Aboveground storage tank inspection is one of the processes in asset integrity management in the energy and industrial industry. As technology advances, new solutions are transforming the way tanks are evaluated and maintained. In this context, technologies such as remote visual inspection, robotic technology, and drone inspection are enabling significant improvement in the efficiency and accuracy of these inspections. In addition, the evolution of API 653 regulations has played a key role in the way these inspections are carried out, adapting to new technologies to ensure regulatory compliance.
This article explains the application of emerging technologies, such as the use of drones and robotics, and how they have improved aboveground storage tank inspections. It also discusses how API 653 has evolved to incorporate these technological innovations.
The importance of aboveground storage tank inspection
Aboveground storage tanks are critical components in industrial and energy sectors, especially for the storage of fuels and other liquids. These tanks must be inspected periodically to ensure that they do not present structural or safety failures. Traditionally, inspection has been carried out manually, which involved safety risks and a time-consuming and costly process.
In accordance with the regulations, the inspection plan and the “maintenance management program”, periodic inspections are required to ensure that the tanks maintain their structural integrity over time. These inspections should cover several aspects, including the evaluation of the external structure, the integrity of the foundations and the internal condition of the tank. Depending on factors such as the age of the tank, the type of liquid stored and its maintenance history, the depth and frequency of inspections may vary.
The inspection frequencies recommended by this standard are as follows:
- Annual inspection of the external structure: Surface evaluation for visible damage, corrosion or any alteration that compromises the operational safety of the tank.
- Detailed inspection every 5 to 10 years: Comprehensive inspection including internal tank evaluation and structural integrity tests, such as corrosion analysis and thickness and discontinuity control.
- Additional inspections: In the event of incidents, significant changes in operating conditions, or following extreme weather events, inspections outside the normal cycles are required to ensure that the tank remains safe and functional.
With the advancement of technology, inspections have evolved, and it is now possible to perform more accurate, efficient and safe assessments through the use of advanced tools such as drones and ROVs (remotely operated vehicles).
These technologies enable remote inspections to be performed without the need for human intervention in hazardous or difficult-to-access areas, significantly reducing the risks associated with working at height and improving the quality of the data obtained. In addition, real-time data collection and analysis facilitates informed decision making, enabling more proactive maintenance management.
Developments in API 653 standards
API 653, the standard governing the inspection, maintenance and repair of these storage tanks, has undergone significant evolution since its inception. Originally, the standard focused on direct, manual visual inspections, which, while useful, limited the ability to detect hidden defects or defects in hard-to-reach areas.
With the advancement of technology, this standard has progressively integrated new methodologies to optimize the accuracy and efficiency of inspections, aligning with technological advances that improve safety and reduce operating costs.
The regulation has integrated new practices such as drone inspection, remote visual inspection and the use of robotic technology to perform more detailed and less invasive assessments of tanks. The implementation of these technologies not only improves the accuracy of inspections, but also facilitates compliance with safety standards and reduces associated time and costs.
The use of remotely operated vehicles (ROVs), drones and advanced data analysis systems provide a detailed view of tank conditions without the need for physical intervention in hazardous or difficult to access areas. These advances not only facilitate early detection of problems, such as internal corrosion, wall cracks or damage to the tank base, but also optimize the time to repair the asset.
As the API standard continues to adapt, there is a growing trend towards the integration of non-destructive testing (NDT) technologies, such as ultrasonic inspection, which allows for deeper and more accurate tank assessments. The updated standard is also aligned with the growing importance of preventive inspection and asset lifecycle management, which helps companies make decisions based on more accurate data and extend tank life.
Technologies in the inspection of aboveground storage tanks
As technology advances, new methodologies enable more accurate, efficient and safer inspections. These innovations improve the accuracy of damage or failure identification, and are used to optimize time and reduce the risks associated with traditional inspections. The following are the main modern technologies that are transforming the way these inspections are performed:
Remote visual inspection (RVI)
Remote visual inspection has transformed the way storage tanks are evaluated. Using advanced technologies, such as:
- High-resolution cameras: These are advanced cameras that capture clear, detailed images of tank surfaces or structures.
- Thermographic cameras: Some IVRs use infrared cameras to detect thermal anomalies, such as hot or cold spots, which could indicate internal indications or component failures.
- Drones: Drones equipped with cameras can fly around structures to image hard-to-reach areas, such as tank roofs or elevated platforms.
With this visual inspection equipment and good imaging, inspectors can perform detailed assessments of the surface and internal structure of tanks without the need for direct physical access. This increases safety by reducing the need for human intervention in hazardous areas, providing a clearer view of any possible damage or corrosion.
Drone inspection
One of the most prominent innovations in aboveground storage tank inspection is the use of drones. Drones equipped with high-definition cameras, thermal sensors, ultrasonic sensors, and corrosion detection tools and other specialized equipment can fly around tanks, positioning themselves in hard-to-access locations, capturing images and data from angles that were previously difficult to reach. This has made it possible to inspect hard-to-reach areas, such as tank roofs or areas with high concentrations of gases or vapors.
