Introduction
END 4.0 is an integration to the new industrial revolution. With continued digitalization and Internet capabilities, Industry 4.0 will become the fourth industrial revolution. The availability of the Internet of Things (IOT), cyber systems, cloud formation, digital platforms, and artificial intelligence, including neural networks, will in the future offer great possibilities and challenges in all areas of production, services in society.
The objective of the Industry 4.0 project is to support the manufacturing of plants of the future in the world so that production is faster, more efficient, and more flexible. It comprises complete networks within industrial processes, from raw materials to the finished product, including design, taking into account non-destructive testing (NDT)1, inspection, production, central quality control, and quality monitoring. Structural Health (SHM).
In the changing manufacturing landscape, the integration of cutting-edge technologies has become a fundamental driver of efficiency and quality. Non-Destructive Testing 4.0 (NDT 4.0) represents a paradigm shift in this sector, taking advantage of the power of Industry 4.0 technologies to improve manufacturing processes.
This article explores the intersection between NDT 4.0 and manufacturing process optimization, shedding light on the transformative impact it has on quality assurance, productivity, and overall operational excellence.
What is industry 4.0?
Industry 4.0, also known as the fourth industrial revolution, refers to the continuous transformation of traditional industrial and manufacturing practices through the integration of digital technologies. This concept is based on the three previous industrial revolutions:
- First industrial revolution: Mechanization and use of hydraulic and steam energy (late 18th century).
- Second industrial revolution: Mass production and use of electricity and assembly lines (late 19th and early 20th centuries).
- Third industrial revolution: Automation and the rise of computers and electronics (late 20th century)
This industry introduces a new era characterized by the convergence of physical and digital systems, creating “smart factories” where robotic machines, processes and systems communicate and cooperate with each other, optimizing manufacturing processes (see video, courtesy of VisiConsult}.
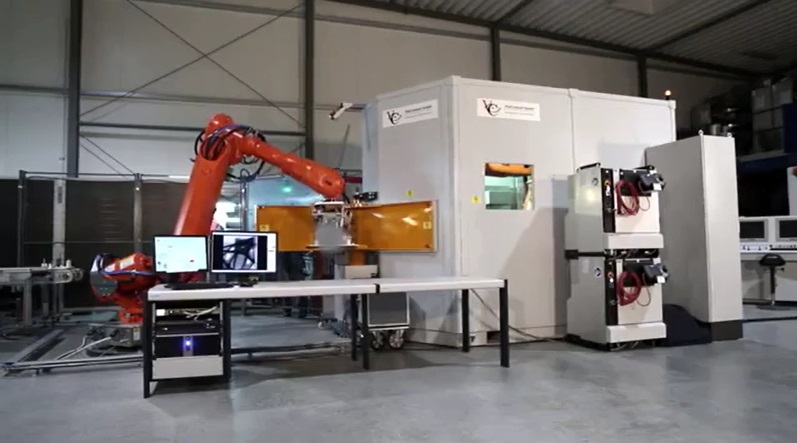
Video, courtesy of VisiConsult
What are END 4.0?
NDT 4.0 2.3 refers to the integration of NDT methods and techniques with the principles of Industry 4.0, characterized by the widespread use of automation, data exchange and smart technologies. This synergy aims to produce a connected and intelligent manufacturing environment, where real-time data and advanced analytics drive decision-making processes 4 .
Key components of NDT 4.0 3.4
- IoT and Sensor Technology: The Internet of Things (IoT) has revolutionized the way information is collected and analyzed in manufacturing. In the context of NDT 4.0, sensors are deployed along the production line to collect real-time information on the quality and performance of materials and components. This continuous monitoring ensures early detection of defects, reducing the risk of low-quality products reaching the market.
- Big Data and Analytics: The vast amount of data generated by IoT-enabled sensors is processed using advanced analytics. Big data analytics not only identifies anomalies, but also provides valuable insights into the root causes of defects. Manufacturers can leverage this information to implement proactive measures, optimizing their processes and minimizing the likelihood of future problems.
- Artificial Intelligence (AI) and Machine Learning (ML): AI and ML algorithms play a considerable role in NDT 4.0 by automating decision-making processes. These technologies can learn from historical data, predict potential defects, and suggest improvements. The result is a more adaptive manufacturing environment that continually refines its processes for improved efficiency 2 .
