In welding processes, the internal integrity of the joint is as critical as its external appearance. Internal welding defects can go unnoticed to the naked eye, compromising the mechanical strength, durability, and safety of the component. The correct identification and evaluation of these defects using weld inspection techniques is essential to ensure reliable and safe quality. This article analyzes the most common internal weld defects, their causes, and consequences, answering questions in the industrial field.
What are Internal welding defects?
They are irregularities or discontinuities that are generated within the weld bead or in the area adjacent to the base metal during the fusion process. Unlike surface defects, these are not visible without special weld inspection techniques, such as ultrasound, radiography, or advanced methods such as automated ultrasonic testing (AUT).
These defects compromise the structural strength, tightness, and performance of the welded component, especially under conditions of pressure, temperature, or vibration, and are critical in industries such as petrochemical, energy, metalworking, and shipbuilding.
Common types of internal defects in welding
The quality of a weld is not only evaluated by its surface appearance, but also by the integrity of its internal structure. Internal defects in welds can arise from improper welding techniques, poorly adjusted parameters, or contaminated materials.
Below are the main types of internal defects in welds that can compromise their quality:
Lack of fusion
This occurs when an adequate bond is not achieved between the base metal and the filler metal, or between successive passes. This creates weak areas with a high risk of crack propagation in the weld.
Common causes:
- Inadequate welding parameters (low energy).
- Poor operator technique.
- Excessive feed speed.
- Low current intensity.
- Surface contamination.
- Inadequate electrode diameter, mainly in the root pass.
- Incorrect electrode angle.
Consequences:
- Significant reduction in mechanical strength.
- Possible initiation of cracks under load.
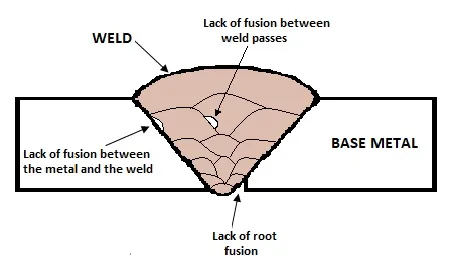
Lack of penetration
is a condition where the weld bead does not reach the root of the joint, creating an internal discontinuity and generating a weak area that compromises structural integrity.
Common causes:
- Low voltage or excessive feed speed.
- Inadequate bevel preparation.
- Poor alignment of parts.
Consequences:
- Failure due to fatigue or cyclic stresses.
- Compromised tightness of the component.
Internal porosity
Porosity refers to cavities generated by gases trapped during the solidification of molten metal.
Common causes:
- Contamination by moisture, oxides, or oils.
- Improper use of shielding gas.
- Unconfined atmospheric air.
- Welding technique that generates excessive smoke or gas.
Consequences:
- Weakening of the weld bead.
- Reduction in tensile strength.
Slag inclusions
These occur when slag remains trapped between passes or at the root of the weld.
Common causes:
- Inadequate cleaning between passes.
- Incorrect use of the electrode.
Consequences:
- Crack initiation points.
- Difficulty in future inspections.
Internal cracks or fissures
Weld cracks are separations in the material caused by residual stresses, sudden thermal changes, contraction during cooling, or inadequate compositions.
Common causes:
- Rapid cooling.
- High levels of diffusible hydrogen.
- Unreleased internal stresses.
Consequences:
- Immediate or progressive failure of the component.
- Repair impossible without removing the defect.
Internal root undercut
This is a longitudinal depression in the root area, creating a stress concentration point.
Common causes:
- Excessive current.
- Incorrect electrode angle.
Consequences:
- Loss of effective section.
- Onset of fatigue cracks.
Comparative table of internal defects
Internal Defect | Main Cause | Main Technical Consequence |
---|---|---|
Lack of fusion | Low welding energy | Reduced strength and cracking |
Lack of penetration | Incorrect parameters or poor beveling | Fatigue failures and loss of tightness |
Porosity | Contaminants in the metal or shielding gas | Weakening of the weld bead |
Slag inclusions | Poor cleaning between passes | Crack propagation |
Internal cracks | Rapid cooling or internal stresses | Catastrophic failure |
Root undercut | Poor electrode technique | Stress concentration |
Heat-Affected Zone (HAZ) and its impact
The heat-affected zone (HAZ) is the region adjacent to the weld that has undergone microstructural changes due to exposure to heat during the welding process. This zone can develop brittle structures, prone to weld cracking, and affect in-service performance, negatively impacting the mechanical properties of the material, such as its hardness and ductility.
