Table of Contents
Industrial boilers are essential equipment in countless strategic processes such as power generation, oil refining, chemical industry and manufacturing, among others. Their ability to efficiently produce steam and transfer heat makes them fundamental equipment for the continuous operation of industrial plants, where any failure or loss of performance can translate into costly interruptions and operational risks.
To maintain its efficiency and ensure safe and reliable operation, rigorous boiler maintenance is essential, and within this, cleaning plays a relevant role, since the accumulation of scale, residues and deposits can reduce heat transfer, increase fuel consumption and cause structural damage that compromises its integrity.
What is an industrial boiler?
It is a thermal equipment designed to generate steam or heat a fluid by transferring heat from the burning of a fuel or other energy source. This steam or hot fluid is used in a wide variety of industrial processes, such as power generation, heating, chemical production, petroleum refining and materials manufacturing.
This equipment consists mainly of the firebox or combustion chamber, the heat exchange tubes, the water supply systems and the pressure and temperature control mechanisms. Their efficiency and safety depend on the design, the type of fuel used and proper boiler maintenance.
Types of industrial boilers
They are classified according to their design and principle of operation into the following main types:
- Pyrotubular (or smoke tube) boilers: In this type, combustion gases circulate inside tubes that are immersed in water. They are ideal for low and medium pressure applications and are characterized by their compact design and ease of operation.
- Water-tube (or water-tube) boilers: In these units, the water circulates through the tubes, while the hot gases surround the outside of the tubes. They are used in high pressure and high performance applications and because they are more efficient they can generate large volumes of steam.
- Electric boilers: They use electric heating elements instead of fossil fuels to generate heat. They are cleaner, quieter and require less maintenance and are used in industries where precise temperature control is required.
- Heat recovery boilers: They use exhaust gases from other industrial processes to generate steam without the need for additional combustion. They are used in cogeneration and combined heat and power plants.
Importance of cleanliness in industrial boilers
Periodic cleaning of boilers is essential to ensure their efficiency, safety and durability. The accumulation of scale, sediment and combustion residues reduces heat transfer, increasing fuel consumption and decreasing steam pressure and temperature. In addition, the presence of corrosive residues accelerates wear and can lead to premature failure.
The major benefits are:
- Performance optimization and energy savings: Eliminating deposits and residues improves heat transfer, enabling efficient operation and reducing energy consumption by up to 15%. This reduces operating costs and optimizes fuel use.
- Prevention of failures and repair costs: Impurities can generate tube overheating, internal corrosion and duct clogging, affecting the structural integrity of the boiler. Proper cleaning prevents serious damage and avoids costly repairs.
- Operational safety and regulatory compliance: Accumulated residues can cause explosions, overpressure and hazardous emissions. Keeping boilers clean minimizes these risks and ensures compliance with international and regional standards and regulations.
- Reduced environmental impact: A dirty boiler emits more pollutants, such as nitrogen oxides (NOx) and carbon monoxide (CO), contributing to global warming. Cleaning improves combustion and reduces the environmental footprint.
- Increased availability and productivity: A boiler in optimal condition reduces unscheduled shutdowns and ensures the continuity of industrial processes, improving system reliability and reducing economic losses.
Types of dirt and residues on boilers
Depending on the source of contamination, wastes found in boilers can be classified as follows:
- Combustion deposits: Soot, coke and ash residues generated during combustion.
- Mineral scale: Deposits of carbonates and sulfates from feed water.
- Corrosion and oxidation: Generated by prolonged exposure to high temperatures and the presence of dissolved oxygen in the water.
- Environmental and biological fouling: Includes dust, grease and microorganisms that can accumulate on the outside and in boiler pipes.
Industrial boiler cleaning methods
There are several industrial boiler cleaning methods for boiler maintenance, each suitable for different needs and types of waste. The main ones are described below:
Mechanical cleaning
This method uses tools such as brushes, scrapers and rotating devices to remove adhering residues on the internal surfaces of the boiler. It is mainly used in industrial boilers with solid scale and carbon deposits.
Advantages:
- Effective against hard residues.
- It does not require the use of aggressive chemical products.
- Low operating cost.
- There are different types of devices that allow the internal or external cleaning of the tubes.
Pressurized water cleaning (power washing)
It is a cleaning technique that uses high-pressure water to remove scale, mineral deposits and accumulated debris from industrial boiler tubes. Depending on the level of fouling and boiler design, specialized nozzles and high-pressure pumps are used that can reach up to 40,000 psi.
Advantages:
- Efficient cleaning: Removes deposits quickly and effectively without disassembling the tubes.
- No damage to the structure: Unlike abrasive methods, it does not wear the tube material.
- Ecological process: It does not use aggressive chemicals, reducing the environmental impact.
- Depending on the type of equipment, internal and external pipe cleaning can be performed.
Boiler shot blasting (sandblasting)
Shot blasting, also known as sandblasting, is a process in which abrasive particles (sand, aluminum oxide or glass beads) are projected at high speed to remove scale and corrosion.
Advantages:
- Ideal for removing rust and hard residues on pipe exteriors.
- Performs very deep cleaning.
