Table of Contents
- Importance of the integrity of pipes through NDT
- Challenges in submerged pipeline inspection
- Guided wave ultrasound test in underwater pipeline inspection
- How does the GWUT work?
- Advantages of GWUT in submerged pipeline inspection
- Limitations of GWUT in the inspection of submerged pipes
- Future Trends in Submerged Pipe Inspection
- Conclusion
- References
Submerged pipelines play a vital role in various industries, such as oil and gas, water supply and shipping. Ensuring the integrity of these pipelines is necessary to prevent environmental disasters, economic losses and possible threats to human life. An advanced technique that is gaining importance in this regard is Guided Wave Ultrasonic Testing (GWUT). This article delves into the importance of assessing the integrity of submerged pipelines and how GWUT emerges as a powerful tool for this purpose.
Importance of the integrity of pipes through NDT
Submerged pipelines face a variety of challenges, such as corrosion, erosion and external damage caused by marine activities. Failure to address these issues can lead to leaks, spills, and structural failures with serious consequences. Regular inspections and maintenance are important to ensure the long-term reliability and safety of these critical infrastructure components.
Challenges in submerged pipeline inspection
Inspecting submerged pipelines presents unique challenges compared to their above-ground counterparts. Limited accessibility, harsh underwater conditions, and high costs associated with traditional inspection methods make it imperative to explore advanced technologies. Through qualified NDT and underwater personnel, conventional Non-Destructive Testing (NDT) methods, such as visual, ultrasonic (UT) and Eddy current tests, could be used to detect and size these defects. However, if the location of the defect is unknown, then the challenge lies in the kilometers of subsea line that must be inspected.
The use of in-line inspection instruments (ILI) such as instrumented tools (also called smart pigs) which make use of magnetic field leakage or ultrasound, have gained wide acceptance in the inspection of long runs of pipelines, however, the conditions for carrying out inspections of submerged offshore pipeline lines represent a challenge for its use, such as the facilities for launching and collecting the instrument, the transmission of data due to distance and the aquatic environment, the diameter of underwater pipelines which can limit the size of instrumented tools that can be used, among others.
Guided wave ultrasound represents a solution to overcome these challenges.
Guided wave ultrasound test in underwater pipeline inspection
GWUT is a non-destructive testing (NDT) method that uses ultrasonic Lamb waves to inspect the condition of pipes. Unlike traditional ultrasonic testing, which typically requires direct contact with the material, GWUT can propagate along the pipeline without requiring direct access. This makes it particularly suitable for inspecting submerged pipelines, where direct access may be limited for the application of other NDT techniques. To do this, GWUT uses an array of special transducers to be installed by divers or robots, personnel specialized in underwater tasks such as cleaning the pipeline (divers), and the use of software for this application.
Several industries have successfully implemented the GWUT for submerged pipeline inspection, demonstrating its effectiveness in ensuring pipeline integrity. Case studies in the oil and gas sector, water utilities and marine facilities show the diverse applications and positive results of adopting GWUT as a reliable inspection technique
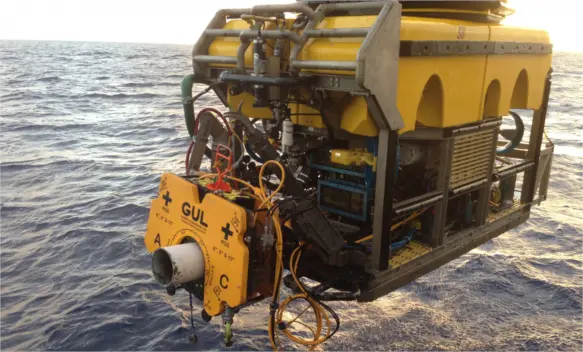
How does the GWUT work?
The GWUT guided wave ultrasound test involves the generation of torsional Lamb ultrasonic waves that are guided by the limits of the pipe thickness and travel along the pipe. As in ultrasound, a wave reflection will occur when it encounters a change in the cross section of the pipe thickness. This change may be caused by a decrease in thickness due to corrosion.
