Introduction
Diesel engines have been a key component of modern industry due to their efficiency, durability, and ability to operate in demanding conditions. Their presence is fundamental in sectors such as freight transportation, power generation, mining, and construction, where high-power engines with low fuel consumption are required. In particular, four stroke engines have proven to be highly efficient in these applications, and their operation is closely linked to the use of compressed air in combustion.
Since their invention by Rudolf Diesel in the 19th century, these engines have undergone significant development, improving efficiency and reducing emissions. Technological advancements have led to electronic injection systems, advanced turbocharging, and diesel particulate filters (DPF), allowing cleaner and more sustainable performance without sacrificing power. Additionally, the use of compressed air in these engines enhances combustion efficiency and reduces pollutant emissions.
This article explores the operating principles of diesel engines, their most innovative technologies, and their main industrial applications. Additionally, we will address the environmental challenges and future trends that will define the role of these engines in the industry, emphasizing the relevance of four stroke engines and the impact of compressed air on their performance.
Operating principle of diesel engines
Diesel engines operate on the principle of compression ignition, distinguishing them from gasoline engines, which rely on spark ignition. In a diesel engine, air is compressed at high pressure, reaching temperatures high enough for the fuel to ignite spontaneously when injected. This process largely depends on compressed air, which facilitates efficient and uniform combustion.
The combustion cycle in four stroke Diesel engines
The cycle of four stroke engines consists of four main phases:
- Intake: The intake valve opens, and the piston moves down, allowing the entry of compressed air without fuel mixture.
- Compression: The intake valve closes, and the piston moves up, compressing the air until its temperature is high enough to ignite the diesel. The use of compressed air at this stage is crucial for improving the engine’s thermal efficiency.
- Power Stroke (Combustion): At the peak of compression, the injection system sprays diesel fuel into the chamber. The mixture ignites instantly due to the heat generated by compression, causing a controlled explosion that pushes the piston downward and generates mechanical power.
- Exhaust: The piston moves back up, opening the exhaust valve to expel combustion gases from the cylinder. In some modern systems, compressed air is used in this phase to improve gas evacuation and reduce resistance in the engine cycle.
Key differences between Diesel and Gasoline Engines
- Ignition: While gasoline engines require a spark plug for ignition, four stroke diesel engines generate combustion through air compression.
- Thermal efficiency: Four stroke diesel engines have higher thermal efficiency, meaning they convert more fuel energy into useful work.
- Fuel Consumption: Thanks to their design and higher compression ratio, four stroke diesel engines consume less fuel than gasoline engines for the same amount of energy generated.
- Durability: Operating at lower revolutions per minute (RPM) and using more robust materials, four stroke engines tend to have a longer lifespan.
The role of compressed air in combustion
Compressed air plays a fundamental role in the combustion process of four stroke diesel engines. The higher the air compression, the higher the temperature, allowing the diesel to ignite without needing a spark. This feature is crucial for engine performance, as greater compression enhances energy efficiency and reduces fuel consumption.
In the following video, you will see how a diesel engine works, the combustion cycle, and its main components. Watch the detailed animation here. Source: Automotive System.
