainly due to deviations in operating parameters and key control points in the plant feed, among the most critical causes are the following:
- The concentration of HF acid: Carbon steels are severely affected by corrosion when the concentration of hydrofluoric acid is low and the corrosion rate is much lower at high concentrations or with pure HF.
- Water content: The presence of water in the environment increases corrosion, therefore, humidity should be kept within the allowed parameter (less than 2 %) using conductivity meters or a moisture analyzer for continuous water monitoring.
- Oxygen: This element can enter the system through breaks in the piping, failures in the joints of the valves, during the loading of raw material into the plant or by loading the acid incorrectly. This compound can be controlled by using nitrogen to drain the acid from the HF storage tanks, by controlling oxygen in the plant feed, and by rigorously inspecting the condition of piping, equipment and valves.
Mechanisms of valve deterioration in HF service
The internal damage to the valves is caused by the fluid that flows inside and has repercussions on all the elements that are in contact. In this case, in particular, it is due to corrosion by hydrofluoric acid (HF), which is used as a catalyst in alkylation plant processes.
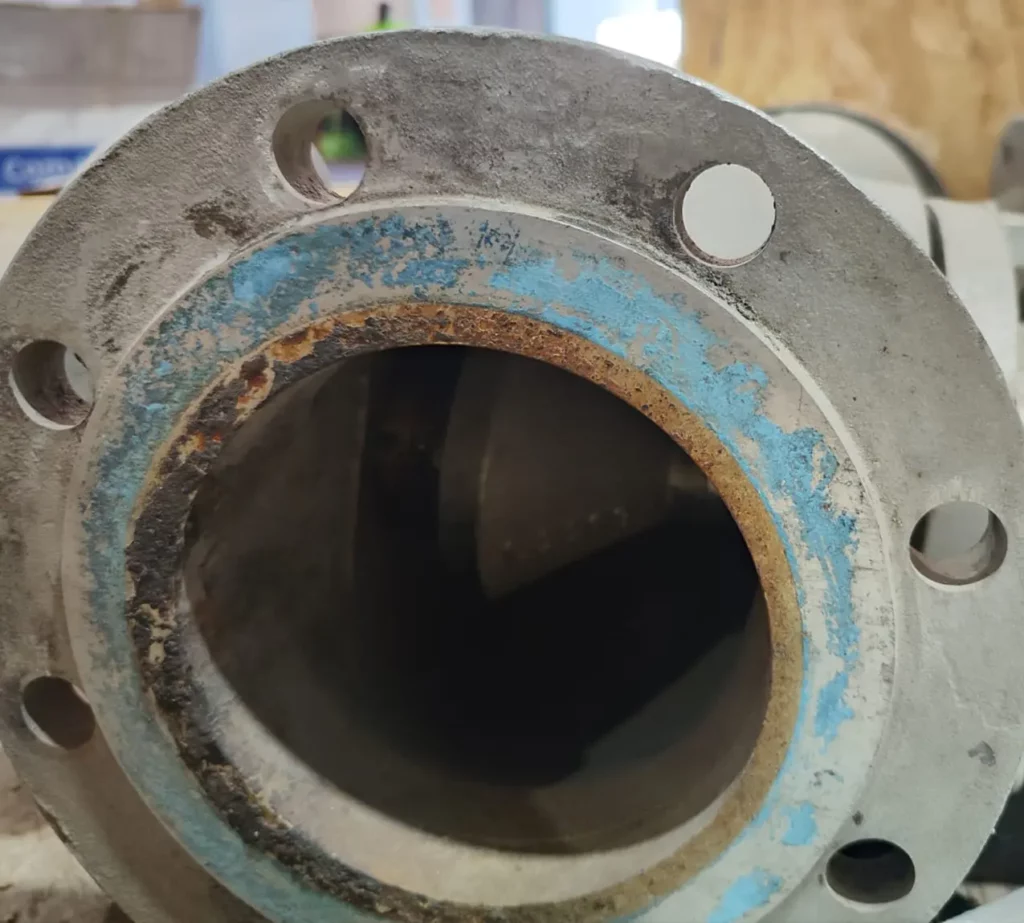
HF service in alkylation plants is particularly aggressive to process valves due to the corrosive and erosive nature of hydrofluoric acid. The main mechanisms of deterioration include:
- Chemical corrosion: HF is highly corrosive, especially in the presence of moisture, which can lead to loss of material in the valve internals, affecting its functionality and useful life. In this case, product leakage from the valve joints would combine with ambient humidity to generate a highly corrosive product that would rapidly deteriorate the carbon steel valves.