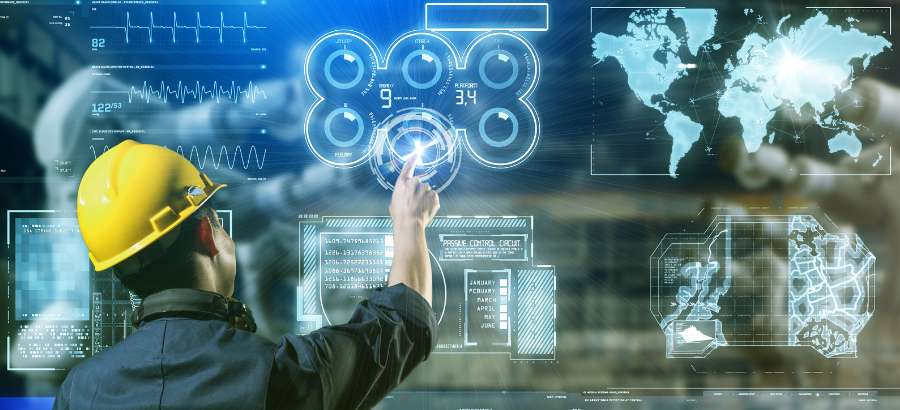
- Digital Twins: Based on the data collected, simulations can be used to recommend actions or predict decisions. A digital twin refers to a virtual representation of a physical object, system, or process. This representation is created using data from the real-world counterpart and the digital twin is designed to mimic the physical entity in a digital space. An AI can be used as a basis for this type of simulations.
- Cloud: Data can be stored securely in a cloud and then accessed from any location. It consists of a network of distributed servers.
- 5G: It is a mobile data transmission technology and successor to 4G/LTE, it allows the connection of a large number of devices and provides strong real-time data connectivity.
- Blockchain: With a blockchain, data can no longer be changed without detection, improving traceability and trust.
Benefits of NDT 4.0
- Improved Quality Assurance: By continuously monitoring and analyzing data, END 4.0 ensures a higher level of quality assurance. Early defect detection reduces the likelihood of defective products, leading to greater customer satisfaction and brand reputation. This proactive approach to quality control also minimizes the need for costly rework and recalls.
- Increased Productivity: The real-time nature of NDT 4.0 allows for faster decision making and problem resolution. Manufacturers can identify and address issues promptly, reducing downtime and optimizing production schedules. This increased efficiency contributes to higher overall productivity and resource utilization, i.e. optimization of production processes.
- Cost Reduction: Through defect prevention and process optimization, END 4.0 helps manufacturers reduce costs associated with rework, scrap, and warranty claims. The predictive capabilities of AI and ML also enable more efficient allocation of resources, reducing unnecessary expenses.
- Regulatory Compliance: END 4.0 facilitates better compliance with regulatory standards and industry standards. Continuous monitoring and documentation of manufacturing processes provide a transparent and traceable record, ensuring that products meet required specifications.
Challenges in the implementation of NDT 4.0
- Skill Set Transition: Existing non-destructive testing apparatus and methodologies required completely different skill categories which, after the implementation of NDE 4.0, will become irrelevant. Skills such as knowledge of materials, temperature, behavior and installation of devices will be replaced by knowledge of information technologies and communication systems.
- Adaptation to existing systems: Profits and economic viability are of utmost importance for all industries, and large-scale implementation of Industry 4.0 and NDE 4.0 can be a drastic change that involves the expenditure of human resources, capital and hierarchy. They demand the growth of a new style of leadership and administration, led by flexible, involved and competent leaders 5 .
- Awareness of the importance of NDT 4.0 implementation: Many organizations have not yet adopted the concepts of non-destructive testing, as the concept of greater initial investment for long-term reduction of resources and capital losses has often been received with concern. It is vital to internalize the importance and need to implement END 4.0 technologies for the efficient development of organizations.
Conclusions
In the era of Industry 4.0, the union of Non-Destructive Testing with cutting-edge technologies has given rise to NDT 4.0, transforming the manufacturing landscape. This integration not only enhances the traditional role of NDT in ensuring product integrity, but also contributes to the optimization of manufacturing processes.
As industries realize the full potential of NDT 4.0, they are not only protecting their products, they are also paving the way to a future where innovation and optimization go hand in hand.
New technologies like these have a huge impact on NDT today and continue to advance and grow as more companies discover how to use them as efficiently as possible.
References
- AIMIL. Non-Destructive Testing: A Complete Guide and How It’s Transforming Manufacturing and Quality Assurance; Consulted on November 14, 2023; https://www.aimil.com/blog/non-destructive-testing/
- MAXIMILIAN TOPP. How does Artificial Intelligence (AI) in NDT work? Consulted on November 14, 2023; https://sentin.ai/en/ai-in-ndt/
- LAURA FLINKERT. Definition: What are NDT 4.0 & NDE 4.0?; Consulted on November 15, 2023; https://sentin.ai/en/what-is-ndt-nde-4-0/
- RAHUL ALREJA. NDT and Industry 4.0; Consulted on November 15, 2023. https://www.qualitymag.com/articles/95370-ndt-and-industry-40 ?
- LENNART SCHULENBURG. NDT 4.0 – A Technology Overview; Consulted on November 16, 2023. https://www.ndt.net/article/ndtp2021/papers/NDT_4.0_—_A_Technology_Overview.pdf