Hydrotreating and hydrodesulfurization (HT/HDS) in oil refineries are combined processes that play a decisive role in reducing sulfur content, mainly in fuels, which allows compliance with environmental regulations. However, these processes involve severe conditions that expose assets or equipment to various types of corrosion.
It is important to highlight that the sulfur content of the fuels depends on the type of product processed; if sweet oils (low sulfur content) are processed, then the sulfur content of the derived fuels will also be low; likewise, if high sulfur content oils are processed, the derived fuels will also be highly sulfurized and the desulfurization process will be more difficult.
However, regardless of whether the oil is sweet or sour, in order to comply with the maximum allowable sulfur restrictions established in global and local environmental regulations, HT and HDS will always be required, since without these processes it is impossible to comply with such requirements. Likewise, to better understand the corrosion mechanisms in hydrotreating and hydrodesulfurization units, it is important to have a general knowledge of the description of the flows and processes.
What is hydrotreating and hydrodesulfurization?
Hydrotreating and hydrodesulfurization are characterized by the fact that sulfur is removed from the feedstock as hydrogen sulfide (H2S). This feedstock is brought into contact with hydrogen-rich gas in the presence of a catalyst at high pressure and temperature. The reaction conditions are such that the hydrocarbon fraction vaporizes completely or remains in a liquid state1.
The product yield is high, since only sulfur is removed. In addition, the hydrogen sulfide formed is easily and selectively removed from the product streams (gas and liquid). Hydrogen sulfide obtained as a highly concentrated stream can be converted to sulfur by the Claus process1. In addition to the aforementioned processes, hydrogenation of oxygen and nitrogen compounds is also carried out.
Types of corrosion in hydrotreating and hydrodesulfurizing units
These plants present different types of corrosion, which depend on the operating conditions, processes and fluid streams. The following are the most important in the refining industry.
Hydrogen attack
Carbide components in steel can react with hydrogen, methane and iron when certain conditions such as temperature and hydrogen partial pressure are exceeded. The reaction starts at the inner wall of the equipment and gradually progresses over time through the wall. The methane formed accumulates on the surface of the metal and produces gas bubbles. The iron formed is weaker than the original carbides, as a result of which the material loses strength and ductility, causing cracks to form. Alloying elements such as molybdenum and chromium stabilize and inhibit the decomposition of carbides by hydrogen.
This hydrogen attack, also called hydrogen embrittlement or internal decarburization, requires careful selection of equipment materials for normal operation. In principle, this type of attack is controlled by a correct selection of materials.
H2S/H2 corrosion
Although several works have been carried out to determine corrosion in different H2S/H2 environments, there is still a lack of research on this corrosion mechanism, being different from that determined in crude and vacuum units, as shown by the different materials required to keep corrosion within acceptable limits. Chromium alloy steels (e.g., 5 Cr-O,5 Mo steels) often prevent severe sulfur corrosion and higher alloy steels such as 12 Cr and 18/8 Cr.Ni steels are necessary to control corrosion within acceptable limits in H2S/H2.
Naphthenic acid corrosion
Naphthenic acid corrosion is a chemical reaction (high temperature dry corrosion). When processing crude oils containing naphthenic acids, corrosion will occur on carbon steels at equipment sites where the product temperature is between 240 – 400 °C and a TAN greater than 0.3 mg KOH/gr, and a protective FeS layer does not form on the steel, mainly under turbulent flow conditions in fittings such as elbows and bends. Figure 1 shows a representative picture of naphthenic acid corrosion2.
The corrosion rate is approximately proportional to the acid concentration and increases with increasing temperature until a protective FeS layer is formed.
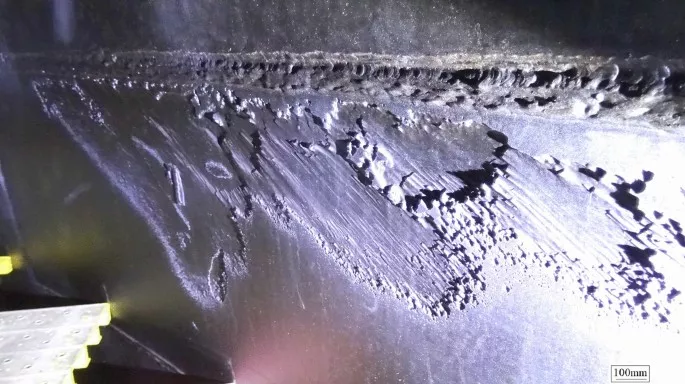
The degree of corrosion of naphthenic acid depends on factors such as:
- TAN (Total Acid Number) of the process stream.
- Molecular weight of the acid.
- Flow conditions.
In general, the following is observed:
- Lighter acids are more corrosive than heavier acids.
- High fluid velocities and turbulence promote corrosion.
