Introduction
Crude oil, due to its origin in natural deposits, contains components that are harmful to its processing, such as groundwater, suspended solids, sediments and dissolved salts. These elements lead to corrosion problems and therefore economic losses and material damage during the storage and processing of crude oil.
Corrosion of metal surfaces in contact with various process streams is a major problem associated with these substances. To safeguard facilities and equipment, chemical treatments are applied, from oil extraction to processing. Despite these efforts, primary distillation towers, in particular, face significant corrosion problems, with frequent damage to their interiors.
Despite the chemical treatments and evaluations, the control and protection of the facilities in these plants are complex due to the variability in the aggressiveness of the crude oil, depending on its type, mixtures, contaminants and corrosive agents. Evaluations of different materials commonly used in the construction of these towers are carried out using the NACE TM0169-76 1 technique.
When processing heavy crude oil, the corrosive effects of high concentrations of sulfur and organic acids must be considered, as well as the high temperatures and type of material, which deteriorate the refining equipment, generating scale and corrosive products that reduce the fractionation capacity of the crude oil. crude oil and complicate its transportation. The most critical corrosion problems usually manifest themselves at the tops and bottoms of the atmospheric distillation tower, the vacuum distillation tower, the furnaces and the transfer lines, affecting thermal efficiency, causing energy losses and plugging.
This section aims to highlight the main types of corrosion, identify where problems occur in primary atmospheric distillation units, and discuss materials commonly used to mitigate these problems.
Main types of corrosion in atmospheric distillation units
The main damage mechanisms due to aqueous corrosion in crude oil distillation processes are: corrosion by HCl, naphthenic acids and sulfidation. These processes can occur simultaneously, depending on the type of alloy, temperature conditions, pH, concentration, and it is possible that one of them is more critical than the others.
- HCl corrosion: Gaseous hydrochloric acid, formed from the hydrolysis of calcium and magnesium chlorides, then condenses in cold areas and upon contact with water forms hydrochloric acid, which is one of the main responsible for severe corrosion in top systems. Hydrochloric acid is formed according to the following reactions:Hydrochloric acid is formed according to the following reactions:
MgCl 2 +2H 2 O → Mg(OH) 2 + 2HCl
2HCl → 2H + + 2Cl –
2HCl + Fe → FeCl 2 + H 2
The mechanism of corrosion by H2S at low temperatures or at high pH in the presence of H 2 S the corrosion mechanism is:
FeCl 2 + H 2 S → FeS + 2HCl
After the HCl dissolves in water near the initial condensation point, the acid attacks the surface of the metal, producing pitting. Corrosion products are metal chloride salts. Additionally, when the pH of the water in this region is less than 5.0, HCl dissolves any metal sulfides, corrosion products, that are present. These corrosion products are carried to the site where the corrosion attack occurs. This is a dynamic corrosive system and there is a tendency to form small cavities. This medium is very aggressive since the chemical reactions occur simultaneously.
- Corrosion by naphthenic acids: Naphthenic corrosion occurs only in the presence of the liquid phase and has as main parameters of the corrosive process: the acidity of the crude oil, type of naphthenic acid, type of sulfide, temperature, turbulence, flow speed, degree of vaporization and the existence of two-phase flow. This attack is not uniform, which makes it difficult to detect and solve the problem. The presence of sulfides and the physicochemical characteristics of naphthenic acids, their content, boiling point distribution and decomposition temperature, have a direct effect on high temperature corrosion of the distillation unit.
- Sulfidic corrosion: Lasulfidation results from the reaction of steels with sulfur compounds at high temperatures. This phenomenon occurs when the metal reaches a temperature of 220°C. Important factors affecting sulfidation are alloy composition, temperature, and concentration of sulfide compounds. The susceptibility of an alloy to sulfidation is determined by its ability to form protective sulfide layers. The strength of ferrous alloys improves with the amount of chromium present.
Construction materials in crude distillation units
Most equipment in a crude distillation unit is made of carbon steel, suitable for temperatures up to 450°F (230°C). However, above this temperature, problems such as high temperature sulfur attack and naphthenic acid corrosion can arise. To address this, highly alloyed materials are used, especially in the upper zone of the Preflash column, where UNS 04400 coating is common.
In units designed to process “sweet” crude oil, the Preflash column incorporates specific coatings. The top uses UNS 04400 to resist HCl condensation, while the rest of the casing is bare carbon steel. Additionally, a 12% chrome coating is applied to the bottom to prevent groove corrosion.
At the feed inlet, it may be necessary to use Type 316 stainless steel for plants that process crude oils with high naphthenic acid content. It is essential to ensure that the nozzles in each zone are lined with the same material as the housing. Following service exposure, the casing immediately above and below the cladding should be closely monitored for possible wall leaks, with the need to expand the original clad areas being common.
