In the oil industry, process furnaces are relevant for the transformation of fossil resources into refined products. These thermal equipments are extremely important, because when their service fails, the plant processes are stopped, which indicates that an efficient and safe operation must be carried out, for which an integral and regular evaluation is required. The purpose of this article is to explain in detail the importance of the evaluation of furnaces in the oil industry, the techniques used and how to improve the efficiency of this equipment.
What is a process furnace?
It is a piece of equipment used in the industry to apply heat to fossil resources or intermediate products in order to carry out specific chemical reactions. These furnaces are designed to reach and maintain elevated temperatures in a controlled manner, which facilitates evaporation, thermal decomposition and other transformations necessary in processes such as petroleum refining.
Configuration and parts of a process furnace
Process furnaces in the oil industry are designed to optimize heat transfer to the fluids being processed. They consist of several essential parts: combustion chambers, where fuels are burned to generate heat; convection chambers, which initiate the heating of the tubes by the combustion gases; and heat exchange tubes, through which the fluid to be heated circulates. In addition, they include burners, control systems to regulate temperature and air flow, and thermal insulation to help prevent heat loss.
Configuration and parts of a process furnace
Figure 1 shows a schematic of the furnace and its main components.
- Burners: Mix fuel with air and generate the flame necessary for heating. They must be able to handle different types of fuels and provide a stable and efficient flame.
- Pipes: Elements through which the product to be heated circulates, allowing heat transfer from the fire and hot gases to the pipes. They are made of materials resistant to high temperatures and corrosion.
- Bends or headers at the ends of the tubes: These elements are located at the ends of the tubes and are responsible for directing the flow through each of them. They also allow the safe connection between pipes and other sections of the process.
- Refractory: Material that lines the inside of the furnace, protecting the metal structures from heat and helping to maintain a uniform internal temperature and minimize heat loss.
- Metal walls: They make up the external structure of the furnace and provide the internal components, as well as helping to contain the heat inside the furnace.
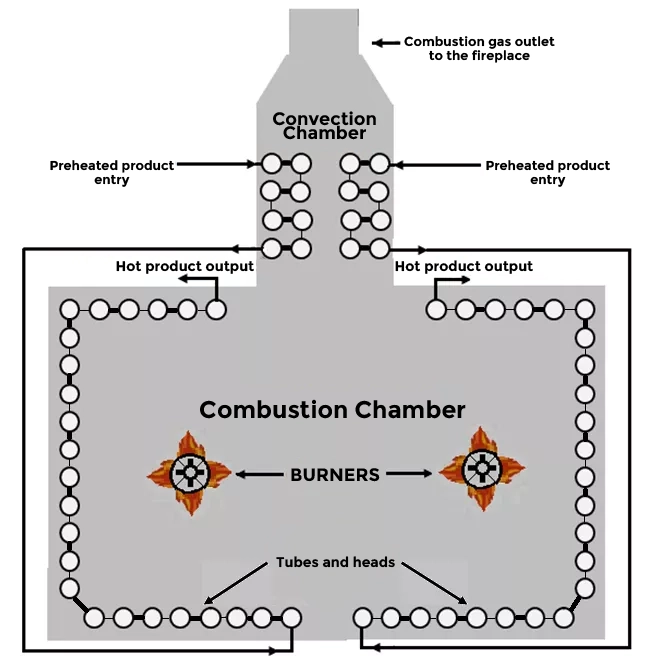
Furnace efficiency in the oil industry
It is defined as the ability of the furnace to effectively transfer the heat generated to the desired process (such as heating of crude oil or derivatives) with the minimum energy consumption and emissions. Several parameters are fundamental to ensure and evaluate this efficiency:
- Thermal efficiency: Refers to the proportion of the heat generated that is actually used in the process. Thermal efficiency is critical and can be improved with proper furnace design, good maintenance, and efficient operation.
- Air-fuel ratio: An optimum air-fuel mixture is essential for complete and efficient combustion. Too much air can lead to unused heat losses and not enough air can result in incomplete combustion, increasing emissions of harmful compounds.
- Combustion control: Advanced control systems allow real-time adjustment of furnace operation to optimize combustion, improve heat transfer, and reduce energy consumption and emissions.
- Insulation and refractory maintenance: Proper maintenance of the refractory material that lines the inside of the kiln is vital to minimize heat loss and overheating of the metal walls. A poorly maintained refractory can mean significantly reduced thermal efficiency.
- Structural integrity and furnace design: The shape and size of the furnace should be designed to maximize heat transfer efficiency. This includes tube layout, burner location, and overall furnace geometry.
- Regular monitoring and maintenance: The efficiency of a furnace can degrade over time due to wear, deposit buildup, and other operating conditions. A constant monitoring inspection program and regular maintenance helps maintain operating efficiency and prevent failures.
- Responsiveness to load variations: The ability of the furnace to effectively adjust its operation in response to variations in heat demand is very important to maintain efficiency under different operating conditions.