- Acid condensation can lead to high local corrosion rates.
- Strong interaction with sulfur (S) corrosion.
In the HT/HDS reactor section, the presence of naphthenic acids can cause corrosion in low-carbon and 0.5 Mo steels above 240 °C if the total acid number (TAN) exceeds 0.3 mg KOH/g. It should be noted that sulfur has a beneficial effect on the corrosion rate of naphthenic acid. A TAN of up to 0.5 is acceptable as long as the sulfur level of the feed is greater than 0.3% by weight. Upstream, including the reactor, the equipment is exposed to naphthenic acids, after which the acids are decomposed in the cracking process.
Aqueous corrosion
Aqueous corrosion is an electrochemical process for which the presence of water is a prerequisite. This can only occur below the dew point of the water or downstream of any wash water injection point. The corrosive compounds come from:
- Food (H2O.H2S, Cl.N).
- Reactions taking place in the HT/HDS reactor (H20,H2S, NH3).
- Replenishment hydrogen gas supplied from platforer (HCI).
- Insufficient neutralization of crude oil and poor separation of water in upstream distillation.
- Presence of oxygen in the injection wash water.
Hydrochloric acid (HCI)
HCI can be produced in HT/HDS units by hydrogenation of organic chlorides. These can originate directly from crude oil, which may be contaminated with chlorinated waste streams, equally from the make-up gas supplied from the platformer can be a major source of HCI in HT/HDS units originating from the injection of chlorinated hydrocarbons into the platformer to control the acidity of the reforming catalyst. HCI is non-corrosive in the dry state at HT/HDS operating temperatures. but becomes extremely corrosive on carbon steel if dissolved in water with pH below 5.
In general activated aluminas will absorb chlorides from the platformer formation gas and to some extent organic chlorides. A normal way to minimize organic chlorides is to periodically change adsorbents.
Ammonium chloride (NH4Cl)
Ammonia (NH3) is formed in HT/HDS units by hydrogenation of organic nitrogen compounds in the feed and the amount produced depends largely on the type of feedstock.
If ammonia and HCI are present, ammonium chloride (NH4Cl) can form and will be deposited upstream (recycle gas compressor, check valves, etc.) and downstream of the reactor. In a dry state, this salt is not corrosive, but in areas where water condenses, the deposited chloride will wet and a pH of 3-4 will occur, generating pitting or crevice corrosion.
This type of corrosion has been found in reactor effluent air cooler heat exchangers (Fin fan Cooler) and in recycle gas compressors, where NH4Clis entrained in the recycle gas.
Ammonium hydrosulfide (NH4HS)
Downstream of the reactor, the dew point of the water in the air coolers (Fin fan cooler) can be reached, giving the condition for the formation of NH4HSammonium hydrosulfide, where severe corrosion of carbon steel can occur under the following conditions:
- The NH4HScontent in the aqueous phase exceeds 2% by weight.
- High velocity conditions due to turbulence at the inlet ends of the tubes.
As the temperature decreases, the concentration of NH4HSin the aqueous phase increases substantially. As the corrosivity of NH4HSis highly dependent on concentration and velocity, it can be assumed that this type of corrosion is much more likely towards the outlet of the air cooler and in the piping leading to the separator. Figure 2 shows a section of pipe with ammonium hydrosulfide (NH4HS) corrosion.
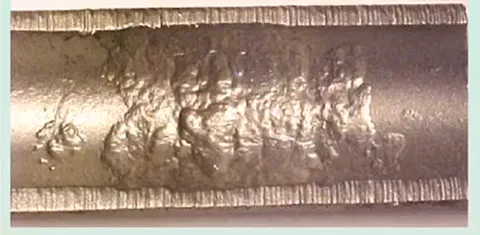
Washing water
Upstream of the water injection point, the process design is such that there is no free water and under such conditions. HCI and its ammonium salts are not corrosive. After water injection, the concentrations of HCI and NH4Clin the vapor, hydrocarbon and water phases can be calculated.
For normal wash water flow rates and typical chloride levels in the reactor effluent, the amounts of HCI in the hydrocarbon phase are very low; chlorides are present in the aqueous phase in ionic form. The high solubility of ammonia and its presence in reactor effluent at much higher concentrations than halides. The wash water is buffered at a pH where ammonia/chloride corrosion should not normally occur (pH>7).
Despite the effect of ammonia on pH, studies have shown ammonia/chloride corrosion generation, so the following precautions should be taken:
- Upstream of the water injection point, noH2Oshould be present.
- Corrosion of the last reactor effluent shell and tube exchanger may be caused by wet ammonium chloride salts.
- The water may come after a unit shutdown or incomplete flushing with water from the exchanger during normal operation. The resulting low pH can cause cracking or pitting corrosion.
