In the oil and gas industry, operational safety and efficiency are critical to ensuring a constant flow of hydrocarbons through the supply chain. However, Corrosion Under Insulation (CUI), a hidden threat, represents one of the most critical challenges in terms of inspection, as it directly impacts the integrity of assets.
In both the downstream and upstream segments, the importance of addressing this issue and establishing risk-based inspection plans has been recognized. In this context, predictive techniques offer promising solutions for early detection and risk mitigation. CUI arises as a result of the interaction of the water present between the insulation and the metal surface of the pipes.
Precision and accuracy in CUI detection remains a major challenge in the inspection of isolated assets such as pipes, tanks and vessels. This article examines current inspection technologies, including visual inspection and non-destructive testing (NDT), and emphasizes the need for effective methods to address CUI-prone areas, with the goal of preventing unnecessary downtime and accidents.
Corrosion Under Insulation (CUI)
CUI is a form of corrosion that develops on the exterior of insulated metal equipment and pipes (Figure 1). This occurs due to the accumulation of moisture and the entry of water into the insulating material, creating a wet zone between the insulation and the metal surface that promotes corrosion. Various water sources can contribute, such as rain, water leaks, condensation, cooling towers, deluge systems, and steam leaks.
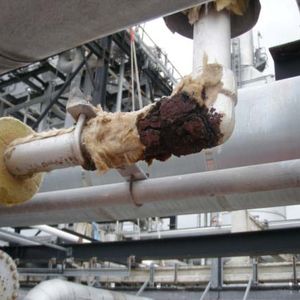
It is characterized as a form of localized corrosion that progresses rapidly under specific conditions, such as repetitive thermal cycles or the presence of chlorinated and acidic contaminants in the aqueous medium. Due to its hidden nature, it remains unnoticed until the insulation is removed or advanced Non-Destructive Testing (NDT) techniques 1 are applied to evaluate the condition of the asset under the insulation.
Challenges and consequences
Oil and gas companies face significant challenges in inspecting isolated assets, impacting both safety and maintenance costs. National Association of Corrosion Engineers (NACE) Reports; current AMPP, point out that between 40% and 60% of maintenance costs and a substantial part of hydrocarbon leaks are due to CUI. These problems have a negative impact in environmental and production terms.
The inspection of isolated assets involves an extensive investment of resources, especially when it comes to extensive networks of isolated pipelines in refineries and fractionation plants. Preventative maintenance and regular repairs are essential to address minor issues before they become more serious threats that could lead to production shutdowns and ultimately lead to catastrophic incidents.
How to prevent corrosion under insulation (CUI)?
In general, Corrosion Under Insulation can be mitigated by preventing water infiltration into the insulation system and keeping the metal surface of the pipes or vessel components dry during all phases of installation and useful life.
Manufacturing and Installation: Close monitoring and control during the manufacturing process and initial installation can prevent insulation defects, which in turn will decrease the risks of CUI.
Repair and maintenance during equipment operation: Properly carrying out insulation replacement or maintenance at various stages of repair and upgrades to pipelines and pressure vessels can also reduce the danger of CUI.
Inspection plan: The most crucial preventative measure to reduce the risk of corrosion under insulation in components involves having a solid inspection and monitoring plan for CUI-susceptible areas. Visual inspection, radiography (X-ray – RX), ultrasonic testing (PU) and surface testing (ES) with liquid penetrants are the most common methods for monitoring corrosion processes 2 .
Current inspection technologies
Various inspection technologies are used to address Corrosion Under Insulation (CUI) , including visual inspection and NDT, which use electromagnetic and acoustic waves, as well as electrochemical techniques to identify cracks and defects in insulation. However, these technologies have limitations and different advantages. The lack of an accurate detection technique and the challenge of implementing an early prediction method are persistent concerns.
Conclusions
Effective detection and mitigation of CUI is essential for the oil and gas industry. Investing in online detection technology has a significant impact on improving safety, reducing costs, and minimizing adverse effects on the environment.
The combination of multiple inspection techniques is crucial to obtain a complete assessment of the asset’s integrity. The lack of accurate detection technique and the need for risk assessment and prediction tools are challenges that need to be addressed in the industry to ensure safe and efficient operations in a highly competitive environment.
Bibliographic references
- Jesus Contreras “Advanced NDT techniques for the detection of Corrosion Under Insulation (CUI)”; www.inspenet.com, October 10, 2022< Link: https://inspenet.com/articulo/deteccion-corrosion-bajo-aislamiento-parte-1/
- https://cadeengineering.com/es/corrosion-bajo-aislamiento-cui/#:~:text=La%20corrosi%C3%B3n%20bajo%20aislamiento%20(CUI,agua%20bajo%20el%20aislamiento%20t%C3%A9rmico.