These waves detect anomalies, such as corrosion, cracks, and other defects, by analyzing changes in wave patterns. The ability to cover long lengths of pipe without the need for physical contact makes the GWUT an efficient and cost-effective method of inspecting submerged pipes.
Under “ideal” conditions, GWUT can cover a total length of 200 m to 300 m, these conditions being: The pipe is not buried, it does not yet contain product inside, it has no coating, its fastening system is not very tight, it does not have accessories installed and it is a straight run (no elbows). As these ideal conditions degrade, the inspected length of the pipe decreases.
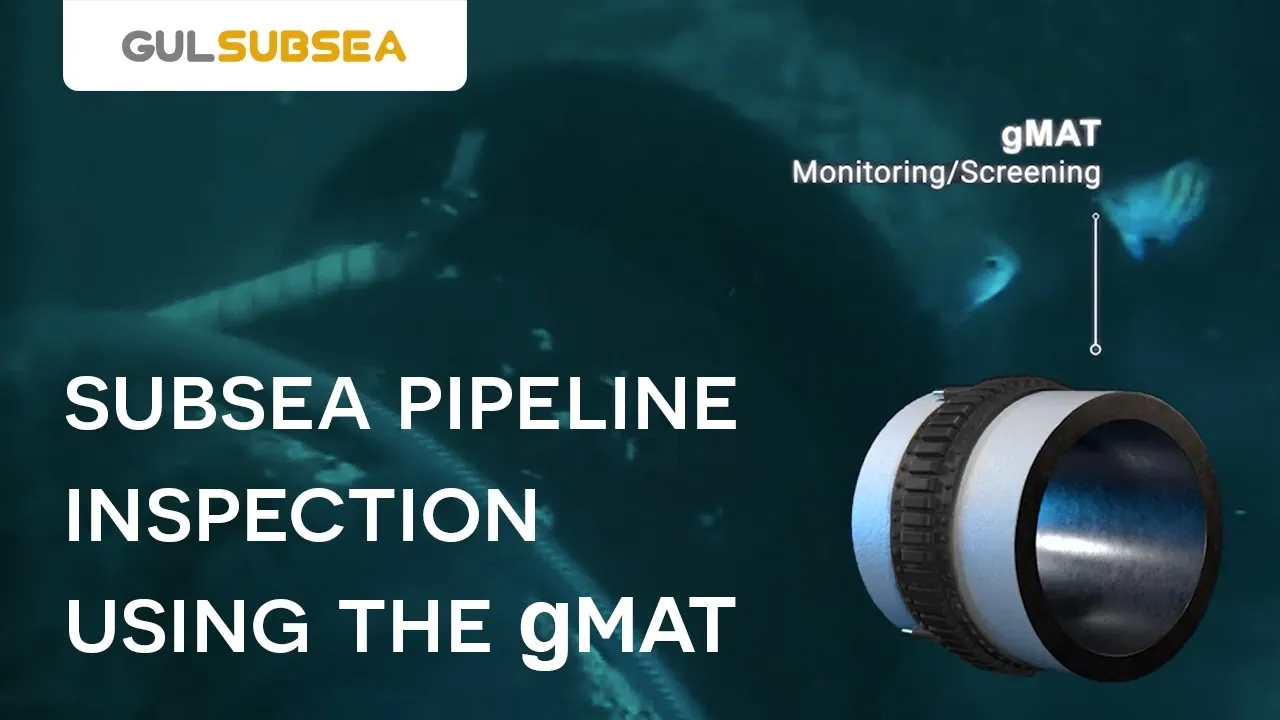
Video courtesy Guided Ultrasonics Ltd. (GUL): Guided Wave Testing (GWT) with GUL Subsea technology.
Advantages of GWUT in submerged pipeline inspection
- Long Distance Inspection : The GWUT can cover significant lengths of submerged pipelines in a single inspection, reducing the time and resources required for assessment.
- Minimal disruption : Traditional inspection methods often require shutting down the pipeline, draining water or using divers, causing disruptions to operations, the Guided Wave method can be applied with the pipeline in service.