Importance of refinery process furnace evaluation
Inspection of refinery process furnaces is performed using a variety of non-destructive testing (NDT) methodologies and techniques, ranging from visual inspections to more advanced testing. These methodologies allow the detection and evaluation of different types of damage and deterioration, such as corrosion, erosion, cracking, deformation, and refractory lining failures.
By identifying and addressing these problems in a timely manner, unplanned failures can be prevented, unplanned downtime minimized and maintenance and repair costs reduced. API 573 (Inspection of Fired Boilers and Heaters) is one of the most important suggested practices for furnace inspection.
NDT techniques for evaluating industrial furnaces
Several non-destructive testing (NDT) methods and techniques play a key role in the inspection of furnaces. These techniques allow the integrity of the equipment to be inspected without compromising its performance or safety. Some of the most common NDT methods used to evaluate process furnaces in the petroleum industry include:
- Visual inspection: This is the most basic and important methodology for the evaluation of furnaces in the oil industry. It detects visible signs of damage, such as cracks, corrosion, or deformations in the structure of the furnace, detachment of refractory, and longitudinal and diametrical deformations of the tubes. The inspectors use tools such as cameras, calipers, inspection hammers, and comparators, among others, and depending on the results of the inspection it can be determined whether it is necessary to use other techniques in addition to those planned.
- Ultrasound: It is used to measure the thickness of the tubes and detect internal defects, such as cracks or other types of discontinuities, by sending ultrasonic waves through the furnace material and recording the echoes.
- Industrial radiography: This methodology uses ionizing radiation to create high-resolution images of the furnace interior, allowing the detection of internal defects such as cracks, foreign material inclusions, or corrosion.
- Magnetic particles: Involves the application of magnetic particles on the surface of the material to be evaluated to detect surface and subsurface discontinuities.
- Penetrating liquids: These are chemical substances that are applied on the materials penetrating cracks and discontinuities open to the surface. After a penetration time, the excess liquid is wiped off and a developer is applied to visualize the discontinuities.
- Infrared thermography: It is a technique that uses special cameras to capture and visualize heat, detecting radiation in the infrared spectrum and converting it into a visual image (thermogram, Figure 2). Its main use in process furnaces is to monitor external temperatures on the furnace walls to locate possible damage to the refractory. Also, for the evaluation of heat transfer efficiency, temperature uniformity inside the furnace, and to detect hot spots in the tubes that may cause creep to them.
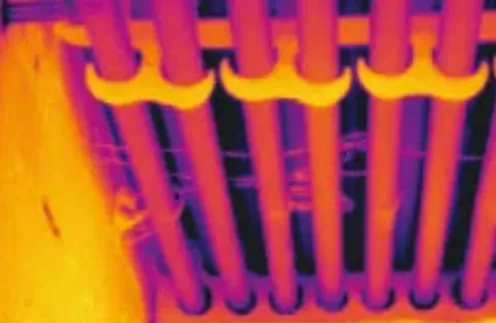
Efficiency of process furnaces
In addition to ensuring the structural integrity and operational safety of process furnaces, it is also important to evaluate and improve their efficiency. The efficiency of a furnace refers to its ability to produce the desired amount of heat or energy with the lowest possible consumption of fuel and resources. Improving the efficiency of process furnaces can have several benefits, including reducing operating costs, minimizing environmental impact, and improving competitiveness in the marketplace.
To evaluate the efficiency of a process furnace, it is necessary to consider various factors, including its design, size, load capacity, fuel used, combustion system, thermal insulation, and maintenance. Some common strategies for improving the efficiency of process kilns include:
- Fuel optimization: Use more efficient and cleaner fuels, such as natural gas or process gas, instead of more polluting fossil fuels such as fuel oil.
- Improving thermal insulation: Install high-quality insulation materials in the furnace to reduce heat losses and improve energy retention.
- Optimizing the combustion system: Adjusting combustion parameters, such as air-fuel ratio, air distribution, and flame temperature, to maximize efficiency and minimize emissions.
- Implementation of heat recovery technologies: Install heat recovery systems to take advantage of waste heat from the furnace and use it to preheat combustion air or generate steam.
- Preventive and corrective maintenance: It is advisable to carry out regular furnace inspections, cleaning, and routine maintenance to ensure optimal furnace operation and prevent efficiency problems.
Conclusion
Comprehensive evaluation of furnaces in the oil industry is essential to ensure their safe and efficient operation. Through advanced non-destructive testing techniques and comprehensive analysis, potential problems can be identified and addressed before they become costly failures. In addition, continuous improvement in process furnace efficiency reduces operating costs and contributes to environmental sustainability by minimizing energy consumption and greenhouse gas emissions. Investing in comprehensive furnace evaluation is one strategy to optimize the performance and reliability of operations in the petroleum industry.
References
- https://www.flir.com/discover/instruments/furnace-boiler/petroval