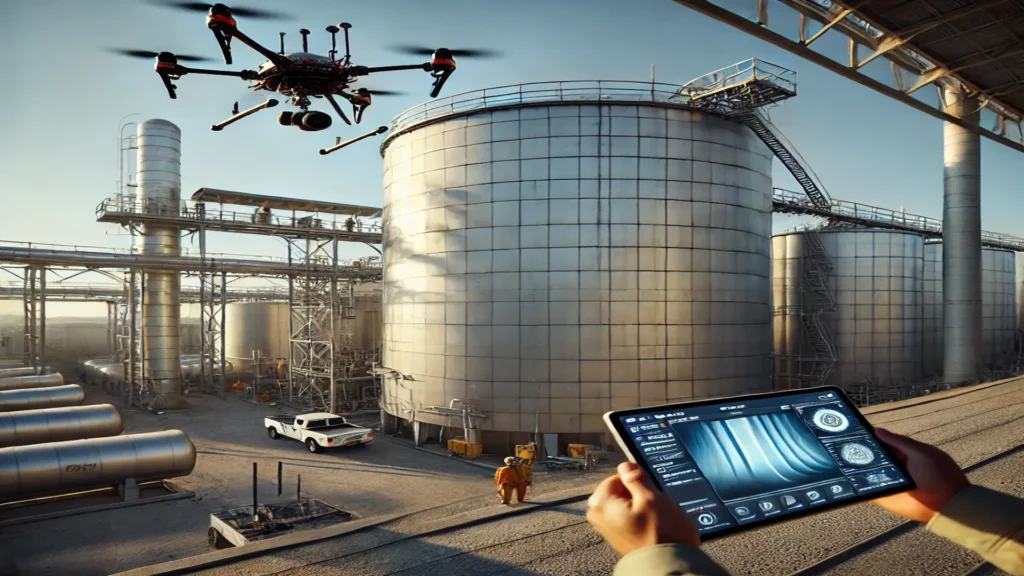
The use of drone inspection has also improved safety by eliminating the need for inspectors to climb dangerous structures. In addition, drones can cover large areas quickly, which significantly reduces inspection times and improves efficiency.
Robotic technology
Robotic technology has advanced significantly in the inspection of these storage tanks. Robots designed to perform tank inspections can enter the interior of tanks, providing detailed information on internal structural integrity that could not otherwise be obtained. These robots can be equipped with cameras, ultrasonic sensors, and corrosion detection tools, allowing them to perform detailed analysis and generate valuable data without putting operators at risk.
One of the most interesting robot applications is the intrinsically safe ROV swimmer. These robots can perform ultrasonic inspection of tank floors, which can identify corrosion or wear problems in critical areas.
Technological evaluation of key components in tanks
Storage tanks are complex structures that require continuous monitoring and maintenance to ensure their integrity and safe operation. These tanks have several critical components and elements that must be inspected regularly for potential failures such as corrosion, cracks, plugging or structural damage.
Tank base (tank bottom)
Description: The base is one of the most critical components of a storage tank as it is in direct contact with the ground. This is where debris and moisture can accumulate and where corrosion is most common due to interaction with water, moisture and fuel. If the tank is well seated on a sound surface, there are no external corrosion problems; but internally the product it stores can generate corrosion.
Applicable Technology: ROV (Remotely Operated Vehicle) robotic technology.
Why: ROVs equipped with NDT tools such as ultrasound, high-resolution cameras and vibration sensors can be used to inspect the bottom of the tank without emptying the tank contents or interrupting operations. These vehicles can access areas that are difficult for human inspectors to reach, such as the bottom of the tank or the foundation, without the fabrication of scaffolding.
Benefits: Detect corrosion and damage in ground contact areas without the need for costly and dangerous disassembly, such as emptying the tank, which reduces interruptions in operations.
Tank walls (outer and inner side)
Description: Tank walls are subject to wear and corrosion due to environmental conditions and exposure to stored chemicals. Internal corrosion can be especially difficult to detect if not properly inspected.
Applicable technology: Inspection with drones and remotely operated robots with high resolution cameras, ultrasonic and thermal sensors.
Why: Drones can perform visual inspections of external tank walls, detecting signs of corrosion, dents, cracks or debris accumulation, thickness measurement and defectology in ultrasonic inspection. In addition, drones with thermal cameras can detect temperature differences in the walls, which can be indicative of structural failure or internal problems.
Benefits: The use of drones improves the speed and safety of tank wall inspection, reducing the need for work at height and speeding up problem identification.
Tank roof
Description: The roof of a tank may be exposed to accumulation of dust, snow or even corrosion. In addition, on some tanks, the suction cup system or roof vents may be faulty and should be detected.
Applicable technology: Remotely operated robots and drones with high resolution cameras and gas sensors.
Why: Robots and drones are ideal for accessing the roof of tanks without the need for inspectors to climb on top, reducing risks. In addition, drones equipped with gas sensors can detect hazardous vapor leaks or emissions coming from roof vents or valves.
Benefits: Allows you to quickly inspect the roof, detect potential failures in vents or ventilation systems and improve process safety.
Valve and piping system
Description: Valve and piping systems are connected to the tank and are essential for the inflow and outflow of stored liquids. Leaks or blockages in these components can compromise storage safety.
