Introducción
El crudo, debido a su origen en yacimientos naturales, contiene componentes perjudiciales para su procesamiento, como el agua subterránea, sólidos en suspensión, sedimentos y sales disueltas. Estos elementos conllevan problemas de corrosión y por ende a pérdidas económicas y daños materiales durante el almacenamiento y procesamiento del crudo.
La corrosión de las superficies metálicas en contacto con diversas corrientes del proceso es un problema principal asociado con estas sustancias. Para salvaguardar instalaciones y equipos, se aplican tratamientos químicos, desde la extracción hasta el procesamiento del petróleo. A pesar de estos esfuerzos, las torres de destilación primaria, en particular, enfrentan problemas significativos de corrosión, con daños frecuentes en su interior.
A pesar de los tratamientos químicos y evaluaciones, el control y la protección de las instalaciones en estas plantas son complejos debido a la variabilidad en la agresividad del crudo, dependiendo de su tipo, mezclas, contaminantes y agentes corrosivos. Se llevan a cabo evaluaciones de diferentes materiales comúnmente utilizados en la construcción de estas torres mediante la técnica NACE TM0169-761.
Cuando se procesan crudos pesados, se debe considerar los efectos corrosivos de altas concentraciones de azufre y ácidos orgánicos, así como las elevadas temperaturas y el tipo de material, deterioran los equipos de refinación, generando incrustaciones y productos corrosivos que reducen la capacidad de fraccionamiento del crudo y complican su transporte. Los problemas más críticos de corrosión suelen manifestarse en los topes y fondos de la torre de destilación atmosférica, la torre de destilación al vacío, los hornos y las líneas de transferencia, afectando la eficiencia térmica, causando pérdidas de energía y taponamientos.
Esta sección tiene como objetivo destacar los principales tipos de corrosión, identificar dónde ocurren los problemas en las unidades de destilación atmosférica principales y discutir los materiales comúnmente utilizados para mitigar estos problemas.
Principales tipos de corrosión en las unidades de destilación atmosféricas
Los principales mecanismos de daño por corrosión acuosa en los procesos de destilación de crudos son: corrosión por HCl, ácidos nafténicos y sulfidación. Estos procesos pueden ocurrir simultáneamente, dependiendo del tipo de aleación, condiciones de temperatura, pH, concentración.
Corrosión por HCl
El ácido clorhídrico gaseoso, formado de la hidrólisis, de los cloruros de calcio y de magnesio, se condensa luego en las zonas frías y al entrar en contacto con el agua forma ácido clorhídrico principal responsable de la corrosión severa en sistemas de tope. El ácido clorhídrico se forma según las siguientes reacciones: El ácido clorhídrico se forma según las siguientes reacciones:
MgCl2 +2H2O → Mg(OH)2 + 2HCl
2HCl → 2H+ + 2Cl–
2HCl + Fe → FeCl2 + H2
A bajas temperaturas o a un pH elevado en presencia de H2S el mecanismo de corrosión es:
FeCl2 + H2S → FeS + 2HCl
Después, el HCl se disuelve en el agua cerca al punto de condensación inicial, el ácido ataca la superficie del metal, produciendo picado. Los productos de corrosión son sales de cloruros metálicos. Además, cuando el pH del agua en esta región es menor de 5.0, el HCl disuelve los sulfuros metálicos productos de la corrosión que estén presentes. Estos productos de corrosión son llevados al sitio donde se produce el ataque por corrosión, en forma de pequeñas cavidades o grietas.
Corrosión por ácidos nafténicos
La corrosión nafténica ocurre únicamente en presencia de la fase líquida y tiene como parámetros principales del proceso corrosivo: la acidez del crudo, tipo de ácido nafténico, tipo de sulfuro, temperatura, turbulencia, velocidad del flujo, grado de vaporización y la existencia del flujo bifásico. Este ataque no es uniforme lo que dificulta la detección y solución del problema. La presencia de sulfuros y las características fisicoquímicas de los ácidos nafténicos, su contenido, la distribución del punto de ebullición y su temperatura de descomposición, tienen un efecto directo en la corrosión a alta temperatura de la unidad de destilación.
Corrosión sulfídica
Lasulfidación, resulta de la reacción de los aceros con los compuestos de sulfuro a altas temperaturas. Este fenómeno se presenta cuando el metal alcanza una temperatura de 220°C. Los factores importantes que afectan la sulfidación son la composición de la aleación, la temperatura y la concentración de los compuestos de sulfuro. La susceptibilidad de una aleación a la sulfidación es determinada por su capacidad de formar capas protectoras del sulfuro. La resistencia de las aleaciones ferrosas mejora con la cantidad de cromo presente.