- Early Defect Detection : The GWUT can detect defects in their early stages, allowing for timely interventions and preventative maintenance. This proactive approach minimizes the risk of catastrophic failure.
- Cost-effective: The GWUT’s efficiency in covering long distances and its ability to operate without direct contact contribute to its cost-effectiveness compared to traditional inspection methods.
Limitations of GWUT in the inspection of submerged pipes
Although GWUT has its advantages, it also has some limitations, especially when applied to subsea pipeline inspections. Here are some of the limitations, most of which also occur in overhead pipeline inspection and other applications:
- Limited sensitivity to localized defects: It is effective in detecting and characterizing defects such as corrosion, erosion and wall thinning along the pipeline. However, it may have limited sensitivity for small or localized defects such as pits or cracks, especially if they are not oriented favorably with respect to guided wave propagation.
- Limitation in discriminating defect types: Although GWUT can identify the presence of defects, it may have limitations in accurately discriminating between different types of defects. For example, it can be challenging to distinguish between corrosion and cracks based solely on guided wave signals.
- Challenges with complex geometry: Subsea pipelines often have complex geometries, such as curves, tees, and other features. These geometric complexities can affect the propagation and reception of guided waves, making it difficult to obtain reliable and accurate inspection results in these areas.
- Influence of temperature and coating: Method performance can be influenced by extreme temperatures or thick coatings, affecting guided wave propagation and signal quality.
- Limitation in axial resolution: It has a relatively long wavelength compared to traditional ultrasonic waves. This can result in limited axial resolution, making it difficult to accurately locate defects along the pipe.
- Limited investigation depth: In cases where defects are located deep within the pipe wall, guided waves may not effectively reach and detect these defects.
- Limitation on inspection speed: The inspection speed of guided waves may be slower compared to other NDT methods, which may be a consideration for large-scale subsea pipeline inspections.
- Attenuation and water depth: In underwater environments, water depth can affect wave propagation, and wave attenuation can occur over longer distances. This may limit the effective scope of the inspection and require careful consideration of deployment methods.
Despite these limitations, guided wave ultrasonic testing remains a valuable tool for subsea pipeline inspections, especially for detection and monitoring purposes.
Future Trends in Submerged Pipe Inspection
As technology continues to evolve, the future of submerged pipeline inspection promises promising advancements. Integration with artificial intelligence for data analysis, robotics, the development of more portable and automated GWUT systems, advanced data analysis, and increased standardization in inspection protocols are expected to further enhance the capabilities of this method.
Conclusion
The ability to detect defects at early stages, cover long distances and minimize disruption to operations makes the GWUT a valuable tool for ensuring the reliability and safety of submerged pipelines. As industries continue to prioritize preventative maintenance and advanced inspection techniques, the GWUT is poised to play a crucial role in the future of submerged pipeline integrity assessment.
References
- VICTOR. M. NÚÑEZ LEDESMA, ELOY PÉREZ BARUCH, ALESSANDRO DEMMA, MJS LOWE. Guided Wave Testing in a Submerged Gas Pipeline; Consulted on January 5, 2024; https://www.ndt.net/article/panndt2011/papers/30_NUNEZ%20LEDESMA.pdf
- WON BAE NA, TRIBIKRAN KUNDU. Underwater Pipelines Inspection Using Guided Waves; Consulted on January 8, 2024; https://www.researchgate.net/publication/245364714_Underwater_Pipeline_Inspection_Using_Guided_Waves
- FRANCISCO CR MARQUES, ALESSANDRO DEMMA. Ultrasonic Guided Waves Evaluation of Trials for Pipeline Inspection; Consulted on January 8, 2024; https://www.ndt.net/article/wcndt2008/papers/96.pdf
- GUIDED ULTRASONIC LTD, GUL. How to Inspect Subsea Pipes Using GUL Subsea; Consulted on January 9, 2024; https://www.linkedin.com/pulse/how-inspect-subsea-pipes-using-gul-guided-ultrasonics/