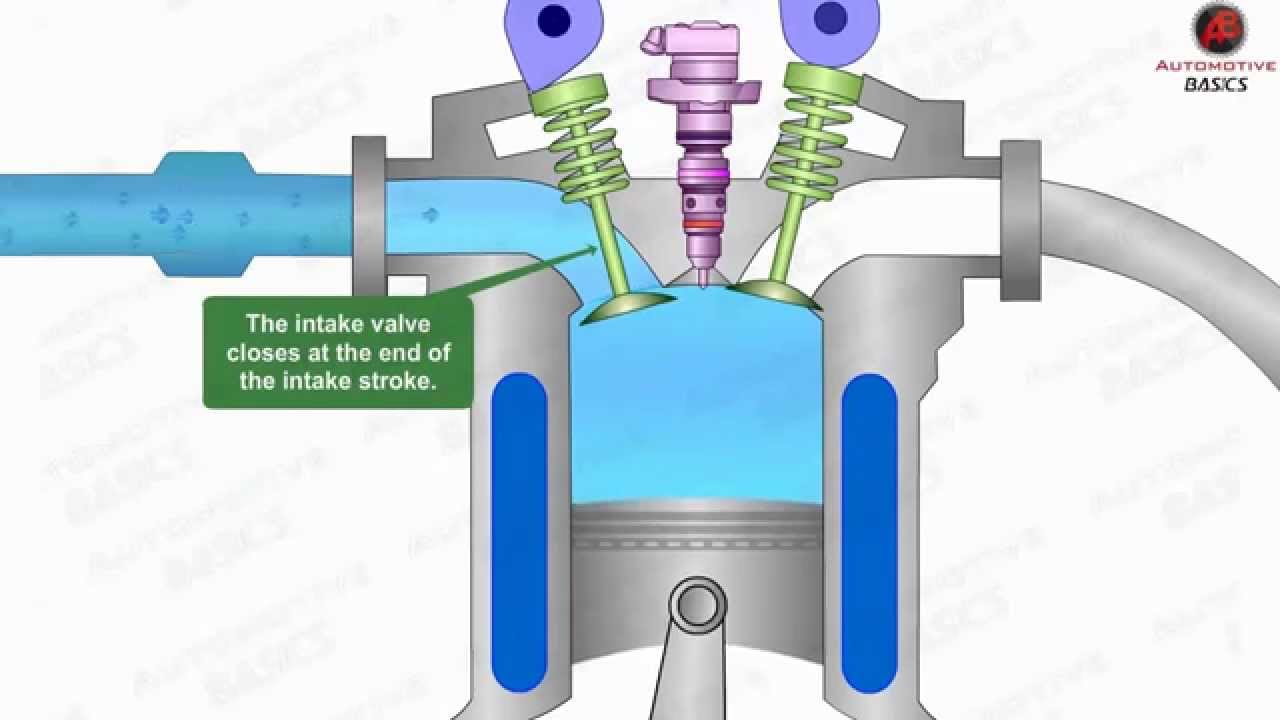
Modern technologies in diesel engines
Technological advancements have made diesel engines more efficient, powerful, and environmentally friendly. Below are the most important innovations in these engines.
Evolution of fuel injection
One of the most significant advancements in diesel engines has been the improvement of fuel injection systems. Originally, these engines used mechanical injection, which, while effective, did not allow precise control over the amount and timing of injection.
Today, most modern engines use the Common Rail system, which offers significant advantages, including greater efficiency, lower emissions, and reduced noise. Additionally, these systems are being optimized to improve the combustion process of alternative fuels such as synthetic diesel, further reducing environmental impact:
- Greater efficiency: Allows high-pressure fuel injection in multiple phases, optimizing combustion.
- Lower emissions: Reduces the production of nitrogen oxides (NOx) and particulate matter.
- Reduced noise and vibrations: Provides a more uniform and quieter combustion process.
Turbocharging in diesel engines
Turbocharging has become a standard in modern diesel engines due to the benefits it offers in terms of power and efficiency.
Advantages of turbocharging in diesel engines
- Power increase: A turbo allows more air to enter the cylinder, improving combustion and increasing engine power without the need to increase its size.
- Fuel efficiency: By utilizing exhaust gases to power the turbo, energy waste is reduced, and fuel performance is improved.
- Reduction of harmful emissions: It improves the air-fuel mixture, reducing the amount of harmful particles and gases.
Variable Geometry Turbochargers (VGT)
One of the most advanced innovations in this field is the use of Variable Geometry Turbochargers (VGT), which allow the airflow to be adjusted based on the engine’s needs. This results in:
- Better response at low revs: Eliminating turbo lag in power delivery.