Materiales de construcción en unidades de destilación de crudo
La mayoría de los equipos en una unidad de destilación de crudo están fabricados con acero al carbono, apto para temperaturas hasta 450 °F (230 °C). Sin embargo, por encima de esta temperatura, pueden surgir problemas como el ataque de azufre a alta temperatura y la corrosión por ácido nafténico. Para abordar esto, se utilizan materiales altamente aleados, especialmente en la zona superior de la columna Preflash, donde el revestimiento UNS 04400 es común.
En unidades diseñadas para procesar crudo “dulce”, la columna Preflash incorpora revestimientos específicos. La parte superior utiliza UNS 04400 para resistir la condensación de HCl, mientras que el resto de la carcasa es de acero al carbono desnudo. Además, se aplica un revestimiento de cromo al 12 % en la parte inferior para prevenir la corrosión del surco.
En la entrada de alimentación, puede ser necesario emplear acero inoxidable Tipo 316 para plantas que procesan crudos con alto contenido de ácido nafténico. Es esencial asegurar que las boquillas de cada zona estén revestidas con el mismo material que la carcasa. Tras la exposición al servicio, se debe monitorear de cerca la carcasa inmediatamente arriba y abajo del revestimiento para detectar posibles pérdidas en la pared, siendo común la necesidad de expandir las áreas revestidas originales.
En la columna de vacío, que generalmente se reviste con un 12 % de cromo, la zona de destellos puede ser problemática debido al ácido nafténico. Para crudos altamente nafténicos, se podría requerir un revestimiento de acero inoxidable Tipo 316 o 317 en áreas operando por encima de 450 °F (230 °C).
En plantas de crudo dulce, los separadores de flujo lateral a menudo carecen de revestimiento, aunque las alimentaciones de diésel y gasóleo atmosférico alcanzan temperaturas de 550 °F (285 °C) y 650 °F (345 °C), respectivamente. No obstante, en plantas que manejan crudo ácido, estos decapantes calientes podrían necesitar un revestimiento de cromo al 12 %.
Intercambiadores y tuberías en unidades de destilación
La metalurgia de los intercambiadores de calor varía según la composición y temperatura de la corriente. La mayoría son de acero al carbono, pero en los refrigerados por agua dulce, los tubos de latón almirantazgo han sido reemplazados por acero al carbono debido a mejoras en el tratamiento del agua.
En ambientes corrosivos como agua de mar o salobre, se utilizan tubos de titanio o aceros inoxidables superferríticos y dúplex. Los inoxidables austeníticos se limitan por su susceptibilidad al agrietamiento por tensión de cloruro y picaduras.
Los problemas de corrosión más graves se encuentran en las áreas de condensación inicial en sistemas aéreos. La corrosión se intensifica donde vapor de HCl, formado por la hidrólisis de sales de cloruro, se disuelve en agua de condensación, creando un ambiente corrosivo. Los revestimientos UNS 04400 y bandejas en la parte superior de columnas son eficaces, pero se deben evitar depósitos de sal de cloruro. Un programa de control de pH e inhibidores de corrosión protege eficazmente las líneas de acero desnudo.
En calentadores, las altas temperaturas plantean desafíos. Los tubos radiantes y de convección utilizan acero al carbono con 5% de cromo para crudos dulces y 7-9% para crudos ácidos. En ambientes más agresivos, se emplea acero inoxidable austenítico tipo 316. Las elevadas temperaturas de la cámara de combustión (>1500 °F) generan problemas de materiales.
Medidas de control de corrosión en la unidad de crudo: Enfoque detallado
Para el sistema de la unidad de refinacion de crudo, se pueden implementar medidas de control de corrosión en u adicionales a la simple elección de materiales, como se mencionó previamente. Varias estrategias pueden reducir la gravedad del ataque ácido en el circuito superior de la unidad de crudo:
Desalación del crudo
- El desalinizador, como su nombre indica, tiene como objetivo principal reducir la cantidad de sal en el petróleo crudo, con un objetivo común de menos de 3 ppm.
- Aparte de reducir la sal, el proceso de desalinización elimina sólidos arrastrados, como arena, sal, óxido y cristales de cera de parafina que pueden estar presentes en el crudo.