The width of the HAZ depends on several factors, such as the thermal diffusion of each material, the amount of heat input, the time of exposure to heat, the cooling rate, the welding technique (TIG, MIG, or SMAW), and the thickness of the material.
Common problems in the heat-affected zone:
- Embrittlement due to phase transformation.
- Reduction in toughness.
- Invisible internal microcracks.
To minimize the negative effects of the heat-affected zone (HAZ), the temperature must be controlled during welding, materials compatible with the process must be used, and techniques that reduce the amount of heat input must be applied. In addition, the use of post-weld heat treatment (PWHT), when necessary, helps to normalize the original properties of the material in the HAZ, mainly in high-carbon and low-alloy steels.
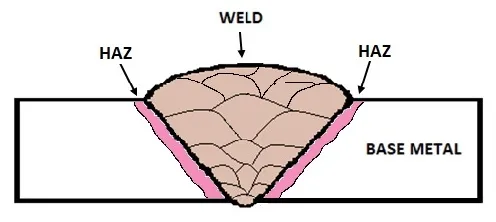
Weld quality control
To guarantee the quality and safety of welds, and given that these internal defects are not visible to the naked eye, advanced weld inspection methods using non-destructive testing (NDT) are required. These methods are the most suitable way to detect internal weld defects without compromising the integrity of the part. The most commonly used methods include:
- Conventional and automated ultrasound (AUT): Enables accurate in-depth detection.
- Industrial radiography: Excellent for visualizing porosity, inclusions, and lack of penetration.
- TOFD (Time of Flight Diffraction): High sensitivity to internal cracks.
These techniques help to accurately identify lack of fusion, lack of penetration, weld cracks, and internal porosity.
Techniques for preventing internal defects in welding
Prevention requires the application of correct welding techniques, including:
- Proper selection of parameters (voltage, amperage, speed).
- Meticulous preparation and cleaning of surfaces.
- Control of preheating and cooling temperatures.
- Use of certified consumables in good condition.
- Strict compliance with the parameters established in the welding procedure (WPS).
- Application of welding inspection during and after the process.
Conclusion
Identifying and controlling internal weld defects is essential to prolonging the service life of structures. Applying appropriate techniques, performing weld inspection, and correcting root causes prevents lack of fusion, lack of penetration, porosity, or cracks in welds, reducing risks and ensuring durable joints.
References
- https://compraco.com.br/es/blogs/industria/compreendendo-a-fusao-de-solda-e-as-zonas-afetadas-pelo-calor?srsltid=AfmBOorDgNIkmhKSjr5FJpr25tBLOjEUNuuZXWWiEuHcRuQ048uYZyA3
- http://scielo.sld.cu/scielo.php?script=sci_arttext&pid=S2223-48612019000300011
Frequently Asked Questions (FAQs)
What are internal welding defects?
They are discontinuities that occur within the welded material and affect the joint without being visible to the naked eye. They can compromise the mechanical strength and functionality of the component.
What is the most dangerous internal welding defect?
The most dangerous internal defect in a weld is an internal crack or fissure, due to its high potential for propagation under load conditions or thermal variations. Unlike other internal defects, such as porosity or lack of fusion, a crack acts as a stress concentration point that can cause sudden and catastrophic failure of the component. These cracks can be caused by residual stresses, rapid cooling, the presence of diffusible hydrogen, or metallurgical incompatibilities. Accurate detection requires advanced NDT inspection techniques, such as phased array ultrasonic testing (PAUT) or digital radiography.
How are internal defects detected?
Through NDT techniques such as ultrasound, industrial radiography, TOFD, and automated methods (AUT).
How do these defects affect weld quality?
They reduce structural strength and can cause cracks, premature failure, or loss of tightness. They also make future inspection difficult.
What standards regulate the inspection of internal defects?
API 1104, ASME Section V and IX, AWS D1.1, ISO 17635, among others.