- The reactor effluent and wash water should be mixed until the HCI solution in the aqueous phase is almost complete. Incomplete mixing of these two streams, leaving HCI in the vapor phase, will cause corrosion in the piping downstream of the injection point and the Fin Fan cooler tubes.
- The wash water should be low in oxygen. Oxygen increases corrosion, especially at the injection point.
Sulfide and hydrogen stress corrosion cracking
Water containing hydrogen sulfide can cause cracks in carbon steel components with high-strength welds, as well as in highly stressed high-strength steel components such as bolts and compressor rotors. This is known as hydrogen sulfide stress corrosion cracking.
There is a clear relationship between the hardness value of a material and the cracking threshold stress. This is the reason for limiting the hardness levels of materials and welds as much as possible, i.e. below 22 Rc. This is also valid for Cr-Mo steels in hot hydrogen service.
Hydrogen induced cracking / blistering
In wet and acidic conditions, atomic hydrogen is produced on the surface of steels due to electrochemical reactions. Normally, the hydrogen produced recombines into molecular hydrogen without diffusing into the steel wall. However, in the presence of HS and HCN, atomic hydrogen does partially diffuse into the material and recombines to form molecular hydrogen in the steel impurities.
Along the longitudinally oriented impurities in the steel, hydrogen will form at high pressure, causing blistering. In case of numerous inclusions, the different inclusions may combine, resulting in the extension of the cracks. This phenomenon is called hydrogen induced cracking (HIC). A hydrogen-induced blister is shown in Figure 34. The occurrence of HIC/blisters is localized to sites where wet conditions can occur, such as in air coolers and separators of low alloy ferritic materials. Austenitic stainless steels are not susceptible to this type of corrosion damage.
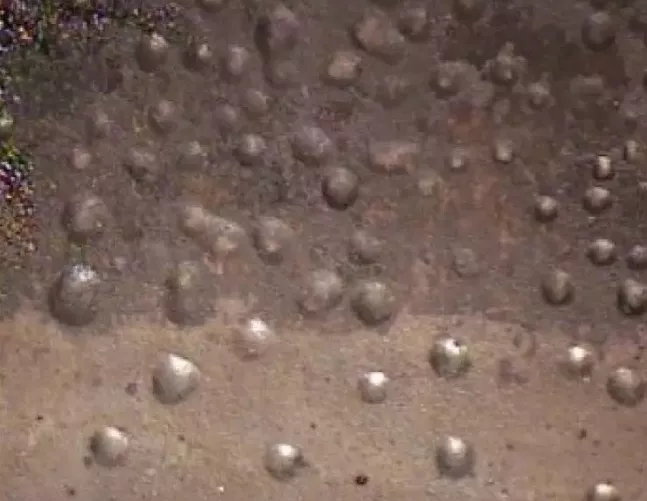
Monitoring and preventive maintenance
Implement a continuous monitoring and control program of the operational variables of pressure, temperature, fluid velocity and characterization of the corrosion products in the equipment, as well as monitor the structural conditions of the equipment using non-destructive testing methodologies such as: Ultrasound, radiography and visual inspection and preventive maintenance based on the data collected.
The monitoring of equipment susceptible to hydrogen induced cracking (HIC) is a special case, since it is a type of corrosion that is difficult to detect and analyze. For this case it is recommended to preferably use the following ultrasonic techniques:
- Backscatter Ultrasound (AUBT).
- Phase Coherence Ultrasound (PCI).
Anti-corrosion measures
To combat corrosion damage, the following strategies should be implemented:
- Selection of materials: From the design itself, corrosion mechanisms must be combated by selecting the appropriate materials according to the corrosive aggressiveness of each process circuit.
- Coatings and linings: Apply internal and external protective coatings to insulate materials from corrosive agents.
- Process control: Reduce the presence of sulfur and minimize hydrogen exposure through purification, drying and adjustment of operating conditions.
Conclusion
Corrosion in hydrotreating and hydrodesulfurizing units represents a significant but manageable challenge with the right approach. Understanding the specific corrosion mechanisms affecting each piece of equipment, along with the implementation of effective mitigation strategies, is essential to maintaining the operability, safety and profitability of these critical facilities in the petroleum refining industry. Combating corrosion is an ongoing effort that requires innovation, research and attention to operational details to ensure long-term success.
References
- https://es.wikipedia.org/wiki/Hidrodesulfuraci%C3%B3n
- Nicácio, J.A.P. & Bracarense, A.Q. Analysis of the naphthenic acids corrosion in a vacuum distillation tower of the Brazilian national oil refinery system. J Braz. Soc. Mech. Sci. Eng. 44, 540 (2022). https://doi.org/10.1007/s40430-022-03830-2
- https://www.youtube.com/watch?app=desktop&v=YGeG4F8vbb8
- https://es.slideshare.net/omaramun/corrosion-tipos