- Esta eliminación ayuda a prevenir obstrucciones y ensuciamiento en calentadores e intercambiadores de precalentamiento.
Adición de soda cáustica
La incorporación de una pequeña cantidad de solución cáustica diluida, generalmente hidróxido de sodio (NaOH), al crudo desalado se emplea comúnmente como un método eficaz para reducir la cantidad de ácido clorhídrico (HCl) liberado en los precalentadores. Esta solución convierte térmicamente el HCl en cloruro de sodio (NaCl), una forma más estable, disminuyendo así la cantidad de HCl libre producido. Aunque los resultados de la inyección cáustica pueden ser beneficiosos, existe el riesgo de ensuciamiento en el tren de precalentamiento, atmósfera acelerada, vacío y coquización, así como el riesgo de agrietamiento por corrosión bajo tensión en presencia de cáusticos y catalizadores.
Para minimizar los efectos adversos de la inyección cáustica y maximizar su eficiencia, es esencial lograr una mezcla completa. Este objetivo se alcanza comúnmente al agregar el cáustico a la succión de las bombas de refuerzo de crudo después de la desalinización. Algunas refinerías prefieren mezclar inyectando la solución cáustica diluida en un rebufo de petróleo crudo desalado antes de su introducción en el proceso principal.
Se desaconseja la inyección de cáustico aguas arriba de los desalinizadores debido al alto pH del agua desalinizada, que podría dar lugar a la formación de emulsiones y permitir la entrada de amoníaco en el crudo. Además, en el caso de unidades sin desalinizador, para reducir el riesgo de agrietamiento cáustico, se recomienda agregar cáustico al tren de precalentamiento a la temperatura de salida del desalinizador o cerca de ella.
Control de pH y uso de inhibidores para prevenir la corrosión
El objetivo principal de un programa de control del pH en el sistema aéreo es crear un entorno no corrosivo neutralizando los componentes ácidos presentes. Esta neutralización se logra mediante la inyección de amoníaco, aminas neutralizantes orgánicas o una combinación de ambas. El rango de control de pH recomendado generalmente oscila entre 5.5 y 6.5.
Es crucial tener en cuenta que los neutralizadores pueden afectar el pH de manera diferente en el punto de concentración inicial, pudiendo aumentar o disminuir según el producto seleccionado. Se debe evitar un pH superior a 8 cuando se utilizan aleaciones de latón en el sistema aéreo, ya que son susceptibles al agrietamiento por corrosión bajo tensión y a la corrosión acelerada a pH elevado.
Inhibidores de corrosión
En cuanto a los inhibidores de corrosión, la mayoría de los programas de control incluyen la inyección de inhibidores orgánicos patentados, conocidos como “filmadores”, en la figura 1, se puede apreciar una imagen de este proceso. Estos inhibidores crean una película delgada que actúa como barrera protectora continua entre los ácidos del sistema y la superficie metálica, ofreciendo máxima protección. Es esencial mantener un control adecuado del pH para obtener resultados óptimos.
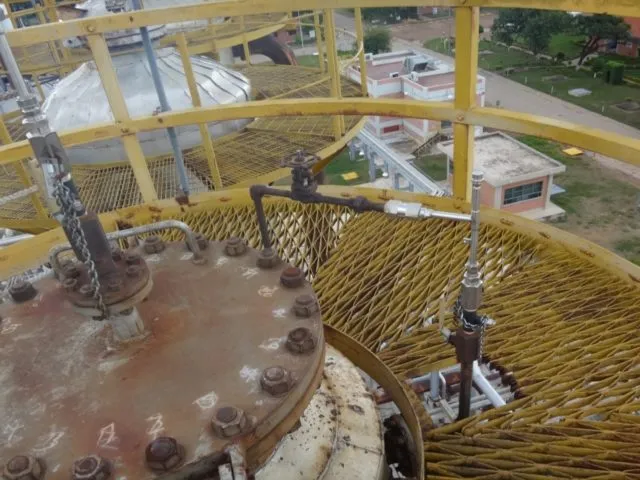
Las tasas de inyección de inhibidores de película varían según la agresividad de la corrosión en el sistema y la concentración del inhibidor. La dosis efectiva se ve afectada por factores como la solubilidad del inhibidor en los líquidos (influenciada por el pH) y la capacidad del inhibidor para adsorberse en la superficie (afectada por la temperatura).