- Higher efficiency across the operating range: Optimizing combustion under different load conditions.
Diesel Particulate Filters (DPF)
The use of diesel particulate filters (DPF) has been crucial in reducing pollutant emissions by trapping soot particles before they are released into the environment. However, their optimal performance depends on the use of Ultra-Low Sulfur Diesel (ULSD), as this fuel minimizes residue buildup in the filter, extending its lifespan and reducing the need for maintenance. To learn more about this clean fuel and its impact on the industry, you can read our article on Ultra Low Sulfur Diesel (ULSD).
DPF operation
- They trap and store soot particles in their porous structure.
- When the filter reaches its maximum capacity, a regeneration process is activated, where the trapped particles are burned at high temperatures.
DPF challenges and maintenance
- Filter clogging: If regeneration doesn’t occur properly, the filter can become blocked, reducing engine efficiency.
- Additional fuel consumption: Forced regeneration requires more fuel to reach the optimal soot combustion temperature.
- Technological solutions: New designs include pressure and temperature sensors to optimize regeneration and improve the filter’s lifespan.
Industrial applications of diesel engines
Diesel engines have been a fundamental pillar in the industry due to their high energy efficiency, great load capacity, and durability in extreme conditions. Thanks to their robust design and low specific fuel consumption, they are the preferred choice in multiple sectors requiring reliable power and extended autonomy. Below are the main industrial applications of these engines.
Freight transportation and logistics
Heavy cargo transportation relies heavily on diesel engines due to their high efficiency and ability to operate long hours without interruptions. They are commonly used in:
- Freight trucks: Most long-haul trucks use diesel engines due to their superior fuel economy and capacity to move large volumes of goods.
- Diesel-electric trains: In areas where railway electrification is not feasible, diesel-powered trains generate the electricity necessary for their operation, providing autonomy and power.
- Cargo ships and vessels: The maritime sector employs diesel engines for their high reliability and efficiency on long-distance trips. High-displacement engines with low revolutions ensure continuous operation with less wear.
Energy sector
Diesel engines play a crucial role in power generation, especially in areas where the electrical grid is unstable or non-existent. Some of their main uses in this sector include:
- Backup power generators: Hospitals, data centers, airports, and critical industries use diesel generators as auxiliary power sources to ensure supply in case of grid failure.
- Autonomous power plants: In remote or isolated areas, such as oil rigs and mining camps, diesel engines provide reliable power without relying on external electrical infrastructure.
- Microgrids and distributed generation: In hybrid systems with renewable energy, diesel engines combine with solar or wind sources to stabilize electricity generation. Some advanced setups now integrate alternative fuels, including synthetic diesel, to further reduce emissions while maintaining energy reliability.
Construction and mining industry
Heavy machinery used in construction and mining relies on diesel engines due to their high traction capacity and resistance in hostile environments. Common applications include:
- Excavators, front loaders, and backhoes: These require engines with high torque to move large volumes of material efficiently.
- Mining dump trucks: Heavy-duty vehicles operating in extreme conditions require high-displacement, durable engines.
- Drilling and crushing equipment: Used in mining to extract minerals, where reliability and autonomy are essential.
Agricultural sector
In the agro-industrial sector, diesel engines have been crucial for improving operational efficiency and mechanizing agricultural tasks. Equipment relying on these engines includes:
- Agricultural tractors: Equipped with 4-stroke diesel engines that provide constant power for plowing, planting, and harvesting.
- Harvesters and planters: These machines require engines with high torque and durability to operate in demanding terrains.
- Irrigation systems: Diesel-powered water pumps allow irrigation over large agricultural areas without relying on electrical grids.
The use of diesel engines in these sectors is due to their ability to provide high power, low maintenance, and autonomy in remote areas, all critical factors for industries that depend on robust and reliable equipment.
Challenges and future of diesel engines
Despite their efficiency and versatility, diesel engines face a number of challenges in a context where environmental sustainability and emission reductions have become global priorities. The industry has responded with technological innovations and the development of cleaner fuels to ensure the viability of these engines in the future.
