When we board a plane, whether for a leisure trip or a work commitment, we place our trust in the aircraft and its ability to get us from one place to another safely. Ensuring the integrity and safety of aircraft is essential, and Non-Destructive Testing (NDT) plays an important role in this process. In this article, we will explore the importance of non-destructive testing in aviation and how it helps ensure safe flights.
What are Non-Destructive Testing?
Non-Destructive Testing are methods and techniques used to evaluate the integrity of components and structures without causing permanent damage to them. These techniques make it possible to identify defects, cracks or wear in materials without the need to destroy or dismantle the piece in question. In the aviation industry, NDTs are necessary to ensure the safety of aircraft, as they detect hidden problems that could put the lives of passengers and crew at risk.
Preventive maintenance in aviation: Key to aircraft safety
Preventive maintenance is a considerable part of the aviation industry. Aircraft are subject to extreme conditions, such as changes in temperature, pressure and mechanical stress during flights. Regular and rigorous maintenance is essential for safety by preventing catastrophic failures.
Types of Non-Destructive Testing in aviation
Visual Inspection (VT)
It involves carefully evaluating the surface and structures of the aircraft for visible signs of damage, corrosion or wear. It is a first step in detecting obvious problems.
Ultrasound (UT)
It is a technique that uses high-frequency sound waves to detect imperfections in materials. This technique is commonly used to inspect metallic parts (see Figure 1), such as the aircraft fuselage and composite materials and honeycomb. Ultrasound operators can identify internal defects, such as cracks or inclusions, as well as laminations in composite and honeycomb-type materials, among others.
Ultrasound has evolved into modern techniques such as Phase Array (PAUT), Total Focus Method (TFM), and PHASE Coherence (PCI) to be more precise, portable, and efficient. On the other hand, the use of air coupling transducers has proven to be very useful in these applications.
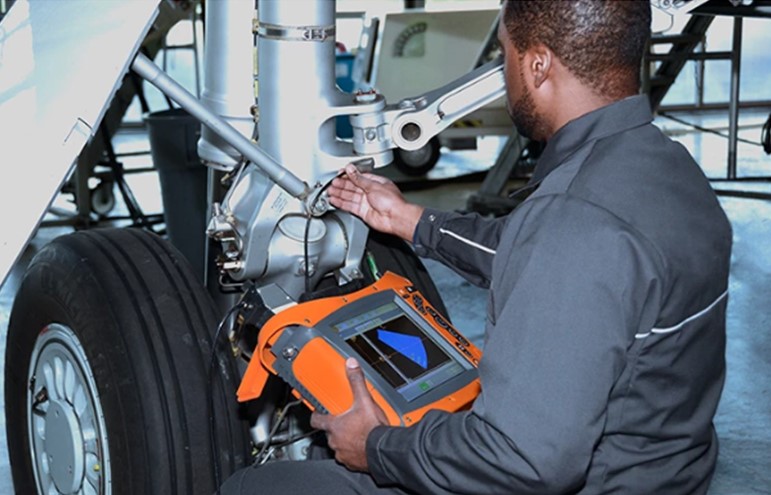
Radiography (RT)
It is another important method in the aviation industry. It consists of the use of ionizing radiation to obtain images of the internal structure of the pieces (see figure 2). This allows defects such as cracks, corrosion and welding problems to be detected. Modern techniques such as Digital Radiography (DR) and Computed Tomography (CT) have been of great support in the inspection of structural and drive components and thus in the safety of aircraft.
These technologies have improved defect detection, reducing radiation exposure and allowing for more efficient and accurate inspection.
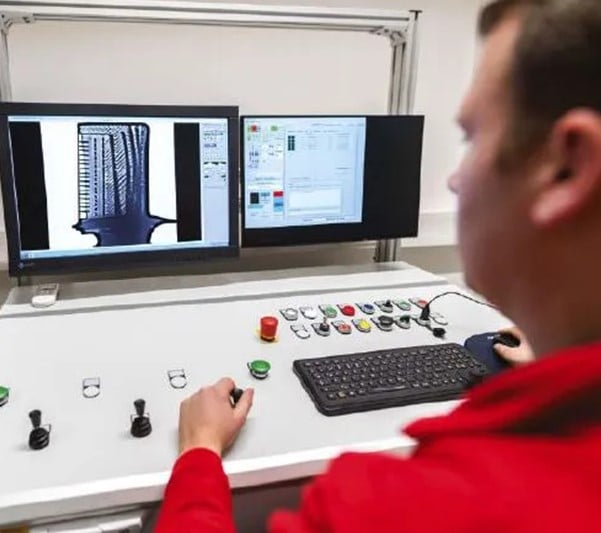
Penetrating Liquids (PT)
Liquid penetrants are used to detect surface defects in non-porous materials, such as aluminum parts. It consists of applying a penetrating liquid and a developer that highlights imperfections.
Magnetic Particles (MT)
This method is especially useful for inspecting ferrous metal components. It involves applying magnetic particles to the surface of the material and observing any changes in its pattern, which reveals the presence of cracks or other defects.