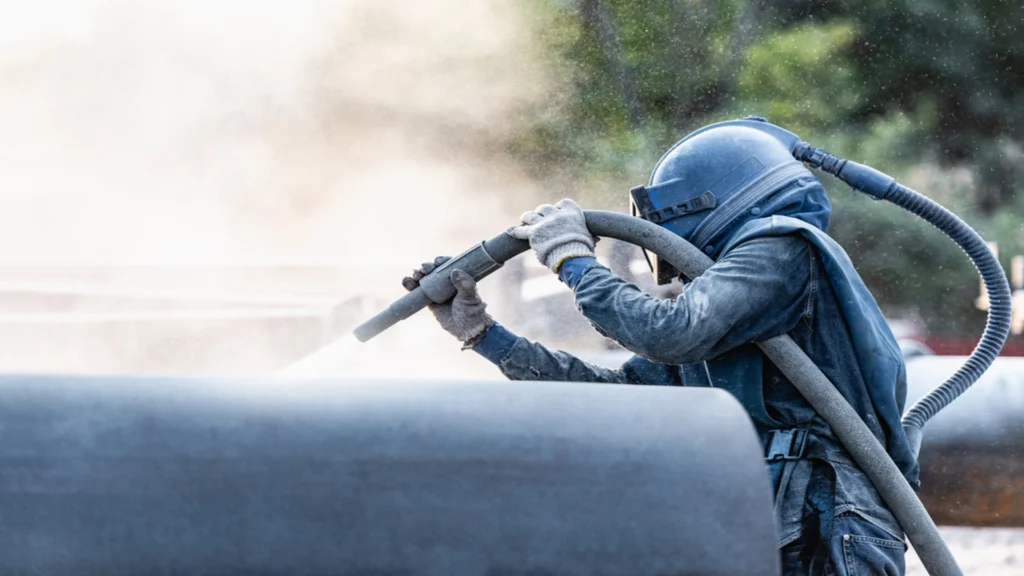
Chemical cleaning
This method uses chemical solutions to dissolve scale and sediments accumulated on the internal surfaces of the pipes. Environmentally friendly options are available to reduce environmental impact.
Advantages:
- Access areas that are difficult to reach by other methods.
- Eliminates residues without the need for disassembly.
- Effective against mineral accumulations.
Dry ice blasting (solid CO₂ or dry ice)
It is a method similar to boiler blasting. It uses dry ice particles projected at high velocity to remove residues without generating secondary fouling.
Advantages:
- Does not damage metal surfaces.
- It does not leave additional residues.
- Environmentally friendly.
Soot blowers
They use jets of steam or compressed air to detach and expel the residues adhered to the external surfaces of the boiler tubes. This system is normally installed fixed on the economizers and superheaters of the boilers and are used manually or automated.
There are three types: fixed lance, rotary air or steam and impact or blow.
Advantages:
- Reduce fuel consumption.
- Frequent cleaning can be maintained on the economized and overheaters.
- They increase the service life of the boiler by preventing corrosive build-up.
Ultrasonic cleaning
This method uses ultrasonic waves that cause cavitation of the molecules removing impurities and residues adhered to the internal and external surfaces of the boiler tubes. The process consists of placing ultrasonic transducers in contact with the tubes to be cleaned so that cavitation occurs.
Advantages:
- Penetrates into hard-to-reach areas.
- Does not require complete disassembly.
- Does not damage metal surfaces.
Acoustic cleaning
They remove ash, soot and other adhering particles from the external surfaces of the tubes using acoustic wave shocks. It is an automatic system using several acoustic wave emitting devices that works with the boiler in service and is a good substitute with advantages of soot blowers.
Advantages:
- They are more energy efficient.
- It is used with the boiler in service.
- Fixed installation on the boiler for frequent cleaning.
- It does not produce erosion.
- Because it operates with the boiler in service, it saves installation costs and equipment downtime.
Application of cleaning methods for each boiler type
The following are the main techniques or methods for internal and external tube cleaning for each type of industrial boiler:
Pyrotubular boilers
- Internal cleaning: Accumulation of soot, combustion residues and mineral deposits in the tubes and water chamber can affect performance. The most commonly used techniques include: Mechanical cleaning with rotating brushes and pressurized water cleaning (hydroblasting).
- External cleaning: The external surface of the boiler can accumulate dust, oils and industrial residues, which can affect heat dissipation and structural integrity. Methods such as pressure water cleaning (power washing) are used.
Water-tube boilers
- Internal cleaning: As water circulates through the tubes, the accumulation of scale, oxides and debris can affect heat transfer and boiler safety. The most common techniques include high-pressure power washing, mechanical cleaning with rotating brushes, chemical cleaning with descaling acids and ultrasonic cleaning.
- External cleaning: External cleaning focuses on removing combustion residues and environmental dust using shot blasting or sandblasting, pressure blasting, acoustic cleaning, hydroblasting, mechanical cleaning and soot blowers.
Electric boilers
- Internal cleaning: Electric boilers do not generate soot or combustion residues, but may present mineral accumulation in the water conduction system and heating elements. Techniques such as chemical descaling with non-corrosive products and cleaning with biodegradable products are used to remove mineral deposits without affecting the electrical components.
When and how often should the boilers be cleaned?
The periodicity of boiler cleaning depends on several factors, such as the type of fuel used, water quality and operating conditions. In general, it is recommended:
- Routine cleaning: Every 3 to 6 months to remove surface residues.
- Deep cleaning: At least once a year to remove scale and improve efficiency.
- Corrective cleaning: Whenever obstructions or loss of heat transfer efficiency are detected.
Conclusion
The maintenance of industrial boilers is a fundamental practice to ensure their optimal and safe operation. The selection of the appropriate boiler cleaning method will depend on the type of waste, boiler configuration and environmental requirements.
Implementing a preventive and predictive maintenance program with advanced technologies will reduce costs, improve efficiency and ensure the operational continuity of the industry.
References
- https://smaltda.com/limpieza-agua-alta-presion/
- https://watex.com/water-jetting-pipe/
- https://umesal.com/en-que-consiste-el-granallado/
- https://reinva.es/productos-vapor-y-combustion/limpieza-acustica-de-calderas-y-equipos/