In the vacuum column, which is typically coated with 12% chromium, the flash zone can be problematic due to naphthenic acid. For highly naphthenic crude oils, a Type 316 or 317 stainless steel liner may be required in areas operating above 450°F (230°C).
In sweet crude oil plants, lateral flow separators are often unlined, although atmospheric diesel and gasoil feeds reach temperatures of 550°F (285°C) and 650°F (345°C), respectively. However, in plants that handle sour crude oil, these hot strippers may require a 12% chromium coating.
Exchangers and pipes in distillation units
The metallurgy of heat exchangers varies depending on the composition and temperature of the stream. Most are carbon steel, but in freshwater cooled ones, admiralty brass tubes have been replaced by carbon steel due to improvements in water treatment.
In corrosive environments such as sea or brackish water, titanium tubes or superferritic and duplex stainless steels are used. Austenitic stainlesss are limited by their susceptibility to chloride stress cracking and pitting.
The most serious corrosion problems are found in the areas of initial condensation in overhead systems. Corrosion intensifies where HCl vapor, formed by the hydrolysis of chloride salts, dissolves in condensation water, creating a corrosive environment. UNS 04400 liners and trays on top of columns are effective, but chloride salt deposits should be avoided. A pH control and corrosion inhibitor program effectively protects bare steel lines.
In heaters, high temperatures pose challenges. Radiant and convection tubes use carbon steel with 5% chromium for sweet crude oils and 7-9% for sour crude oils. In more aggressive environments, type 316 austenitic stainless steel is used. High combustion chamber temperatures (>1500°F) create materials problems.
Corrosion control measures in crude oil unit: Detailed approach
For the crude unit overhead system, corrosion control measures can be implemented in addition to the simple choice of materials, as previously mentioned. Several strategies can reduce the severity of acid attack in the upper circuit of the crude oil unit:
- Mix
- Often the predominant technique for controlling corrosion.
- In cases where the mixture does not offer sufficient problem reduction, other options require special attention.
- Desalination
- The desalinator, as its name suggests, has the main objective of reducing the amount of salt in crude oil, with a common goal of less than 3 ppm.
- Aside from reducing salt, the desalination process removes entrained solids, such as sand, salt, rust, and paraffin wax crystals that may be present in crude oil.
- This removal helps prevent clogging and fouling in heaters and preheat exchangers.
- caustic addition
Incorporating a small amount of dilute caustic solution, usually sodium hydroxide (NaOH), to desalted crude oil is commonly employed as an effective method to reduce the amount of hydrochloric acid (HCl) released in preheaters. This solution thermally converts HCl to sodium chloride (NaCl), a more stable form, thus decreasing the amount of free HCl produced. Although the results of caustic injection can be beneficial, there is a risk of fouling in the preheat train, accelerated atmosphere, vacuum and coking, as well as the risk of stress corrosion cracking in the presence of caustics and catalysts.
To minimize the adverse effects of caustic injection and maximize its efficiency, complete mixing is essential. This objective is commonly achieved by adding the caustic to the suction of crude oil booster pumps after desalination. Some refiners prefer to blend by injecting the diluted caustic solution into a slipstream of desalted crude oil prior to its introduction into the main process.
Caustic injection upstream of desalters is discouraged due to the high pH of desalinated water, which could lead to the formation of emulsions and allow ammonia to enter the crude oil. Additionally, for units without a desalter, to reduce the risk of caustic cracking, it is recommended that caustic be added to the preheat train at or near the desalter outlet temperature.
- pH control and use of inhibitors to prevent corrosion
The primary objective of a pH control program in the air system is to create a non-corrosive environment by neutralizing the acidic components present. This neutralization is achieved by injecting ammonia, organic neutralizing amines, or a combination of both. The recommended pH control range is generally between 5.5 and 6.5.
It is crucial to keep in mind that neutralizers can affect the pH differently at the initial concentration point, potentially increasing or decreasing depending on the product selected. A pH greater than 8 should be avoided when using brass alloys in the aerial system as they are susceptible to stress corrosion cracking and accelerated corrosion at elevated pH.
- Corrosion inhibitors
Regarding corrosion inhibitors, most control programs include the injection of patented organic inhibitors, known as “filmers”, an image of this process can be seen in Figure 1. These inhibitors create a thin film that acts as a continuous protective barrier between the acids in the system and the metal surface, offering maximum protection. It is essential to maintain proper pH control for optimal results.