Environmental regulations and transition to cleaner energies
Environmental regulations, such as the Euro 6 standard in Europe and the EPA regulations in the United States, have imposed strict limits on nitrogen oxide (NOx) emissions and harmful particles generated by diesel engines. To comply with these regulations, manufacturers have implemented technologies such as:
- Selective Catalytic Reduction (SCR) systems: Uses a urea additive (AdBlue) to reduce NOx emissions.
- Diesel Particulate Filters (DPF): Trap and remove soot generated by combustion.
- Hybrid diesel engines: Integrate electric systems to improve efficiency and reduce fuel consumption.
Development of Biofuels and synthetic fuels for diesel engines
The transition to alternative fuels is one of the key strategies to reduce the carbon footprint of diesel engines. Among the most promising options are:
- Biodiesel (B100, B20): Derived from vegetable oils and animal fats, it can be used in conventional diesel engines with minimal modifications.
- Synthetic diesel (HVO – Hydrotreated Vegetable Oil): A renewable fuel with similar properties to fossil diesel but with a lower environmental impact.
- E-fuels and hydrogen-based synthetic diesel: Developed through carbon capture processes and electrolysis, they offer a sustainable alternative with cleaner combustion.
Innovations in emission reduction and thermal efficiency
The future of diesel engines also focuses on improving thermal efficiency and reducing their environmental impact through innovations such as:
- High-pressure engines with a higher compression ratio: Optimizing combustion and reducing fuel consumption.
- New multi-injection technologies: Allow finer fuel atomization, improving efficiency and reducing emissions.
- Hybridization and partial electrification: Combining diesel engines with electric systems to improve energy efficiency and reduce emissions in industrial and transportation applications.
Despite environmental and regulatory challenges, diesel engines continue to evolve with cleaner technologies and sustainable fuel alternatives. Their role in industry remains crucial, especially in applications where efficiency and autonomy are paramount. In the future, we are likely to see a combination of advanced diesel engines, renewable fuels, and hybrid solutions, ensuring their viability in a world transitioning toward sustainability.
Corrosion protection for diesel engines
To extend the service life and ensure the reliability of diesel engines, especially during periods of inactivity, storage or transportation, the use of Volatile Corrosion Inhibitors (VCI) has become increasingly relevant.
Cortec Corporation has developed VpCI®-706, an additive formulated for use in diesel and biodiesel fuels. This innovative product effectively protects ferrous metal surfaces in contact with fuel and those exposed to the vapor phase, mitigating the risk of corrosion. Its application in the fuel tanks of heavy equipment guarantees protection during storage, transportation and operation.
Conclusions
Diesel engines have been, and continue to be, a key component in modern industry due to their energy efficiency, durability, and load capacity. Their presence in sectors such as freight transportation, energy generation, construction, mining, and agriculture highlights their irreplaceable role in applications that require reliable power and long-term operation. Over the years, they have evolved significantly, adopting innovative technologies such as Common Rail injection, advanced turbocharging, and diesel particulate filters (DPF), improving both performance and environmental impact.
However, environmental and regulatory challenges require ongoing transformation. Stricter regulations have driven the development of emission reduction systems, as well as the integration of biofuels and synthetic fuels, which offer a more sustainable alternative without compromising engine efficiency and autonomy. The industry has also invested in hybrid solutions and improvements in thermal efficiency, ensuring their viability in a future where sustainability is a priority.
In conclusion, while electrification is advancing in various areas, 4-stroke engines will continue to play a crucial role in the global industry. The combination of advanced technology, renewable fuels, and stricter environmental regulations will enable these engines to evolve and remain a viable option in the future energy and transportation landscape. Furthermore, the implementation of compressed air in various combustion and exhaust processes will continue optimizing engine efficiency, ensuring their adaptability to new industrial and environmental demands.
References
Own source