Eddy currents (ECT)
It is a technique used in the aviation industry. This method is based on the detection of changes in the generation of induced currents in the specimen, due to the presence of defects, such as cracks or corrosion (see figure 3), in electrically conductive metal structures or due to changes in the properties electrical of this. Eddy current testing is particularly valuable for inspecting aluminum parts and drive components, such as turbine parts.
New technologies such as Eddy Current Array (ECA) have solved challenges in the aeronautical industry such as the detection of extremely small defects to the inspection of surfaces of complex geometry and the coverage of a wide area represents a fundamental test in the safety of the aircraft.
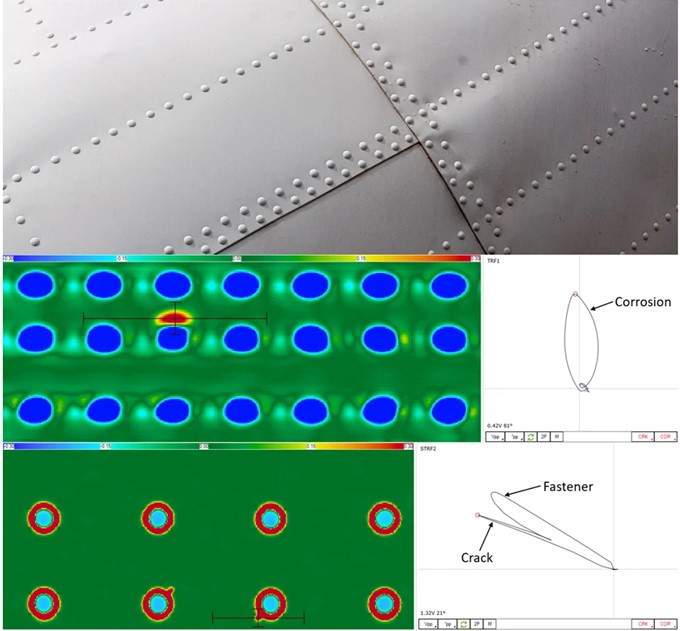
Infrared Thermography (IRT)
This test method uses infrared cameras to detect temperature differences on the surface of the aircraft. These differences can reveal problems such as overheating in electrical components or irregularities in the structure, which helps prevent possible failures.
Catastrophic Failure Prevention
Non-Destructive Testing plays a critical role in aircraft safety by preventing aviation failures by detecting structural defects in time. NDTs allow defects to be identified before they become serious problems, which is why their application in this area and the acceptance criteria used are more strict. This not only ensures the safety of passengers and crew, but also prevents costly repairs or even the loss of an aircraft.
Compliance with security standards
Aviation is highly regulated and subject to strict safety standards. Aircraft must undergo regular inspections including non-destructive testing to ensure they meet safety standards. This applies not only to commercial aircraft, but also to military and private aircraft.
Economic benefits
Although aircraft safety is the primary concern in aviation, Non-Destructive Testing also offers significant economic benefits. Detecting and addressing defects reduces repair costs and extends the life of aircraft. Additionally, it avoids disruption to operations and loss of revenue that would result from an unexpected failure.
Technological advances in Non-Destructive Testing
Technology has driven significant advances in Non-Destructive Testing. Modern techniques and equipment are more precise, efficient and safer than ever. Drones, for example, are used to inspect hard-to-reach areas on the aircraft structure. These methods also benefit from artificial intelligence and machine learning, which can analyze large amounts of data to identify defects more quickly and accurately, all benefiting aircraft safety.
Conclusion
Non-destructive testing is essential to ensure the safety of aircraft. These techniques allow us to identify hidden defects and problems, prevent failures and comply with the safety standards required in the aviation industry. Additionally, they offer economic benefits by reducing repair costs and extending the useful life of aircraft. These tests are important in the aviation industry, and it continues to evolve thanks to technological advances.
The next time you board a plane, you can be confident that NDTs play a significant role in keeping your flight safe.
References
- PHILIP GRAHAM. Three forms of non-destructive testing to take aviation safety to the top; Consulted on November 3, 2023; https://www.olympus-ims.com/es/insight/3-ways-ndt-helps-take-aircraft-safety-to-new-heights
- JESUS CONTRERAS. Role of non-destructive testing in the aerospace industry; Consulted on November 3, 2023; https://inspenet.com/articulo/ensayos-no-destructivos-aeroespacial/
- ALLPRODUCTIVITY. Non-destructive testing of composite materials in manufacturing processes; Consulted on November 4, 2023; http://todoproductivity.blogspot.com/2008/07/ensayos-no-destructivos-de-materiales.html
- EDDYFI. Aircraft and Aerospace NDT; Consulted on November 6, 2023; https://www.eddyfi.com/en/application/aircraft-and-spacecraft-ndt
- LENNART SCHULEMBURG. Aircraft and Aerospace NDT; Consulted on November 6, 2023; https://ati.mydigitalpublication.co.uk/articles/how-to-unlock-the-potential-of-digital-radiography