Applicable technology: Drones equipped with gas sensors and cameras.
Why: Drones can inspect exterior valves and piping, detect gas or liquid leaks, and verify proper operation of control systems. This is especially useful in hard-to-reach or high-risk areas.
Benefits: Aerial inspection reduces risk exposure and allows efficient inspection of valves and connections without operational interruptions.
Anchors and structural reinforcements
Description: Tanks often have anchors that hold them firmly in place. Any failure in these components can compromise the stability of the tank, especially in areas prone to earthquakes or extreme weather conditions.
Applicable technology: ROV with vibration sensors and cameras
Why: ROVs can be equipped with vibration sensors to monitor the structural integrity of anchors and reinforcements. In addition, high-resolution cameras can provide detailed images of component conditions, allowing for a comprehensive assessment.
Benefits: ROVs can provide accurate assessment of structural stability, especially in situations where physical inspections are not possible without disrupting operations.
Inspection with “Scorpion 2” robot from Eddyfi Technologies
One of the most outstanding implementations of robotic technology in aboveground tank inspection has been carried out with the Scorpion 2 robot, developed by Eddyfi Technologies, a company that is part of Inspenet’s corporate ecosystem. This technology represents a significant advance in the automation of non-destructive inspections, especially on vertical or difficult to access surfaces.
The Scorpion 2 robot has been designed to perform high-precision ultrasonic inspections of metal tank walls and ceilings, significantly reducing inspection times without compromising the quality of the data collected. Thanks to its optimized configuration and remote access capability, it is positioned as a robust solution for structural evaluation in compliance with API 653.
Scorpion 2 key benefits
- High scanning speed (10 meters in less than one minute).
- Dry coupled rolling probe, eliminating the need for liquid couplings.
- Remote operation up to 50 m, ideal for harsh environments.
- Increased probability of detection (POD) with continuous readings.
- Fast assembly thanks to its modular three-component system.
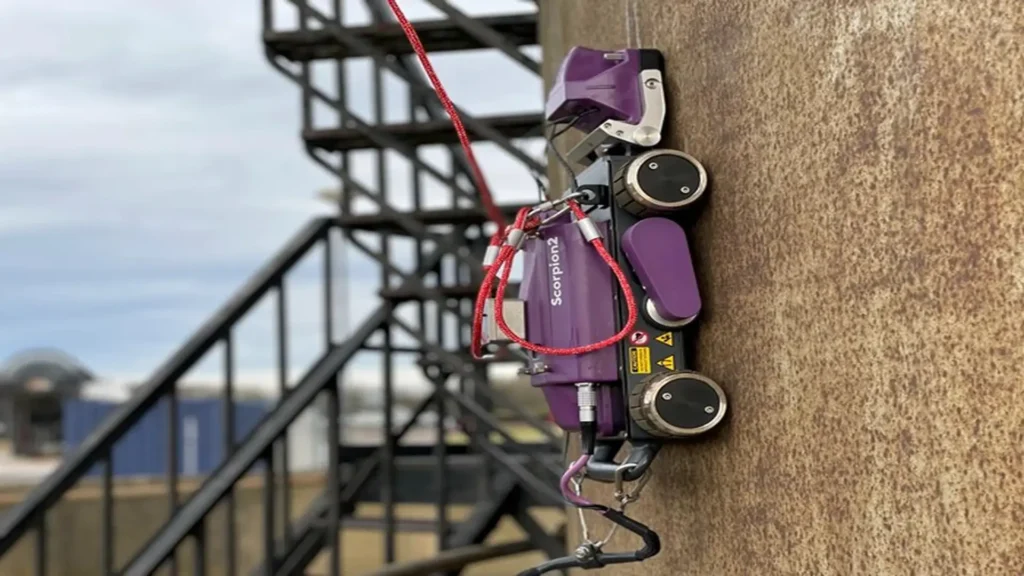
This success story not only demonstrates the effectiveness of today’s robotic technologies, but also the Inspenet platform’s commitment to promoting advanced technological solutions that raise safety and integrity standards in the global energy and industrial industry.
Conclusions
The inspection of aboveground storage tanks has evolved considerably with the incorporation of advanced technologies such as robotics, drones and remote visual inspection systems. These tools have optimized the structural evaluation and integrity monitoring processes, allowing for more accurate, safe and efficient inspections.
Furthermore, its application facilitates strict compliance with API 653 requirements by reducing the need for manual interventions and downtime, without compromising the quality and traceability of the data obtained.
The incorporation of ROVs and drones has made it possible to carry out remote inspections in areas with difficult access or hazardous conditions, significantly reducing personnel exposure and improving operational coverage. This automation contributes to reducing the costs and time associated with conventional inspections.
At the same time, the use of non-destructive techniques such as ultrasound facilitates detailed evaluations of the structural integrity of tanks, providing critical data for predictive and reliable maintenance management. The adoption of these technologies positions companies to face today’s challenges in industrial asset management with greater strength, promoting safer, more efficient operations that are aligned with durability and regulatory compliance standards.
Take your maintenance to the next level with Inspenet innovation!
References
Own source