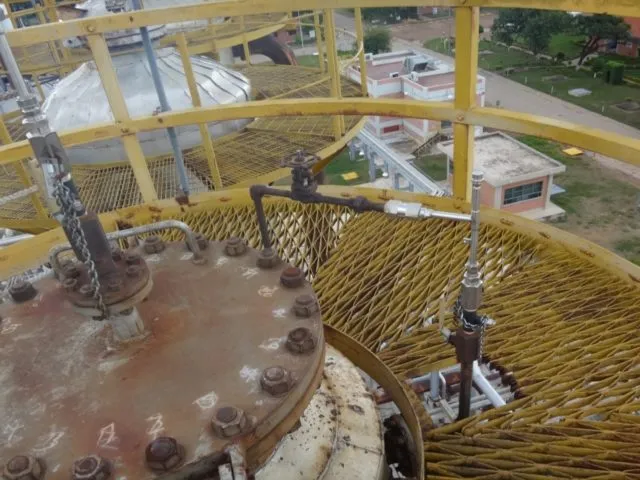
Injection rates of film inhibitors vary depending on the aggressiveness of the corrosion in the system and the concentration of the inhibitor. The effective dose is affected by factors such as the solubility of the inhibitor in liquids (influenced by pH) and the ability of the inhibitor to adsorb to the surface (affected by temperature).
Inhibitors can also have a cleaning effect, removing iron sulfide deposits, especially at higher injection rates.
Inhibitors are high molecular weight and non-volatile, they must be injected independently into both stages of a two-stage aerial system. It is generally not recommended to inject film inhibitors in concentrated form, as near 100% concentration can be corrosive to injection equipment. Naphtha dilution is provided to facilitate dispersion at the injection point.
Although these inhibitors may offer some economic advantage over alloys when acidic crudes are charged intermittently, their effectiveness may be difficult to determine. It is important to note that most available inhibitors contain phosphorus, considered a poison for some hydrotreating catalysts.
- Water wash to control corrosion
Corrosive products, such as ammonium chloride or amine chloride, derived from neutralization reactions, can cause corrosion and form scale; it is common to recirculate water from the aerial receiver to the overhead vapor line of the column. In some refineries, extracted sour water and other water condensates are also found. However, it is crucial to avoid water with dissolved oxygen, as it can significantly accelerate corrosion. Although water flushing can be effective, its design must be careful to avoid generating further corrosion problems and to not cause considerable loss of heat exchange in air naphtha coolers (Figure 2).
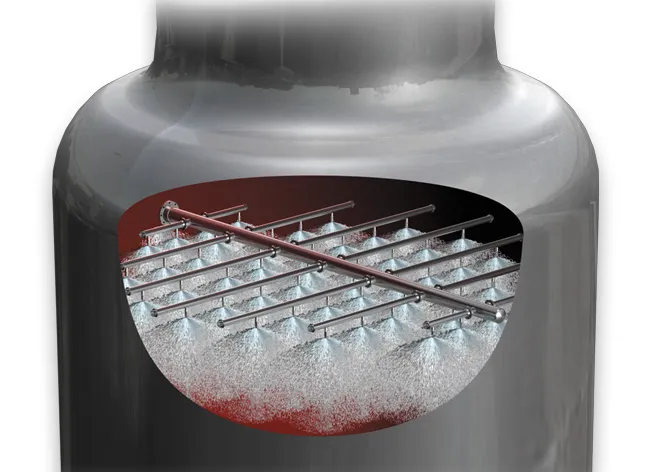
The optimal water injection rate is between 5% and 10% of the airstream. However, excessive water rates can result in poor separation in the upper drum, which could cause water to return to the tower through backflow, causing corrosion in both the tower and the airline. With proper mechanical design and precise chemical balance, water flushing can be a critical part of the airborne corrosion control program.
Conclusions
Effective corrosion control in atmospheric crude distillation units is important to ensure the integrity and operational efficiency of these units. Corrosion, due to the presence of acids and aggressive compounds, can cause significant damage to equipment, compromising the safety and durability of the plant. The implementation of preventive measures, such as the proper selection of materials, the use of corrosion inhibitors, crude oil desalination and pH control, becomes imperative to mitigate corrosive risks.
A comprehensive corrosion monitoring and control program not only preserves the structural integrity of equipment, but also contributes to maintaining operational efficiency, reducing costs associated with maintenance and component replacement. Ultimately, effective corrosion management in these units is essential to ensure the safe and profitable continuity of atmospheric crude distillation operations.
References
- NACE TM0169-2021/ASTM G31-21, Standard Guide for Laboratory Immersion Corrosion Testing of Metals.
- White, RA and Ehmke, EF, “Material Selection for Refineries, Pipelines, and Associated Facilities.”
- Humphries, MH and Sorell, G., “Corrosion Control in Crude Oil Distillation Units,” presented at NACE CORROSION/75.