Los inhibidores también pueden tener un efecto de limpieza, eliminando depósitos de sulfuro de hierro, especialmente a tasas de inyección más altas.
Los inhibidores tienen un alto peso molecular y no son volátiles, deben inyectarse de forma independiente en ambas etapas de un sistema aéreo de dos etapas. Por lo general, no se recomienda inyectar inhibidores de película en forma concentrada, ya que cerca del 100% de concentración pueden ser corrosivos para el equipo de inyección. Se proporciona dilución de nafta para facilitar la dispersión en el punto de inyección.
Aunque estos inhibidores pueden ofrecer cierta ventaja económica sobre las aleaciones cuando se cargan crudos ácidos intermitentemente, su eficacia puede ser difícil de determinar. Es importante destacar que la mayoría de los inhibidores disponibles contienen fósforo, considerado un veneno para algunos catalizadores de hidrotratamiento.
Lavado con agua para controlar la corrosión
Los productos corrosivos, como el cloruro de amonio o el cloruro de amina, derivados de las reacciones de neutralización, pueden causar corrosión y formar incrustaciones, es común recircular el agua desde el receptor aéreo hacia la línea aérea de vapor de la columna. En algunas refinerías, también se encuentran agua agria extraída y otros condensados de agua. Sin embargo, es crucial evitar el agua con oxígeno disuelto, ya que puede acelerar la corrosión de manera significativa. Aunque el lavado con agua puede ser eficaz, su diseño debe ser cuidadoso para evitar la generación de más problemas de corrosión y para no causar una pérdida considerable de intercambio de calor en los enfriadores aéreos de nafta (Figura 2) .
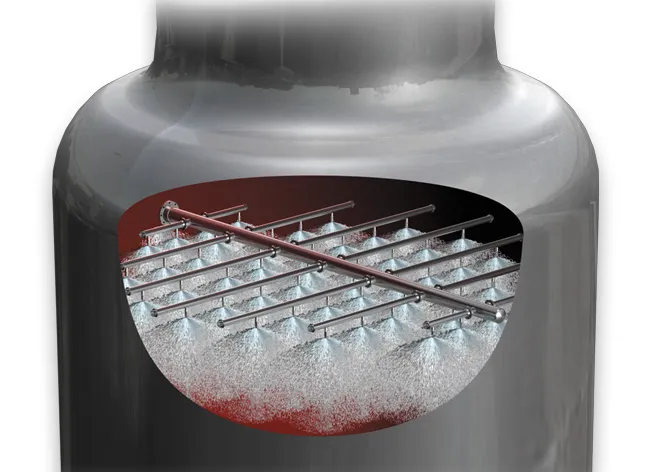
La tasa óptima de inyección de agua oscila entre el 5 % y el 10 % de la corriente aérea. Sin embargo, tasas de agua excesivas pueden resultar en una separación deficiente en el tambor superior, lo que podría provocar el retorno de agua a la torre a través del reflujo, ocasionando corrosión tanto en la torre como en la línea aérea. Con el diseño mecánico adecuado y un equilibrio químico preciso, el lavado con agua puede constituir una parte fundamental del programa de control de la corrosión aérea.
Conclusiones
El control efectivo de la corrosión en las unidades de destilación atmosférica de crudos es importante para garantizar la integridad y la eficiencia operativa de estas unidades. La corrosión, debido a la presencia de ácidos y compuestos agresivos, puede ocasionar daños significativos a los equipos, comprometiendo la seguridad y la durabilidad de la planta. La implementación de medidas preventivas, como la selección adecuada de materiales, el uso de inhibidores de corrosión, la desalación del crudo y el control del pH, se vuelve imperativa para mitigar los riesgos corrosivos.
Un programa integral de monitoreo y control de la corrosión no solo preserva la integridad estructural de los equipos, sino que también contribuye a mantener la eficiencia operativa, reduciendo los costos asociados con mantenimiento y reemplazo de componentes. En última instancia, la gestión efectiva de la corrosión en estas unidades es esencial para garantizar la continuidad segura y rentable de las operaciones de destilación atmosférica de crudos.
Referencias
- NACE TM0169-2021/ASTM G31-21, Standard Guide for Laboratory Immersion Corrosion Testing of Metals.
- White, R. A. y Ehmke, E. F., “Selección de materiales para refinerías, oleoductos e instalaciones asociadas”.
- Humphries, M. H. y Sorell, G., “Control de la corrosión en las unidades de destilación de petróleo crudo”, presentado en NACE CORROSION/75.