- Leaks: The presence of highly corrosive fluids and high pressures can cause deterioration of valve seals, resulting in leaks. These not only represent a safety risk, but can also cause corrosion damage to materials.
- Erosion: Particles entrained in the fluids can cause physical wear on internal valve components, exacerbated by the high flow velocities common in these processes.
- Stress corrosion cracking (SCC): The combination of mechanical stress and exposure to HF can cause cracks in the valve materials, mainly in the studs or bolts, where product leakage through the flanges generates stress corrosion caused by acid attack.
Inspection and maintenance of valves in HF service
Regular inspection and preventive maintenance are crucial to mitigate valve deterioration. Recommended practices include:
- Regular inspections: Using non-destructive testing techniques to detect corrosion, erosion, and cracking at early stages.
- Preventive maintenance: Replacement or repair of worn parts before they fail, based on the findings of inspections at manufacturers’ recommended intervals.
Mitigation action against damage and failures
Preventive action should be taken to avoid valve damage or failure with the following actions:
- Proper material selection: Choose corrosion resistant materials for all parts of the valve according to the HF concentration and the presence of contaminants. Materials such as high-alloy stainless steel and mainly nickel-based alloys offer better resistance in these environments and are suitable for manufacturing valve internals.
- Alkylation system design: Optimize the process design to minimize areas where acid or sediment accumulation generally occurs, causing corrosion problems. This includes the design of flow systems that prevent stagnation and promote efficient cleaning and drainage.
- Acid quality control: Keep a close watch on the quality of the acids used in the process to ensure that impurities that can accelerate corrosion are kept to a minimum.
- Preventive maintenance: Implement a preventive maintenance program that includes regular inspections, cleaning and replacement of worn or corroded parts. Early detection of problems allows interventions to be made before they become significant failures.
- Corrosion monitoring: Use corrosion monitoring techniques, such as corrosion coupons and ultrasound, to assess the corrosion rate in different parts of the system and take corrective action when necessary.
- Process control: Adjust operating conditions, such as temperature, pressure, and reagent concentration, to operate within ranges that minimize corrosion.
- Training and awareness: Train personnel in proper operating and maintenance practices to handle corrosive substances and operate the plant safely and efficiently.
- Vapor capture systems: Install adequate systems or filters to control moisture, handle and treat acid vapors and other corrosive by-products, minimizing exposure to equipment and personnel.
Sound risk management practices
Risk management plays a key role in the safe operation of alkylation plants. Good practices include:
- Risk assessment: Identification and analysis of risks associated with valve deterioration, considering the probability and consequences of failures.
- Material handling: All valves, as well as any material that is removed or moved inside or outside an alkylation plant, must be subjected to a neutralization process to avoid HF burn accidents.
- Emergency response plans: Establishment of procedures to respond to valve failures, minimizing the impact on plant safety and operation.
Conclusion
The deterioration of valve internals in alkylation plants using HF represents a significant challenge to the safe and efficient operation of these facilities. An understanding of deterioration mechanisms, coupled with a robust inspection and maintenance program and proper risk management practices, are essential to prevent failures and extend the life of process valves. Adopting these approaches not only improves safety and operational efficiency, but also ensures the long-term integrity of the assets in alkylation plants.
References
Own source